Introduction: Loudspeaker Design by Trial and Error
"Now I need to make my own pair of loudspeakers!" I thought, after finishing my Serious Amplifier. "And if I can make a decent amp, I can surely do this." So I jumped into the world of speaker design and building, expecting a nice clear path to a pair of speakers that would exactly match my wishes. Little did I know.
What followed were countless hours of designing, making, listening, getting lost, enjoying, failing, learning, and starting all over again. I discovered how speakers turned out to be wonderfully straightforward, and yet delicate and subtle machines with lots of possibilities and lots of constraints.
In this Instructable I'll try to summarize the process I went through and what I learned about making loudspeakers in general, based on my own successes and failures and on what I learned from others.
Please give this Instructable a vote in the Audio Contest, if you think it's worth it. Thanks!
The result, a pair of rather uncommon but surprisingly nice sounding speakers, is described in this Instructable: Serious Speakers on a Budget.
Step 1: Why the Trouble of Making Your Own Speakers...?
Firstly, because there's magic involved. The basic idea of (most) speaker drivers is beautifully elegant and simple: a lightweight coil in a permanent magnetic field starts oscillating when a music source (an alternating current) is connected to the coil. When mounted in an enclosure, a million different things happen at the same time.
And that is when we speak of magic. Although speaker systems are thoroughly engineered, the available science and mathematical models can't quite catch (or predict) your listening experience. So in the end, you'll need your ears, your intuition, and some guts to make your speakers really awesome. You must add something personal in it, something of your own. If nothing else, this will make you fall in love with your own speakers :)
Secondly, because building your own speakers is literally worth the effort. I spent €250 on components for both speakers, resulting in a pair of speakers which are comparable to €750+ speakers if I had to buy readymades.
Thirdly, it's not that hard. You can make speaker building as easy or as hard as you want. A simple driver and a small cabinet, combined with a few hours of trial and error, can give a pretty good result. After that you can (and probably will, because it's simply great fun) decide whether you want to go on.
Finally, just because you can. You're a Maker or want to be one, so c'mon.
For me, building loudspeakers involves everything I love about making and tinkering. Woodworking, electronics and modelling software, testing and improving, and a result which is very much worth the hard work you put in.
Step 2: Keeping the Costs Acceptable (Not the Audiophile Way) - Tips and Tricks
When searching for information about loudspeaker building, you inevitably bump into "audiophilism". For audiophiles, the making of, purchasing of and listening to audio equipment is close to a religious experience. Audiophilism is the search for the ultimate listening experience, aka Audio Nirvana.
To get to this audio nirvana, audiophiles are vulnerable to two major temptations:
- An oversized interest in the use of rare materials and high precision specifications of parts. This results in a nice sound, and also in very extreme sums of money being spent on literally each single part of a loudspeaker.
- An ardent eagerness to be in charge of every little aspect of audio, such as opinions, measurements, conclusions, confusions, facts and fables about everything audio. This leads to endless discussions about the use of silver as soldering medium, the layering of capacitors, snubbing of capacitors, surface of cables, etc. etc.
These discussions are held between people who are often experts on audio equipment. As a novice in speaker building and with a background in engineering, I spent a lot of time figuring out which discussions were about major improvements and which merely concerned details. Here's a summary of some findings:
- Online audio calculators are not perfect. Use them wisely. Use the calculator's outcomes as a starting point, and then start deviating from the calculated values and listen to the speakers.
- The size and shape of the cabinet are a huge factor in the sound of ported speakers.
- Experimenting with the length of ports is very, very useful.
- PVC tubing (for drain pipes) works fine as a port in a speaker.
- Experiment with the amount of filling/damping material in the cabinet.
- Pillow filling (Ikea!) is great as damping material.
- Free wool carpet samples are perfect for acoustic isolation on the inside of the cabinet.
- 18mm chipwood (€15,- for a sheet big enough for three cabinets) is very suitable for building prototype cabinets.
- Speaker wire of 1.5 mm2 is good enough for internal wiring of the speaker.
- Ready-made crossover filters work fine and are easy to tweak.
- The ratio of costs between woofer, mid-tone driver, tweeter and crossover can be 2 : 2 : 2 : 3.
I choose a US$15 woofer and midrange driver. The tweeter was US$25. So I'm willing to pay around US$ 38 for my crossover.
