Introduction: Power Loader Cosplay
Hello! Welcome to my power loader instructable!
This project was completed over 7 weeks and cost.....$500..ish? I'm sure that could easily be done cheaper but I wasted a lot of material testing things out and buying tools that I didn't have previously...and Modgepodge.....SO MUCH MODGEPODGE! Take my advice, Buy in BULK!
I had a few goals in mind when I was designing the build. I had to sacrifice some film accuracy for the sake of logistics. My main goals were the following:
LIGHTWEIGHT: I'm not the strongest person and this was a costume that needed to be worn for a long period of time without killing myself. I think i accomplished this pretty well with hollow boxes and foam.
MOBILITY: This was REALLY important. I wanted to be able to move with decent speed and be able to have a wide range of motion with the arms. With a big space like a convention center I needed to be able at a decent, if not fast, speed.
TRANSPORTABLE: I have a Ford Focus.....Originally the goal was to create something I could break down and transport in just my car. In the end it turned out to big for a compact car. It did however, fit nicely in a full sized SUV. The whole thing can be broken down into 5 parts.
INDEPENDENCE: I had hoped to create a costume I could get in and out of alone. I failed at this and the final costume required a Handler to help put the costume on.
I'll be referencing these goals as I go through the process of the build and how they influenced the design choices. Anyone creating their own power loader can make adjustments based on their own goals for the build.
Okey dokey.....ONWARD!
Step 1: Stilt Walking Is FUNdamental
I'd been wanting to do a cosplay with stilts for a while, so the Power Loader idea actually evolved around the stilts rather than the other way around. Having never worn stilts, I wanted to get something that was easy for beginners. I found the shortest drywall stilts on Amazon. They ended up being 15". I've seen other PL builds where they make their own stilts. That could be a better option for people looking for a shorter height or a steadier footing. But for me, the drywall stilts were perfect and easy to use. They also had the extra support of the leg brace, which was great for stability, but did get in the way of the joint I built in later.
It's really important to practice on the stilts and get all of the adjustments and sizing figured out before building around them. The way I built the leg made it difficult to adjust the settings afterwards.
I would like to say I planned everything out well before starting this project.......but I did not. The first thing I did was just build a cardboard box around the lower part of the stilt with no real idea of what I was doing. I cut holes in the cardboard and used zip ties to secure the box to the stilt.
It's important to get this base REALLY secure. I had some issues later on with the whole foot sliding up and down the stilt as I was walking. It was much harder to secure it after all the foam was put on. I recommend making sure this base is very secure, and using grommets in any cardboard holes to prevent the ties digging into the cardboard. Or whatever you can come up with. Just make sure it's not going to move.
Step 2: Foam Party
The majority of this entire build was created with insulation foam at HomeDepot.
HINDSIGHT: If you're really smart you would plan out and measure so that you know exactly how much foam you'll need. I didn't do this and ended up with a lot of scrap, which can add up costs.
It comes in big sheets, but if you drive a little Ford Focus and can't fit it in your car....they let you cut it down into fourths at the store. :)
I cut out the basic shape for the base foam pieces with a tiny saw. Don't use a saw. Use a box knife. It's a cleaner faster cut. to get an even circle for the top of the joint, i traced a large pot lid.
I glued the foam to the cardboard base with a combination of tacky glue and hardware caulk. There's probably a better way to glue it but I'm literally figuring this out as I go along and it's not fallen apart yet.....so......whatever works.
I made sure to add an extra layer of the foam on the inner part of the stilt to give myself room for my foot. I would actually suggest doing this on both sides, because you'll want a little extra space for the joint on the outer side.
Sanding down the edges was important(because I used a saw and it was a huge mess, use a box cutter and it's easier!)
After assembling everything I also sealed all of the gaps with the silicone caulk...sanding it down after it tried. In addition to making everything look better, it helped keep everything from falling apart.
Step 3: Cardboard Flappy Things
I call this next step....winging it without really looking to closely at the source material!
The lower legs were the first thing I did, so they're the least developed of the whole costume. I did a lot of experimenting during this stage, and just kind of trying things out as they came into mind. Since I was also on a timeline, I used shortcuts in the detail work. Take out container lids made for really easy cool looking details. Also bottle caps, and other random crap I found around my apartment.
Originally I wanted to have actual moving hydraulics. I've seen this done and it's actually pretty straightforward. Dowel rods inside of PVC. Mine ended up static because I changed my mind and ended up being all....."Meh, whatever, I'll just do it this way."
HINDSIGHT: Limit the amount of bulky stuff on the inside of the legs. I walked with a wide stance, but the insides of the leg did bang into each other as I walked. I ended up having to take off both hydraulic bits from the insides(mostly because they fell off).
