Introduction: Leather Belt With Removable Buckle
I've always been a fan of leather gear. it feels strong and real. It reminds me of history, of armor and of airplanes and of mail bags. Leather is rich with context, with feeling. and, growing up, leather has always been too expensive for me. I'd had designs, growing up, of getting my hands on a hide and turning it into a satchel, or a suit of armor, or a wallet or a bomber jacket. But as a youth, leather isn't something I could have afforded.
Fast forward too many years, and it's still something that isn't easily within my reach. But I'm going to reach anyway! I decided, some time ago, that I was going to make something from leather, and it just needed the right excuse. This year I've got that excuse. my family and I are going to the local ren-faire, and we're going in costume. And I need a belt.
My design criteria are pretty straight forward, though they introduce some interesting problems.
- The belt should be wide. preferably 2" wide. This likely isn't period correct but it's what Hollywood likes to show us and it's what we've come to expect of ye olde tymes. Plus it's freaking cool!
- The belt will be tooled leather, so the leather source must be veg tanned and preferably undyed (i'll be doing the dying myself thanks! :P). I'm actually unsure if you can tool dyed leather, as it should also be finished against moisture
- It needs a buckle that doesn't look like it was purchased at Spencer's. No triforce, no captain America shield, no Cocky. It should also not, for aesthetic preference, be just a generic loop and pin.
- The belt has to look good on a pirate, or be nautical themed.
- It has to look decent with the rest of the costume, which limits color choices.
- Make the buckle removable. a late choice on my part, this not only means I don't have to sew, but it also means i can market the belt to a wider audience who may not like my choice in buckles. Honestly the lack of sewing isn't a big plus to me, as i like stitched leather's aesthetic, but for you guys it might very well be a plus!
The first problem to overcome is that there is only one kind of belt buckle that fits a 2 inch belt. A kilt buckle. All of these feature Celtic knot-work and or some rather strange references to Scottish history. There where a few that'd work, but they just weren't what I wanted. Instead I chose to find the biggest belt buckle that I could and will notch the bet so that it fits into the 1.5 inch loop of the buckle.
With that decided, I shopped around for a nice plain buckle that wasn't covered in floral patterns or Celtic knot-work or modern designs.
Bill of Materials:
- a 2" x 50" belt blank. I got mine from Springfield Leather Company
- a belt buckle. This is the one I bought: https://www.amazon.com/gp/product/B00CTS6OOM
- a stamp set for leather working: you only REALLY need a few tools but they come in sets and they're cheap.
a swivel knife. you can technically get away with using a scalpel or something but this tool was designed for cutting leather and doing it gracefully. (it's easier than it looks to learn and hard as hell to use right... >.<) https://www.amazon.com/Tandy-Leather-Craftool-Adj...
- a mallet. wood, rubber, even a small hammer. something to hit your punch with. it shouldn't be too heavy. you don't need to hit too hard and you'll be doing a LOT of hitting, so lighter is better.
- a flat, sturdy surface. i use an old cutting board. a lot of pros use a chunk of granite.
- a snap set and tool. https://www.amazon.com/General-Tools-1265-Fastener...
- leather dye. I bought a set of Tandy dye years ago at a flea market. This is the set I have:
- it's cheaper to buy just one color if you know what you want.
- a gallon ziplock bag.
- a leather hole punch set. I borrowed a set from a friend. I know, I cheated
- a boxcutter or xacto knife.something sharp and long enough to cut through your leather
- thick nylon cutting board. (WILL get damaged)
- Optional: leather sheers. colossal super sharp scissors. you can do anything these can do with a box cutter. it's just a lot easier to use the scissors.
So far, not counting shipping, I've spent less than 50 dollars. and most of that was the cost of tools and gear. The belt material has only cost me 19 bucks, Not counting replacement snaps (which I didn't even bother to source cheaper since i had them already.)
Step 1: Design
The Canvas:
Before we can start designing our tooling we have to think about how big the belt is, both how wide and how long, and set up our drawing area. I want a 2 inch wide belt, and it has to fit around my waist, which is.... considerable. normally i wear my pants where any sane individual would, just above the hips. but as this is a costume piece, wearing the belt higher is necessary. My belt measures 44 inches long from buckle to hole. there should be some extra length for a few adjustment holes. Add three inches for more holes, plus at least one more for rounding the end, preferably two with a belt this wide. The belt buckle will require you to fold the leather, so add the length of the fold to your canvas. In my case it was also 3 inches. this makes my total belt 44+5+3=52 inches long. which is a problem! most belt blanks are marketed in 50 inch long pieces. However, I got lucky and my belt was shipped a full 64 inches long. I'm not sure if the standard is to get it 'close enough' or if they accidentally sent me more leather than they intended, but it really worked out for me.
