Introduction: Makita Battery Storage and Carrier
Most power tools nowadays are battery based, meaning that many will dedicate them to one brand, to use the same batteries with many different tools. This however also means that you end up having batteries around that you need both to store and transport when using them.
For me this is Makita batteries and in an attempt to get more organized with my tools and batteries, I wanted to make something that I could use to store the batteries as well as use to easily transport the batteries when I have to take them with me.
So in this Instructable I will describe how I designed and made a battery carrier for Makita batteries.
Supplies
Tools
- Access to an FFF 3D Printer
- Pliers
- A hobby knife
- Clamps... Lots of clamps :D
Materials
- Some PETG filament or similar
- Glue e.g. B-6000, Epoxy or similar
- Electrical tape or similar (Optional)
- 2 small pieces of 5mm thick rod/pin/etc. (Optional)
Step 1: Idea and Design
NB. If your are not interested in my thoughts behind the project or the design and modelling of it. Then fell free to skip this step, no hurt feelings ;P
Before starting the project I defined a number of design goals for the carrier, to guide me through the process.
- It needed to be fast and simple to make/produce
- I wanted it to be parametric, so that I could easily change the number of batteries it would hold
- I didn't want to do a lot of post processing
To make the 3D model I decided to use Fusion 360.
I started by making a derivative of my Makita battery connector, which is the part which actually interfaces with the Makita battery. I am using derivatives as it allows me to make the base part once, and the reuse and modify it as needed for the individual projects but still maintaining a link which makes it possible to update and improve the battery connector without having to repeat these steps for all my projects that use this connector.
It will be more apparent why this approach is valuable, In some of my other projects.
I will try to update this with links once I complete writing the Instructables for my Makita battery to TS100 adapter and a variable bench power supply using Makita batteries.
After having added my derivative and making the adjustments needed, I then proceeded to model the left side of the carrier making sure that it would be wide enough to accommodate the hole for the handle when the carrier only holds 2 batteries (On on each side).
To make the carrier stand on its own, I added a simple foot/stand to the bottom of the connector and at the same time added a few alignment holes to the back.
Then I added a user parameter which defines the number of sets of batteries that the carrier should hold. With that defined I could then add a dynamic back plate, which would change its width depending on that number, as well as a pattern of the battery connector with the foot and alignment holes to make the necessary copies.
This makes it trivial to change how many batteries I want the carrier to hold, as it will automatically adjust the model depending on the value that I define.
The final touches were just to add a centered handle to the back plate with a nice fillet.
Step 2: Preparing for Assembly
The parts that needs to be printed are fairly easy prints.
You will need to print two sides of the carrier, which is symmetrical, so just print the same twice.
You can find the 3D model files for a carrier that holds: 2, 4 or 6 batteries here: Makita Battery Carrier
NB. You will need a larger then average build plate for the carrier for 6 batteries, around 300 mm or more.
I would recommend using PETG, ASA, ABS or similar material for printing the parts.
Although I suspect that PLA would work fine, I am just unsure of its longevity.
To print the model successfully you will need to add support in the battery connector part of the print as shown in the pictures.
Also depending on the printer you are using, you might want to use a brim to avoid warping as these are big flat parts, and therefor could lift in the corners.
Once printed, simple remove the supports using some pliers and knife and clean the backside of any residue, glue stick etc. so that it is ready for gluing.
Finally if you want to add a bit of extra strength and help with alignment, then cut 2 small pieces of 5 mm rod, bolt steel etc.
Make sure to do a test fit of your pieces before starting to glue. Nothing hurts more then starting to glue and realize that the parts a just a fraction to tall
Step 3: Putting It All Together
The assembly of the carrier is straight forward.
First add an appropriate amount of glue. I had originally decided to use a two component adhesive, but ended up using some B-6000 as it proved to be plenty strong but easier to apply.
The important part is that you get coverage, and make sure to get it close to all the edges, so that it closes up nicely and doesn't leave any gaps
Before pressing the two pieces together I added the pins, which in my case was two small pieces from an old 5 mm aluminium rod I had laying around, but it could just as well have been two bolts with the heads snipped off or similar.
The pins are completely optional as they are mostly for alignment and to give some additional strength.
Once pressed together add clamps, as many as you have or can fit, what ever comes first.
That is it, just wait for it to harden completely before putting it to good use.
If the prints turned out a little rough around the handle part, then I would suggest taking some electrical tape or similar and just warping it a couple of times.
If you have any questions, constructive feedback or comments, fell free to post them, and I will do my best to get back to you.
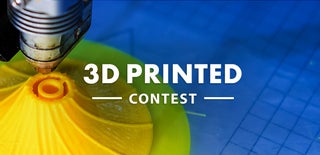
Participated in the
3D Printed Contest