One thing I did use for a more metal look, is a one inch craft foam border around pretty much every edge. This allowed me to go in later and add shading and just gave the whole costume a more....realistic look? It was one of the simpler details that really added to the final look, even if i'm not sure 100% why.
The movie PL has these interesting metal flaps....things....sides? I cut a groove into the foam which made a good base to put the cardboard.
HINDSIGHT: Cardboard isn't great on it's own. I had to later seal up the edges with caulk and in the end they were pretty easily damaged because cardboard isn't very strong. I'd use something more substantial on future builds.
The rest of the details were made from cardboard and craft foam.
Step 4: Joint Pain
OK.....so....the main issue with the joint was the placement. The nice thing about the drywall stilts is the extra security created from the calf strap and the brace that goes up the outer leg. Unfortunately, the top of the brace was exactly where I needed the inside of the joint to go. It took some adjusting and I worked it out eventually by smooshing it around......but it wasn't the greatest, and like they say in the infomercials...."There's gotta be a better way!". Hopefully someone else with figure it out in the future and let me know.
Mobility goals are the reason only the lower half of the leg goes around the leg fully. Originally, i'd wanted to have a costume I could take on and off independently. To do this, I really needed to be able to SIT. By keeping the upper half of the costume limited to just the outer leg, I was able to walk, sit, and move around MUCH easier.
One thing that did work out really well was the ziptie belt loop. The upper half was pretty much just a layer of cardboard glued to foam board. through the cardboard I used a ziptie to create a loop. After gluing the inside of the cardboard to the foam, it made a really secure hook. I had originally planned on using a belt to secure the top part of the legs around my waist. But it ended up working better, to just tie the tops directly to the belt loops on my jeans. This kept the top part of the legs right at the hip joint and they didn't shift around much.
The height of the upper leg needs to not come above the hip bone or you risk hitting the torso part of the costume as you move. I had to cut down the upper leg for this reason.
The joint itself was a simple PVC pipe joint.
HINDSIGHT: Secure the joint somehow. This joint is the one that got the most stress and one did eventually fail on the final hour, on the final day of Dragoncon. Since the upper half was secured to the Outside at the knee, and the top was secured to my hip, the top half was always bending inward. The hole where the PVC pipe was, was always getting bent and smooshed because it was just foam. Eventually the left joint smooshed the foam and doubled the size of the hole. The joint fell out. In the future I'd use some kind of material to serve as a grommet and keep the foam from getting damaged.
Step 5: Backpack, Backpack!
When starting on the cage/pack part of the costume, the most important thing to keep in mind at every step is WEIGHT. This is the part of the costume that has the most impact on the quality of life while walking around a convention floor. I learned that just a few tweaks can be the difference between being relatively comfortable, or DYING at every step as your shoulders and back kill you.
HINDSIGHT: The backpack I chose was $12 from Walmart. Once the whole section was finished and the weight set in....it FELT like a $12 backpack. It's worth every penny and for the sake of your body, INVEST in a decent backpack or harness system....or whatever it is you need to bear the weight of the pack and arms comfortably. I will go more into the adjustments I made post-project to fix the issues I had during Megacon. Keep Ibuprofin with you.
I slipped the straps of the backpack through a very sturdy cardboard piece that i took from the trash at work. It was a really thick and heavy bid of board. I thought it'd be great! It was, but it was also the heaviest part of the torso. I'd use a lighter, but still sturdy, backing.
The cage was the easiest part to make. The PVC is perfect for getting the look you want and you can adjust and tweak it around until you have the perfect shape and size that fits you. Right next to the PVC i found some PVC insulation foam. It looks great around the upper and lower parts of the cage.
Step 6: IMPROV!
On top of the carboard base, i glued another layer of foam (With a space cut out for the backpack. Because the width of the cage was wider than I expected, I cut groves around the connectors, and kept the main part thinner. It didn't look to weird when i finished.
This is another area where I only slightly tried to match the source photos. I took a bunch of empty cardboard boxes i had lying around and tried to arrange them around in a way that looked cool. This saved a lot of time, but someone with more could accomplish a very source accurate design using foam core and cardboard.
I repeated the ziptie hook technique from the legs on the shoulders. The shoulder area is a piece of foam with a layer of cardboard. The ziptie was looped through the cardboard. I'll go more into the shoulder joint in a later step.
The hydraulics on the back looked cool when they were the larger size! But that had to GO almost right away. I didn't realize how much weight really came from the plastic of the thicker PVC. I cut down the amount of PVC i used and replaced it with dowel rods. Much better!
