Introduction: Monogram Mallet
Whilst antiquing I found this small monogram stamp with the initials ‘’J.L.M.’’. For 3 quid, I decided to pick it up and use it to mark my work as my name begins with a J. I find that metal stamps or punches are always a bit tedious to use, especially because they require an additional tool to leave an impression. They also require the use of both hands. Time to rectify this with a Monogram Mallet !
Step 1: Tools and Materials
Metalworking Tools:
- Vise
- Anvil
- Hammer
- Drill or Drill Press
- Torch + Fire Brick
- Files
- Cutting Oil
- Sacrificial Allen Wrench
Woodworking Tools:
- Awl
- Carving knife
- Spokeshave
- Sanding block (220 grit)
Materials:
- Handle Blank
- Monogram Stamp
Step 2: Preparing the Monogram Mallet Head
*First, whenever working with steel, always wear at least protective eye wear; hearing protection and a dust mask should also be worn.
Start by cleaning up the steel stamp and find its center point by resting it on your finger until it levels off. Mark that point with a permanent marker. Instead of making a tapered hole for the handle to be wedged into, I decided to use the straight section of an Allen wrench to connect the head of the mallet to the handle via an epoxy bond. I arrived at that decision because the miniscule head of the mallet would render any wooden joint susceptible to shearing upon first use.
Using plenty of oil to cool and lubricate the drill bit, drill a hole slightly smaller than the Allen wrench you’ll be using. Next, prepare the Allen wrench by lopping off the bent section with a hacksaw or angle grinder, being sure to clamp it tightly within the jaws of a vise. Then, use a file to clean up the cut and slightly ease over its edges. Now, insert it into to the head of the mallet using a few hammer blows.
Step 3: Preparing the Monogram Mallet Head Pt.2
Once the Allen wrench piece has been inserted into the mallet head, rest it in a vise so that the small exposed end of the Allen wrench is facing upwards. Next, making sure to have a firebrick in behind your work area, heat up that end of the Allen wrench until is red hot. Once it has reached this malleable temperature, use a pair of pliers to pick up and place the piece onto a hard surface (preferably an anvil ). Then, with a ballpein hammer, strike the exposed end of the Allen wrench until it becomes dome-shaped. This might take a couple of heats. Once cooled, check the fit of the mallet head to the modified Allen wrench, there should be absolutely no play.
Step 4: Finalizing the Monogram Mallet Head
After testing the fit, I used a file to remove the superfluous letters from the head of the mallet. This took quite a while, but the result was achieved. I cleaned up the file marks with some medium grit sandpaper before moving to shaping the handle.
Step 5: Shaping the Handle
I started by drilling an undersized hole in the end of a 12’’ x 5/8’’ square piece of roasted maple before starting to shape the handle. Use your preferred method for shaping the handle, but if you’ve never made a handle before use the sharpest knife you have to round over the corners of the handle blank (which should be straight grained ). The first illustrated carving knife is a chip knife which is a good general-purpose carving knife. The second is my preferred carving knife, a Swedish-style carving knife which has a thick robust blade that is ground to a fine point, this lends itself to removing a lot of material by using broad strokes or fine detail work by using the fine point of the knife.
Once the corners have been knocked off, I used a miniature spokeshave to continue to round over the corners and further shape the handle. In fact, both a knife and a spokeshave can be used to shape the entire handle from start to finish, use what you have access to. I followed up the shaping by sanding the handle with a fine grit sanding block. By using a foam sanding block, the rounded edges of the handle won’t be deformed as the foam follows the sinuous contours of the handle.
Step 6: Gluing the Head to the Handle
Now, back to the head of the mallet. Before gluing the head to the handle, I decided to notch the edges of the Allen wrench shaft to increase the surface area of the shaft and maximize epoxy adhesion. Theses notches were achieved with a small triangle file and patience. I then mixed up some 5-minute epoxy and glued the mallet head to the handle, wiping any squeeze out with a damp paper towel.
*Life changing shop tip: When using parallel tubes of two-part epoxy, cut the tab that connects both plungers together, that way you can control precisely how much of each part goes into your mix.
Step 7: Finish and Use
Once the glue has dried, coat the handle in the finish of your choice. I prefer to use a natural oil for handle finishes. After the finish has dried, test it out! I used it to initial a battery powered lamp I made, and it performed perfectly! *It should be noted that this was preceded by many practice attempts on bits of scrap and on my workbench before I got up the courage to whack the one of a kind solid poplar geometric lamp that took me dozens of hours to design and build.
*Update, I’ve become obsessed with whacking my initial into everything…make YOUR mark!
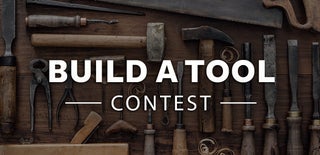
Participated in the
Build a Tool Contest