Introduction: Record & Stereo Shelves
One of my biggest motivating factors in growing my understanding and skill in woodworking is simple: to replace all of the Ikea cardboard furniture that fills my house, one piece at a time. Just about everyone who has furnished an apartment or home with Ikea stuff has bought one of their cube towers which, among other things, happen to be the perfect size to house a burgeoning record collection.
I wanted to replace this cheap block shelving with something more sleek and handsome, with a modern but organic look, and a piece that could house my record collection, speaker system and other stereo gear. A while back, a friend of mine showed me a picture of a LP stand he found online that he wanted to build - though he never did - and I was inspired to try this design out in my project. I couldn't find the image of the piece online so I was going largely from memory, but the key design element was having interlocking beams that create a segmented look.
Something I had been meaning to try in some previous builds was using tension via threaded rods to assemble a piece of furniture. This offers several benefits and does not require the use of any of the more traditional means of wood engineering, such as nails, screws, and glue. Since I had all the tools and finishing products that I wanted to use for this build already in my garage, the only cost for me was the wood (about $40) and the hardware (about $10). Here's what you'll need to build this:
Materials:
Eight 10' 2x4s
Two 36" Aluminum Threaded Rods (you'll be cutting these down to four pieces - these come in a variety of diameters, but I used 1/2" rods)
Eight Washers and Nuts (sized to fit your threaded rods, obviously)
Stain and/or Finish (depending on how you want your final product to look)
Tools:
Power Miter Saw (this is your primary saw in this build, and it would be tough to make this without one)
Hacksaw
Power Drill & Bit Set
File
Sander (I prefer using a random orbit sander)
Jigsaw (optional)
Dremel (optional)
--------------------------------------
And if you like the build, I'd appreciate your vote in the Shelving Contest!
Step 1: Cut 2x4s to Length
This rack is made up almost entirely of 2x4s, and the design is all about angles. Lots and lots of angles. Oh, and I hope you like fractions. Lots and lots of fractions... But not to deter you! Despite this piece being entirely wood, there is surprisingly little cutting involved. You'll essentially be needing three types of 2x4s:
Top Rack: Four boards 55" in length
Bottom Rack: Four boards 60" in length
Legs: Ten boards 44" in length
Now, it should be stated that these lengths were designed to maximize what I could get out of 10' 2x4s, but can obviously be adapted to any size you wish, based on desired length and height of the final product. The only thing that's really important when cutting these to size is that the boards are all the same length as the other boards of the same group.
Once the boards are cut to length, it's time to angle the edges. When planning this project, I wasn't entirely sure how angled I wanted the leg pieces to appear. I decided to play it safe and go with 10º initially, so I took two leg pieces and cut off 10º of each end using my miter saw.
Note: Not to give you flashbacks of your high school geometry class, but based on how we're cutting our angles, we'll be turning our leg boards into parallelograms, and our top boards into trapezoids... Sorry, that is to say that the ends of our leg boards will be parallel, while the ends of the top boards will be mirrored reflections of one another.
With two leg pieces cut, I laid out one layer of the shelf on the floor to see if I liked how angled the frame looked (see picture). Well, I didn't, so I decided to throw caution to the wind, ignore all regard for sensibility and step over to the dark side. 15º. That's right, I'm a mad man. This looked much better, so I went ahead and cut the angled edges of my first top board to test out the final shape (again, these top boards will be cut in a trapezoidal shape with the longest side edge at 55" in length).
With the final angles and lengths determined, you can now cut all of the pieces to length, using your initial ones as guides. Needless to say, you want all of these to be cut precisely identically to avoid issue later on.
Step 2: Drill Rod Holes
With all of the pieces cut, let's talk about how we'll fit them together. As mentioned earlier, I wanted to try a furniture design that didn't use your standard hardware or joinery - i.e. screws, nails and glue. Using tension as an engineering principle in your furniture builds offers the ability to make slight adjustments in setting the individual pieces with only the turn of a wrench, and when tightened can make for a piece of furniture as sturdy as one filled with wood screws and glue.
That being said, the key to a successful build using tension is having perfectly drilled holes. Measure twice, drill once will be our motto with this rack. So, let's figure out where we want to drill. There will be four tension points in this polygonal design, so let's start with the top pair.