I'll be doing my drawing in Krita, a free drawing program, but you can also make a paper strip. With paper just make the strip as long as your belt blank. In Krita I set up my canvas to 100 DPI, and then made it as long as my blank. In either case, you will probably be aided in making the canvas wider than the actual blank, so you can draw 'off' the belt and draw shapes that are not constrained by the canvas. I made my canvas 600 pixels tall, putting two inches of canvas on either side of the belt, then drew the belt's outline on the paper to show me where it actually ends..
Designing
Now that we've got a sizable canvas to work with, let's think about what we want to put on it. The only real restrictions are in color and theme. I want a nautical themed belt and it has to fit well with a bright blue shirt with yellow trim. In my head I pictured something cyan, maybe with natural color for a two tone effect, and that's what I tried to make (you'll see later that my dye betrayed me and I ended up with a much MUCH darker blue than I wanted.)
I am a colossal geek and whenever I make something like this I always start thinking about DnD. The fantasy designs and the magic items always stoke imagination. So when I decided on a nautical theme the first thing to come to mind immediately was 'kraken'. A belt wrapped in tentacles and giant eyes. I could work with that.
There's two general ways you can go about drawing something like this on a belt.
- you can draw really small and try to fit everything on it.
- you can draw large and try to fit most of 'it' on your canvas.
The former has a few options. You can either draw what you're trying to draw realistically, which will leave a lot of white space, or you can stylize it and leave off realism to fill most of the belt. Something like Celtic knot or a squarish, more Aztec pattern perhaps. This can be really cool, but it's not what I want. I want the belt to feel like a window into another realm, to feel real. To not only look like an octopus or squid but also feel like a creature that size could actually exist.. so, the other method!
This part of the process requires artistic talent and I really can't tell you how to do it. Get an idea in your head and put it on paper! I've included some examples of designs I might have gone with, along with the design I settled on. don't worry about being super precise. Leather has a low resolution so mistakes kind of smudge away. Just try to make smooth curves and straight lines.
Once you have a design you are happy with, get it in paper form. I shouldn't have to tell you how to print out a picture and cut and tape it together :P
i'm providing my final design for this particular belt for you to use to make your own, but i'd rather you not do so commercially.
Step 2: Casing and Bringing to Working Moisture
When working leather like this there is a technique called Casing which is designed to work moisture deeper into the leather to allow for a longer working time before it has to be re-wet. It's actually pretty simple to do. Take your leather and run it under the tap until it's all wet, then leave it out to dry. When the leather reaches a half dry point where it's still dark but not super wet, roll it up and stuff it in a ziplock bag. Leave it in the bag overnight. Most sources suggest to leave the leather in the fridge at that point to prevent mold growth. When you come back for it the next day, the leather will be thoroughly saturated with moisture to it's core, allowing for easier working and a longer time before the water in it evaporates away.
Now would be a good time, before you wrap it. to scribe your lines with a stylus or ball point pen. Lay your pattern down over the belt and trace it lightly with the tool so it leaves impressions in the surface for you to cut later. You don't have to press hard, and I wish I had pushed lighter.
after you've cased it you will want to preserve the moisture as best you can, so have plastic wrap ready to wrap over most of the belt to trap moisture. only unwrap what you're working on until you are finished tooling.
Step 3: Tooling the Leather
This is the bulk of the project, and it will take time. First you have to let your leather section dry to a workable moisture level. You do NOT want it just soaked. For best impression you want the leather to dry until it has almost recovered it's original dry coloration, but still feels cool to the touch. Many suggest touching it to your cheek. it's a hard balance to reach (and I'm no expert) but if you do it right your tools will easily burnish the surface of the leather, leading to the darkening that adds depth to your tooling and improves the look. Unwrap a small section of the belt at a time, maybe a foot or less (I tend to work in about 8 inch segments on a belt this wide.) and leave the rest wrapped up so it doesn't dry out. If your leather gets too dry you can re-wet it with a damp paper towel, but you'll have to let it get back to that nearly-dry, cool to the touch state before you start working again.
