Introduction: Kayak and Canoe Cart (Boat Trailer)
In this instructable I show you how you can build your own proper kayak caddy with leftover aluminium scraps. You can of course just take this as inspiration to build your own caddy out of any materials available to you like wood, steel or PVC pipes. This is a fun project, however you atempt it. And if you use recycled materials you do something good anyway.
Materials you need:
- 20x40mm Aluminium profiles.
I have always leftovers in my shop, but there are also a lot of offers on ebay. People take apart a machine and are leftover with a lot of profiles that they sell cheap. Short pieces are perfect for this application. I didn´t even have to cut anything. If you want to buy new profiles I can reccomend motedis.com in Europe. They are very cheap, or in the US 8020.net
- Carpet or foam for the cushion.
- Screws that match the core of your extrusions.
- 2 Wheels bigger than 15cm or 6inches.
- A solid axle. I used threaded rod instead.
- webbing brackets
- zip ties
- Hair Pins
Tools you need:
- chopsaw (they cut aluminium fine)
- cordless drill
- bandsaw (they cut aluminium fine)
- automatic centre punch (manual works too)
- some pliers
- some screwdrivers
Step 1: Plan Your Build.
I started by laying out some profiles to visualise how the cart would look like. Two uprights, two rods going from left to right, and two supports for the boat itself. I put a 20x60mm piece in the middle to stiffen up the frame. Obviously you could put anything there to make it stiff.
Then I used a marker to roughly mark the places where I needed to drill holes. These profiles can take an M5 thread on the inside which makes it easy to connec them.
Luckily I didn´t have to cut anything, but if you do, you can just use a chopsaw. Carbide teeth cut aluminium fine and can make thousands of cuts. The more teeth you have, the finer the cut. Mine has about 60.
Step 2: Drill All the Holes.
I marked the holes propperly by measuring them with a ruler. A caliper is even better. Then I used a centre punch to mark the location. This allows the drill to grab into the right spot without wandering off. I drilled 5.5mm holes for M5 screws to go through into the next profile.
In metal, you should first pre-drill with a smaller drill and then use the final size. I went from 3mm to 5.5mm. That is because the centre of a drill does not actually remove any material. So on a 3mm drill that diameter might be 0.2mm which it can push aside, but on a 5mm drill, that could be .5mm which is harder to get through. So always pre-drill.
You can use a countersunk bit to clean up the sharp edges. Gives a nice finish.
Step 3: Checking All the Holes.
You should have 4 holes each for the pieces going from left to right, and one 12mm hole for the threaded rod. If you don´t have a 12mm drill you can use a stepped drill bit. You can of course improvise if your plan is different.
Step 4: Thread the Holes.
The profile cores can receive M5 threads. To drill them, I chuck up an M5 spiral tap into my cordless drill. This is much faster than doing it by hand. Aluminium is soft, so the forces are not as big as in steel. Spiral bits are much better and safer to use than regular bits than you get in the hardware store, but both work fine.
I only buy HSS taps over Carbide. HSS theoretically does not last as long as Carbide, but Carbide is so brittle that you will likely snap it off by accident at some point. That is very difficult to get out. Chance of success maybe 10%, so your part is ruined.
Use plenty of oil as lubrication. I use sewing machine oil for pretty much everything in the shop. It is great stuff without any drawbacks.
Step 5: Assemble Your Frame!
So far we drilled holes and tapped their counterparts. Now its time to assemble the frame. Its like LEGO or Ikea. Fun and easy.
I used zinc coated screws, stainless might be better, but I am not sure. You will be fine with either. Stainless screws have the tendency to cold weld when you insert them. They are also much softer than zinc coated steel. Stainless does not rust quickly, but it does eventually and it has worse mechanical capabilites and is more expensive. Chose whatever you want.
Step 6: Adapt to Problems.
I noticed that the boat supports were not stiff enough. The force of the boat could potentially have ripped them off, because they were only fixed to the frame at one point. So they needed some cross braces. After a lot of debating, I just picked up a piece of flat alumium sheet metal and bend it into position. It magically took shape and stiffened everything up. Then i clamped it to the frame to mark where to cut it and I also drilled holes for screws.
You can cut aluminium on your bandsaw. Use some lubricant though. Bandsaw blades are not made of carbide, they are just steel. Steel is harder than aluminium, so it does cut, but not for very long. I used old blades for this and next time I cut some fine wood, Ill get a new blade. They are only 10$ or so.
Step 7: Finishing Touches.
End caps really tidy up these aluminium structures. If you don´t have any, you can also file the edges smooth with any metal file. Takes a few minutes, but also works well.
These webbing brackets are meant for tarps I think on trailers and range rovers. I get them on ebay, but I belive in some countries you also get them in hardware stores. For the straps, I used 4m long ones. My friends can cut them to their desired length later.
Step 8: Add Carpet for Protection.
This green carpet was lying on my shop floor for a long time. If you don´t have any carpet you can get scraps for free at any place that sells carpet. You can fix them with zip ties. Zip ties are just as soft as any kayak, so they won´t scratch it. Tape is also possible, but it degrade with heat and time.
I cannot recommend foam, because it easily breaks. Especially with sunlight. Insulating foam is not made for use in the sun.
Step 9: Add the Wheels!
My wheels came from an old gold trolley. I had them lying around for 5 years and I am glad I finally got to use them. Buying such wheels is kinda expensive, so its worth looking for any wheels on the scrap yard or at an old BBQ.
The wheels had 12mm holes and the aluminium profiles had holes big enough to slide a 12mm threaded rod through them. If your axle is bigger, you can just tie it to the outside of your frame with hose clamps. They are very strong and easy to use.
The threaded rod was secured with nylock nuts to stop it from sliding. Those nuts fit very tight and don´t vibrate loose. Which is a nightmare on a cart.
Use plenty of grease on the entire shaft and the wheel. Especially also at the ends. I used a few washers with grease in between to isolate all the moving surfaces. That makes it less likely to bind. The wheels are attached with split pins. There are better pins available that you can remove without tools, but not in my hardware store.
Step 10: Admire Your Work!
I hope you are happy with your results.I am keen to see some pictures!
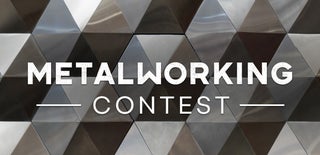
Participated in the
Metalworking Contest