Introduction: Split Wood and Alumilite Bottle Stopper
The wood most sought by woodworkers is always the most extreme. On one extreme straight grain is highly desirable for consistency and strength. And on the other extreme we have burls where the direction constantly changes and spalted woods which are infested with colonies of mold are two examples. One feature almost always considered is negative is checking, not so much a flaw in the wood itself as a result of improper drying procedure. Checking is the splitting of the wood often seen at the ends of logs or boards as the moisture leaves the wood more quickly than at the center of the log or away from the ends which causes uneven stress within the grain of the wood. Rather than an annoyance or waste checking is going to be treated as a feature of the wood and highlighted in this project.
The inspiration for this project came from a gift from my brother who lives on and works on a cherry orchard. He made a display dish from a cross section of a trunk of one of the trees when the orchard had been cut down. The dish prominently displayed an interesting pattern of checking and in fact broke apart many times while he was shaping it. Cherries are harvested by large earwig looking machines which spread a net below the branches of the tree and a large set of claws grasp the trunk. Then the machine shakes the tree freeing the ripened cherries. The shaking of the tree also weakens the fibers of the tree making it much more susceptible to checking. With that in mind, I figured if he had some spare wood from one of the trees on his firewood pile, casting some of the log in Alumilite ought to provide an interesting result.
Step 1: Selecting and Preparing the Wood
Sourcing Wood
I was lucky to have access to some of the cherry wood from the orchard from my brother. It was sure to have plenty of checking and weaknesses in the wood from the cherry harvester machines shaking the trees. Assuming you do not have access to cherry trees, I would think your best bet for wood for a project like this would be apple or pear orchards which often cut their trees down after a number of years and replant the orchard. While the wood isn't going to be pre-weakened to make checking easier, it should suffice. Often this wood is simply set aside as firewood. In fact, pretty much any firewood pile should have something interesting to start.
The greener or wetter the wood the better for inducing checking by kiln drying it in the oven. While I haven't tried anything highly figured, I would think that the straighter grain wood I used would be more visually appealing since the viewer will be able to follow the grain pattern across the sections of the wood which are separated with the Alumilite.
Avoid woods which has already been kiln dried as even soaking the wood to re-add moisture will not be nearly effective for inducing checking. I would also avoid woods which have a high oil content, such as exotics. Also very dense woods, common in exotics, would not be very effective.
Cutting Lengths
Using the oven to kiln dry the wood is going to be inconvenient enough as it is, so cutting the wood down to approximate lengths that will fit into the oven is absolutely necessary. Leave only a couple inches either direction on the log sections. For instance, I was planning on doing bottle stoppers which the blanks start at about 2 1/2", I doubled that to 5" for two blanks, and then added two inches for a total of about 7" lengths to start. Other sorts of projects would have different requirements.
Step 2: Creating Checking
As mentioned earlier starting with some of the trees from a cherry orchard which is harvested with shakers will make the wood naturally check as it dries. Inducing more checking will enhance the project by allowing the Alumilite to seep into more cracks. I was determined to enhance this project as much as possible so I came up with a pretty abusive regimen for the logs.
Crushing
Since shaking the tree weakens the fibers in the wood, I figured some crushing of the log segments with the maul would probably help out. With the wood still green and full of its moisture I crushed the log with a maul with several heavy blows. While it left marks in the bark and some of the outer layers of wood, those crushed fibers would be removed when the whole log is milled to size. The stresses from the blows should have been somewhat evened out towards the core of the log.
Baking
Normal kiln temperatures range from 120ºF to 160ºF to pace the rate of moisture loss. I bumped the oven up to 260ºF, well above normal kiln temperatures) to ensure a quick as possible moisture loss in the wood which would provide more stress on the log. This was done for over 24 hours with pieces that were about 7-8" long and about 7" round. Longer logs would take longer, a larger radius would probably not affect drying time substantially since most moisture is lost through end grain rather than long grain. As can be seen from the pictures the results were very encouraging. The bark was coming off while baking so it was removed during one of the 12 hour cycles.
Rehydrating and Freezing
While I was waiting for the log to bake it came to me that another mechanism to add stress to a log and induce more checking would be to soak the log and freeze it since frozen water takes up more volume than liquid water. I place the log in a vacuum chamber weighed down under water. Vacuum was applied for 3 hours to remove all of the air from the log. The vacuum was then released with the log submerged in the water and left for 12 hours for the log to absorb the water. After 12 hours the log no longer floated without the need for weights indicating it was completely saturated. The waterlogged log was then moved to the freezer for 24 hours to allow the moisture in the log to completely freeze.
Final Abuse
After the log was completely frozen the baking cycle described above was repeated to remove the moisture from the log. The log was showing a great deal of checking along through the core of the log and along the outer edges. The log was very brittle at this point and a single blow from the maul split it into several pieces. The larger pieces were split again until there were about half a dozen similarly sized pieces. The small chips were discarded as they will provide larger holes in the final blank which will be replaced with Alumilite.
Step 3: Milling Log Into Blanks
The previous step ended with the log looking less like a log and more like kindling. The log will need to be reassembled to be effectively milled. And as Red Green would say, "We need the handyman's secret weapon duct tape."
Reassembling the Log
The easiest way to start is to tape each of the smaller sections together in pairs. Then combine the pairs together. The tape will not hold the log tightly together, so you should be able to shift the pieces to get the aligned correctly. Once the alignment is correct wrap several courses of duct tape around the log until it is sufficiently rigid so that it will not shift while being sawn.
