Introduction: Modern Live Edge Waterfall Coffee Table | How to Build
In this collaboration build between myself (Johnny Brooke of Crafted Workshop), James Wright of Wood by Wright, and Zack Herberholz of ZH Fabrications, we'll show you how to build this Modern Live Edge Waterfall Coffee Table. We built this piece together in my shop a few weeks ago and we each contributed our own skillset to the build. Let's get started!
Also, don't miss the build videos above for a lot more details!
Step 1: Gather Tools & Materials
This build is divided into three main sections: flattening the slab top and cutting the waterfall leg, forging the drawer pulls and welding the leg, and cutting the sliding dovetails and building the drawer. Below are the tools we each used on our sections of the build.
Tools Used On Flattening Live Edge Slab & Cutting Waterfall Leg:
- DEWALT FLEXVOLT 12″ Compound Sliding Miter Saw : http://amzn.to/2ah20gS
- Supermax 19-38 Drum Sander : http://bit.ly/supermax1938
- DEWALT DW621 2-Horsepower Plunge Router : http://amzn.to/2niHu9f
- 8 Inch Jointer : http://amzn.to/2n7JK4z
- MIRKA DEROS Sander : http://amzn.to/2oz4QIN
- DEWALT TrackSaw : http://amzn.to/2nTMqzI
- Festool Domino XL DF 700 : http://amzn.to/2n88S7S
Tools Used On Drawer And Drawer Slides:
Supplied Needed For Drawer:
- 3/4" Walnut 2" X 6'
- 1/4" Plywood sheet
- Wood Glue
Step 2: Cut Leg From Slab and Rip Straight Line on One Edge
I started by removing the length I'd need for the leg at the miter saw. It's a good idea to leave a few extra inches on the leg section to account for any loss while cutting the miters later or trimming the leg to length. I also ripped a straight line on one side of the slab using my track saw.
- Johnny
Step 3: Flatten the Live Edge Slab
planerTo flatten the slab, I used a trick where you remove the guard from your jointer then run the section of the board that will fit over the jointer until that portion is flat. This is obviously inherently dangerous, so do this at your own risk.
With a section of the slab flattened, you'll be left with a ridge of unflattened area. Attach the slab to a flat planer sled, in my case a piece of ¾" plywood, that's longer than the slab with the flattened area of the board sitting on the sled.
Run this through the http://amzn.to/2nZ1dfL until the top of the slab is flattened, then remove the planer sled, flip the slab, then run the bottom through the planer until the ridge is removed and the slab is completely flat. Watch the video at the top of this Instructable to get a better handle on this process.
If you don't have a planer or jointer, you could also flatten the slab with a router sled.
- Johnny
Step 4: Cut Miters for Waterfall & Temporarily Attach the Two Pieces
I cut the miters for my waterfall edge on the miter saw, but this wasn't perfectly accurate. I probably should have used my table saw and a miter gauge in retrospect. After cutting the miter, I needed to attach the two pieces. This is a little tricky, and I'm lucky enough to have a Festool Domino XL, which made quick work of this.
If you don't have a Domino, you could also use splines to strengthen this joint instead, or a metal angle bracket underneath. Considering the table is very low, no one would see the angle brackets.
- Johnny
Step 5: Shape Live Edge and Blend Waterfall Joint
With the two pieces temporarily attached, I shaped the edge of the slab with a spokeshave followed by a random orbit sander. Live edge slabs will usually have some fragile edges that need to be removed so that they aren't damaged later. A spokeshave makes quick work of this.
- Johnny
Step 6: Route Groove for Metal Leg
The reason I only temporarily attached the leg is that there is still some work to be done on the slab that is easiest accomplished without the waterfall leg attached. I needed to route the groove for the metal leg and the sliding dovetails needed to be cut, which will be a later step.
The groove I routed needed to be exactly 1" by 1" and I used a plunge router and a ¾" template bit for this. I made multiple passes, lowering the bit a little on each pass, until I reached full depth, then moved my fence, a square in this case, over until I reached full width.
We also notched out a 1" square on each end of the groove, all the way through to the other side of the slab, to house the portion of the legs going down through the top.
- Johnny
Step 7: Cut Steel for Handle to Length
The forged handles were sort of a last minute idea, so the only material I was able to obtain was ½” zinc plated square stock. The first thing I needed to do was remove the zinc coating, I removed this with a Dewalt Flexvolt angle grinder. I then decided on the length and shape, and removed the excess stock with an Evolution steel chop saw.
- Zack
Step 8: Forge & Shape Steel Handle
I used a NC Tools Whisper Momma forge to heat up the stock. The first step was to flatten out the corners to make a slightly octagonal profile. After profiling the stock I then upset the ends in order to flare them out. And finally I decided to add a slight S-curve to the handles, I did this over the horn of the Rigid/Peddinghaus Anvil.
- Zack
Step 9: Attach Threaded Ferrules to Handles & Apply Burnt Paste Wax Finish
For the next step, I used a Lincoln Electric Powermig 210 to weld threaded ferrules onto the handle, and I ground them smooth with a Dewalt Flexvolt angle grinder. For the blackened finish I re-heat the handles and applied a coat of Johnson’s Paste Wax.
