Introduction: Pocket E-Waste Microscope
“Education is the most powerful weapon which you can use to change the world”
For my first major project on Instructables, I wanted to create something that would help tackle two problems: the abundance of “useless” Electronic Waste, and the high cost of scientific educational equipment.
Before I started, I set myself a list of goals I wished to achieve as well as a list of considerations when making the microscope:
The Leeuwenhoek style Microscope must:
Have parts sourced from E-Waste: The main lens must be sourced from a CD / DVD / BLU-RAY drive as they are abundant and easy to obtain for free
Be user friendly: with my main target audience being children, the device should be as user friendly as possible
Be portable: a pocketable device opens up the ability to use the microscope on the go or in the outdoors
Be Material Efficient: coinciding with the previous goal, by reducing material used to produce the product, there is less waste generated when the microscope reaches its end of life
Be Simple: This will both help keep costs down, and to help make assembly, manufacture and use easier (opening up the product to a wider audience)
Not have any sharp edges: self-explanatory
Not use any Permanent adhesives: If I find that the design can be improved, or I want to reuse parts for another project, specifically designing against the use of adhesives mean that I can easily disassembly any part and help reduce any waste
What I personally hope to achieve from making the Microscope:
How to salvage materials from older devices such as DVD drives and other forms of E-Waste
Improve upon my CAD/CAM skills
See if one of my ideas actually work!
Tools required for the construction:
A computer with chosen slicer and CAD software (SketchUp, Fusion360)
A cross head screwdriver
A pair of wire cutters
A 3d printer with Filament (or access to a 3d printer / printing service)
Step 1: Sourcing the Parts
As the main part of a microscope is the lens, I needed to source the required CD Drive – luckily, due to the recent decline in the use of CDs and other optical media, there is an abundance of optical drives people are willing to either give away for free or for a small charge. However, I chose to use an older IDE interface CD drive as the donor for parts, as the (in relative terms) ancient hardware has been completely phased out, and I would not be able to find a use for it as a functioning drive (If you can, always reuse before recycle).
Disassembly was a quick and painless procedure, as this drive like many others of a similar age are held together with a small number of Philips head screws, and within 5 minutes I had completed the removal of the main housing. The part I needed for the microscope was the main focus lens, held in the centre of the carriage by some fine wires and magnets. With the use of a pair of wire cutters (Supplied with my Anet A8 3D Printer), I was quickly able to remove the main lens with little effort.
However, I chose to completely disassemble the main housing and remove the secondary lens, the magnets, the stepper motors, the mirrors and the laser diode for use in future projects – the older plastic was very easy to break with the wire cutters, however it should be noted that the brittle plastic was prone to pinging bits of material when cutting, so eye protection would be recommended
After removing the main lens, I performed a few tests to get a feel for how much magnification I would be able to expect, and I was pleasantly surprised at its ability: I was able to see the individual pixels on both my older Moto G’s and Moto X Style’s display in good detail – I also expected this result to improve when using the proper microscope.
After removing all the required parts, I then moved on to the design phase...
Step 2: Designing the 3D Printed Parts
For ease of both design and use, I chose to use a friction fit style design (I had previously fully designed and printed out a screw fit type design, however my printer couldn’t print with a fine enough detail for the required small threads, and the overall print ended up being a bit too messy for my satisfaction).
For my microscope to be pocketable, I wanted to ensure that designs were roughly the size of a 2 Pence Piece, and that they would not be too bulky so that the user would not stand out with them in his or her pocket. Using an old pair of Vernier callipers, I made the required measurements of both the lens and a 2 pence piece to get a rough bearing as to the required CAD models.
Once I had an Idea as to the rough sizes of the models, I prepared my chosen CAD and Slicer Software. Although I have heard great things about Fusion360 and the Autodesk range of model designing tools, I chose to use SketchUp to design my models and Cura to slice them, just because that was what I was taught with and the software I know best – I recommend that if you are starting as a complete beginner you try both options and make a judgement for yourself!
In order to export the finalised models into my slicer software, I needed to install an additional plugin that would allow me to export in the STL format used by slicers. To do this, I installed SketchUp STL from the extension warehouse, which added an extra drop down menu to the tool bar to allow for easy exporting of files out of SketchUp.
Now I was ready to start designing!
Using the dimensions taken from my measurements earlier, I began making an outline of the main lens, and the footprint of the lens in the primary slider. Afterwards, I made a circle on top of the outline with the “Shapes” tool, and used the “Push/Pull” function to stretch the model until it was of equal height to the lens. This meant that the carriage would provide a snug and smooth fit for the lens, and would help prevent both wobbling of the lens, and the need for any permanent fixtures.
The final addition to the main carriage was creation of a small handle that would enable the user to focus the lens more easily on the desired target. After drawing a circle at the base and drawing a small sector off to one side, I again used the push pull function to create the desired handle, and position it in a point that make focusing the carriage easy to do. Finally, I removed the unused part of the circle with the “Erase” tool.
After this, I began designing the housing for the lens housing – due to tolerance issues with my printer, I had to make all contact gaps around 0.3mm apart. With that in mind, I first drew two circles on top of each other, one with a radius 2mm greater than that of the other (producing a housing wall thickness of 2mm). Afterwards, I again drew two lines from the centre to the outside circle to produce a separate section (However it is important that this section is atleast 2 mm greater in chord length than that of the handle of the main carriage, or using the slider will be much more difficult), and then, after removing all but the crescent section of the circles, used the push pull function to elongate the 2D crescent into a 3D object. I would recommend a height of around 2x the height of the main carriage, as this will give the user plenty of room to focus the lens for various sample heights.