In short, I tried to keep my loudspeaker design as simple and clean as I possibly could. Instead of spending money on parts, I spent time (and chipwood) on six different cabinets. I truly believe that was a smart choice. (More about "my simple and clean design philosophy" is in Step 8, Cabinet design. I used Occam's Razor in peculiar ways :s)
Step 3: Pre-building Choices - List of Materials
The premise
My initial idea was to make a mini-array of four small full range drivers. In hindsight, that was an odd choice. But I purchased eight Visaton Full Range FR10 drivers, four drivers per speaker. I wanted to build speakers using simple (affordable) drivers in an array with a minimum of filtering. I found two reasons to do this:
- By keeping the design simple, I hoped to minimise the losses and distortion of the music source. Perfect components do not exist. Every component in the speaker causes loss of and distortion in the signal. Reducing the number of parts also reduces the distortion.
- By distributing the audio signal over many small drivers instead of a few bigger ones, the load per driver is smaller. The distortion of drivers becomes bigger when the power increases. So dividing the load over as many drivers as possible decreases the load per driver, and hence the distortion of the audio signal decreases.
I limited my options for cabinets by choosing for a "vented box", aka bass reflex speakers. The reasons are simple. Bass reflex speakers are the most common type and very thoroughly documented and engineered. Besides that, a vented box, especially with a two-way driver set, is a forgiving design. Small flaws through building or miscalculating only have a limited effect on the sound quality.
After making and listening to 3 different cabinets or so, I realised that a different set of drivers might have given me better results. But drivers are the most expensive part of loudspeakers, so I decided to stick with what I had. I did add a pair of tweeters (Visaton DT94), though. And because of the extra tweeter, I also needed a two-way crossover.
Materials per speaker
For drivers and crossover filter I used:
4x Visaton Full-Range Speaker 10 cm (4'') 8 Ohm FR10/8.
1x crossover filter 3000Hz Visaton HW2/70NG (8 Ohm)
To tweak the cross-over filter, you need some extra parts:
Visaton air-core coils. I ended up using one 3,3 mH coil of 1.0 Ohms. (3,3 mH is a big coil. It acts as a low-pass filter for the "woofers". More about that later.)
Capacitors of various capacities, MKT type. Suitable values ranged from 2.2 to 20 uF.
A set of various 10W resistors (eg. 2.2 Ohm, 5.6 Ohm, 12 Ohm, 22 Ohm)
For the cabinets I used:
- 1 sheet of 18mm OSB chipwood, 1,22 x 2,44 meter.
- Fluffy filling. Pillow filling works fine and is much cheaper than audio-grade PolyFill.
- Lining for the inside panels of the cabinet. I got some wool carpet samples for free at a local store. Instead, acoustic foam can also be useful (available at a hardware store). I tried both and chose wool carpet in the end.
- Wood glue and screws (4 x 45 mm)
Step 4: Investigating - Resources
The amount of information on loudspeaker design is nothing less than overwhelming. It's just a little bit too much.
Here's a list of resources that I used at one moment or another.
Here's what others did. DIY loudspeakers (and kits)
Paul Carmody's DIY Audio Projects
Troels Gravesen DIY high quality loudspeaker kits (and lots of resources)
Lautsprechershop.de. This site is in English. Lots of kits and inspiration. Lots of theory as well, but not very accessible.
Free plans for loudspeaker kits.
Fantastic custom-built speakers. Just to drool over...
The DIY audio forum. Large forum, thousands of Q & A's and DIY projects.
Noahw's classic Instructable on Loudspeaker building.
Loudspeaker design in general
Article about the "Thiele-Small parameters" of drivers. This is a must read if you want to understand a little of what the loudspeaker calculators are doing.
DIY Audio (and video). Extensive website on loudspeaker design, with calculators.
Linkwitz Lab. Thorough and technical yet readable articles on loudspeaker design.
Very nice article on port tuning by Troels Gravesen. About the limitations of vented box calculators.
Get stuffed. Article on lining and filling of cabinets.
Listening to loudspeakers. Describing what you hear makes it easier to compare different speakers.
Boxsim modelling software. Great little app to model a loudspeaker. Configure cabinets, crossovers and filters and create frequency-response diagrams. Windows only.