Craft foam details.
HINDSIGHT: When using sharp tools, make sure to wear shoes if you're cutting foam close to your foot.
Step 7: Step One...Cut a Hole in a Box.....
Step two.....put a light in the box!
I'm going to be totally honest.......I had someone else do this part for me because I don't know much about electronics. I'm not fully sure how they did it. They took the light I bought (Battery operated and light weight) and added a really long wire with an on off switch that I secured to the bottom right near my hip. It was easily reached.
This was one part of the cosplay that got the most gripe from critics(people on the internet who need to point out all the ways you suck). The light flashes instead of spins. I was aware that it was a difference from the source movie...........but at this point I was running out of money and this light is cheap, and it's really lightweight so I didn't really care. Choose a more accurate one if you are doing your own build.....or don't...
Step 8: One Woman ARMy.....
Ok, so my Pun game still has some work to do.
But guess what??? Turns out, the arms actually ended up being the easiest part of the whole build!
It's 4 pieces of foam thick for the forearms and two thick for the upper arms. Joint is a very simple piece of PVC pipe.
I used the same pot lid I used on the legs, to trace the circle on the end, to make sure everything matched. To glue together the boards I used the same material as the legs, silicone caulk and tacky glue. I didn't have any kind of press, so instead I laid a lot of heavy books and weights on the foam boards as they were drying.
After everything was dry, it took a lot of sanding to even everything out. I ended up going back with some drywall plaster and sealing up gaps or holes and then sanding down again.
Step 9: Go Big or Go Home
So, as far as the sizing goes.....the arms are where it got really out of hand. Before I even put the claw things on, I had cut the upper and lower arms to the size they were by just kind of eyeballing it. Once I went to add on the hands/claws the only way to keep the whole thing proportional and looking good was to have the whole arm end up being WAY bigger than I had ever intended.......and any hopes of being able to fit this costume in my little ford focus were dashed to pieces.
BUT it all worked out. Because in the end, the arms are the centerpiece of the whole costume. They're the focus and the coolest part of it. They're the first thing people look at and get the most attention overall. So if you're going to put the most work into something, this is it. And in this case, bigger WAS better. I'm pretty please at how accidentally massive these turned out. Because of the lightweight foam, they were still very easy to manage.
Originally I was just going to use thinner craft foam to decorate the upper arm. But that ended up looking to thin. The big accent of the 1 inch foam on the upper arm was the better choice. I traced the outline of the upper arm out onto a new board and was able to draw what I wanted and cut it out so that it fit perfectly.
The claws are three foam boards across for the lower part, and two for the prongs. I had to fit the thin dowel rod through the prongs before fashioning them onto the base. Since this part of the costume is getting a little more fragile....I made sure to use dowel pins to secure the prongs to the base and the base to the upper arm......and since i didn't actually have dowel pins, i used shish kabobb sticks from my pantry and snapped them in to 2" pieces. That and a ton of glue, and they hold pretty well.
The handles for the arms were just PVC glued into the foam.
Step 10: Shoulder Joint
There were multiple techniques I looked into for the shoulder joint but everything I found didn't seem to really give me the range of motion I needed. I also needed something that could detach so I could transport the costume without a box truck.
The utility straps worked perfectly. The arms clipped right in and came off easily.
I used zipties to create a loop the same way I did with the upper legs. I took the straps I bought and cut them down to size, then sewed them to the loops I created.
Step 11: And It Was All Yellow
SO.....turns out the Hardest part of all this was the painting. It took a full two weeks.
My choice to use foam is great for weight......but inconvenient for painting. I was VERY lucky to discover BEFORE painting, that spray paint will dissolve foam. It just eats it away. To prevent this, takes a lot of time and layers.
I started out with layers of modge podge to try and create a seal. I found a styrafoam primer spray at Michaels and tried that out as well. It's specifically made to protect foam so you can spray paint it. It worked.....kind of. I sprayed the first time too close to the foam, and even the primer started to eat away at it. I learned that you had to keep a distance when putting down layers. Unfortunately this left quite a lot of primer getting sprayed into the wind. I used up two cans right away and only got a dusting on my project. I do think the primer really works, but you've got to use a LOT to cover a project this big. I was not anticipating how much I would end up using. It was a large part of the end budget, which I why i did not end up using the primer on the arms.
Since I was worried the primer wouldn't be enough, I took it a step further and covered everything in a layer of acrylic paint. I wouldn't use acrylic paint by itself, because it's streaky and looks cheap. But the extra layer did work well to stop the spray paint eating away.....mostly. You still have to spray at a distance. Don't get too close.