Start by taking your swivel knife and carefully cutting out the outlines you scribed in the previous step. You can actually do this while you are waiting for the leather to get to a workable moisture level if you are feeling particularly impatient.
The first step to tooling your leather, once your lines are cut and the leather is at the right moisture level, is to go over the outlines with your beveler. This is a very small stamp that looks like a wedge with a crisscross pattern on it. It only takes a small bump with the hammer to make a decent impression, you don't have to go crazy. On the flip side don't be afraid to hit your leather. Go around the outside, facing the slant away from the 'object' you are tooling. in my case an octopus. you want to lower the background around it so that it pops out.
After you have finished the outline, look over your design and find any spots that need to be lower inside the outline. for example, if I was making Celtic knots, some of the lines go under others, and would have to be lowered. In my case, I have many MANY suckers to round off. Going around the edges of these, and paying attention to what should be in front of what, will go a long way in making the tooling pop. At this point you may want to try using a shader tool instead (I actually highly recommend switching tools. using a tool without a texture on it will help differentiate the background from the foreground.). I have a teardrop shaped tool that is good for lowering areas smoothly, and a flat wedge that can be used to sculpt the straighter bits. I've found myself using the tear drop more than any other tool with this belt.
After Ive worked the inside of the octopus and lowered all the steps, I'll go back to the white space with a textured stamp and hammer it down. this isn't strictly necessary, but it provides a texture that helps differentiate the octopus from the background, so think about your design! i was very tempted to use the basket weave tool instead of the textured tool, but my basket weave tool is rather cheap and doesn't make good impressions. Instead I dug through my tools for the other teardrop shape that has the same texture as the beveler and used it for the whole background. I also have a very small tool with a similar texture that I used to get into hard to reach places.
When hammering you can also kind of fade the effect by hitting lighter and lighter as you go. A light tap hammered a lot will still produce a noticeable effect. Play with some scrap! The shader can also be used by hand instead of using a mallet. There where a lot of points where I found it was easier to push the tool into the leather and slide it around instead of hammering on it.
Step 4: Cut Ends and Notches
after your tooling is finished you can round off the ends in whatever fashion you desire. I brought both of mine to a long arrowhead point. Rounded but with a tip.
I also took the time to cut out the grooves for the belt buckle to fit in. measure three inches in from the end of the belt, where it will fold around the buckle. find the center of the belt at this point, and make a mark 3/4 inches to either side of it. measure 1/8th on either side of these marks to find the corners of the notch. mark out each notch, and cut them out.
Step 5: Slick the Edges and Punch Belt Holes
Now is time to burnish the edges. You take your leather slicker, which looks kind of like a honeycomb, and you rub the edges till they are smooth and burnished. Start with a gap that's too big and work your way down. You can always go over it again with a smaller gap but if you use a gap that's too small it'll compress the tooling on the front (which you can see in my belt... >.>). Maybe you want to do that on purpose! It does give a sort of 'edge' to the surface of the belt.
My belt has eleven holes in it, and thankfully they all use the same size hole. There are four for the snaps that hold on the buckle (two holes for front and back of each snap) and seven holes for actually wearing the belt. Put the right die in your hole punch and set the belt over your cutting board. The punch will right through the belt and likely DEEP into the cutting board, so you don't want to do this on your kitchen table with nothing underneath. And probably not with your wife's favorite cutting board.
There are marks on the pattern I produced for where to place my holes for the buckle prong. To determine their location for yourself, we need to start with the waist measurement of the intended user. As i stated in step two, my waist measures 44 inches wide. This means that my 'main' hole needs to be 44 inches from the fold of the leather, minus the width of the belt buckle. Place a mark at this location in the center-line of the belt. I used an awl and poked a small hole. From there measure every inch in each direction and add three more marks on either side, for a total of seven. or however many suits your fancy!
Step 6: Snap Holes
The other four holes are a little more critical. They need to be placed so that they line up with one another. The key is that each pair of snaps on either side of the fold is the same distance from the each other. If the surface you are punching into is smooth, like a wood block, this is pretty easy. Just cut your holes on one side, fold the belt over, and use the punch to score the back of the leather for placement of the holes on the other side. My surface, a thick nylon cutting board, is NOT smooth, and leaves a textured surface on my leather that I didn't want on the 'right' side. instead I punched one set of holes, and then the other, using the first to make sure the second was lined up.
