Introduction: Photo Ligthbox - Laser Cutter
Before going further, this is a translation of my original post, you can read it [French] on my blog.
The little story of the project
In a fablab several objects are created from the machine tools which are made available. Often users take pictures of their creation during the entire production process, but especially at the very end once the project is finished. However, in this type of place, the environment and the lighting are not necessarily suitable for taking beautiful photos.
Sometimes it is interesting, even necessary, to photograph an object in a refined context in order to perceive the details of the creation. It was then that the idea of a light box made of fablab came to my mind. Furthermore, the interest of such a box for the fablab I visit arose from the need to identify the projects carried out in their fablab. Users must make a check-in each time they come to the fablab and they are encouraged to photograph their project and share it on social media, which is a bit like checking out. In my opinion, this is also a great way to provide a pleasant user experience for fablab users. Taking photos of projects not only allows us to share our creations, but also to produce visual documentation relevant to the maker community. For this mini photo studio project, several phases were necessary in order to design an effective, aesthetic and safe product.
Supplies
Machine (s) used: Trotec Speedy300 laser cutting
Software (s) used: Fusion 360 for parametric box design and Inkscape for file preparation for cutting
Material (s) used:
- Russian birch wood 3 mm
- Corrugated polypropylene (Coroplast) 4mm,
- Set of leds
- Wood glue
- Project name: Light box
- Designer: Nicole Fodale
- Creation date: April 2019
- Location: Montreal, at fablab échofab
- Project progress: Completed, but still room for improvement
- Required skills: Use of laser cutting
- Project license: Creative Commons Attribution License - No Commercial Use - Sharing under the same conditions 4.0 International
Source files
If you would like to create this box, you can download my files (links for download): SVG - PHOTOSTUDIO
Step 1: Research and Analysis
First, I had to do some research on the light box models already on the market. I didn't want to reinvent the wheel, but I knew I wanted to create a product that was easy to make with the machine tools found in a fablab. Firstly, I had already experienced a DIY (Do It Yourself) light box, and this twice rather than once!
They were effective in terms of photo quality, but although the latter was foldable and easy to store, it was always a headache to install it whenever I wanted to take a picture of an object.
So for this project, research concerning light boxes or photography tents that are sold online indicated to me that:
- they are designed to be easily transportable;
- they can be assembled and disassembled for easy storage;
- they are made of fabric (canvas) or light plastic;
- some have a silver coating to better reflect light;
- they have removable bottoms;
- some have built-in LED lights, others have outdoor lighting;
- they often have an opening at the top.
Images:
Canvas model with silver coating from Amzdeal Light Box Photo Studio
WhiteBox Plug & Play Lightbox foldable plastic model
Step 2: Design of the Box
Once the research is done, we must move on to creating the model we want to make. I wanted my structure to have a fablab design look and the removable side was not absolutely necessary. Especially since I thought it more relevant that the box was solid. I did different sketches to see what could be done. My sketches are always done by hand, it allows me to reflect on the design while drawing.
First concept
My first idea, following a request for a box for a fablab, was to make a light box on a support. It had to be dedicated to the check-out function in the fablab so the possibility of moving the entire kiosk with all the elements necessary for the box (consumables, decorative accessories, lab camera, etc.) seemed to me a interesting avenue. So my first model had support and lights integrated into panels.
Second concept
Finally, the project in this case wanted to be simpler and I therefore focused on the design only of a fablab style light box that can be placed on any type of furniture. I still had to see the style of the box either really a tight assembled look or straighter lines and discreet joints.
Other sketches for design and top opening. Before going further on my choice, I decided to make some models in the Fusion 360 software. Then, I was going to decide what would be more attractive and practical.
The goal of final product design
The idea is to make the object safe and compact in order to take up as little space as possible in the laboratory and above all not to have too many accessories outside the box which can become bulky objects.
Dimensions
After making the sketches, I had to turn to a design that could easily be done in a laser cutter machine (in my case, the Trotec speedy 300). The dimensions of this one being 17 ″ x29 ″ (726 x 432 mm) I had to make sure that there was enough space to create the structure of my box.
The fact of making the box with the CNC had been discussed, but ultimately the dimensions of the prototype seemed satisfactory.
I chose to make the box with a size of about 15 ″ or 380 mm. So I designed my box model in Fusion 360 parametrically so that I can change the dimensions of the box quite easily. The notches can also be resized as desired.
I had already experienced parametric design in other projects, but rarely completely effectively. It must be said that the more complex the object, the more difficult it is to give it parameters since several elements have to be taken into account. In the case of a box, it is quite simple to carry out, however it is necessary to have a good vision of the assembly of the box so that the reference lines and the constraints are in the right place.
Basically the box in 3D software is simple, it does not have the final design that is found on the sides of the box. It was in 2D software such as Inkscape that I added the text and the material sections to create a light effect on the outside of the box.
Step 3: Conception of the Box
Vector files
In my profession, I have worked a lot with Illustrator since it was the software used mainly in the world of graphics. So I had to learn to use Inkscape for a few years. I don’t have a crazy love for her, I have to admit. But since it is free software and often used in fablabs, I had to use it. Here are the different panels for my first version. It is missing some elements that were added in the second version that you will find later in the manufacturing stage.
