Introduction: Spot Weld Plastic
I'm a big fan of the plastic milk jugs. They're a strong, flexible, accessible, free material. There's hardly a jug that makes it to my recycle bin, without a gaping hole of some sort, in the side.
The only problem I had was the HDPE (high density polyethylene) plastic is, it's almost impossible to glue. Glue just won't stick.
I decided I wanted to develop a method to weld this plastic and make it even more versatile.
In his instructable, I'll show my process, successes and failures and I hope you'll find some tips for your own creativity.
Step 1: The Jug
I'd suggest starting off with milk jugs. The thinner plastic will be easier to weld. With more practice you can weld thicker plastic.
Step 2: Tools and Materials
1- Photo 1 shows a Bbq mat. These teflon fiberglass reinforced mats are used on barbecues, to keep your food from falling through the grill. They will withstand very high temps. 550F 288C. This is what you will use to protect the plastic from burning, but also allow the heat to transfer through and melt the weld. It stops the iron from burning the plastic, which is a real problem with other plastic welding methods. There's no toxic smoke with my method, but just to be safe, do this in a well ventilated area.
2- Cut 2 strips, from your mat. 4cm x 12cm.
3- This is an aluminum espresso tamper. Any smooth flat piece of metal should work.
4- This soldering iron is as cheap and crappy as they come. It's only 30 watts. I would recommend low wattage. Higher wattage, more heat, and more likely to melt through.
The tip has been removed, but you want an end that looks like the picture. Others I've seen, do not have the flat washer shaped surface, that helps make the weld. They are more like a tube, and would not have the surface area, to press the weld. Although, if you found the right size bolt to fit into the hole for the tip and flattened the head, it would probably work.
5- A piece of rubber to give a bit of cushion and heat protection.
Step 3: Do It!
1- Cut up some small pieces of plastic to experiment with. Heat up your soldering iron. Have your tamper close to your work.
2- You will be making a sandwich of the 2 pieces to be welded, between the 2 strips of the bbq mat. This will sit on top of the rubber block.
3- Once you have it lined up with your iron perpendicular to your work, lower it to the spot to be welded. Use a medium amount of pressure. Too much pressure and it will burn through, and squeeze the melted plastic up and out, too little, it won't stick. 1 or 2 pounds.
If you look on my cover photo, you'll see on the bottom 2 spots right side, there are tiny voids. This is the plastic starting to bubble/boil. You don't want too much of this or it will eventually break through the layers and weaken the final weld. Walk the fine line between time, temperature, and pressure.
My ideal time is 9 seconds. It will vary for everyone, so experiment to get the correct time for you. I find it useful to have a clock ticking in the background, so I'm accurate each time.
4- After 9 or so seconds, remove the iron and apply your tamper and press for a few seconds.
5- Now you have a hot little plastic sandwich, stuck together. Don't pull off the mats till it cools. It will only take a minute or so, but if you peel it off too soon, it will stick, and ruin your surface texture. If you are using different coloured plastics, be sure to use a fresh area of your teflon, the colour can transfer to lighter coloured plastic.
Step 4: Voila!
A beautiful strong weld.
The second and seventh picture, are the back views of their preceding pictures.
You will soon get the knack of knowing if it's a successful weld or not. Mostly by ripping them apart.
If you are successful, you won't be able to pull them apart. It's all about timing of your heat, so be accurate in your timing, so you can reproduce your success.
The nice thing about this method is, there is a small amount of fold over on the weld as a result of pressing, after the heat and it acts like a grommet and strengthens it at the weakest point of the weld.
This method would also work well as a reinforced hole, like a grommet.
The final picture shows a nice distribution of plastic within the weld.
Step 5: And Now for My Failures.
It doesn't take long to master the weld.
The first picture shows the timing from 8 to 20 seconds.
The last 3 photos are without the teflon mat. Lots of smoke and melted through very quickly.
I tried other heat shields, including silicone, which sort of worked, but not as neat, and there was colour transfer.
Step 6: Different Materials
I tried welding this thicker plastic. I'm not sure what type it is, but it's not HDPE. After a bit of experimenting, I had success. I found with the thicker plastic, you don't put pressure on the iron and let the heat slowly penetrate through the thickness. I found 2 minutes made a strong weld. I was able to rip, but with a lot of effort and even then, it ripped into the surrounding plastic. If it was HDPE, it definitely would not have ripped. The 5th picture shows 20 60 120 seconds. The 120 seconds had no pressure, and worked well.
Looking at the back of the weld is a pretty good indicator to a good weld. You want it to have melted through to the back.
KLARCK, posted below, and wondered about welding, coraplast corrugated polyethylene. I gave it a try, and it worked beautifully. You have to push down quite hard, and the teflon gets forced into the hole, but a very nice result.
(See pictures)
Thanks for asking.
I tried welding 2 layers of a 55 gallon barrel, total of 1 cm thickness. The photo shows 2 welds. Top weld, the iron was left for 5 minutes, the bottom weld, was 10 minutes. Only slight discolouration after 10 minutes. It did melt through to the second layer, but not enough to make a weld. I think a higher wattage iron, might work. (stay tuned)
Step 7: Thicker Plastic Experiments
A lot of people have been asking about welding thicker plastic. I have one of those 55 gal HDPE barrels, I've cut up and been using, over the years. It ranges in thickness, depending where on the barrel.
I tried the above method on 2 layers, total 1cm thick. I couldn't seem the get the melt much deeper than the first layer.
I thought maybe if I could get a probe down through the full thickness, and melt the full depth, it might work.
I made this tip, out of aluminum pipe. I thought the metal mass, and the good heat transfer of the aluminum, might work.
With the flat blade shape, I could take a small narrow piece of teflon mat, down the hole and just let it sit and melt, without rumpling the teflon, and weakening its structure.
It worked very well. I was able to get through to the back, with a good amount of pressure and get a good melt, in about 2 minutes.
I pulled out the teflon before cooling, and pressed with the tamper, and the hole closed in nicely, with the molten plastic.
I could, in no way pull this apart. Put a few of these in line and you would have a very strong patch. It might take some care, to get it water tight, but I think it could be done.
Step 8: Now, Go Make Something!
I hope you find many uses for this method of welding plastic, and I look forward to hearing all about them.
Step 9: B Movie
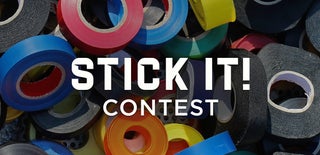
Runner Up in the
Stick It! Contest