Introduction: Custom Pattern Bookcases
A little while back, I set out to build a bookcase. I wanted to house my books and also have space for things like puzzles, games, and keepsakes. Since they're all different dimensions, standard shelves weren't going to cut it! I grabbed some scraps and made a prototype to quickly explore options and build out my final shelves.
Part the inspiration for how this was made came from a new tool I had access to in a communal woodshop that I haven't used before, the Festool Domino Joiner. My dad always says projects are an excuse to buy tools - sometimes new tools are an excuse for new projects.
The nod to Mondrian (a photo of his work is attached here for reference) wasn't intentional when I first started but it was the first association my husband had when he saw my prototypes, so I explored this style a bit more and the final version isn't a mirror of any of his pieces but does have a resemblance.
Let's dig in to how it's made!
Step 1: Prototype!
I grabbed some scraps from bin and made sets of different length pieces to work through ideas. This created a great system to work through options quickly.
A note on prototyping with thin wood pieces: After trying this on paper with a wooden frame, I realized it was too frustrating to move the pieces around and/or transport the prototype - I basically made a domino set. So I took a small cutting mat and covered it in duct tape, sticky side up. This allowed me to place the wood pieces on the mat without knocking others over and meant if I had to relocate, I could chuck it in a bag and take it with me without losing context. Worked like a charm!
I was able to visualize horizontal and vertical spaces while looking at the pile of books and objects I envisioned the final product holding. As I prototyped, I lined up all my books in the groupings I wanted and measured the length to see how much storage I needed to accommodate.
The final version is very similar to the first image here! After prototyping, I decided to make two separate bookcases instead of one large one. If we move or want to reposition the bookcases, this will give us more flexibility.
Step 2: Prep the Wood
Prototyping at scale also helps determine how much wood to buy. I always buy a little extra to allow for mistakes or variations in the wood, but this will help ensure you don't run out in the middle of making your project.
Join and plane the boards down to your final dimensions. In the case of this project, I wanted to keep the boards at an even 1" thickness so I could use the 8mm domino on the edges for maximum support.
Several boards were similar dimensions but varied slightly depending on whether they were the overlapping part of a joint. I marked the front edge of all with a simple shorthand system for each of the boards positions in the overall piece and the final length they should be to keep myself sane throughout the project.
The process for prepping was very straightforward, but for those newer to woodworking here's the basic steps:
1) Cut wood to rough length on the chop saw. Leave an extra inch or two so you can take it down to the final dimension on the table saw and make sure it's square.
2) Plane the wood. Ideally, you'd start with a joiner but the boards were too long for the joiner I had access to and I'm not a purist so away we go!
3) Join the third edge. Once the boards are surfaced, the jointer will make an edge perpendicular to the edge from the planer. 'But acoens,' you ask, 'isn't this backwards? I usually surface one edge on the jointer, then a second perpendicular edge, then put it through the planer!' Fair point, hypothetical Instructables member! But here I'll mention again that my boards were too wide for the jointer I have access to and knowing how to get the results you need with the tools you have access to is also important.
4) Cut the final edge on the table saw. Now that you have an edge to use against the fence, you can make the fourth edge cut on the table saw. Setting the fence will also enable you to run all the boards through at once to get a nice, consistent dimension on the depth of all pieces.
5) Cut the pieces to final length dimension on the table saw. I used a sled to cut my boards down to their final dimensions. Measure twice, cut once!
Step 3: Rough Layout of Pieces
Since all the edges are smooth and even, I was able to stand them up to get a rough feel of the dimensions of the entire piece. It's of course similar to the prototype, but this step helps visualize to make sure all the decisions are correct before beginning joinery.
This was the stage where I nudged interior shelf dimensions. I brought two books into the shop that I wanted to help define the max height of the upper and lower shelves and moved the interior unit to accommodate. Gotta love building for yourself! It fits what I need perfectly.
Step 4: Festool Domino Joiner
For the type of joinery I wanted to do, the Festool Domino shaved hours off the overall project. The domino system combines the best of biscuits, dowels, and actual dominos to make precise cuts (you can specify the depth of cut, width of cut, and size of domino).
I spent some time making sample cuts first to get at feel for the tool before working on the final piece.
The diagram in the images shows the more detailed view of what I assembled for the edge/face connections that exist throughout this piece. I made a horizontal mark on the boards, sandwiched them together and clamped them down, then used the Festool Domino Joiner to plunge into the edge and face of each connection. Instead of measuring each one, I used the edge of the tool flush with the edge of the boards to keep consistency.
If more detail would be helpful here, I'm happy to expand! Leave questions in the comments if there's something I should talk about in more depth.
Step 5: Stand It Up!
After making all the insertion cuts for the dominos, I dry fit the pieces to stand them up. This was exciting as the two bookcases really felt like they were coming to life!
Step 6: Glue Up & Clamp
With a system this complex, it's important to consider the order of to glue and clamp. Know the dimensions and constraints of your clamps, as you might have to work in more local areas.
I started on the inside sections, thinking through the smallest box units first as they offer the least flexibility in installing the dominos. With my design, there was always a way to connect the pieces naturally. I used regular wood glue, making sure to not put too much in the routed holes as the dominos will overfill any excess back onto the piece.
Clamp overnight and up to 24 hours, then remove the clamps.
Step 7: Put It to Good Use!
The bookcases are now full of the books they're designed to hold! They also house some of my favorite treasures perfectly.
You can see similarities in the prototypes early on to the end result and hopefully follow this evolution to make a similar version that fits the things you love.
I'm really pleased with the final result and love that this project was motivation to learn how to use a new tool, the Festool Domino Joiner. I look forward to other projects keeping this new way of working in mind.
Thanks for reading! Please comment and let me know if you have any questions.
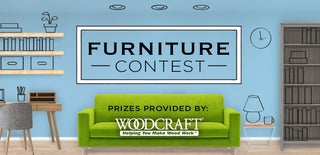
Participated in the
Furniture Contest 2017
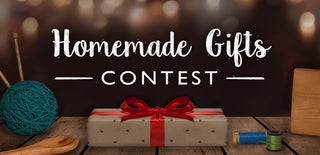
Participated in the
Homemade Gifts Contest 2017