However, Because I wanted to add extra functionality to the housing, I chose to add a small lip on one side of a height of 1mm, as it would allow the microscope to be used with standard 1mm slides used on other traditional educational and professional microscopes, but also use the other flat side for other non-slide based uses. To do this, I used the “Draw” tool to draw a rough line that went from the outside circle, touched the inside circle, stopped at the outside circle again. After clearing up any overhangs, I used the pull tool to achieve the desired 1mm height.
The final design part was to create a small case and lid to protect the microscope from damage when being put in a pocket or compartment. This time, I chose to use a larger gap between models for the inner case to prevent binding and allow for easy removal of the microscope, and a thicker case wall of 3mm to help prevent the case being broken if accidently dropped or sat on. I also used the 0.3mm rule for designing the join between the case and the lid, as it would also need to be a friction fit in order to stop it falling off.
To make the case body, I drew one circle with a radius 4.5mm greater than that of the main housing, and used the pull function to raise the model by 2mm. Then I drew a secondary circle on top with a radius 1.5mm greater than that of the main housing, and used the pull function to pull the outer ring up by a height that was 2mm greater than the total height of the main housing. For the lip of the case body, I drew another circle from the centre at an equal height to the top of the case with a radius of 1.65mm greater than that of the central housing, and used the pull function to raise the inner ring by 2mm.
For the Lid, I repeated the same procedure as the case body by pulling a circle with a radius of 4.5mm greater than that of the main lens housing, however the secondary circle had a radius of 3.15mm greater than that of the main housing. Using the Pull function, I then elongated the outer ring by 2mm to provide the required lip for the lid.
After I designed all the models, I ensured that they were all oriented correctly, and that all surfaces were facing in the correct direction - if any faces are a dark grey colour, that means that they are inside out, and if not flipped using the “Reverse Faces” function on the right click drop down menu, the Slicer might miss some parts of the model out, resulting in a failed print (can be identified by Red Areas in Cura)
Finally, using the STL plugin I installed earlier, I saved each of the 4 separate designs as an STL file, and moved on to the slicer
Step 3: The Slicer
Using a properly configured slicer is crucial to ensuring a good and high quality print – Although some would recommend that you prioritize speed over precision, I suggest that when printing models such as these, you choose to go at a fairly slow rate, but at a very high detail (E.g. 0.1mm layer height, 0.4mm line width, 100% infill). This is because, especially for friction fit models, tolerances are tight and need to be exact, and due to the small size of the model, printing with too fast a flow might cause inaccuracies and poor use. Furthermore, the size of the prints means that even with 100% infill, they take around 2 hours to print all four parts, so time is generally not a massive problem. I would also recommend using supports for the main slider to help print the small handle, and printing the main housing with the lip upwards (If included in your design) – You can adjust each model’s settings individually if printing multiple together with the “Per Model” setting on the left hand of the screen
When you are satisfied with the slicing settings, send the models over to the printer!
Step 4: Printing the Models
After ensuring that the print conditions are just right for printing (Level bed with auto bed leveler or folded paper trick), set the models printing and kill some time! (Because everyone loves a time-lapse, I Included a short Time-lapse of my Anet A8 Printing the Models :) )
I am printing with 1.75mm K-Kamel PLA in Blue, and at a temperature of 200 Degrees Celsius with a print speed of 60mm/s – I would recommend PLA over ABS for this project as the model will rarely be under any high temperatures, and the slight flexibility of the PLA will help reduce the chance of breakages.
Step 5: Finishing the Parts
After the print is complete, you might need to sand down some of the rougher edges of the print. Using some high-grit sandpaper, remove any stringy edges or blobs within the friction fit parts, and try to remove any sharp corners that might have been made in the printing process.
Finally, after inserting the primary lens into the carriage and ensuring a tight fit, use some light 3-in-1 oil to help ease the sliding motion (if the action seems at all rough)
Step 6: Test Run
I have taken a few test shots with the microscope to try out the concept: I have included several close ups of a leaf, an LCD Display and an Eye Lash – I would have included more but focusing a camera onto the small details is very hard!
Overall, I am very pleased with the way the microscope came out – the simple design means that I can easily change or edit it if need be, and the minimal component requirements means that I can easily reproduce the design essentially for free
I definitely feel this project has helped me with my CAD and CAM skills, and am also more skilled at disassembling old electronics so will be better prepared for future projects!
I have included all the required STL Files to complete this project for yourself if you wish to do so - you might have to adjust the tolerances slightly, however you are free to use the models as you wish (I believe that the best way to spread something beneficial is to make it free to use, forever)
Thank you for taking the time to ready my (admittedly word heavy) Instructables! If you found it interesting or enjoyable, please vote for this project in the Pocket Sized and Trash To Treasure Challenge!
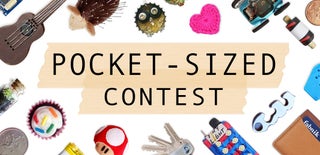
Participated in the
Pocket-Sized Contest
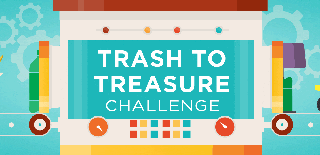
Participated in the
Trash to Treasure