I used Safety Yellow for the majority of the base, but I also did some shading with a Goldenrod (or any slightly orange yellow). I feel this second yellow color helped add some depth. It's not something you'd notice unless you're really looking for it, but I'd recommend it for a better end look.
TLDR: MODGEPODGE, MODGEPODGE, FOAM PRIMER, ACRYLIC, SPRAY PAINT.
HINDSIGHT: Use the Primer! While the arms looked fine without this step.....I did find that the spray paint didn't hold up that well under heat. I live in Florida and over time, the heat and humidity caused a bubbling effect on the paint. Luckily, it ended up looking more realistic, because paint on factory equipment DOES kind of do that. But over time, it's only going to get worse. The arms have bubbled WAY more than the legs where the primer was used. If you have the time to do everything correctly, do it that way.
Step 12: Let's Get DIRRRRTY!
If this whole Instructable has come across kind of spacey this whole time, it's because that's how I felt through the entire build. This is the first cosplay of this level i'd ever created and the whole time I was just guessing and making things up as I went along, with no real idea if it was going to end up usable. But if there's anyone reading this, thinking about making their own, but don't really know if they're capable......DON'T WORRY! Because even if the build is a hot mess the whole way through.......a good paint job covers up EVERYTHING! If the paint work is good, it covers up all the little mistakes and messes, and parts that looked stupid before suddenly look pretty OK!
First things first......the stickers, logos and stripes. I printed off all the logos and numbers and made them look like stickers decoupaging them onto the Build. AKA: i put down a layer of Modgepodge, put the logo, and put more modgepodge on top of that.
The stripes were just painted on very carefully after drawing them out with a ruler.
MAKING THINGS LOOK METAL:
1. So you have your freshly painted beautiful robot pieces. You've just put on the logo and stripes on....the black looks awesome against the yellow. You sit back and look at now neat and clean the whole thing looks..........AND THEN YOU BEAT THE LIVING CRAP OUT OF IT! Anyone who's ever worked with machinery knows it's not going to stay very clean for long. The dings and paint chips are what make it look more realistic. The best way to get the dinged and scratched look is to beat it up a little! This will hurt your soul a little, after having just spent weeks putting it together, but I promise it will make the finished look much better. I used scissors, heavy shoes, my dog, and just threw things around my apartment. The fancy term is "Distressing"
2. After you've got your physical dings you want to take your metallic paint and paint silver into every scratch and groove. I also took a thin line of silver over every edge and extra on the corners. Anywhere that paint would usually wear away over time, i'd put some silver. Some places i'd use the acrylic silver, which is less opaque, and then wipe over with a cloth. This would leave a very thin layer and it would look like the yellow was slowly wearing off.
3. Dirt, Grim, Oil. I have the advantage of working in Manufacturing. My factory is FILLED with reference material of what machines look like after a few uses. Unless there's someone taking a toothbrush and detailing their power loader every night.........there will be dirt and grime in EVERY crack and crevice. All the foam details I added before, now needed to be shaded, essentially. I found the best way to create this look, without everything looking like an outline or stencil...was to wipe away the paint with my finger or smudge it with a cloth as soon as I painted it on. Acrylic paint from Walmart or Target worked great for this.
4. After I painted the whole thing, I actually went back and made the dirt and grime darker and more noticeable. It's a BIG costume and most people will be looking at it from a distance under florescent lights. While all the details are great up close, they get lost if you take a step back. Paint it like it's on a Large stage, not an intimate dinner theater. The feet were especially dirty and you'll want to use the Black in places where you want the detail to show.
Step 13: Improvements
After wearing the full outfit during Megacon I discovered some improvements that could be made.
The most important thing was making it more comfortable. The most important thing was the weight on my shoulders. I upgraded the backpack with cushioned straps. I was not able to modify the entire backpack without tearing apart the whole torso.
I added a hip strap which made a MAJOR difference in how the weight was distributed. I bought a thick utility strap and screwed it into the base. I sealed over the nuts and washers with more pipe insulation, cut in half.
I added a few other details such as wires for decoration but my favorite addition was the cabling. I bough a couple different sizes of cable wrapping at an overstock hardware store. They also had random plastic hardware bits that looked good as decoration. It was easy enough to cut a hole to place the cables. They were very light weight but a large amount of glue was still needed to keep them from falling out.
Step 14: Wearability...Megacon Vs Dragoncon
The challenge doesn't end once the project is finished. Wearing this build was a challenge all in itself. BUT it was less than it looked. The lighter you can make the build the better. Overall I'm guessing mine was a total of 50-60 ish pounds. Just a few adjustments made a WORLD of difference walking the loader around the convention floor. My time at Dragoncon was almost a completely different experience.