About configuration of multiple drivers
MTM configuration (Midrange - Tweeter - Midrange driver)
Article about D'Appolito configuration (MTM with adjusted crossover)
Online calculators (use them wisely)
All the calculators you need in one place. Dutch website (in English).
Another set of calculators by DIY Audio & Video.
Manufacturers (the affordable kind)
Visaton website. Lots of components, lots of kits, lots of information.
Dayton audio. Lots of components, lots of kits, lots of information...
Finally, a link to an article about the why's and won'ts of the use of spikes under loudspeaker cabinets. It gives a good insight in the world of audiophilism and how hard it sometimes is to separate the sense from nonsense.
Step 5: Getting a Grip on Dimensions - Using Online Calculators
Once I knew which drivers I was going to use (the Visaton FR10), it was time to get a grip on the cabinet. Where to start? How big is big enough? How does a cabinet sound that is too small, or too large?
This is where the box-size-calculators come into play. The box size depends on certain characteristics of the driver. These characteristics are called the "Thiele / Small parameters".
In most cases, the TS-parameters of the driver are provided by the driver's manufacturer in the spec sheet. When you don't have the spec sheet but do know the model and manufacturer, chances are that you can find the T/S paramaters online in a database via a google search. If that also fails, you can use a measuring tool such as this "woofer tester" (this one is rather expensive, but I'm sure there are cheaper alternatives on AliExpress :)).
However, please bear in mind that the box-size calculators are not oracles. It appears that different formulas are used to compute the box-size, and hence different calculators provide different answers. Check the screenshots of two calculators I used to calculate the size of a vented (bass-reflex) box for one Visaton FR10 8 Ohm driver:
- mh-audio calculator: 10,98 liters
- DIY Audio & Video calculator: 12,27 liters.
That is a 10% difference :). I then guessed the "optimal volume" (if there is any) for my FR10 driver would be somewhere between 10 and 13 liters. So now I could start building boxes!
Step 6: Start Simple: Box, Driver, Tube, Filling, Lining
A friend of mine made the straightforward rectangular box with one port in the pictures. Volume: 7.2 litres.
I fitted my FR10 driver into his box to experiment with the following attributes:
Length of the port.
Just cut off a series of lengths of PVC tube and fit them into the box. It is easy to hear the difference between the different tubes. By closing off the port, you can really hear (and appreciate) what a port is doing for the low frequencies. In this cabinet, a 7cm port (3.3 cm diameter) worked best. The working of ported loudspeakers is described here (wikipedia) clearly.
Filling.
I tried different amounts of filling (pillow fluff) in the cabinet. The quality of the sound is surprisingly dependent on the density of the stuffing.
Too little or no filling: The speaker sounds harsh and noisy.
Too much filling: The speaker sounds muffled. The lows are there, but midtones seem to disappear.
(The use of filling is a smart trick to make the cabinet seem larger for the sound waves inside the cabinet. When the sound travels through the fibres, the speed of sound decreases. This way, lower frequencies with larger wavelengths still fit within the cabinet.)
Lining.
Lining is used to prevent echoes from bouncing back and forward in the cabinet. However, it is not always necessary. Attach carpet or foam on the inside of one of the cabinets and compare it with a cabinet without lining. I lined the walls of one of the cabinets with acoustic foam. With lined walls, the speaker seems to sound a bit "easier", less noisy. In another cabinet I used carpet as lining. I believe this works better than the acoustic foam, though the difference is subtle.
Not all walls need to be lined with foam or carpet. In the final design, I only lined the back, top and bottom panel.
Step 7: Learn From Other Speakers - Listening, Comparing, Taking Apart
Comparing your speakers to other speakers is one of the most rewarding (yet confronting) and informative things you can do.
Comparing speakers between themselves
I started my project with building two slightly different speaker-cabinets. I compared them by listening to them at the same time and one by one (using the balance slider on the computer to switch from one speaker to the other). It surprised me how clearly audible the difference was between two speakers that only differed in volume and geometry.
After that, every time I built a new cabinet or crossover, I replaced the lesser sounding version with the new one. So each time, I compared the new stuff to the best I had made until then.
The rewarding thing was that almost every time, the new version turned out to be an improvement on the best version yet. It gave me the confidence I needed that I was learning and that there was room for improvement in the design.
