Introduction: Refurbish an Old and Rusty Cast Bell at TechShop
I have an old bell that has seen its better days.
By utilizing a couple of tools available at http://techshop.ws/ts_chandler.html TechShop in Chandler, I intend to refurbish this bell.
I will be using a media blaster (commonly called a sandblaster) and the powder coating station.
In the first photo is the bell after I have disassembled it and did a basic cleaning with a metal brush and air-gun.
The second photo shows the comparably cleaned yoke of the bell.
Step 1: Media Blaster
The Media Blaster (or sandblaster) is used to remove paint and rust from parts.
The blaster can also be used as an intentional abrasive, for example to etch patterns into glass or other surfaces.
The reason this device is called "media" blaster rather than just sandblaster, is that many different types of abrasives can be used within the machine each with their own characteristics. Walnut shells are a common, soft abrasive.
For this task, I am using a common silica abrasive.
Note: I failed to take a picture of it - but operation of this machine is triggered by a foot pedal - not some trigger on the air gun.
Photo Descriptions:
1) I show the door in an open position to insert objects for blasting.
2) This photo into the chamber shows hands inserted into the gloves holding the airgun and a part.
3) The valve for air must be on for operations.
4) The switch on the left operates in series with...
5) the switch on the right - to provide lighting and operating power.
6) This image through the window shows a part being blasted by the abrasive.
A video (sorry for the length) shows the blaster being used to clean the yoke.
And a quick video showing the clean parts.
Step 2: Washing Parts
A quick washing of the part to remove grease and contaminants should be performed prior to the powder coating operation.
For most metals, Trisodium Phosphate (TSP) is an excellent and minimally hazardous choice.
Note: This is not a good choice for aluminum parts.
While washing the parts, I have the oven preheating.
After a quick wash, each part is hung from a conductive wire hook (for the powder coating operation).
Step 3: Prepare the Powder Coat Gun
The powder coat chamber provides a safe place to apply the powder coating resin to your metal parts.
The chamber includes a fan to suction off the airborne dust.
The gun allows siphoned powder to be positively charged and blown towards your parts.
You should inspect and clean the gun prior to use. This ensures the proper operation for you. It also prevents a prior paint color from contaminating your project.
Step 4: Powder Coat the Parts
Powder coating is actually quite simple.
The gun acts as a positive source and the parts act as the negative.
You connect a lead from the gun controller to a metal portion of the cabinet where you have hung your parts.
Each squeeze of the trigger causes a small puff of paint to be blown past the electrode of the gun and into the air.
The newly charged paint particles are attracted to your part thus reducing waste paint.
Pressure and voltage levels for your gun should be tested prior to applying paint to your parts.
A quick "puff" into the chamber allows you to see the current settings.
I used a fairly low pressure and voltage set to about 70.
It should be noted that while the risks are minimal - you should NOT allow the gun to get closer than three inches to your parts or the cabinet while spraying. The finely dispersed paint resin is flammable - the spark from the gun getting close to the part may ignite the powder.
Step 5: Fire (Bake) the Parts
The final step of this process is to fire the parts in the oven.
We have two different sized ovens here at the Chandler TechShop, my parts were small and best suited for the smaller oven.
But the smaller oven had not been installed at the time I did this project - so the larger oven was used.
The instructions on my paint resin provided the oven settings (400° for 10 minutes) which I followed.
I had pre-heated my parts prior to the powder coat application, and I allowed some time for the parts to heat up before counting the 10 minutes.
The use of the non-contact thermometer allowed me to verify when the parts had heated up properly.
Once done, I allowed the parts to cool off in the oven with the door slightly opened.
Then assembly - and - finally I have my old bell looking as good as new.
Thanks for the great facilities! I made it at TechShop!
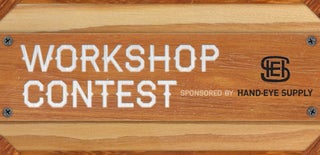
Participated in the
Workshop Contest