Their placement on the length of the belt belt isn't super crucial, but their placement in regard to one another is very important. Make sure there's enough space from the fold line for them to function, perhaps half an inch. Like the buckle holes, these will go down the center of the belt. it's important to consider the consequences of deviating here. Obviously you're free to place your snaps wherever you like, but if you place them too close to the edges you wont be able to fold up the belt's end and slip it through the buckle loop, which is the key to getting a 2 inch belt into a 1.5 inch buckle. You might be able to place them somewhere other than the center-line of the belt, but look it over long and hard before you punch any holes for the snaps.
I cut the holes for one snap first, the one closest to the end, and then folded the leather on itself to find where the hole would end up on the 'right' side. Using an awl i punched a hole through the leather to find the hole on the front. With the hole marked on the front I'll flip the belt flesh side down and punch the matching hole. After I've got one set of holes i perform it in reverse. Figure out where the second snap should be, and punch the hole into the side of the belt that faces outwards. Line up the two holes from before, and use the awl to transfer the new hole to the other side of the fold. Unfold, flip flesh side down, then punch it out.
Step 7: Dying
This step is pretty straight forward, though some might say I'm doing it 'the wrong way'. Honestly this is the first time I've dyed anything! First wipe down the belt with rubbing alcohol to strip it of oils it might have picked up from your hands and work surfaces. Then grab a q-tip and dunk it in the dye. Evenly work the dye over the areas that should be dyed. Most of the colors that came with my kit go on evenly without much fuss, but the blue dye becomes rather splotchy if you aren't careful about overlap.
After the dye dries, go over it with a scrap piece of soft cloth, like an old t-shirt, and buff out the extra pigment. Redye as needed to get the results you want.
I don't have any good pictures of the process, but I CAN show you a few mistakes. first, use gloves, this stuff is sticky when it dries and builds up pretty thick. Worse, it'll leave marks on everything, including your new belt.
If you make a mistake, don't fret, just try to carefully sand it off with high grit paper. I used 200 grit. It wont be perfect but it'll be a start.
The q-tips I used had a paper core and that was a mistake. they soak up a LOT of dye. I recommend getting ones with a plastic rod instead of paper. even more, I recommend getting the q tips that are wedge shaped and not made of fluff. It was a pain in the but to dye the detailed bits. You could also try a brush i guess. DON'T mix colors in the bottles. try these: https://www.amazon.com/G2PLUS-Disposable-Eyeliner...
I haven't used them but they look like they'd work well for both detail and not soaking up a lot of dye.
I also learned that you should not connect your outlines to the lines inside the design. any area that will color change should be isolated from the rest of the design by a few millimeters of uncut leather. Otherwise capillary action will suck the dye right into the other half of the design and you'll end up with color where you don't want it.
Step 8: Conditioning and Finishing
After dying you will definitely want to finish the leather with a compound of some kind. I intend to use Resolene on my belt, but I don't have any and cant afford to buy any just yet XP
Finishing will add gloss to your project (unless you pick one that's designed to be matte!) and will also deepen and darken all the colors.
When I get my hands on some I'll finish the belt as soon as I can and then post more pictures.
Step 9: Install the Snaps
This step is pretty straight forward. You'll need four caps and two of each of the socket and stud. And of course the setting tool. My kit was REALLY simple and has a two sided 'anvil' for setting the whole thing in, and a stamp (that is frankly too short to be practical) to crush the post on the snaps and rivet everything together. It's pretty hard to mess up, so just read the instructions that came with your tool. Make sure to keep the sockets to one side and the studs to the other, so you don't end up with two studs or sockets on the same snap set.
Step 10: Show Off
Slip on your belt buckle and snap it all together and you're done! feel fancy. Feel accomplished! Feel like you need to make six more so that the last one looks professional!
Jokes aside I'm really happy with how this came out. Now comes the full disclosure. This is the second thing I've ever made out of leather. The first was a little design I did to play with the leather stamps and learn them right. I know there's a lot that could have been done better if only I had the skill, but for a first time attempt I feel like I aimed high and did alright. And enjoyed the process too! I'm going to wear it to the local ren-faire and then i'm going to maybe make another! (and maybe add some more pictures. :P)
If you liked my instructable please vote for it in the Leather Contest!
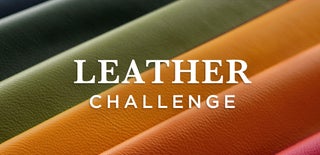
Participated in the
Leather Challenge