Introduction: Keg Stand Burner
I needed a decent burner and stand for my Mash Tun that I am making so I had a look around for some off the shelf ones and none of them seemed to be very good or large enough to support the keg.
They also seemed to be very flimsy, and these are suppose to be for commercial use? really?.
So I figured I would make one my self using angle iron and a mig welder, I didn't have a mig welder but it was a great excuse to spend £400 ;-) I have also never mig welded before so I wanted to give it a go, previously I have welded using an arc welder which is hard to get started. Mig welding is suppose to be fairly easy to do, much easier than arc welding.
Step 1: Materials and Equipment
Materials
4 x 1.5 Meter lengths of 2.5mm thick 25mm x 25mm angle iron.
4 x Plastic feet to fit the size of angle iron
1 x Can of high temperature paint, or stove / BBQ paint.
1 x burner, I had to buy one with a stand to get one at a price i liked and the size i needed
Equipment
Mig welder, you could use an arc welder or other welder
Welding gauntlets
Welding mask, i got a decent auto darkening one when i bought my mig welder.
I also got a welding jacket to protect my arms while welding and cutting
An electric mitre saw that can cut steel, or be good with an angle grinder.
a wire brush
some methylated spirit and a rag
an electric drill with a drill bit for steel in the size for the screws, for me this was a 6mm bit.
Grind wheel or angle grinder with grinding blade
a screw driver
Safety goggles
Tape measure
Pencil / Sharpie Marker pen
Riggers gloves
Welding clamps and Magenets
instructbles t-shirt is optional, but cool ;-)
Step 2: Cutting, Measuring and Preparing to Weld
Ok for this part you will need to make sure you are protected, make sure you wear decent gloves, i used riggers gloves and wore my welding jacket, and goggles to protect my eyes.
I did all of the cuts using my Evolution mitre saw which can cut steel, I felt a little wrong as I have never used a saw like this to cut steel but it said I could do it so I did.
I worked out previously how large I wanted my burner, my keg is 40cm in diameter (roughly) but i also wanted to use the stand later for a copper Still at a later date which I have also worked out how large I can have it.
so the inside width I set to 45cm or 450mm, I need 2 square frames this width, one to support the keg and one to support the frame and keep it ridge. So i cut 8 x 45cm Pieces.
I also worked out the height I needed including the keg that it would be comfortable for me to work with, minus the height of the keg left me with 40cm or 400mm. So i cut 4 of them.
I made sure I labeled up each of them with a sharpie so i knew what part what what.
with the remaining pieces I cut up 3 about 10cm long to support the keg, and one that would come out and have a piece welded to the end to bolt the end of the burner to.
Now I have them all cut to length I then cut a 45 degree angle on the end of each frame piece, so they will fit together nicely in a frame shape.
using the bench grinder I put a slight angle on the metal for the weld to go in to, when the 2 pieces are put together it should give me a nice v to weld in to.
so a quick recap
8 x 45cm (450mm) pieces with a 45 degree angle on each end for the 2 frames
4 x 40cm (400mm) pieces for the legs.
3 x 10cm (100mm) pieces to support the keg
the rest will form the part for the end of the burner to bolt on to.
Step 3: Welding and Drilling.
Before welding make sure the are you are welding is clean from dust and rust using a wire brush, you also need to have bare metal and no paint to weld on to.
I have never mig welded before this is the first time I have ever done it, I watched a few youtube videos on mig welding before I tried this, and only ran 1 bead on test material before I started. The key is to take your time, make sure you have a comfortable grip, and don't move to quickly you want the metal to heat up enough to bind to the weld. You should see a little bluing on the metal when you are done, this means that it got hot enough to penetrate enough. It took me a couple of welds to get comfortable with it, and unlike an arc welder I didn't have to start an arc and try and maintain it I could just get on with it. I managed to get all the welding done in about an hour and a half including a lot of cigarette breaks.
Using welding magnets to hold the pieces together I put in a spot weld just to securely hold it, my magnets were cheap and didn't seem very well. Once it was spot welded I ran a bead through the V I had created on what would be the underside of the frame.
Clamping the legs to the first frame I could run a bead down the sides and around the top edge on what would be the underside of the top.
I marked up the legs from the bottom (where they will be on the floor later) about 10cm (100mm) which is where I want my 2nd frame to sit. I had to man handle the frame in to place, and using a hammer tap it so it was inline with all the marks. Then I ran a bead of weld on the inside of the leg to attach them to the frame. This second frame will keep the shape of the stand and stop it from flexing or buckling.
Now its just a case of welding on the supports for the keg to sit on and also for screwing the burner in to.
I had to extend the plate on the front of one of the supports that the burner will screw in to because the burner would not have been level.
Making sure to measure where I was going to drill the holes for the bolts on the burner i used a HSS drill bit and an electric drill. tip for drilling in to metal, you don't want your drill bit to slip do use a center punch to put a dent where you want your hole and your drill bit shouldn't slip. Also you need to cool and lubricate the drill bit some 3 in 1 oil is perfect for this.
Step 4: Painting
Before painting I ran the wire brush all over the whole frame to remove any loose debris such as paint or dust or slag from the welding.
I wiped it over with a rag soaked in methylated Spirit to get all the dust off from brushing it with the wire brush.
Gave it a coating of High Temperature paint, the key here is to keep the can at least 8 inches away from the piece you are spraying, use short bursts and shake the can between sprays. Do this in an area you are not going to accidentally spray something you don't want to. I did this on the lawn near the bonfire.
Slide the plastic feet on the bottom, screw on the burner and its done! I am very pleased with the result, now all I need to do is finish my mash tun, an instructable for this will be coming soon.
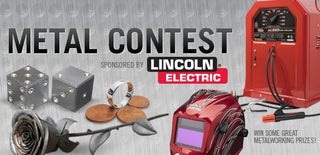
Participated in the
Metal Contest