While the sides of the top shelf will be flush with the outside of the leg pieces, the legs will protrude past the top shelf. I decided I wanted this to sick out 6" past the top shelf. But since 2x4s that you buy at big-shop hardware stores aren't really 2" by 4", you'll need to make sure you're drilling in the precise mid-point in the board. My boards were 3 1/2" wide, so I want to measure 6" from the top angled edge of the leg pieces and 1 3/4" from the side edge, marking these intersections with a pen or pencil. Since the top shelf boards had their ends cut to 15º, you need to find the center point on these boards and measure 1 3/4" from the middle of the angled edge.
With the hole positions marked on both ends of your top shelf boards and the top end of your end boards, you can begin drilling. Since I will be using 1/2" threaded rods, I drilled these holes with a 5/8" bit. This extra eighth of an inch will make it easier on you when assembling the final piece.
As for the bottom shelf, I decided that I wanted about a foot of clearance between the bottom 2x4s and the ground. To make a nice even number (and since the boards are really only 3.5" wide), I chose to drill my bottom holes 13" from the angled end of the leg pieces, and once again 1 3/4" from the edge. However, since the bottom shelf boards will be protruding from the sides of the leg pieces, I had to do a little extra math to figure out the exact points along these boards that I need to drill, relative to the angled leg pieces. Time to bust out the Pythagorean Theorem!
----------
Disclaimer: I'll be honest with you here. Although it's entirely possible to determine the precise points to drill using angles and equations, I was a few beers in at this point, and my head started to hurt when I pulled out the protractor and calculator. A much simpler (yes, slightly less precise, but much simpler) way is to lay out your pieces on the floor and line them up by eye. With the top pair of holes drilled in my legs and top shelves, I used a tension rod to line up these holes and keep them in place. Then I took a 2x4 and laid it on the bottom edge of my leg pieces, rotating them until their 15º angled edges sat flush against the base piece. With three of my four pieces sitting in place, I was able to lay out my bottom board, ensure that it was sitting perfectly symmetrically relative to the leg pieces, and measured 13" from the base piece and 1 3/4" from the edge of the board. Voila! I now have the hole locations for the last pair of holes, and with (hopefully) only a couple millimeters of error.
----------
Now that I have a top shelf board, bottom shelf board, and a leg board fully drilled, I can essentially rinse and repeat on all of the subsequent pieces. Although my last example of precision left a lot to be desired, it's really important that you take every precaution when measuring and drilling the rest of your holes relative to your initial pieces, as you want everything to line up perfectly flush in our next step...
Step 3: Cut Threaded Rods and Test Assemble
With all of your pieces now cut and drilled, you've almost finished your assembly process. Stack them on top of one another roughly and you'll have a close approximation of how deep your finished project will be. To see exactly how long you need your threaded rods to be, you can slide one through a couple of your newly-drilled holes until it's flush with the floor. It's important to note that, when fully tightened, your wood boards will be more tightly compressed together than they are lying on the floor right now. With that being said, mark off the edge of your threaded rod relative to the depth of your leg boards using a Sharpie. For me, this was right at 16" long.
Remember that hacksaw mentioned in the tool inventory earlier? Well it's time for it to shine. Make sure your rod is clamped down nice and securely. Aluminum threaded rods are pretty soft when it comes to metals, so it shouldn't take you long to cut right through it. When you get close to the end of your cut, you should be able to bend the rod and snap the end off. This end will be very sharp, so we'll need to file it down to be soft to the touch. Be careful with this step, however, because you need to preserve the integrity of the threads while filing off the sharp edges left from cutting. If the tip of your thread isn't filed properly, you'll be unable to get the nut on during your assembly (trust me on this one...).
I decided I wanted to use a spade bit to make recessed holes in my front and back leg pieces to conceal the rod tip and nuts when the tension rods were secured. If you haven't done so already, now is the time to decide which two leg pieces you want displayed in the front of your finished product. Once assembled, the only board faces that you'll be able to see well will be the four front-most boards, so choose your two leg pieces that have the best wood grain pattern. For the back two, it honestly doesn't matter. Using a 1 1/8" spade bit (large enough to accommodate the size of my washers), I drilled approximately 1/2" into the pre-existing rod holes for my front and back pieces.
