Introduction: Restoring a 100 Year Old Vise!
Vise Restoration - 1910 Chas Parker 205-P
I picked up this vise from a metal scrapper, he was ready to throw it away and I couldn't let that happen. This vise is close to 100 years old and over its life its clearly had some issues. In this intstructable I will go through the process of restoring it, and giving it a chance at a new life. There is a video embedded below that goes through the entire process, and for a detailed write up head into this instructable. This is also entered in the “FIX IT” contest so if you enjoy it please vote for me! Enjoy!
Step 1: Removing They Beautiful Piece of REBAR
When I saw this vise for the first time this rebar stuck out like a sore thumb. Parker vises are notorious for having difficult to replace jaws. I got this vise from a metal scrapper so I can only assume someone lost one of the jaws and just mig welded this piece of rebar onto the vise to get them through the job. I was very excited to get started on this restoration just to remove this rebar! I started with an angle grinder and a hammer to loosen up the rebar and eventually was able to smack it off. This vise is cast iron so i knew the welds on it wouldn't hold up very well.
Step 2: Removing the Factory Jaw
The factory jaw of the vise was also welded on, so that had to go. These vise jaws were originally pinned in place so I guess once the first jaw got lost he previous owner wanted to make sure this one wouldn't disappear. To remove this one it was just a matter of cutting/grinding the weld away, removing the pin and talking nicely to it by way of a mini sle
Step 3: Disassembling the Vise
These old vises are very simple and are only held together by a few major bolts. The largest of which is in the base, i didn't have a socket large enough to fit it so I used an adjustable wrench to grab it and a large pipe wrench to get it loose. I then proceeded to remove the rest of the base parts and set them aside.
I removed the lead screw nut from the dovetail slot it sits in with a piece of scrap metal and a hammer.
After that was complete I removed the handle and lead screw by taking off the single plate that holds them in place using a flat head screwdriver.
Step 4: Removing the Old Paint
I began this process with a crimped wire wheel and used a few different style wire wheels to get off al the old paint. I chose to do this outside and made sure to wear protective gear during this process. Wire wheels are notorious for spotting little wire strands out like shrapnel and i found pieces of wire in my clothes for a few days after this process. I wore a full face shield, gloves and my welding jacket to protect myself. Also, doing this outside kept all that dust out of my shop which is always a good thing!
Once I was finished with the large parts that I could do with the grinder i moved inside to the bench grinder and wire wheeled some of the smaller parts
Step 5: Test Assembly Number 1
With my eyes set on rebuilding the jaws for this vise i put it back together to get a sense of how they would fit up. As i mentioned earlier, these are very simple in their assembly so it only takes 5 or so minutes to get one from a pile of parts to a working tool.
Step 6: Milling New Brass Jaws
I had envisioned a method for milling these new jaws in advance and ordered material a couple weeks before the project to do so. The material i purchased was c360 solid brass bar in 1 1/4” x 2” x 12” long. As you can probably guess, this piece of brass was EXPENSIVE. So in order to make sure i didn't ruin it i cut a piece of pine to those dimensions and did a test run of my milling operation to see if it would work. My plan was to mill a 5/8 slot first, then follow it up with a 135 degree dovetail cutter which would provide me with 1 piece of material that could be split into two jaws.
After doing my test and seeing that it would indeed work i set over to the Bridgeport and make some chips. The end mill I used was a 2 flute solid carbide and it flew through the brass with ease. All in all the milling op was very successful.
Step 7: Fitting Up the New Jaws
When the jaws came off the bandsaw they didn't really fit great. The Parker vises are notorious for having an uneven angle on the vise body themselves. For this reason many people that make vintage vise jaws don't offer replacements for the Parkers. My angle was off a little bit with my 135 cutter, so I had to spend some serious time on the grinder. I spent probably 30 minutes on and off the grinder refitting the angle and going back and forth checking against the vise.
I finished up on the belt grinder and let the shop for the night and the next day I decided to go a little bit further and adjust the fixed jaws on the vise with a 3M cubitron disc on the angle grinder. I took little steps with the wheel and checked periodically to make the fit as good as I could get it. I wanted to make sure the jaws sat nice and flat and didn't have any rock or wobble.
