Introduction: Sapele Wood Makeup Box
I set out to build a makeup box as a Christmas present. The final
result came out almost entirely the way I intended when I drew up my original late night sketches. Which was so satisfying for me to see a goal come together with all of my added complications. Everything revolved around the pattern I wanted inset on the box walls, and I was able to fill my time waiting to gather all of the parts I needed by photoshopping the pattern in to a useable template.
You can also view this project on my website: AbsurdProjects
Step 1: The Walls
I tried three different ways to transfer my template on to the
wood. The first method was to use dark iron-on fabric transfers which yielded essentially no transfer. The second method was printing the pattern on to freezer paper then ironing that on to the wood. My printer tore apart sheet after sheet of the freezer paper, even after sealing it on to a solid backing. Finally, my boss explained to me that the proper way to transfer a pattern on to wood is using graphite transfer paper. This worked like a charm, but took hours of scratching at the pattern, then touching up all of the missing spots.
Step 2: Routing the Pattern
After straight routing a perimeter to the pattern I free-handed the removal of the inset using a 1/16″ router bit.
Step 3: Cutting in to Wall Pieces
All of the original boards came 1″ thick which was too much to leave
the correct amount of space inside the box. I used a straight router bit, various jigs and several passes to thin the wood out within a reasonable size. Then I cut the pieces in to four walls and chamfered them where they would join together.
Step 4: Staining
What followed was two coats each of ebony stain for the inset and
natural stain for the pattern. I did my best to leave the upper and lower edges the natural finish of the wood, but my mineral spirits left those tinted.
Step 5: Struggling to Make the Base
I did not want to use a secondary wood for the base, but instead
make it out of the same Sapele as the rest of the box. I made three bases from the Sapele, but with each attempt my method of planing it down with a straight bit to a reasonable thickness left me with wood that was far too textured for the risers I intended to adhere to it. Finally I yielded to using a nice piece of Luan wood which cut beautifully to the exact dimensions I wanted.
Step 6: Forming the Legs
The legs were a bit of a freeform design. They are hand sanded to
shape with the exception of the deep groove which I carved most of the way using a narrow dremel sanding head.
Step 7: The Trim
I wanted to make sure that the mouldings for the base were made from
the same wood as the box. I used a very small classic roman ogee bit and carved it along both sides of a plank. I straight routed the plank along both sides down to the height I wanted the mouldings, then used a table saw to cut them free.
Step 8: The Lid
Suprising to me, the lid came out so close to how I had originally
sketched it. Key differences being that I switched from using SOSS hinges to quadrant hinges which are correct in a makeup or jewelry box like this. The other difference being that I decided not to do a garnet perimeter inside the upper dome, cast in resin (like this, but with garnets instead of sea stones). I thought there was too much risk of it maybe looking tacky and too much risk of ruining the lid. I’ve tried using cast resins a few times before and have never succeeded in getting it to set nicely.
Step 9: Lid Continued
The lid has an inner and outer dome, a doubled inset with round
routed edges on the inside, a round-over lower outside edge and a decorative ogee upper outside edge. The topside of the lid was domed using a belt sander and finished by hand. The inner dome was made by trying out various dremel heads. It’s all finished with a decorative removable mirror covering the inner dome. It was important to me that such a narrow mirror be removable so that she wouldn’t have to bend over and struggle to use it at whatever angle needed. I wrestled a long time over how to make the mirror removable, but settled on one friend’s perfect suggestion of velcro. I wasn’t confident that I could make a mirror setup out of wood that would stand up over time and not risk damaging the lid; though I thank several friends for their very clever suggestions at how best to do that.
Step 10: Box Joints
I feel that there is something uniquely disappointing about opening a
mystery box to find it empty. So when I originally sketched this up I wanted to have the inside purpose-built with two tall inner boxes for narrow items like eyeliner or mascara brushes and lower compartments for other random paraphernalia. I wanted to make the boxes unique from styles I’ve used in the past (typically butt or chamfer joints), so I tried my hand at making box joints. I resolved to make one narrower box of purpleheart and a denser one of yellowheart wood.
Step 11: Internals
Making box joints is not nearly as easy as they make it look in the
videos. Every tooth has to be sanded individually. For whatever jig you use to make them, my major stumbling block was making certain that the distance between your blade and your key remains precisely the same distance as the actual diameter of your blade. If this measurement is off slightly it will multiply across your work piece and your teeth will be out of line with each other. Routing should also be done gradually with several passes as even the best router bits will chip large splinters out of the wood like teeth off a meth head.
Step 12: Internals Continued
The most painful obstruction in this undertaking was not being able
to make the second box out of yellowheart. I did still get to use what yellowheart I had to make the risers for the lower compartments of the makeup box.
Step 13: Finishing
I’ve used polyurethane to finish just about every wood project I
have made since the age of four when my father first cracked me open a can. For this, I used brush lacquer for the first time and I was bent on doing it perfectly. I set alarms throughout the night for every two and a half hours to make sure that all four coats were applied exactly two hours apart. My last going on only an hour before leaving to work.
I was forewarned about the potency of lacquer, but underestimated the fact that this is some seriously toxic shit. I cannot emphasize enough the importance of adequate ventilation when using lacquer. An open quart sized can filled my house with lasting toxic fumes.
Step 14: Conclusion
As I fill out this blog post I am in awe that I ever put this
together. This makeup box was the most difficult thing I have ever put together and I’m blessed for the inspiration I had to do it. I am happy to have had the chance to make something so beautiful with my favorite woods in the world, exotic woods I never gave myself the chance to carve before.
Most projects I finish unsatisfied, wishing I had done something differently. All though I look at this and have thoughts of what could have been done better, I am elated with what was made; not wishing to change a thing. As the hours I put in grew, and each piece became its own project, I re-worked every single piece that didn’t measure up and took no compromises. If not for the deep love and deep insanity that drove me to build this, I would not have gotten halfway there.
This box is filled with my love in every piece and cut. I put everything that I had in to turning a singular quixotic soothing vision in to something real. Even though it’s gone from my hands and maybe it’s discarded or caked in dust, it contained two hearts that I can feel, as I can still feel its finish under the tips of my fingers.
Please view this instructable with photo captions on my site: Absurd Projects
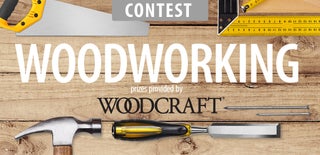
Participated in the
Woodworking Contest 2017