Introduction: Lathe Tail-stock DRO. ( Showing Phases of the Design Process)
I had a job to do that required 24 items drilled and rebored to the same depth to a close tolerance. The dial on the handle of the tail-stock, though accurate, is a faf to zero every time I started a new hole, I needed a DRO (Digital Read Out) which can be zero'd with the touch of a button.
First picture is my final design but I thought I would write up the development stages as they give an insight into the design process.
Second picture is trial one, third picture trial two,
both of which are described below.
Step 1: Design Criteria
I wanted to do this as cheaply as possible...nothing new there!
It needed to be simple to attach and remove from the lathe.
I wanted to do it with as little modification the the lathe as possible.
It needed to be more accurate and easier to zero than the scale on the tail-stock quill.
Originally I intended to use an existing vernier caliper but as it was 150mm long it got in the way of the handwheel, I has a choice, cut that one down in length or.....
... spend £7 on this 100mm vernier , I find it difficult to destroy perfectly good equipment so buy this I did. I will need to modify and fit it when it arrives, the 150mm one will be used to get the job done in the meantime.
Step 2: Mounting the Moving Parts
I knew I had a plastic ring mount knocking around the workshop that I could clamp onto the outside of the tail-stock quill, (I think it was for mounting a grinder to a drill press nose), this could be just as well done with a block of hardwood as per the drawing.
I fitted the clamp with the screw threads uppermost so that they would be available for attaching the vernier.
Step 3: Mounting the Fixed Parts
I was rather lucky with the design of my lathe in that the tail-stock casting is basically square with nice right-angles to work from. I used a piece of aluminium that was just thinner than the quill clamp washer, drilled a hole to fit the O/D of the washer. I then bent the bracket, drilled and threaded the tail-stock for an M4 countersunk screw through the bracket just to make sure there was no movement. The tapped hole is the only modification to the lathe.
A small clamp plate was then made to hold the front end of the vernier in place.. it was then I realised that the backlash on the quill was going to be a problem....read on below.
Step 4: Backlash in the Quill
DRO trial and mod Backlash from Rog8811 on Vimeo.
The rotational movement you can see in the quill puts a bending moment on the scale of the vernier, this will damage it very quickly so I came up with a quick fix which was a piece of squared tube peened onto the anvil of the vernier and two tubular nuts that the modified anvil slides up and down between.
I then went ahead and clamped the slide of the vernier to the bracket and drilled and bored my 24 items.... no photo's of that as I was in "work mode". Suffice to say the zeroing was easy to do and the depths were repeatable BUT the square tube was a bit rattly in between the tubular nuts and the vernier is a bit exposed stuck out at the side of the tail-stock.
Another redesign needed, though as a one off setup to do a job this was a complete success!
Step 5: Final Design
I found a piece of hard plastic that I cut, drilled and tapped to go onto the quill clamp ring . The next step would be to cut a slot for the end of the scale to drop into then the vernier can run along the top of the tail-stock.....awaits arrival of vernier :)
Step 6: The Last Leg
The 100mm vernier arrived... and I chopped off all the bits I didn't need.
The plastic block had its slot machined across it and the remaining anvil was machined to fit the slot.
Step 7: OK, the Last Last Leg :)
I modified the bracket as I no longer needed the bit sticking out.
The vernier was stuck in place with double sided tape and the following movie shows how the setup easily deals with the backlash.
DRO Final set up from Rog8811 on Vimeo.
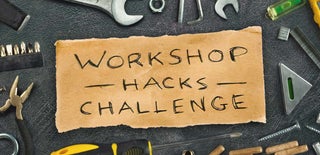
Participated in the
Workshop Hacks Challenge 2017