Step 8: Drilling the Jaws for New Pins
The pins go through the vise body and the jaws at an opposing angle to the angle cast into the vise itself. Since I don't know this angle i figured the best way to chase that angle was to clamp the brass jaws to the vise and drill up through the factory hole with a long “probing” drill bit. The factory holes were approximately 17/64” ( 1/64” over 1/4”) The probing bit was 1/4 so it ran inside the factory hole very well, and since the vise is steel and the brass is soft I didn't have any concerns about damaging the factory holes.
Once I had the pilot holes drilled at the proper angle with the 1/4” drill bit I went back and chased all 8 holes with a 17/64” drill.
Step 9: Making New Pins and Installing Them
I had 5/16 stainless steel rod laying around and I thought it would make a good material for the pins. I made a quick little jig using the 2 x 72 grinder an a 80 grit belt. The illustration shows how I have a 1-2-3 block set up on an angle to drive the stainless rod down to the correct size. I use a small drill to spin the pins as I feed them into the block and belt to turn them down.
I chamfered the ends of the pins to help persuade them in to the holes drilled in the brass and steel. A little bit of banging around and they were set. These opposing angles made the new jaws extremely tight and I was really happy with the way they fit up.
Step 10: Shaping the New Jaws
This was the best part of the whole restoration. Shaping these jaws was like power carving but in metal! I used a fresh 3M cubitron grinding wheel. I took down the brass to a nice looking curve that matched the shape of the vise body. I worked up a with grits a little bit to lose some of the heavy scratches and blended everything nice.
I then closed the vise and used a cutting wheel to slice both jaws simultaneously and get them square to each other. This worked out well enough and squared everything up nice.
Step 11: Final Prepping of the Bare Metal Parts
After shaping the jaws I took the vise apart again to do some final prep work on the parts before paint. I used a polycarbonate paint stripping wheel to get everything that would be metal on metal. These paint stripping wheels cleaned up the parts really nicely and got anything that he where wheels didn’t. What I like about these in particular is that they don't take away any considerable amount of metal.
Step 12: Masking Off for Paint
I masked off the bare metal vice parts with blue painters tape. I also decided not to take off the brass jaws and just tape them over to keep them rom getting paint on them.
Step 13: Paint!
I decided to use “hammered” spray paint to get the look i was going for on the vide body. I put 5 or 6 coats on the vise and gave it time between coats to harden. I then gave the whole thing 48 hours to fully dry and cure.
Step 14: Buffing the Handle
I decided to go with a polished handle and threaded rod end. Using the bus buffer and green compound I went over the handle and the ball end for 10 or 15 minutes, adding compound a little bit at a time. The handle turned out pretty nice after some cleaning up.
Step 15: Removing the Masking
Its always fun to reveal a bunch of parts once they have been painted. The parts turned out really nice with the hammered paint.
Step 16: Highlight the Raised Text
From the beginning of this restoration I knew i wanted to go with black and gold. I got myself an oil based gold paint marker to highlight the raised text on the handle, vise body, and parker emblem that holds the handle in place. Using a paint marker to color over raised text like this is really easy! It does take a bit of a steady hand, but its much easier than using a brush and pin striping paint.
Step 17: Reassembling the Vise
I used Red’N’Tacky grease on all of the metal on metal parts to keep them moving smoothly. The only part I didn't grease up was where the drum brake style internals run against the base. I also made sure to grease up the threads liberally to make sure they ran well and the action was smooth.
Step 18: DONE!!
This was a lot of work but man I'm so happy with how it came out!! Don't forget to check out the youtube video showing the whole process, and if you have any questions let me know down in the comments! If you like this, vote for me in the Fix It and Metalworking Contest! Thanks!!
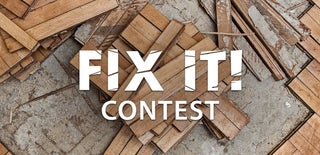
First Prize in the
Fix It! Contest