Press fit - Tight assembly
I reduced the width of the notches of the model which was 10mm x 3.125mm and that I narrowed on the width to 9.7mm x 3.125 so that it could be assembled tight (press fit). It was, so much that I had to sand the ends of the tabs a bit so that they could enter more easily. Probably I should have made a slight curve on the tabs so that they slide better in the notches. I did not modify the files for this purpose, I may try the experiment with a sample to see how much the curve should be.
Logo and design
I had initially created a logo which was entitled LIGHTBOX with the phrases "Share your project" and "Share your project". But the word "lightbox" was an English word only and I wanted the box to be read in both French and English. So I adjusted the name so that on one panel it says "Photo Studio" and on the other side "Photo Studio" with always the two sentences available on both panels.
Then in order to make a small animated instruction guide, I brought the SVG files from the box into the 3D modeling software in order to see the final assembled product. You can see the video above.
Step 4: Identification of the Interior Coating
The possibilities of interior coating are numerous. In my test period, I tried two which are foam board (Foamcore) and corrugated polypropylene (Coroplast). There is also the possibility of painting the walls with neutral white paint. However, the walls of the box must obviously be full and the wood must be prepared to receive the type of paint chosen.
Corrugated polypropylene
The corrugated polypropylene is easily washable and it also allows to stick supports during the photo taking and to remove them easily. The only disadvantage that I have noticed is that this type of coating can create static which causes particles of dust or the like to stick to this surface.
Foam board
Foam board is less resistant, easier to pierce with certain objects and difficult to clean although easily replaceable. It would also be possible to simply put white cardboard, but again its properties, may cause it to need to be replaced often. In any case, we are talking about an element of the box which is a consumable in the same way as the boxes used for the curved bottom (cyclorama wall).
Step 5: Choice of Lighting
The research on the type of lighting was done based on the models of light box or tent already existing. However, first you have to understand what the different abbreviations and numbers mean when you want to get LED lights.
Color temperature - Kelvins
First, we find the kelvins which represent the color temperature of a light source. Most light boxes use between 5400k and 6500k since this is the light spectrum that most closely approximates neutral white.
SMD - Surface Mounted Device Then choose the format of the LEDs (Light Emitting Diode). The SMD formula which represents the words in English Surface Mounted Device translated into French "surface mounted component" (CMS) simply means that the lights are mounted on an aluminum substrate. The soldering is done on the surface on the printed circuit and this allows for lighter and smaller components. So we can have behind the strip of lights an adhesive surface to be able to install the lights where desired.
Bullets format Finally, you need to know the size of the LED chips. Here is a picture that illustrates it well.
Source: FlexFire LEDs LEDs have roughly the same intensity, except that 5050 chips can be 3 to 5 times more powerful than other formats since they can contain three light components.
I admit that I did not explore wattage and energy consumption any further since I bought a set of LEDs on tape. The set comes with an adapter, a switch and a 3 meter strip of SMD 3528 LED light.
For the light box project, just use half the length of the LED strip that needs to be cut where it can be done.
With the rest of the tape, I'm going to create other light boxes. All I need to do is solder a standard female connector to the remaining LED strip so I can then add a switch and then plug into the male connector on the adapter. The difference with the original purchase version is that the switch is part of the transformer wiring.
I finally had this experience, I will share the details of this practice in a future post. I will put the link as soon as possible.
Step 6: Sending the File Box in to the Laser Cutter
Finally comes the stage of making the prototype. The SVG files are ready. Everything must be prepared so that the laser cutting can interpret what must be done.
Job Control settings - Color code
Several elements must be set for the laser cutting machine to decipher what it must accomplish as a function. One of the essential elements is the choice of the color of the lines.
Below you will see that the vector files have lines of different colors unlike the first image above whose lines were only black.
Obviously here I made an assembly to visualize the parts, but the laser cutting was carried out one panel at a time to enter the dimensions of the machine.
The colors identify the lines that will have a function assigned to them. For each color we find a drop-down menu which allows us to choose that this color is for engraving, cutting, without (no function) and positioning which simply allows us to be a positioning reference.
The tasks performed by the machine are done in the order of appearance of the colors presented, but we can choose the colors that suit us from this list. For the sake of simplicity we take those that are the first in sight. So often the engraving is found to be in black (RGB = 0) since it is ideally always necessary to engrave before cutting so that the material is as stable as possible. Then, red (R = 255 VB = 0) for the interior cuts and blue (RV = 0 B = 255) for the exterior cuts. In one case, I used green (R = 0 V = 255 B = 0) for a third level of cutting. It is important to start with the interior cutouts before those that are outside of a design always with the aim that the cut pieces move as little as possible.
To know the color code, just go over the color and the indication RGB appears. It is therefore necessary to identify in the vector file the lines with the correct color code.
Regarding cutting values, always check with the machine you are using by testing the material you have chosen. Sometimes from one machine to another the values may vary slightly so the best is always to test or check with the technician in place what it is better to put.