Speaking of which, I encountered an issue that I had not seen up to this point in my woodworking journey: it's a huge pain trying to drill holes on top of already-drilled holes. This is especially true with a spade bit, which is really doing more cutting than it is drilling. If you go this route, be prepared for a bucking drill and some curse words. It's really all about finding the right ratio of speed and pressure to prevent your spade bit from getting stuck. In retrospect, a hole saw probably would have done a better job.
At any rate... now you're all set for a test assembly! I found the easiest method here (and for the final assembly) is to lay all of the pieces down on the floor and, one by one, thread the rods through the holes. This will take some effort, as the pieces wont just slide together harmoniously. Having a hammer or mallet to help tap the rods in further as they get stuck will save you some stress. Once the rods are in, you can carefully tip the structure up and crank down the washers and nuts to see how it fits together. The top and bottom edges of all your boards should (hopefully) be level.
Step 4: Final Cutting, Sanding, and Applying Stain / Finish
Now that you got it all together, standing up nicely and looking great, it's time to... lay it down and take it apart again. I know, I know... but you do want to make sure it fits well before you finish it, right? If any of your pieces weren't cut or drilled right, or if the ends of any of your boards weren't flush with the others, this is your chance to go back and fix or replace it with a new board.
There are a couple of things we'll need to do before we get to my all-time least favorite step of the woodworking process: sanding. The first thing is cleaning up the recessed holes that we just drilled. A Dremel and small grinding stone worked perfectly for me, but if you don't have these at your disposal you can accomplish the same result with some small scraps of loose sandpaper. Lastly, I decided that I wanted to give the piece a slightly sleeker look by rounding the edges of the protruding ends of my bottom shelf boards (and I foresaw the inevitable incident of me hitting my shin on them as I turned the corner into my living room...). I didn't want the ends to be completely rounded off, just the edges, so I grabbed a pencil and my jigsaw and set off to trim off a bit of the edge.
Now it's time to grab your sander (I prefer using a random orbit for most jobs) and get to work. You'll want to be thorough here since this is a piece that you'll be showing off in your home and setting your prized record collection on. I still wanted the final look to be very angular and clean, but also not something that had edges and corners that were too sharp.
Once completed, it's time to stand and/or finish your wood. I feel like I rave about Danish Oil in every Instructable I author, but it's just so easy to work with and I've never met a stain that's given a result I've been happier with. I feel like most stains hide the natural wood grain of your materials, but Danish Oil really makes it shine and gives it character. I chose to use two different colors to give the leg boards and top/bottom shelves slightly different looks, but the difference in color was slight. I may have chosen some more highly contrasting shades in retrospect. Whatever you decide upon, whether it's just stain or just finish or both, you're almost done.
The last thing I decided to do was a poor man's powder coating on my washers and nuts. I thought this would make the finished product look less like it was just 2x4s and cheap aluminum hardware, and I think it definitely helped. I just took a can of matte black spray paint and coated all of my nuts and washers. It certainly doesn't offer the durability of powder coating in terms of chipping, but it was a quick/easy solution.
Step 5: Final Assembly and Display
It's dejavu all over again! Time to reassemble. With your wood fully dried after staining/finishing, you can carefully reassemble just as you did before. Take caution when cranking down your nuts and washers so that the hardware's paint doesn't chip when tightening down.
Since you're now dealing with about 90 or so total feet of 2x4s it may be on the heavy side, but once you have your piece in place, you can make sure that the shelves are level before cranking down the nuts all the way. Once fully assembled and tightened, this will be very sturdy, all without a single screw, nail or drop of glue.
Now it's just a matter of setting up your stereo equipment and hooking everything up. You can use small hook screws to help hide your cabling along the back edges of your frame. One great thing about this design is that your records will sit naturally angled, allowing you to easily flip through your collection. That should be it! Hopefully you get inspired by this design, and share your builds below!
And... if you enjoyed this Instructable, please vote for me in the Shelving Contest! Thanks!
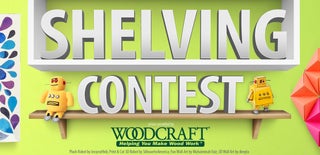
Participated in the
Shelving Contest