Introduction: Recreating an Antique Divers Helmet From Foam
I love the ocean. I can sit on the beach all day just watching the waves do their wavey thing. Sadly, I happen to live in the middle of the Canadian prairies. No ocean to watch here. But there's always the world of make-believe, and what better way to get in the ocean vibe than with an amazing deep sea diver costume. I created this costume pattern to try and recreate the feel of the classic "Mark V" dive helmet which has become an iconic image of divers and the sea. It was used by the U.S. Navy from 1916 until 1984! Let's make one of our own.
Here are the tools and materials I used:
- Pattern: I used the one that I created. You can find it on my website. It includes an adult and a child size.
- 5-8 mm thick EVA foam: I used the foam from an anti-fatigue floor mat, but you can also use the less dense foam from a camping mat.
- 2 mm EVA craft foam: One sheet is enough
- Vinyl tubing: 3/8" outside diameter
- Wingnut: 1
- Super Glue
- Hot Glue Gun: I love my glue gun because it is adjustable temperature. I like to use it at as low a temp as possible so that the glue cools quickly.
- 6 & 8 mm leather punch
- Cutting Surface
- Gluing Surface: I absolutely love using a silicone baking sheet. Nothing sticks to it.
- Sharp Knife: If it is not really sharp you will have a terrible time when you are cutting the foam. I like to use a scalpel.
- Blowdryer: Used for heating the foam so it can be shaped.
- Ballpoint Pen
- Scissors
- Paint: I used Liquitex Basics "Mars Black", Liquitex Basics "Bronze" and DecoArt Americana Decor Metallics “Vintage Brass”
- Rubber Gloves
Please note, the above links are affiliate links, and I do get a small commission if you buy through these links. It doesn't cost you any more and it helps me out!
Step 1: Safety First!
It's fun to get started, but you want to stay safe so that you can enjoy your amazing creation!
- Wearing the dive helmet severely limits your vision. Be very aware of the activities you are taking part in so that you do not get into a dangerous situation. Children should always be supervised by an adult to ensure their safety.
- Some EVA foam contains a chemical called formamide. There are some people that say there isn't enough formamide in EVA mats to be harmful, and others that say there is. Do your research and come to your own conclusions. At the least, I would say it is a good idea to open your foam mat up and let it sit in the sun for a day or two, as most of the chemical will off-gas from the foam. Or buy foam that is labelled formamide free.
- Do not wear your helmet until all fumes from glue and foam are gone. The helmet is a fairly enclosed environment and you only have one set of lungs.
- Do not block off the viewports with glass or plastic. These are open to allow proper airflow for breathing. Closing them could cause suffocation.
- Sharp knives and hot glue can cause injury. Be sure to use in accordance with the manufacturer's instructions.
Step 2: Print and Cut Out the Pattern
The pattern I used is made to be printed on a standard home printer, therefore it is necessary to tape some of the pages together to create the larger pieces. If you hold the pages up to a window, you can see the alignment crosses through the paper and get them taped together perfectly.
Cut the pattern out of the paper, cutting as close to the line as you can without removing the line.
Place the pieces on the foam and trace around them with the ballpoint pen, holding them firmly so that they don’t move while being traced. Many pieces will need to be flipped over and traced again as indicated on each piece. This is especially important if you are using foam with only one smooth side.
It is important to mark the labelled alignment points around each piece. They help so much in knowing how to line everything up later. Extend them in from the edge of your pattern once you finish tracing each piece.
Mark each foam piece with its number, and if it is a flipped piece, add the letter "a" after it: 1a, 2a etc.
Step 3: Cut Your Foam
Using a sharp knife, cut out all the foam pieces that you traced earlier, cutting directly on top of the pen line. I like to use surgical scalpels for this as they are very sharp and allow me to make tight curves.
Make sure to keep your fingers away from the scalpel blade so you don't cut yourself!
