Introduction: Industrial Record Holder for Under $20
In this Instructable, I will show you how to make an easy, low-cost record/magazine holder. This is perfect for anyone who has piles of records and no place to store them, as it is both stable and good looking. Even to a non-experienced builder like myself, it was quite simple and took just about a day and a half to make. This is my first Instructable, so feel free to comment below and let me know how I can improve!
Step 1: Materials
Wood
- Two 48'' long pieces of poplar (1/2'' x 2'')
- Two sturdy 48'' long dowels (3/8'')
Hardware
- 2 bolts (Mine were about 1.5'' long with a 1/4'' diameter)
- 2 large washers that fit over the hexagonal part of the bolt
- 2 small washers that fit over the regular part of the bolt
- 2 nuts that fit the bolt
Fabric
- I used an old curtain made of canvas to keep the cost down. However, If you are buying fabric, get a strong, heavy duty fabric. 1.5 yards is enough. If you are looking to get cheap fabric, go to the thrift store and try to find a curtain with good fabric
Tools
- If you are cutting your own wood, you will need a saw like the one pictured in the next step.
- A drill
- 3/8'' bit
- Sandpaper
- Electric sander (optional but much easier)
- Stain (optional)
- Wood Glue (optional)
- Sewing machine (optional if you want to hand sew)
- Ruler
- Pencil
- Scissors
- Clamp
- Safety glasses, latex gloves, and mask
My total cost at the hardware store wound up to be just under $16 USD. Yours may vary depending on what you need to purchase.
Step 2: Cutting and Drilling
Cutting
If your local hardware store offers cutting services, use that opportunity to get everything cut there. That way, you won't need to do any sawing which is always easier.
**Ask to keep the scraps**
Before you begin sawing and drilling, please wear safety googles and a safety mask to avoid breathing in sawdust or getting it into your eye. Do this outside or in a workshop.
I had my 1/2'' x 2'' pieces cut into four 21 inch long pieces. If possible, get the angles cut as well. The angle degree for mine was 30 degrees. Cut the bottom and the top as shown in the picture above. This keeps the top and bottom parallel.
Next, cut the dowels. You will need two 20 inch pieces and two 19 inch pieces. This is because the 20 inch pieces need to travel a bit farther to reach the outer parts of the frame than the 19 inch pieces, which only go to the inner parts.
Drilling
This project requires 3 holes to be drilled. One in the center of the 1/2'' x 2'' pieces and one on each of the outer edges. If you zoom in on the top piece of wood in the picture provided, you can see the markings for my holes. I put the outer holes one inch from the edge and in the center of the 2'' part. Drill all holes with a 3/8'' bit.
Drilling tips
Only mark one piece of wood. When you begin drilling, stack and clamp two pieces of wood on top of each other and drill completely through the top piece and halfway through the bottom one. To ensure this result every time, put a piece of tape on the bit at the spot where the bit reaches though one and a half pieces of wood. Use the guide holes on the bottom piece to know where to drill the rest of the pieces. When you reach the last piece of wood, put your scrap piece underneath the hole to prevent drilling into the table.
Step 3: Sanding
Now we have the fun part! Sanding ;)
I used three different grits of sandpaper for this project. Using an electric sander, I started with 80 grit, then moved on to 120 grit, then finished it off with 240 grit sandpaper. Remember to wear safety goggles and a face mask if you don't want sawdust in your eyes and lungs. If you don't have an electric sander, chances are someone you know has one or there is a place you can use one. However, if necessary, you can hand sand. The number I was taught was 100 strokes per side per grit. Sand with the grain, not against it.
For the dowels, I lightly hand sanded the curved sides and used the electric sander on the tops.
Step 4: Dry Fit
Once everything was nice and smooth and the table was wiped down, I proceeded to assemble the wooden parts to see if everything fit. I first put the bolt into the center hole with the big washer, then put the little washer and the nut on the other side. When the nut is not completely tightened, the frame can be adjusted and turned. I put the 19 inch dowels through the holes on the inside pieces, and the 20 inch dowels through the holes on the outside pieces. This will probably look way too big, but it will all work out in the end.
