Introduction: Make Beautiful Solder Joints
The quality and design of project boards has become so good in recent years, that I almost feel bad putting them together. In this guide, I'm going to show you a simple soldering technique that can make the back of your boards look as nice as the front. You'll learn how to make perfectly smooth, consistent solder joints that look impossibly tidy.
In full disclosure, I learned this technique from Saar Drimmer, who runs Boldport and sells stunning kits (some shown above, with permission) through his club. I don't work for them or make any money from them, I'm just a fan.
But as a fan, I had this dilemma of loving his board designs so much that I didn't want to destroy them with my haphazard soldering. The boards in his photos looked immaculate, like the soldering had been done by a robot.
It turns out he was just using a technique I hadn't seen before (also described in his video here). I suspect the technique predates Boldport, but I refer to it as Boldport Style. If there's already a name for this I should know of, please correct me.
Step 1: Create a Standard Through-Hole Solder Joint
First, you just need to make a standard, through-hole soldering connection. Nothing fancy. No special solder or soldering iron.
For what it's worth, though, here's what I'm using (linked out to Amazon):
Hakko FX-901 Portable Soldering Iron
Love this thing. Heats quick, gets hot, solder anywhere. I use rechargables.
Hakko CHP-170 Flush Cutters
THE critical tool for making this technique work, though any flush-style snips will work.
Lead Free Rosin-Core Solder
Because it turns out lead is toxic, so why not?
Brass Wire Sponge
Cleans without water. Keeps your tip hot. Looks like C-3PO's... er, ashtray.
Safety Glasses
All those clipped leads have to go somewhere. Better it not be your eyeball.
If you need any guidance learning how to solder, Adafruit has a great guide. I also love the EMSL guide on how NOT to solder.
Step 2: Flush Cut the Joint
Next (with safety goggles on your face!), trim the lead or wire you just soldered down as flat against the board as you can go. Basic wire cutters won't get you all the way flat, that's why the flush cutters are key.
If you've received any instruction on soldering, or read any books on the subject, you've likely been warned not to aggressively cut the solder joint down all the way. For all practical reasons, they're right. If you're soldering up something that has a critical task and people depend on it working, don't monkey around with fancy soldering tricks. You could damage the board, weaken the joint, and generally ruin someone's day.
That said, if you're soldering up a blinky robot badge (like me) and don't want the backside poking your shirt. Or maybe you've got some artsy, portable project that people are going to fondle at Maker Faire -- then by all means, live dangerously and flush cut that sucker in the name of beauty.
Step 3: Reheat Joint With Dab of Solder
Now, the trimmed joint may be flat, but it's not pretty until you briefly reheat it and introduce just a touch of solder.
Poke your iron back into the joint just long enough to see the solder liquify, then add just the smallest amount of new solder back into it and pull your iron away. This will take some practice to not go overboard with the solder or leave your iron in too long.
Ideally, what your left with is a smooth, shiny dome of solder that reminds me of a mini upholstery tack. My guess is that it has something to do with the surface tension created by adding new solder and the lack of any central element for it to gather around.
When you do this across every solder point on a board, the cumulative effect looks really sharp. And because every joint is built up from the same flat starting point, I find it much easier to get a consistent look from point to point.
That said, pulling off this trick essentially means soldering every connection twice. For a few dozen connections, it's cute. For a few hundred, it's a chore.
Step 4: Remove Flux
And since we're being all type-A about making the board pretty, take a moment to soak a rag in some rubbing alcohol and scrub away at the little pools of flux left behind on each joint. With the solder points all smooth now, it's really easy to scrub away at the board without hurting your hands or getting the rag caught on the leads.
For what it's worth, I also have a can of stuff called Flux Off, but I don't recommend it. It's nasty stuff with all kinds of warnings on the side. Especially with the smoothed out solder connections, rubbing alcohol and elbow grease tends to get the job done just as well in most cases.
If you liked this tip, be sure to give me a vote!
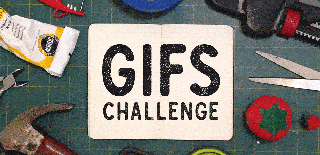
Runner Up in the
GIFs Challenge 2017