Milling the Log
It is dangerous to saw on the bandsaw when the material can roll or be pulled down. Use a bandsaw sled to support the log while making cuts. Then ends are squared up first by cutting the log at 90º for each end. Then the log is rotated on the sled 90º to make a rip cut along one side of the log. Since the log is no longer held together on the freshly cut side more duct tape is added to hold that side together. The log is then rolled with the new surface facing down on the sled and another side is ripped. Duct tape is again applied to the newly sawn side.
The log is then brought over to the table saw to be squared up and sized for a bottle stopper blank. Bottle stopper blanks are roughly 2" square by 2 1/2" long. At the table saw rip the block down to those dimensions trying to keep the center of the log centered for what will give in my impression the best looking stopper. After each rip cut keep add more tape to keep the blank solid and keep loose pieces from turning into projectiles. Finally cross cut the blank to approximately 2 1/2".
Step 4: Casting Blank in Alumilite
Alumilite comes in two primary flavors, white which is opaque and clear which is transparent. Alumilite clear is the two part casting resin used with this project. The clear will allow some of the light to filter through the core of the stopper once it is turned. It is best to read through the Alumilite documentation prior to attempting to use Alumilite and watch a number of their videos to get a good understanding of how to use their product.
Setup
Casting with Alumilite requires a certain amount of setup since the open time is somewhat limited. Alumilite clear has an open time of approximately 7 minutes with a slow set variety (which was used in this case) with an open time of approximately 13 minutes. Make sure everything is close and available so you do not need to rush through the process and potentially make mistakes.
- Pressurize the air compressor so the tank does not need to recharge once the casting is in the pressure pot.
- Prepare some sort of weight to hold the wood of the blank in the mold while pressurized.
- Set out the Alumilite parts A and B.
- Set out the mixing cup with stir stick.
- Set out the dyes which will be used, make sure the tops are cut open and ready to use.
- Prepare the mold with Stoner, which is a mold release agent that can be sprayed into the mold.
- Remove the blank parts from the duct tape taking care to keep them ordered or together.
Preparing and Pouring the Alumilite
Alumilite is a two part resin with equal parts by weight. The clear resin will show streaks through the mixture until it is completely mixed.
- Zero your scale with the container you will mix the Alumilite.
- Add part A of the Alumilite visually approximating 1/2 the volume you will need in the casting, if you have to error go on the extra side. Record the weight to the 1/10g to 1/100g.
- Add as close as possible (at least to the 1/10g for small castings) of the part B of the Alumilite. Watch the scale, not the volume.
- Using the stir stick mix the Alumilite. Scrape the sides and bottom of the container to ensure a complete mixing of the resin. Trails or streaks will be visible until the mixture is completely mix. Alumilite clear will be completely transparent except for air bubbles when it is completely mixed. There is not a timeframe for mixing, but visual inspection.
- Once the Alumilite is completely mixed you can add the dyes. A single drop of red and yellow was added to a total of about 80g of alumilite to give an indication of the dye's potency. Mix the dyes into the mixture.
- Pour approximately half of the resin into the mold.
- Press the parts of the blank into the mold. The parts will give a little resistance as the Alumilite squeezes around the parts of the blank.
- Pour the remaining Alumilite over the blank in the mold. Work the mixture around the pieces of the blank with the stirring stick.
- Transfer the mold with the blank into the pressure pot.
- Add the weight you will be using to hold the blank down in the mold.
- Secure the top of the pressure pot onto the tank.
- Add pressure to the pressure pot keeping away from the limit of the pot. Alumilite recommends using at least 40psi to crush the air bubbles for a bubble free appearance of the final result.
- Keep the project under pressure for at least 2 hours at 70ºF temperatures, Alumilites recommended de-mold time. At cooler temperatures I recommend allowing longer cure times.
- Remove the blank from the pressure pot and de-mold the blank.
- Allow blank to fully cure, following Alumilite's recommended time frame of 5-7 days at 70ºF temperatures.
Step 5: Turning Bottle Stopper From Blank
Bottle stopper hardware is simple screw threads.
Drill and Tap
The blank is clamped with a hand screw clamp to keep it square. Then the drill press is used to bore a hole slightly smaller than the threads into the bottom side of the blank. Then a tap with the same threads as the bottle stopper hardware is chucked into the drill press. This well help the threads to be cut squarely in the hole to avoid any misalignment when tapping by hand.
Turn Stopper
The blank is then threaded onto the a bolt held in the chuck. The first step in turning the stopper is to knock off the corners and turn it round. Using the side edge of the carbide tool the face towards the threaded end is cut straight so it will meet the hardware without a gap. At that point the color and shape reminded me of the Planet Char from StarCraft so I decided to turn a globe shape for the stopper.
The Alumilite seems to have a tendency to chip a bit with the carbide tools so I switched to the high speed steel tools. This seems to get a more consistent and smoother cut between the different consistency of the wood and Alumilite.
Sanding and Finishing
To avoid the larger scratches in the Alumilite portions of the stopper I started with 220 grit sand paper. Then with the lathe on the slowest setting I sanded radially with the lathe running. Then stopping the lathe I switched to hand sanding along the grain on the wood sections. This pattern as used from 220 grit to 600 grit.
After 600 grit paper the stopper was wiped with mineral spirits. Then using mineral spirits as a lubricant the micro mesh pads from 1500 grit to 12000 grit were used to sand with the lathe on. The mineral spirits were allowed to evaporate for a couple hours.
A friction finish was used to coat and protect the stopper. Six coats of the friction finish were applied.
Finally the stopper was removed from the threads of the bolt and the stopper hardware was threaded onto the stopper to complete it.
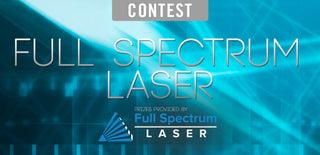
Participated in the
Full Spectrum Laser Contest 2016