Step 5: Staining
It's looking good so far, but to take it to the next level, I decided to put a dark stain onto the wood. If you like the wood the way it is, you can skip this step. I used a two in one stain/sealer.
Wear rubber/latex gloves and a safety mask
Before I began staining, I covered my work surface with plastic protector. A garbage bag would also work. I opened my stain with a flathead screwdriver and started applying thin coats onto each side of the wood. If you see the stain start to clump up around the edges, just smooth it out with your brush so you can avoid sanding later on.
For the dowels, I found that the best way to stain them was to line them up together and brush the stain on that way, then I turned all of them to the unstained side and repeated that step. I am not an expert stainer, so if you know the right way to do it, let me know!
Once everything was the way I liked it, I put the lid back on the stain with a hammer, making sure to put a paper towel over top so that any stain in the grooves didn't splatter and get all over me. After the stain dried, I noticed that I didn't really need to sand that much. I only sanded inside the holes by wrapping a pencil with sandpaper. If you notice that the are dark uneven clumps of stain, simply sand and do another coat.
Step 6: Cutting, Pinning, and Sewing
While the stain is drying, cut a 42'' x 16'' piece of fabric with a 3/4 inch seam allowance.
Main Body
Start by folding the edges over once, then fold over one more time as shown so that the raw edge is completely hidden. Pin as you go. I started by doing the edges of the long side first, and then the shorter side. Sew with a straight stitch all along the side closest to the un-hemmed main fabric part.
Tabs
Next, cut out four 5''x1'' pieces of fabric with seam allowance. Hem as shown above, then fold in half and sew the two 'legs' onto the top of the main body fabric. I placed my tabs 2 inches from the top corner on the short side, then one for each corner. If that was confusing, look at the final product pictures. The fabric bits connecting the body to the top dowels are the tabs.
Step 7: Pinning and Sewing the Bottom Part
Now that the main body has been hemmed and able to connect to the top dowel, it is time to make it connect to the bottom dowel. I measured 16 inches from the small side then marked where that was. I then marked 4 centimeters back from that line. (Sorry for the unit switch). I repeated this with both sides. I then folded the four centimeter marking in half so I had a two centimeter flap and sewed along that line with a straight stitch. (The sides I sewed together were the sides with the hemming). I put my spare dowel piece through the pocket to make sure it fit, then repeated that same step with the other side. If it doesn't fit, use a seam ripper and redo the stitch. The two pockets should be about 10 inches apart.
Now it is time to check and see if the stain has dried if you stained your wood. If it is, sand the holes and re-assemble the record holder with the fabric. You will probably notice how the bottom and the sides sag and the holder falls over when records are placed into it. This is why we will add tension to the fabric. While the fabric is still on, run your fingers along both of the bottom sides of the fabric until the fabric is taunt on both the bottom and sides. Pin where this is and sew from that point in a straight line using a straight stitch. (Ignore my crooked stitch). Hopefully the pictures should clarify this.
Step 8: Final Touches
To finish it off, I turned the whole contraption upside-down and added some canvas to the feet so it wouldn't scratch up the floors. To do this I used contact cement. This is completely optional.
If you so desire, you can use wood glue to stick the dowels in permanently, but I chose not to so I could store it more easily and wash the fabric if it gets dirty.
Please feel free to let me know if you made this, have feedback/questions and whether or not you liked this.
Thanks for reading!
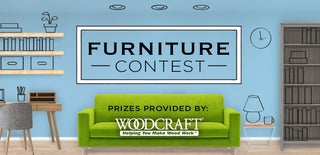
Participated in the
Furniture Contest 2017
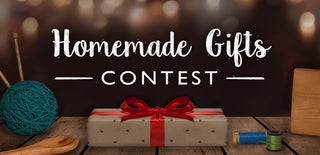
Participated in the
Homemade Gifts Contest 2017