MEGACON:
Because my apartment is small, I hadn't actually had a chance to walk very far in the loader before the day of con. So my first real test run was at the convention itself. It hurt. A lot. First thing I learned was that I needed better shoes and more padding for the drywall stilts. I had walking shoes on, and the ankle straps dug painfully into the top part of my foot/ankle. With the stilts being extra heavy this got painful quickly. I ended up using socks to pad strap. The other two days, I used my work shoes, but they were not ankle high, so it only helped a little. The straps need to be as tight as possible to stay sturdy, so padding is essential.
The second thing I learned is how uncomfortable PVC pipe handles are. I didn't think much about padding the grip. Holding on to the bare plastic gave me blisters over time and dug into my hand. This wouldn't have been so bad if it weren't for the over sight on the arms. The arms were very light weight.....at first....and very easy to handle.....at first. But since they had no straps or bungy to hold them, they were 100% held up by just ME. Holding any weight for a long period of time at a 90 degree angle with your arms is difficult. Especially if you're like me and have the upper body strength of a 6 year old.
The third thing was the pack...Oh the pack. I have never been a fan of heavy backpacks. It was always the worst thing about walking to school. I've never liked them. The weight really wasn't really bad. But over time it get's heavier and heavier. Since the pack was pretty cheap it dug into my shoulders and hurt by back. Anyone who saw me at Megacon noticed a continuing readjustment of the pack. I also ended up buying strips of moleskin to wear on my shoulders. This really helped prevent blisters from the straps.
Exertion- The nice thing about cons, is that the collective energy is revitalizing! The adrenaline I got from walking around the floor was better than all the caffeine or energy drinks in the world. I was able to go much longer that I ever thought my body could. I wouldn't describe the exertion as a cardio burst or anything. I was similar to using the stair machine. It was definitely a workout but I was never breathless. I was able to go an hour or so more at a time each day. Luckily I was stopped for photos often, so I got lots of breaks.
DRAGONCON:
FIX ALL THE PROBLEMS AND EVERYTHING IS BETTER! SO much better! So much! I bought brand new steel toed work shoes(I needed them for my job anyway). I got some with a strong base and a high lip. Drywall stilts are made for workmen and a workers boot made the stilt less wobbly and felt better. I was able to pull the ankle strap very tightly without any problem. To solve the issue of the calf strap, i bought a pair of foam knee pads and wore them lower. Worked perfectly. Incredibly tight strap with no pain. Feeling steady on your feet is amazing.
The arms got a "Duh why didn't you do this right away" strap that held them at 90 degrees when my arms were at rest. I still had full mobility of the arms and the straps could be removed if needed. But it took the workout off my arms by about 80%. I covered the entire handles with foam cushioning and then wrapped them in black grip tape. So much better!
I couldn't get a new backpack. But as shown in the previous post, some simple padding and the addition of the hip strap was a huge difference. My shoulders still hurt over time. But it was low enough that I could Power through.
The costume was easier to wear also, because I decided to train before con! I felt pretty out of shape and tried to focus on getting better at endurance and building up my upper body strength. I think it made a big difference.
Step 15: Conclusion
So that's it. 6 weeks of work and another week for modifications. The original plan was something way smaller and simpler.....and the whole thing just got out of hand. But it was out of hand in a fun, crazy kind of way that I ended up loving.
The only goal that I didn't really succeed at was being able to fit it in my car. At minimum, I needed a full size SUB to transport it. A box truck may have worked but I didn't want the heat to damage the paint any more than it already was.
If anyone would like to see the videos of this build you can do so on my FB or Instagram.
Facebook.com/AllisonChaseMakeup
Instagram: aachase1401
If anyone else is building a Power Loader and has ANY questions at all....i'm thrilled to answer them! This is a really fun build that is much easier than it looks!
A big thanks to everyone who helped and gave me tips and tricks as I went along. Big thanks to Patrick (https://www.facebook.com/Rocky-Start-Productions-1... My Handler for both Megacon and Dragoncon! Thanks to my boss Shaun Sontos who put the light together for me! And a big thanks to my doggo Lyanna! Who put up with the constant chaos of our apartment and less attention as I worked instead of walkies or play.
Step 16: VIDEOS
Megacon Video someone was nice enough to get for me. No cables on it yet, though. :(
Second Video is Dragoncon
Third Video is full Megacon Cosplay Contest. Power Loader is 51:36
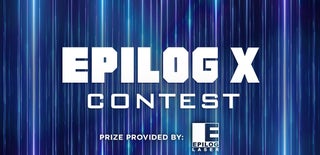
Runner Up in the
Epilog X Contest