Introduction: Laser Cut and Engraved Coffin
I made a coffin for the monster high dolls my little niece loves so much about a year ago.
Was quite crude from thin MDF and decorated (to cover the imperfections) with some decals I printed.
Now it was time to use my new toy to create much better looking one:
As you can see it is not just the standard cutting job.
Could not find any box maker to suit this project so everything was done by hand in Inkscape.
It was only when I assembed the parts that I realised I did not count for the kerf of the laser - stupid mistake but did not spoil the results too much as the parts were meant to be glued together anyway.
After all it is a kids toy and without glue it won't survive long ;)
Materials and tools needed:
Access to a laser cutter with engraving capabilities.
Wood glue.
Maybe a sponge to clean the carbon dust from the engravings and cutting areas.
A toothpick or some wire in similar diameter for the hinges.
Super glue, rubber bands or clamps to hold everything in place while the wood glue sets.
3mm thick plywood, birch, MDF, acrylic or whatever material you decide to use for the coffin.
Skillset required:
If you know how to use wood glue and how to get the files to the machine you are good to go.
Nothing special needed for this one :)
Time required:
On my machine each engraving round takes about an 90min, the cuts are not worth to mention for the lost time.
That means you should plan for 90 minutes for each half of the coffin plus the time for the assembly.
With good glue it should be doable in under 3 hours.
Step 1: How It Was Done
First I create the basic shape for the coffin parts and made sure the angles would fit.
Next and most time consuming step was to create some finger joints to make assembling much easier and to give the glued joint more stability.
After tracing some decals and creating others as raster engravings I decided the raster engraved ones provide a much better look.
Takes much more time in the machine but compared to a vector engraved image you just get the full picture instead of just outlines.
The first assembled model did not look too well considering it was not just a box but a coffin - the finger joints just did not look right.
So I added even more engravings to give the joints a more color pattern.
I was actually quite pleased with the outcome until my niece dropped the bomb that she would prefer some hinges this time to make it look even more real :(
Back to the drawing board...
I considered the weight and my options of hinge placement and could only use two hinges on the long ends without destroying the entire design.
They are a bit oversized compared to normal box designs but all is designed for just 3mm playwood and the coffin should survive at least the first week of playtime without repairs LOL
Step 2: How to Do It on Your Machine
I don't know what laser cutter / engraver you use but unless it supports raster and vector engravings you will have a hard time.
I converted my china laser box to run on Arduino to overcome the problems, you can find the Ible for this in my profile.
You need quite a bit of build space for this one, my machine was on the limit here but the standard 230 by 300mm models should be enough.
Start with a test of the cuttings on a piece of cardboard or paper first to get your alignment right or just use a sheet to cover the entire build area.
For the real job on the plywood I suggest this order:
1. Start with the engravings of the side panels at low power and do two passes.
This will prevent a lot of the overburn and gives a much nicer finnish IMHO.
If your machine supports it you can of course do it at normal power levels with pulse control - I used 20 pulses per mm on the engravings.
2. If you want the slightly darker joints engrave the extra blocks for the joints now, otherwise skip this step.
3. Last but not least cut the parts out.
There are multiple layers inside the provide SVG file.
Each layer corresponds to one print job.
All non-raster objects are paths only so the Inkscape plugin I use can recognise them as vector cuts.
Some better machines support different colors to define the jobs, I don't have a controller to support this, so you might have to change the colors to your needs if you have problems using it the way it is.
Step 3: Assembling
There really is little to no chance at all to get the parts together in the wrong order, so I did not make a picture gallery for it.
Please don't blame me if you used a panel from the top part on the bottom part of the coffin ;)
Take these pics as a guide on how to get it together, there is little chance to get it wrong as the parts are designed so they only fit without a gap in the right place.
As you can see it is the classic finger joint design, so the pieces should fit into the slots and you add some glue to hold them there.
To avoid rubber bands or similar it might be a good idea to first secure the parts with a drop or two of super glue and then to add the wood glue once all is aligned.
Here is a closeup of the hinges.
As you can see the toothpick is sitting flush - just push it in and cut it off on both ends with a sharp knife ;)
When all is glued together and set it should look a bit like this:
I used a drop of super glue here and there to hold the parts together and once happy added a line of wood glue along the inside of the joints.
The hinges just got a drop of glue and were pushed into the holes.
Inside the hinges a piece of a tooth pick is used to keep metal out but of course you use a bit of stiff wire or similar if you don't trust your toothpick.
With a tight fit they are surprisingly strong.
If you want something more durable then use pieces from an old bicycle spoke as they are the same diameter and should fit right in.
Secure with some glue from one side only so if something happens you still have the other side to glue a replacement on.
Step 4: Download
Here is the SVG file I created.
As said it contains multiple layers, each layer contains the images / paths for one job on the machine.
If you want to combine multiple jobs into one, like doing the engravings and cuttings in one go, then simply make the corresponding layers visible and select all parts.
My apologuise for not supplying a file in different colors for the jobs but as I can not use them I did not bother.
Maybe someone who made this coffin on such a machine would be so kind provide his modified files instead ? ;)
Attachments
Step 5: Possible Options to Use / Mount
It was intended to be a coffin with lid and hinges.
That does not mean you can tweak it any way you like.
For example leaving the hinges out (and the holes for them), turning the bottom part upside down and use it as a coffin bed.
Some of the decals might need to be turned 180° if you like the bed idea better.
As single pieces they also make a nice display on a shelf your your favourite doll.
And of course there is always the option of adding some fancy padding.
After all a bed should have it, but I left step out so my niece can experiment a bit.
Step 6: Disclaimer
For this project I used Monster High decals and logos that I collected quite some ago by taking images of the packing materials.
I do realise the images might still pose a copyright problem in some areas but as it is meant for private use only and all commercial use is excluded I hope I am forgiven for this one.
After all you can not make a monster high coffing for your niece if there is no moster high stuff on it :(
All engravings have been converted to laser engravable raster bitmaps in BW and would be pretty much useless for any other purpose.
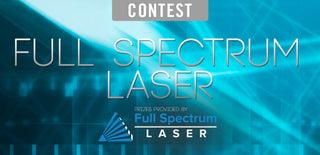
Participated in the
Full Spectrum Laser Contest 2016
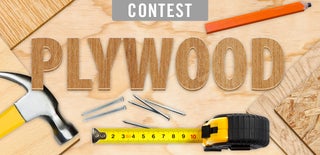
Participated in the
Plywood Contest