- Zack
Step 10: Cut Steel Leg Pieces to Size & Weld Together
The first step was obviously measuring out the required dimensions. With the measurements in hand, I again turned to the Evolution steel chop saw to cut the steel tubing to length. I then chamfered the ends with a Dewalt Flexvolt angle grinder and welded the pieces together with a Lincoln Electric Powermig 210 welder. After welding, I ground out the welds with the angle grinder.
- Zack
Step 11: Weld Nuts Into Steel Leg
With the leg assembled, it was time to attach some sort of mounting system. I decided to drill two recesses into the leg in which I would weld some threaded inserts.
- Zack
Step 12: Sand & Finish Steel Leg
I hand sanded/burnished the steel leg with 160 grit sandpaper in order to obtain a polished look. The leg was then topped with multiple coats of gloss spray lacquer.
- Zack
Step 13: Cut Dovetails for Drawer
Though this is a detailed step, I do not want to go into great detail as "How to cut dovetails" is its own Instructable here.
- Lay out the tails. I do this with a baseline and spaced out marks in the end grain for where to cut. I do not draw out the angle of the cut as I like them to be organic, but most people like to draw down the face with the angle.
- Chop out the waste. I do this with a chisel, chopping down near the baseline then pairing in to remove the waste.
- With the tails cut, you can transfer the marks to the end of the pin boards, then you can chop out the waste on the pins.
- Test the fit and change them where needed.
Here is a second instructable on speeding up the prosses and making hand cut dovetails faster. Here
- James
Step 14: Cut and Install Drawer Bottom
Before gluing the drawer sides, we need to cut the groove for the drawer bottom. This is 1/4" deep and wide and 1/4" up from the bottom. Normally, I would use a Plow Plane, but in this case, I used a router.
For the bottom, I used a piece of 1/4" Plywood. It is stable and will not expand and contract as much as solid wood. I cut this with a panel saw.
Now it 's time for glue up! I used Bessey Parallel Clamps for this, keeping them just off of the tail. Also, I make sure the drawer bottom slides into the groove all the way around the drawer.
There will be 4 small ¼" X ¼" holes in the ends of the drawer from the groove. I want to fill these with square pegs that I made with a chisel. They have end grain showing so that they will hide nicely in the end of the drawer. Last, they are flush cut with a Flush Cut Saw.
- James
Step 15: Cut Sliding Dovetail for Mounting Drawer
In the first picture, you can see the sliding dovetail drawer glide.
First, we need to make the dovetail in the slide itself. To do this, I clamp it to the bench top with a scrap piece of wood set up as a fence in 1/4" from the outside edge. I will use a Panel saw or a Sash saw to cut down along the fence about ⅛". Next, I use a dovetail plane to cut in the tail along the edge of the piece. I will then repeat this on the other side so that I have a symmetrical tail.
- James
Step 16: Cut Drawer Slide
Now, let's make these slides functional. The piece I last cut the tails into needs to be ripped down so that it is ¾" deep with a dovetail in one side.
To slide on the drawer, we need to cut a ¼" groove in the drawer sides ¼" down from the top. You can use the same setup to cut a ¼" groove in one side of the slide, so that it will leave a 1/4" tongue that can fit into the ¼" groove in the drawer. The picture above should make this a bit more clear if confused.
- James
Step 17: Cut Sliding Dovetail Groove
Now it's time to cut the dovetail groove in the underside of the top. I start by laying out where the grooves need to be to fit the drawer nicely. Keep in mind, the bottom of the groove needs to be ¾" wide and the top of the groove (the part you mark on the board) should be as wide as the thin part of the dovetail you already cut.
Next, I use the dovetail plane as the fence to cut in the dovetails with a saw. I just use some F-Clamps to hold it onto the top, then I can carefully slide the saw along the dovetail plane to cut in either side of the dovetail groove.
With a chisel bevel down, slowly come in and remove the majority of the waste, getting close to your depth but not going over. I will then use a Router Plane to clean out the bottom of the groove and get all the way into the corners. This should take it down to the final depth and allow the dovetail slide to slide into the groove. You can test the fit of the drawer at this point.
- James
Step 18: Glue Up Waterfall Table
Step 19: Installing the Forged Handle
The installation was pretty straight forward--mark out the holes, drill, and screw in place.
- Zack
Step 20: Prep for Finish & Apply Finish
To prep for finish, I sanded everything up to 180 grit using a random orbit sander and also chamfered all of the straight edges using a block plane.
For the finish, I used General Finishes Arm-R-Seal and I absolutely love the way it brought out the deep figure in this wood.
- Johnny
Step 21: Install Metal Leg, Hardware & Drawer
The metal leg was installed using two small bolts that thread into the walls of the leg. The hand forged drawer handles are installed using a few bolts and washers. Finally the drawer slides onto its tracks with a little paste wax added to reduce friction.
- Johnny
Step 22: Enjoy the Finished Live Edge Waterfall Coffee Table!
Hopefully you enjoyed this collaboration build! If you don't already, subscribe to our channels on YouTube using the links below:
We're hoping to do one of these collaboration builds at least once per year, so make sure to stay tuned to our channels for more!
Also, we are auctioning off this piece to cover our costs on this trip and are donating 10% of the proceeds to Habitat for Humanity. If you're interested, check out the auction here.
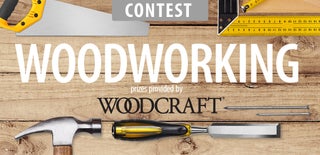
Participated in the
Woodworking Contest 2017