If you are getting a rough edge on your foam, your blade is too dull and you need a new one. Or you can sharpen it if you have a sharpener and know how to use it:)
Step 4: Foam Forming Fun!
Heat pieces 1, 2 and 3 one at a time with the blowdryer, and mold them over your knee to give them a rounded shape. If you are using textured foam, keep the texture to the inside.
Repeat with pieces 1a, 2a and 3a.
Step 5: Before You Glue...
If you use hot glue, just glue a small section at a time and hold it together while also pressing the seam down onto your gluing surface. Hold it until the glue cools. Then move on to the next section. This is a lot faster if you use a glue gun with adjustable temperature control because you can set the gun to a low temperature so you don't have to hold the pieces together as long.
As you get used to your glue gun, you can also try wiping the glue off the seam just as it gets cool, giving you a nice clean seam. Just be careful not to burn yourself on glue that is still hot!
Another tip for clean hot glue seams is to rub vigorously over top of the seam after the glue has completely cooled with some scrap foam to clean it up. I have a little video about getting nice hot glue seams that you can watch here.
I have changed my technique over time and find it easiest to glue with the finished side up rather than down against the silicone mat. This means that I will basically make the helmet inside out until near the end, at which point I will turn it right side out.
Step 6: And...Start Gluing.
Using your hot glue gun, start by gluing together the V-shaped cut-outs on pieces 1, 1a, 2, and 2a.
Glue pieces 1 to 3 lining up alignment marks 10 and 11.
Glue piece 2 to the now combined piece 1 and 3, lining up alignment marks 6, 7, 8, and 9.
Now glue the other edge of piece 2 to the edge of piece 1, lining up alignment mark 4.
Repeat these steps with pieces 1a, 2a, and 3a to form the opposite side.
Step 7: Two Halves Come Together. Excitement Builds.
Glue the two halves together, starting with the long seam down the back.
Before you glue the two shorter seams, turn the helmet right side out.
Now you can glue the two short seams on the front of the helmet.
Glue piece 4 to 4a to create a ring.
Glue this ring to the bottom of the main helmet body. Line up one of the seams on the ring with the front centre seam on the main helmet body. Then line up the other seam with the rear centreline and glue into place. Now work your way around the seam and glue a bit at a time until the ring is evenly and completely attached to the main helmet body.
Step 8: The Faceplate
Glue the ends of piece 5 together to make another ring, and then glue the flat side of the ring to piece 6. Line up the marks on piece 5 so that they are in the centre of the flanges on opposite sides of piece 6. In other words, you want the thickest part of piece 5 where the tabs come off piece 6.
Glue the completed faceplate (pieces 5 & 6) to the front of the helmet, keeping the flanges on the faceplate horizontal across the helmet.
Step 9: The Side Viewport
Glue piece 9 and 9a over the holes on the sides of the helmet body.
Take two piece 10s and two piece 11s, and glue them together with the slots interlocking to make a grid. Repeat for the second grid.
Glue the grids onto the two side viewports.
Step 10: The Top Viewport
Form a ring with piece 7 and glue the ends.
Glue piece 7 to piece 8, this time lining up the narrowest part of piece 7 with the centre marks on piece 8. Once those two spots are glued, work your way around until the pieces are all glued.
Glue the top piece over the rectangular hole on the top of the helmet body.
Cut diagonally on each end tab of the grid (piece 16).
Glue the grid over the top hole.
Step 11: Bits and Pieces
Glue two of piece 12 together. Glue it to the side of the faceplate so that the smaller tab on the faceplate goes in the gap.
Curve the tab on the faceplate down and glue it into place.
Glue the front grille (piece 17) diagonally over the front faceplate.
Stack and glue three of piece 15 together. This stack gets glued on the opposite side, directly under the larger tab.
Step 12: The Breastplate
Heat piece 11 with the blowdryer. Curve it so that it bends gently in half.
Line up the tabs on piece 11 with the centre line of the helmet. The tabs are glued on the outside of the helmet and positioned so that the top edge of the breastplate slightly overlaps the bottom edge of the helmet (about 1 cm). This helps piece 11 to keep its curve once it is glued down.
