Introduction: Solder Stamping
If I were a rich man,
Daidle daidle deedle daidle dum!
Sorry, I get that song stuck in my head a lot. Mostly because I would love to afford all the new crafty tools and toys, but, you know, adulthood. So instead I research all the cool things and then try to find ways to get similar results on the cheap. I really like the look of embossed metals and got an idea after finding some jewelry solder at an estate sale. After a little research I found out rubber stamping solder is an actual thing! Therefore, something I needed to try. It was surprisingly easy and a lot of fun!
Step 1: Suplies
-Jewelry Blanks
-Lead free solder
-Something Pokey
-Fire! I used a mapp torch
-Steel wool
-Rubber stamps
-Fire Brick
-Metal/flame proof surface
-Goggles (not shown, but I promise I wore some!)
Step 2: Rubber Stamp
When you are picking out your rubber stamp there are a few things you want to watch out for.
- You want a red rubber stamp. The kind attached to a thick wood block. DO NOT use the clear rubber stamps! I can promise you all they will do is melt and waste your money.
- Pick out a stamp with an easy to recognize pattern. You probably don't want a stamp of something, like a cat. Chances are you won't be able to get the whole image on, and it will just look messy and unfinished.
- Make sure your stamp has very crisp, defined lines. Inspect the rubber pad. I found that a shallow cut very detailed print worked best for me.
- Make sure the stamp is clean! In the last picture I have a stamp that is both dirty and has poor lines. The image showed a cool ivy pattern, but when I tried using it. it just looked like a bunch of blobs and the orange ink stuck to the metal.
**unless you want to play around with inky stamps and hot solder, which I am totally going to try at some point**
Step 3: Prepare Your Blank
I fully understand that in a perfect world you should know the material of your blank. Also you probably cleaned it really well. Made sure there were no finger prints or oils on the surface. You probably even put a thin lay of flux where you want your solder to go.
We do not live in a perfect world and I'm apparently lazy with all of these shortcuts.
To be perfectly honest I got some (what I was told was lead free) solder at an estate sale, aaaand a few blanks on clearance. What can I say? I'm a sucker for a good sale and like to try new things.
Anyway. Take your jewelry solder, cut off a small piece and wrap it into a flat circle. Place it on your blank, not too close to an edge.
Step 4: Playing With Fire
I tried using a soldering iron at first, but it was nearly impossible to melt enough solder at once to stamp.
Then I remembered that I got a mapp torch for Christmas.
They are really easy to use. Just turn the knob in the direction the arrow tells you to. Once you hear the gas, push the button. Voila! Fire!
Lower the gas so you have a shorter flame, but be careful not to turn it down too low. You don't want the flame sputtering.
In small circle heat up the whole blank, and then slowly start to concentrate on the solder. Once it melts it will ball up, if you keep the flame on it it will flatten back out in a couple seconds.
Step 5: Stamp It
Once your solder is hot, you have a little bit of time to stamp it. I waited between 5-10 seconds and it was still hot enough to stamp.
Firmly press your rubber stamp into the solder and let it sit there. Wait about 30 second before trying to move your stamp.
When you do, your blank and solder might be stuck to your stamp. That's okay. Just grab your pokey tool and gently pry your blank off. The rubber on your stamp will be a little soft, so try not to rip the piece off too fast. If you are worried, just let it cool on the stamp a little longer. Any extra bits stuck in the stamp can easily be picked out later.
Step 6: Cleaning Up
These cooled really quickly. I picked off some of the solder pieces on the edge just with my fingers. Then I lightly buffed the piece with some steel wool. I really like the color variation that came form the process so I wanted to keep that as much as possible. You could always sand if you wanted to get rid of some of that distortion.
I left my pieces raw, but you could always clean them up and then give then a clear coat.
I'm really digging the distressed look though.
Step 7: Things NOT to Do!
-Leave large gaps in your starting solder.
-Without flux, the solder won't move much, and won't really fill in. You could use this to your advantage, I suppose. If you have something you want to have little gaps in. I felt these pendants were too small for this to be really effective, but you do you.
-Choose a poor stamp.
-I sort of covered this earlier. So we know what to look for in a stamp, but I wanted to show you an example of a poor stamp too.
-I fount this adorable tiny little butterfly stamp. The lines weren't as sharp and I wanted, but were really good for the size of the overall image. I though surely this would work. After a few tries I gave up. It was a huge waste of supplies.
-The thicker lines don't really do well with this. Also, it's really difficult to get the molten metal's surface area big enough to be able to tell what it is a stamp of. Maybe you like the messy blob look. Maybe flux would help with this. Maybe you just call it a loss, like i did.
Step 8: Sometimes, It's Not You, It's Your Supplies.
I wanted to make these two heat halves match as much as possible. I was worried that if I did them broken edges together, the solder spillover would make them stick together. So I decided to do them back to back and have the pattern edges reaching towards the other. To make the solder even I made a swirly "s" and places it between the two. Thinking I could just cut the center piece out when I was done.
However, these blanks melted at the same temperature as the solder. I still tried to stamp it, but it didn't take. I guess this is why it's important to know your materials. I still think it's neat looking and will probably still use it for something. I'm counting this one as a happy accident. haha
Step 9: Finished Project!
I used some steel wool to clean up some of the edges. I like them as is. If you wanted you could always clean them with rubbing alcohol and then give them a good coat of clear acrylic spray. Seeing it's something to be worn, I don't think it would really chip off. If you are worried about that, you could dip them in resin. You could add ink to bring out the design, or layer charms on top of these pendants. I really liked this project because I can see lots of variations that this project could be used for. I hope you can too!
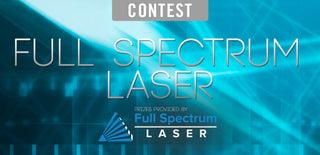
Participated in the
Full Spectrum Laser Contest 2016
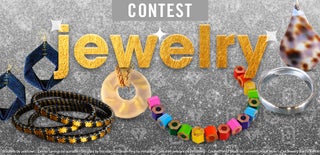
Participated in the
Jewelry Contest

Participated in the
Rainy Day Challenge