Comparing your own speakers with different speakers
This is great fun! Set up your speakers next to another pair. Just to feel good, I bought simple bass-reflex speakers in secondhand stores for a few euros. And that did make me feel good :). When comparing to other speakers, you can really distinguish whether your own speakers are good at and what could be better.
I also went to friends to compare their (diy) speakers to mine. One of them makes single-driver quarter wave type speakers which are totally different from mine, but then you learn about the differences in speaker design and the quality of the sound that comes with it.
I learned a lot by listening to other speakers, both similar and very different from my own design. Each time you compare your speakers to another pair, you learn something about the sound and performance of your own speaker, and bit by bit you get a grip on the spaghetti incident of variables that define the sound of your speakers.
Most regular speakers sound boomy (loud bass in a limited frequency-range) with sharp high tones. Better speakers have a more balanced sound, with lows, midtones and highs clearly audible and distinguishable.
Reverse engineer loudspeakers - take them apart
Look for left-over loudspeakers or buy simple loudspeakers in a second-hand store. Listen to them, and then... take them apart. Look at the drivers, the cabinet, type of filling and the crossovers. You'll probably find that the quality of your own speakers' cabinet and parts is a lot better than the ones you have just taken apart.
Learning to listen
By comparing speakers, you'll start listening more closely to what you actually hear. Initially, I was sceptical about the differences I would hear between "normally priced" speakers and my diy speakers. As it turned out, the difference is easy to hear, yet sometimes difficult to describe (this is a nice article on how to describe the sound of loudspeakers).
The downside of listening to many different speakers is that you can become very critical and demanding of your own loudspeakers. Perfect sound and perfect loudspeakers do not exist. Every speaker you hear has its own charms and limitations and no loudspeaker will ever match the sound of live performance.
Step 8: Cabinet Design
When you browse through the pictures, you'll find all the different cabinets I made. I added comments with the pictures to explain what I did.
What I learned about cabinet design
- First and foremost: Keep it as simple as you can. The simplest design is the easiest to measure and judge, simply because there are fewer variables in play. Aka Occam's Razor.
(I feel a bit awkward here mentioning Occam and the similar "less is more" principle, because I totally violated those rules at the very start of the project. I chose to design a speaker with no less than four drivers. When that didn't work out, I added an extra tweeter instead of subtracting two drivers from the equation. That's not exactly simplification, is it? But hey, I learn by making mistakes!)
- Place opposite panels not parallel to each other. The sound from the "skewed" cabinets is much clearer and the different instruments and frequencies are better recognisable. Skewed boxes sound better than rectangular ones. Period.
- Place drivers as closely together as possible, especially the midrange drivers and the tweeter. The "woofers" are placed above and below the midrange drivers, about 42 cm apart. They are filtered around 700 Hz, so the shortest wavelength they produce is about 47 cm long. Just enough to avoid most interference.
- Put the tweeter in between the midrange drivers, as closely as possible. This is called an "MTM" configuration (Midrange-Tweeter-Midrange). It makes the speakers sounding "lighter", less weary.
- A special version of MTM is called a D'Appolito configuration, which has adjustments in the crossover. Here is a readable discussion on MTM and D'Appolito configurations. This is a thorough article about MTM speakers by D'Appolito himself for Seas (manufacturer of gorgeous but expensive drivers).
- Experiment with different volumes for the cabinet, starting with a volume provided by an online calculator. Smaller volumes/compartments tend to sound better in the midrange frequencies. Larger volumes sound lower (more bass) but dampen the midrange. Those tend to sound a bit muffled. I ended up with compartments of about 10.4 liters, a bit smaller than predicted by the Thieme/Small calculators I mentioned earlier.
- I made several cabinets with compartments of different volumes, hoping to combine the best sound aspects from the two compartments. I ended up with a cabinet that was divided into two equal compartments. It is Occam's Razor in another way. The different compartments make the drivers behave a little different, which makes the speaker sound uneasy and too demanding.
- Experiment with the length of the bass reflex tubes. The length calculated by calculators is an approximation and usually a bit too long. I mounted a 44 mm tube connector on the backside of the baffle (see the pictures) to experiment with different lengths of tubes easily.