Once the front and back tabs are glued, glue along the sides (where the shoulders would be) and then glue the rest into place.
Step 13: Long Strips of Foam
Cut a strip of foam in accordance with the pattern (measurements depend on the size of helmet you are making) Glue this strip over top of the seam between pieces 4 and the helmet body. When you get all the way around to where you started, cut off any excess length so that the ends of the strip meet nicely.
Cut a strip of foam about 1/3 the width of the previous one. Glue this strip down the centre of the wider strip. Again trim off the extra.
Cut one last strip of foam according to the pattern measurements. Glue this strip of foam, starting at the centre back, all the way around the outside edge of the breastplate, and cut off any excess.
Step 14: Valve Assembly and Transceiver Recess
Glue piece 13 on top of piece 14, then glue it in place on the helmet.
Glue the ends of piece 18 together to create a tube. Glue piece 19 on top of that tube.
Glue piece 21 on top of piece 19 and glue the two flanges down to the outside of the tube.
Glue piece 22, 23, and 24 in order on top of each other to complete the valve assembly.
Step 15: Nuts, Nuts, Nuts....
Use some 3/8" outside diameter vinyl tubing, and cut it into 12 short pieces using the tubing cut guide in the pattern.
Cut 12 foam discs using an 8 mm leather punch.
Push a foam disc into each tube pushing it back so there is a little space in front of it. Use a small stick or something similar to do the pushing.
Apply some super glue around the inside edge of the vinyl tubing and quickly push the foam disc forward so that it is flush with the front edge of the vinyl tube.
Step 16: ...and More Nuts
Glue the ends of all piece 20s together to make 12 little rings.
Spread glue inside each ring and then squeeze it around one of the vinyl tubes you made in the last step. The vinyl tube should be flush with the back of the foam but stick out from the top side. Hold it until you are sure the glue has cooled completely. Repeat 11 more times:)
Glue the nuts equally spaced around the dive helmet rim.
Step 17: Weight Rings and Name Plate
Make 2 loops by gluing the ends of piece 25 together. Cut a little off one edge to create a flat spot, and glue them to piece 26.
Now you can glue those two loops onto the breastplate.
If you would like a nameplate on the front, you can use a pen to etch whatever you would like into piece 27. Just draw your design and then go over it a few times with decent pressure until you have compressed the foam.
Step 18: Faceplate Embellishments
Glue a wingnut to the faceplate tab.
Use super glue to glue some 6 mm foam discs to the four points of the faceplate grille.
To make them look like screws you can cut two slits across the surface of the discs, and then cut perpendicular across the bottom of those cuts to remove a little strip of foam.
Step 19: Paint It Black
Paint the helmet black. Give it at least three good coats of artists acrylic paint.
Step 20: Rub on Some Copper
I used Liquitex Basics bronze acrylic paint to colour the main body copper. (See completed picture for reference)
Don't use it like normal paint though. Squeeze a little on a piece of paper, and then with a rubber glove on your hand, rub a little on your finger and then rub that lightly onto the black painted surface. It takes patience, but produces a great result!
Step 21: Rub on Some Brass
Use the same technique to apply the brass colour to all of the accessories and foreground areas.
For this, I used DecoArt Americana Decor Metallics “ Vintage Brass.”
Step 22: You're Done! Give Someone a High Five.
Thanks for hanging out with me!
If you'd like to see more of my projects you can find me here:
Subscribe to my YouTube Channel: https://goo.gl/v5clos
Follow me on Instagram: https://www.instagram.com/lostwaxoz/
Check out my pattern shop: https://www.lostwaxoz.com/shop/
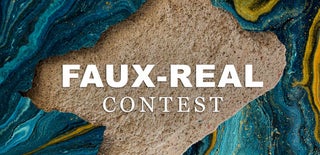
First Prize in the
Faux-Real Contest