Introduction: Miata Hardtop Rolling Rack That Stowes in the Trunk
What is that old saying? Necessity is the mother of invention? Not that I would be so bold as to take credit for this rolling rack design, but I did modify it to fit in my trunk. So maybe necessity was the mother of adaptation this time.
I recently moved into my very own apartment, which is great, but I no longer have a yard in which to leave my hardtop, white trash style. Since it's summah summah summah time, I had to find a place to stow my top, and ended up with a 5' x 5' storage unit. These measurements are generous, probably to the outside of the corrugated aluminum dividers :-P. Not wanting to end up with a 'painted into a corner' situation, and to make the most of my space, I found plans for a rack for my Miata's hardtop online. This was also a necessary plan because my unit was inside a storage warehouse, down a long hall, pretty far to carry the awkward top with a friend. The rack is primarily PVC pipe and fittings cemented together as shown, with casters epoxied on. There was one final issue to figure out: my unit was about 40 min away, and I wanted to be able to drive there with a friend / boyfriend / helpful person in the Miata, instead of taking a second car for the rack.
Thus, I decided to break the rack up into cemented modules, and use sheet metal screws to attach the modules at the storage site.
Step 1: Materials and Tools
To make your very own, search for "Miata hardtop rack pvc" on google or pinterest. The dimensions I used are here (I didn't think I could include the photo here since it is not my own): http://forum.miata.net/vb/showthread.php?t=382066
You can make the above rack with five 4' sections of 1-1/2" PVC, with a little left over. Don't forget to add 0.75" to each dimension shown for the fittings, and don't forget to make little 1.5"-long pieces for places where two fittings butt together.
Materials:
- Five 4' sections of 1-1/2" PVC pipe
- PVC bonding cement
- Scrap wood or MDF for the feet
- Casters - I bought the largest rubber-wheel size so I could roll over thresholds more easily
- Hardware to attach casters
- Sheet metal screws
- Epoxy
Tools:
- Saw
- Drill
- Clamps
Note: My front feet did not work out. Please read about my proposed fix in the last step.
Step 2: Sawing
Not much to say here, just cut out the pieces you will need. Here was my strategy:
I cut the first two PVC sections into 45.625", 9", 2.875", and 2" pieces. The rest were as follows.
3rd section - 30.5" and 27"
4th section - 27", 22", and 4 x 1.5"
5th section - 22" and 2 x 14.125"
Step 3: Dry-Fit Up and Choosing Modules
Next, I put it all together according to my reference photo, and tried to imagine the best way to break it up into modules. I will try to explain the best I can here, but the photos on this and the next step will help.
I broke the bottom H- shape into it's three obvious components, meaning the fitting pieces at the junctures stayed on the side modules.
I kept the diagonal pieces separate, since they were the longest sections, and just fit inside my trunk.
I cemented the short piece, fitting, and long piece to make each of the two side uprights. I kept the back horizontal piece of PVC separate.
Then, I made the remaining top parts (3 pieces of PVC and 4 fittings) one module.
Step 4: Cementing the PVC Parts and Adding the Feet
I cemented my PVC modules starting from the bottom and working up. When I cemented the lower fittings for the diagonals, I put the whole thing together to make sure the angle would be cemented correctly.
Be careful not to cement any of the modules together!
Then I measured and cut 4 rectangles that would fit the casters from MDF. I drilled the holes, and when the modules with the feet were done, I epoxied them on (this did not work out so well for the front seat, so please see my note in the last step).
Step 5: Drilling and Assembly
Then it was time to throw it all in the trunk and drive to my storage place!
After fitting it all together, fire up your drill and put a hole through the fitting and pipe at each connection point. It might be nice to have a friend help you, if any measurements were a bit off, you might need someone to push the connection together while you drill and add the sheet metal screws.
Next, lay the rack down and add the casters. Set it back up, and you are ready to load it with your top. Stand back and admire your work.
Step 6: Notes
This is where I planned to have a cool time-lapse of my boyfriend rolling it into storage with ease, but the sad thing that happened with mine is that the front two feet broke off at the epoxy joint when he hit the ramp.
My epoxy was pretty old, and took longer to set up than it should have, so that could have been the culprit, since the original directions on that forum used epoxy. However, that is not a very large contact area, and I have to admit I was a little skeptical even when I was reading those original plans.
I have not fixed mine yet, but my plan is to use a hole saw to cut a hole in a second layer of MDF or scrap wood. The PVC will be epoxied into the hole, with much more contact area, and the added benefit of a friction fit.
I will probably make this improvement in the next week or so, as it is getting to be time to put the hardtop back on the car, so look for an update. I just wanted to post this now, so I could enter the cars contest (hint hint, vote vote).
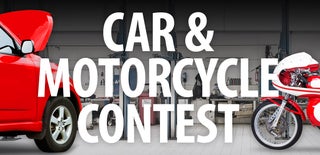
Participated in the
Car and Motorcycle Contest