- Sink the tweeter into the front panel ("baffle"). That takes some effort with a router, but it is worth the trouble. The tweeter and midrange drivers will be on the same plane, which avoids interference and makes your speakers sound more precise an less noisy.
Step 9: Modelling Your Speaker - BoxSim and Frequency Response Diagrams
After building and listening to three different cabinets or so, I started to get a grip (although slippery) on what was happening in a loudspeaker and why.
When I started tinkering with the crossover and added a coil and capacitor in series with the drivers, it occurred to me that I knew what I was doing, but only in a qualitative way. For instance, a coil works as a low-pass filter and a cap as a high-pass filter. In numbers though, I couldn't predict with which frequencies the components would do their work.
The maths needed for calculating impedance in networks is a bit tricky. (And that is a mild way of putting it!) This is where Boxsim comes to the rescue. Windows-only, but still a killer freeware app for designing loudspeakers. A good tutorial is over here.
Using Boxsim, I strengthened my grip on the loudspeakers I was designing. Learning to use the program and entering characteristics of the cabinet is a bit of a pain, but very much worth the effort.
Once this is done, you can start tinkering with crossover components and the effect they have on the frequency-response diagram. And how helpful it is! Like the Thiele/Small calculators, however, what BoxSim gives you is an approximation. It's not real, it's a mathematical model. But it does point you in a direction.
Step 10: Crossover and Filters
A well-designed crossover can improve the quality of speakers dramatically, so this step is not to be underestimated.
On the other hand, a crossover causes distortion and damping. The amplified music signal travels through the crossovers' components before reaching the drivers, each component adding a little disturbance to the signal or removing some information. So you'll want a crossover design that has as few components as possible with each component of a good quality to keep the deformation and dampening as small as possible.
As with all components, audiophiles can spend a fortune on a crossover network. 700 euros can be spend on one (1) 100 uF capacitor. If you think this is exceptionally expensive, then take a look at these crossovers :D !
The crossover I ended with consists of the following parts:
- 1x Visaton 2-way crossover @3000 Hz for 8 Ohm drivers: €25,00
- 1x 3,3 mH / 1,2 Ohm air-core coil: €15,00
- 1x 33uF Visaton bipolar capacitor: €3,00
- 3x 10W resistor: €0,60 each
Total costs for the crossover are €45. The five drivers costs €75,00. I think 45:75 is an appropriate ratio.
I used Boxsim a lot to configure the crossover. For me, the beauty of Boxsim lies in the crossover editor. Changes in the circuit are immediately processed and plotted in the frequency-response diagram. Of course, you must be able to read a frequency characteristic in order to interpret the changes you've made in the crossover schematic. This article gives some explanation, just like this one.
Adjusting the crossover is fun to do. The components are small and easy to replace or remove. And that is nice after the hard work of building and adjusting wooden cabinets.
I tested the crossover and adjustments in the same way I tested the different cabinets. I made changes to one of the crossovers and then compared it with the unaltered speaker. So again, I listened to two different speakers, using the balance slider to listen to each speaker individually.
I used electric wire connectors to hook up the parts and 1,5 mm2 speaker wire to connect the crossover to the loudspeaker and between parts if needed.
Listening to changes in crossover design is similar to listening to different cabinets. Most of the time, you'll notice the difference immediately when you play music. Describing the difference you hear can be harder, because it is often more subtle. But, as with everything, you get better at that after a while.
Step 11: Wrapping Up
I've been listening to music all my life. I love it. Music can make me happy, comfort me, focus me, strengthen me, and make me dance.
The speakers I made are the best I've ever owned and listening to music feels better than ever. I can enjoy listening to music so much that I forget about time, forget about a tv-show I wanted to see and just remain listening.
It took me over a year and a half to design and make the speakers that are now in my living room. I've learned more than I could imagine beforehand and have enjoyed the making and tinkering from the start. I actually feel a bit sorry now that these speakers are more or less finished.
(although there might be room for improvement in the crossover design... :D )
If you've ever even remotely considered building your own loudspeakers, I hope that this Instructable can help you to start the project. For me, it was the best project ever, and extremely rewarding.
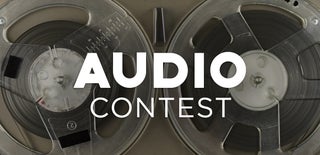
First Prize in the
Audio Contest 2018