Introduction: Shop Vac Squid Brush
Sometimes you need something you can’t find anywhere else and you don’t care if it looks great as long as it works. It’s just an added bonus if it only costs a couple dollars to make yourself.
I was looking for a way to get into hard to reach places with my shop vacuum and also trying to find a fast way to clean sawdust and other debris out of parts bins without dumping everything out of the containers.
I realized I had some shop vac tools I never really used and thought I would sacrifice a couple in order to make a new fitting to help me with these situations. One of the problems with a regular shop vac is that it has too much suction and can't reach into narrow crevices. You end up sucking up all of the parts you are trying to get the dust out of and then digging through the shop vac bin to find them again.
I ran across some small diameter water line tubing at my local home store and thought I could use it to add a bunch of smaller lines to the end of an existing shop vac tool and make a bunch of very small suction hoses to the end of the large main hose.
Step 1: Tools and Materials Needed
This is a very simple project and should only take you an hour or so once you have all of the materials. An added bonus is that you really only need a few tools.
Materials
- Existing shop vac hose tool you will be modifying
- Flexible small diameter plastic tubing - Tubing I used
- Hot glue
Tools
- Hot glue gun
- Utility Knife
- Drill
- Band Saw (a hand saw could be used if you don't have a band saw)
- Rotary Tool (optional)
Step 2: Measure Tubing
Most of what I wanted to use this brush for was for was for reaching recessed areas that were a few inches out of reach with the regular shop vac hose end. I figured the flexibility of the small tubing that I was using would be rigid enough if it was a couple inches long, but anything longer and the tubing would be flexing all over the place.
I decided to go with a length of 3.5 inches outside of the hose attachment. I really didn’t think I would need to get into deeper areas than that.
I cut the tubing into equal length pieces 4.25 inches long so 0.75 inches would be inside the vac attachment.
You will be cutting the tubing off at an even length after gluing them all in place so don't worry about cutting them off to a perfectly exact length at this point.
Step 3: Prepare the Attachment
Since I am going to be cutting down the area of the opening in the end of the hose attachment by quite a bit I decided I had better cut a hole in the back of the attachment to allow for more airflow. I didn’t want to overwork the motor in the shop vac every time I used this brush.
I assumed this hole would be easy enough to cover with your hand while using the attachment to get more suction, but wasn't positive.
I decided to cut the hole in the part of the attachment that is most like a cylinder and used a matching part from a nearly identical handle to make a cover that could be used to control the amount of suction to the attachment. I cut the cylinder part out of the matching piece and cut a potion out of one side of the cylinder. See the pictures for more detail. This allows the cover to slide over the attachment and cover as much of the new hole as you want.
I did forget to take into consideration the part of the shop vac hose that extends inside the attachment, so some of the hole I cut into the attachment is covered (from the inside) with the end of the hose. You may want to adjust where you cut the additional hole in your attachment due to this.
Step 4: Glue the Tubing in Place
The next step is where you glue the tubing into the hose attachment. I used a hot glue gun to make this a fast process. I wasn't really sure what to use, but decided to try hot glue as a way to try out the concept. I decided if the hot glue didn't hold well or started coming apart then I could remake the squid brush with some other type of adhesive. Maybe epoxy would be a better long term adhesive, but would take longer to use.
Before I started gluing the tubes inside the attachment I thought it would be good to rough up the inside of the attachment opening using a Dremel with a grinder disc on a rotary tool. I thought that might help the hot glue stick to the surface better by making a rougher surface. This is really up to you.
I took some of the tubing pieces I pre-cut and held them inside the opening to see how well they fit and what pattern of the tubing layouts would work best.
I decided the best thing to do was to start on the bottom at one side with the first piece and move across from there.
The next row of tubing I placed in between the tubing in the first row. Then I just kept filling in row by row.
The last couple pieces of tubing were a little more difficult to install since I wanted to be careful not to plug the end of the tubing with hot glue as I inserted them.
Step 5: Cut the Extra Tubing Off
One I had all of the tubing in place I needed to cut the ends at the same length.
I marked each row of tubing with a permanent marker using a straight edge.
I then used a new razor blade to cut each tube at the marker line. Be sure to have something under the row of tubing to support it as you cut.
Step 6: Testing
I tested the completed brush in a variety of situations. One of the main reasons I wanted this brush for was for cleaning out sawdust from containers of parts. The other reason was for cleaning deeper recesses such as some of the areas under my table saw that always hold sawdust and the full size shop vac hose will not reach into. The 2-1/2 inch diameter shop vac hose was just too large to get into those tight areas.
You can see that the squid brush does a great job of cleaning in grooves and holes of various sizes. The tubing is flexible enough to conform to the shape of the area, but rigid enough to hold it’s shape.
In some of the video testing I used coffee grounds since it makes it easier to see the results. Do I spill coffee in my work area? No, but you might want to use this for spilled coffee in a kitchen drawer full of utensils.
One thing I realized is that you can suck the dust out of very small holes by inserting just one of the tubes into the hole.
I set up a couple deep slot layouts using two pieces of clear acrylic with sawdust poured between them. Watch the video to see how well it pulled the sawdust from the slots.
Step 7: Final Thoughts
This isn't really a squid or a brush, but it looks a little like a brush shaped like a squid. At least I thought so and named it for that. Please post any other names you can think of in the comments below.
I really like the way it turned out. In fact, I made one for my smaller shop vac so I could use it more easily when cleaning out our cars. It has been really useful for cleaning out the cup holders and center consoles.
Is it pretty? Absolutely not, but it is incredibly useful and it was very cheap for such a functional new tool to add to the shop. I already had the shop vac attachments that I made the squid brush out of and the tubing was the only material needed. The 25 foot long roll of tubing cost $3.50 at a local home store. Since I made two squid brushes with the tubing I made each one for under $2.00 if you don't take into account my time to put them together.
I think it worked out well to have the opening cut on the back side of the brush to allow for additional air flow since the tubing drastically cuts down on the amount of open area that goes into the shop vac hose. Being able to adjust the suction by changing the opening size really gives the brush some flexibility.
It's also very easy to use your hand to cover the opening on the back of the brush when you want to increase the suction temporarily.
One thing I didn't think about was the situation where a larger item that is too large to be sucked through the tubing is encountered. If it is sucked up against the end of the tubing it is easy to pull the piece off the end and then just drop it in the new airflow opening you cut in the back of the attachment.
My intent in making this brush wasn't to create something that would vacuum up a large volume of material, but rather to vacuum up a relatively small amount of dust or saw dust from hard to reach places.
If you think you could benefit from making this brush I highly recommend it. I have used both of my squid brushes many times since I made them.
As you can see, the squid brush is great for cleaning the dust out of containers with items like nuts, bolts, and screws. I can’t tell you how many times I wish I would have had this when I sorted through a container of nuts and bolts and blowing the dust out of the pieces with good old lung power. I'm sure I'll be using this more and more.
I hope this is something you find useful or saves you time when cleaning in your shop or around your home.
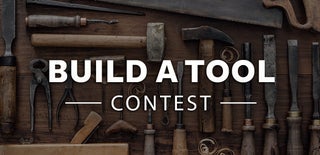
Second Prize in the
Build a Tool Contest