Introduction: 2x4 Settlers of Catan
Settlers of Catan is a board game which was quite popular while I was in college. While this build is specific to Settlers, it could be adapted to pretty much any board game. I go through the process to create cards, meeples, tiles, 3 dimensional components, simple six sided dice, and dying and image transfer onto the components. The majority of various board game components are covered in the creation of this game, but it is possible that other types of components could also be created with a little creativity. Adding images and dyeing components is covered in the last step.
The included video shows the process used for this particular game, Settlers of Catan.
Step 1: Select and Prepare 2x4
Since the entire game is created from a single 2x4 and it is composed of mostly small items it is necessary to select sections which are free of knots. Most off the shelf 2x4s from home centers are full of knots, but there are enough clear sections to get sufficient material for the game.
- Mark off the knot sections of the 2x4
- Use a miter saw to cut out the knot sections from the board
- Select clear sections to most efficiently create components of the game
Step 2: Create Cards
Create Shavings
Setup a hand plane to take about .005" shavings. Place the 2x4 section onto work surface with the narrow side up with a stop block. Carefully plane consistent shavings from the 2x4 on end. The first few shavings will be narrower to account for the round over typically put on home center 2x4s which can be discarded. Once the shavings are the full width of the board collect them up into a bucket or similar container. The shavings will have about a 1" to 2" curl into a loop.
Prepare Shavings
The shavings are of no use all curled up tightly, so they need to be prepared. Dry as they are the wood fibers will break if you attempt to uncurl the shaving. Dip the curled shaving in some warm water for a 5 - 10 seconds to soften the wood fibers. This will allow you to uncurl the shaving without breaking the fibers. Then, using an iron you do not plan on using on clothing again, iron the shavings until they are flat and dry. This should take less than half a minute per shaving.
Create Card Sheets
Armed with hundreds of flat 2x4 shavings it is time to create the sheets of "paper" which will be used for the game cards (in Settlers of Catan this is the resource cards and action cards). You will need a couple heavy flat surfaces which will work as a press, I use two sheets of 5/8" glass which measure about 16" square. A couple sheets of plywood or melamine covered particle board with a weight should also work effectively.
Cover the bottom panel of the press with wax paper. Fill the bottom of a disposable bowl with contact cement. Apply the contact cement to a single side of one of the shavings with a spatula. Lay that piece contact cemented side up. Apply contact cement to another shaving and lay it next to the original piece, also sticky side up. Apply contact cement to another shaving and place this one sticky side down on the overlapping both of the previous shavings. Work this pattern until you have a sheet of shavings which will still fit in the press. Add a sheet of wax paper above the sheet of shavings and then put the top part of the press on the sheet. While probably not necessary, I gave the sheets about a day to fully cure under the weight of the press. Remove the sheet from the press and carefully peel back the wax paper to avoid damaging the shaving sheet.
At this point you will need to calculate the size of the cards you will want to use based on your first sheet made from the shavings. Determine how many cards you will be able to fit per sheet and plan on making about 10% extra to determine how many sheets you will need to make. The 10% extra accounts for cards which are on seams which break because they are too brittle or chipped out corners when cutting. I was able to get about 20 cards per sheet and needed 120 cards. So I did 7 sheets which gave me about a total of 140 cards.
Preparing Sheets
A sanded surface will take the ink transfer better than the rough surface that come right out of the press. Once you have sufficient sheets of material for the cards use a palm sander to smooth out the sheets. Do not use a sand paper grit that is too aggressive. I used 220 grit, 180 should be acceptable, but anything less would probably be too aggressive. Note that the edges are brittle and will likely chip apart while sanding.
While it could be accomplished with a number of cutting mechanisms, I would suggest using a roller style paper cutter. This should allow you to get a good straight edge and same size for each card. First cut across the grain of the sheet to get the height of the cards. Flex the row of cards to look for weak seams which should be avoided. Finally cut along the grain of the sheet to get the width of the cards, avoiding weak seams. And of course get a card count total to make sure you will have sufficient numbers. It is also a good idea to keep some of the rejects to do your initial ink transfer testing later on when printing on the cards.
Step 3: Create Meeple
About a 10" section of a clear section of the 2x4 was ripped down square and put between centers on the lathe to round it out with a roughing gouge. Once round, the work piece was mounted into the 3 jaw chuck. A spindle gouge was used to shape the meeple. And finally it was parted with a hand saw.
Step 4: Create Tiles
Creating Tile Stock
Select enough sections of the 2x4 stock which can fit 3 hexagon tiles and another piece which can fit the ocean tiles. The fence on the bandsaw is set to 1/8". The 2x4 is then ripped into as many 1/8" slats as you can get from the original material.
Land Tiles
Gang the slats back together with painters tape and use spray adhesive to attach the tile cutting templates. While cutting the ganged together tiles, make sure to replace tape on unsupported sides (where you just cut) to keep the stack square and together. Prepare each of the three stacks of hexagon tiles in this fashion.
Remove the tape from one side at a time and sand the edges of the tiles. Replace the tape and switch to another side for each of the sides of the ganged together tiles. Once all of the sides are sanded remove the tape and sand both the top and the bottom faces of each tile.
Ocean Tiles
The ocean tiles have a bit more detail which would be hard to cut out on the band saw. So gang the ocean tiles together into two stacks of three with painters tape. Apply the cutting template with spray adhesive like the hexagon tiles. Use a scroll saw to cut the ocean tiles.