In the case of my 3mm plywood box (Russian birch) the values were the same either for cutting power 100 and speed 0.9 to 1000 PPI / Hz and engraving power 100 and speed 40 to 1000 PPI / Hz.
I also made a small file for the lid handle. I slipped the design into one of the side panels when cutting into a part that was going to be a scrap. I did it at two heights not knowing which one would be best in practice.
Step 7: Creation of the Box Structure
For my prototype, I had chosen an oak plywood for material which is rather beautiful on one side and less pretty on the other. I bought it all in a big box store and had 16 ″ (406 mm) squares cut on the spot from my 4 ′ x 8 ′ panel. Unfortunately the panels curved a lot which made my cutting to laser cutting more complex. So I had to fix my panel with adhesive tape in several places on the screen of the machine, but still unfortunately the laser was not always in focus. Therefore, there was a lot of smoke and the cuts were not all of the same quality. I even had recourse to the mediator of the fablab who made manipulations during cutting with the level of the tray. I’m not ready to venture into this maneuver yet!
Despite these small pitfalls, I managed to make the prototype box that I assembled and glued. Since the wood was curved the assembly was more complicated, but in my final version the wood was straight and in addition I had added notches in the center of my design and the slots and tabs were adjusted tight (press-fit).
Important during assembly
It is essential to assemble the panels of the box in a certain order, otherwise it may be impossible to properly build the box. Here is a small video which illustrates the assembly well.
After joining all the panels except the one on the front, proceed with the installation of the polypropylene covering the inside of the box. And at the very end, we place the front panel to close the box.
Coating chosen - Corrugated polypropylene
For my part, I therefore cut my sheet of Coroplast 4’x8 ′ to obtain 16 ″ x16 ″ squares and then I cut the excess with a retractable knife so that everything fits in my box.
I don't have any files for the polypropylene panels since I cut them by hand.
The panel found in:
- the back of the box 379mm x 377mm
- the bottom of the box 380mm x 380mm
- the top of the box 380mm x 380mm with a hole in the center for the opening of 130mm x 130mm
- sides 375mm x 369mm
The important thing is to make sure that the wooden structure is well glued and solid before installing the panels. Then, they must be placed in the order mentioned above in the list so that the placement is adjusted tight and avoid having to stick the plastic to the wood. But it’s my personal preference to be able to easily remove the polypropylene panels. If you want to fix them, you can use double-sided adhesive tape.
After further research, I knew that Coroplast is actually polypropylene and therefore can be laser cut.
Coroplast, Corex, and others are made with polypropylene and OK to laser. I have cut shapes with it for signs, with some success and no flaming. I use a lower power, frequency, and more speed with two passes.There may still be a few places to hand cut but overall it’s still a lot faster and nicer looking than cutting it all by hand. I looked at the settings I used last on my Epilog 45 watt, and it was speed 20, power 50, frequency 1000 for 3mm coro, 2 passes.
List of materials that can be cut, engraved or laser marked with Trotec.
Step 8: Improvements
My prototype was really experimental. So I made a few changes and additions that I knew were essential from the start. For example, the boxes to change the background had to be removable. For the prototype, I intentionally omitted this step since I wanted to test the lighting first and foremost.
Aperture for diving shots
You also had to make an opening on the top of the box to be able to take pictures from above or, say, from above.
But I had to check how I was going to hold the cover. So after thinking about it, I decided to make sure that the polypropylene at the top should be cut so that it protrudes slightly inward from the plywood hole (about 10mm on each side). Thus the removed plate could easily be deposited on the plastic edge.
Also, I fixed with double-sided tape the piece that I cut from polypropylene on the lid so that the ceiling of the box is completely white when it is closed.
The interior lining is installed mainly by the tight assembly, but for this part which risks being used often, I put double-sided adhesive tape so that the plastic does not move when the cover is removed.
Accessibility of removable cardboard
My prototype had a frame in front which did not easily allow the cardboard to be changed from the bottom since it was inside. So, I had to modify my design in order to keep the upper frame about 4 cm in order to stick the LEDs on it and also to play the role of protection for the eyes against the bright light of the LEDs in the box. However, I had to shrink the thickness of the frame so that it reaches the same level as the polypropylene and thus facilitates the sliding of the cardboard inside the box.
I didn't put any hooks on the inside, the cardboard was rigid enough to hold it in place. If necessary, it is possible to put velcros in the box and on the removable cardboard.
In my case, however, I had to make a small cardboard tab in the part at the bottom before to be able to easily remove the background (photo to come). Otherwise, since it is adjusted to the walls, it is less accessible and therefore more difficult to remove.
Holes for the electrical cord
In this second version, I obviously made the hole so that the cord of the LED strip goes through the rear panel, something that I had omitted in the first version and that I had to do so manually with a drill. But for the hole in the polypropylene I did it again with the retractable knife.
This concludes this post. If there is anything that may be missing or need to be clarified, please let me know and I will make the necessary changes.
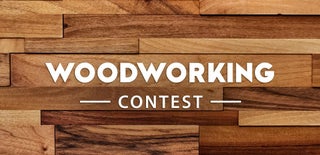
Participated in the
Woodworking Contest