Hand sanding will be required for the edges, using a block to keep the edges square. The faces of the ocean tiles can be sanded at the belt sander.
Step 5: Create Components
Roads
While the bandsaw fence is still set at 1/8" a slat is cut from another clear section of the 2x4, length is not important, but it would be good to be able to get about 4-6 lengths of road. Then the slat itself is tilted 90º onto the bandsaw table and small narrow sticks are ripped from the slat. Keep the fingers away from the blade since these are very tiny pieces. Take the sticks and hand sand them to remove roughness and fuzziness from the cuts. Finally, the road sections can be cut to length in a miter box with a stop block.
Roll Tokens
The roll tokens are the round tokens in Settlers of Catan which are placed on each of the land tiles which indicate who receives resources when the number is rolled. The remains of the dowel which was turned on the lathe for the meeple can be used to create these tokens. Round items on a bandsaw need to be held to prevent rolling away from the operator. While the bandsaw fence is still set to 1/8", clamp the dowel into a wood hand screw clamp. Then cut the end off of the dowel against the fence, keeping the fingers away from the blade. Collect up the tokens and sand the edges and surfaces of the tokens smooth.
Building Tokens
Adjust the bandsaw fence to 3/8" and rip a couple pieces off another clear section of the 2x4. Apply a cutting template with spray adhesive to the 3/8" slats. At the scroll saw I found cutting each row apart first, before trying to do the detail on each of the larger buildings made cutting a bit easier. Then cutting the detail of each building worked once there was a straight edge to work from while cutting the roof of the larger buildings. Then the small buildings were cut into rows also, and then each building was cut free. All of the building components were then sanded at the belt sander. And the small buildings had a roof sanded onto the tops of them.
Step 6: Create Dice
Settlers of Catan uses two six sided dice for the game. The off cut from the meeple was sufficiently large for the purpose.
Create the Cubes
The table saw fence was set at 3/4", though any size would be sufficient. Then the meeple off cut was ripped to about 3/4". Push sticks were used to keep the fingers away from the saw blade in the cut. Without adjusting the fence the result was flipped sideways and ripped again. Again, use push sticks to keep the fingers away from the saw blade. Next, clamp a spacer block to the fence behind the blade. Adjust the fence and spacer block to the thickness of the square sides of the die. Using the miter gauge with a sacrificial backer to support the back of the cut (for tear out) and the die on after the cut to the right of the blade to prevent it from kicking back, cut the cube from the stock piece.
Sanding
At the belt sander sand each of the faces. Try to keep each side of the die on the sand paper the same about of time. Additionally, for very precise dice you can test thicknesses with calipers to your desired level of precision. though keep in mind humidity levels will always change the shape of the dice. Chamfer the edges of the dice at the sander also to get a smoother rolling.
Adding Pips
With pencil mark the layout of the die. Six sided dice have opposite faces add up to seven. So six and one go on opposite faces, five and two, and four and three. Take a framing nail and blunt the end, either with a hammer or file. Heat the tip of the nail, it does not need to be glowing red hot, just enough to burn the pip. Testing on a scrap piece of the same wood before the actual die would give a good indication how long it takes to burn in a pip. Once the pips are burned into the die it is complete.
Step 7: Adding Images With Laser Toner Transfer and Color
Transfer Images to Tiles and Cards
If you have a laser printer, you can use the technique I am using, otherwise if you have an ink jet printer you can use one of the other possible techniques to transfer images. I am using the laser toner transfer mechanism which uses lacquer thinner.
I started by using google image search to find images which represented the various hexagonal tiles landscapes and images which represented the resource cards and various action cards. I decided to skip putting text on the cards being familiar enough with the game I didn't need the rules. If I did want the rules for the cards printed I would have to reverse the text so it transfers correctly. One thing to remember about this transfer mechanism is that whites do not come across (it uses the white of the page being printed), so finding wool I had to print a woman at a spinning wheel. Armed with all of the images I printed up enough sheets of for all the tiles and cards. And then printed all of the number tokens in reverse so they transferred correctly.
The image being transferred is cut from the page of other tile images. Then the printed side is laid on the tile the image it to be transferred. Hold the image in place while a paper towel is dampened in lacquer thinner and dabbed onto the image. The paper will become translucent and the image will show through. Carefully lift the paper from the tile and the image should be transferred. While it is possible to reuse the paper, the image will transfer lighter than the original, so it is best to use a new image each time. Allow the tile to dry (should not take long) and apply a coat of water based polyurethane to protect the images.
Use the same process for the numbered tokens and the cards. When transferring onto the cards avoid using too much lacquer thinner since it will soften the contact cement used in the cards. Also add a couple coats to the cards fronts and backs to make them more rigid and less likely to chip.
Dyeing Components
Each of the sets of buildings and roads need to be colored for each player. Using a small dixie cup I added about a 1/4 cup of water. Then about 25 drops of food coloring were added to the cup. The roads and buildings were added to the cup and shaken up until each of the components was dyed. A couple more drops of coloring were added if the color was not as stark as desired. The pieces were then removed from the cup and laid out on paper towel to dry. After the components are dry a couple coats of the same water based polyurethane can be put on the components.
When moving between colors, make sure to use a separate cup, and dry the gloves off completely so you do not transfer colors between the different components.
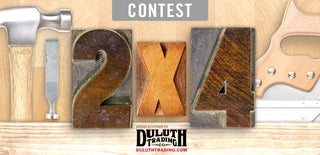
Participated in the
2x4 Contest