Introduction: The Modular Breadboard Kit (version 2)
This is a "Modular Breadboard Kit", which is designed to fit in a Stanley 014725R organizer case. You can actually fit two of them in there (a left and a right version). The idea behind this was to be able to store and transport a work in progress electronics project inside a nice dust free case that I could also keep a few other things in. The small modules are for things that are useful like potentiometers, switches, and also some things I don't really need but are cool, like the 2-wire LCD volt meters (which I had not used before this). There may be some more modules in the future too.
There are currently 2 larger modules which either contain a DC-DC buck converter and a DSO112A mini Digital Storage Oscilloscope, or a12864 Mega328 LCR Transistor Resistor Diode Capacitor Mosfet Tester. There is another Instructable for the (blue) 12864 Mega328 LCR module here (I had to post it separately due to the different license, as I remixed part of the blue LCR module). The large (red) module included in this Instructable holds the DSO112A which is a mini oscilloscope, which I honestly have not used much, but wanted a place for it. The DSO module also has a small compartment for storing a the leads. Additionally there is a "comb" to help keep any unused wires organized or out of the way.
I am entering this Instructable in the organization contest, so if you like it, please vote for it, thanks!
Before going on though, I would like to thankLaura Taalman aka Mathgirl (at Thingiverse.com) for letting me use her print in place hinge design on the DSO module door, you can check it out here:
https://www.thingiverse.com/thing:436737
MathGirl's Hinge Design (which the DSO112A module uses) is licensed under the Creative Commons - Attribution - Non-Commercial - Share Alike license. If you remix the DSO112A module or use the hinge design, please include the same attribution to Laura Taalman for the hinge.
I'd also like to note that I am not an electronics expert, just a hobbyist that is trying to get stuff organized. The steps and diagrams here show how I assembled the kit which I use, and there may be a better way so as always please use your own judgement. Please let me know if you see something that can be improved. As for the electronics, after the initial design I decided to add some fuses to protect the inputs for the DC-DC converters which I have included in the diagrams. I did not add any reverse protection or anything like that for any of the components, but please consider that if you see the need for it.
If making this, please understand the limits of the components being used, and make your own judgements on where, if, and how you feel additional protection such as fuses, PTC's or diodes are needed to make your project safe for how it will be used. If you see a problem let me know, thanks!
Step 1: Bill of Materials
(the links provided are either what I purchased or for reference, you can probably find these in smaller quantities or cheaper if you check the usual places)
Parts for the Small Modules and Base
- LCD voltmeters If you get the 10x22.5mm versions (linked), then use the "SM" or small modules. If you happen to buy the larger type, then use the LCD parts that have "LG" in the name. I used the small type voltmeter modules which are linked. Two per voltmeter module are needed.
- STANLEY 014725R organizer case (Optional, but the kits are designed to fit 2 per case. Zoro.com is the cheapest place to get these - or Ebay)
Mini 25 Point Solderless Breadboard (2 per potentiometer module)
170 Tie-points Mini Solderless Breadboard - Don't get the type with the holes and the square lugs on the sided (one per kit)
830 Point Solderless Breadboard (2 boards per kit)
- 1 pin Dupont connectors (female) and shells will also be needed (four per module, for the voltmeters and switch modules). Some pre-made jumpers with the dupont female connectors on the ends similar to these could also be used (by cutting one end off, or cutting them in half).
- "Rotary Potentiometer Panel Pot Linear Taper 500 - 500K Ohm " with caps (available on Ebay). See the pics for an example of the type used. The pots I purchased for this project have a 15mm shaft length (8-9mm knurled part), 6mm shaft diameter and are 24mm overall. (see the 4th pic)
- Momentary switch (these are only needed for the modules with switches)
- Toggle switch AC 250V 3A/125V 6A (Only needed for the small module with the toggle switch and momentary switch) The link shows two types, I used the smaller switches for the modules with the toggle switch.
DSO112A module
DSO112A oscilloscope (Ebay or Amazon) (qty 1)
- DC DC Buck converter Mine have an 5-23V input, and the seller stated they have a 3A max - but under 2A is recommended (much cheaper on Ebay) (qty 1)
- Rocker Switch (qty 1) - rated for 6A 250V;10A 125V,10A 12V. I used switches similar to these, and the larger switches in the assortment linked above also work (but are a bit loose). There seem to be many of these toggles however so just make sure they fit the cutout which is 19mm x 12.8mm. The switches I am using have a dimension of 17mm x 12.8mm (measuring the body of the switch and not the larger face dimension, and not including the side clips).
- DC 2.1x5mm panel connectors, these can be found cheaper on Ebay (qty 2)
- Fuse to protect the DC-DC converter, I used a 2.5A fuse since that is what I have on hand (and my power supply only does 2A anyway). I recommend using a fuse to protect the electronics.
Hardware:
Potentiometer module
- M3x8 (qty 2)
- M3x12 (qty 1)
M3 4mm x 4.3mm brass inserts (qty 3)
Voltmeter module
- M3x8 (qty 2)
- M3x16 (qty 1)
M3 4mm x 4.3mm brass inserts (qty 3)
Switch modules (both types)
- M3x8 (qty 2)
- M3x16 (qty 1)
M3 4mm x 4.3mm brass inserts (qty 3)
DSO112A module
- M3x8 (qty 12)
M3x16 (qty 4) - M3x30 (qty 2)
- M3 nuts (regular, not locknuts) (qty 2)
M3 4mm x 4.3mm brass inserts (qty 10, get some extras though)
- 1 spring from a retractable ball point pen, I used one like this.
Tools and odds and ends:
- wire (I used mostly 22 gauge silicone insulated wire which doesn't tend to melt as easily when soldering)
- soldering iron, solder, etc
- glue (I used clear Gorilla Glue but any glue that can be used with plastic would work)
- Double sided tape like 3M 4011 can be used if you decide to stick the "dots" to the base of the smaller modules.
- screwdriver and bits for the M3 and M2.5 screws
- heat shrink, electrical tape or liquid electrical tape
- several thin zip ties (only used on the larger modules for cable management). These need to be the thin kind since the opening in the cable management clips is only about 4mm wide.
Step 2: Printing
Most of STL files can all be printed at 0.2mm layer height and you can use the default 20% infill.
The only parts that should be printed in0.1mm layer heights, since they are small and will look better at higher resolution, are:
MBBKV2-D10-mod-dupont
MBBKV2-D10-button
I printed mine in PLA but there is no reason ABS or other plastics would not work. Because the parts have small clearances (usually 0.25-0.3mm) it is important to have the extruder steps per mm and flow (in Cura) calibrated for the type of filament being used.
I suggest printing one of the smaller modules first to make sure it has the correct dimensions before going and printing the lot of them. If you have a caliper or metric ruler, you can confirm that the dimensions of the smaller module is 43mm x 42.7mm (see the 3rd pic, which shows the shorter dimension on the side that connects to the breadboard base).
See the txt file called "Breadboard_Kit_V2_D10_Print_list" for a list of which parts below are needed for each module. The "sides" in the file names for the STL's refer to the side of the Stanley case the module was designed to fit (see the 1st pic). Only the left or right side parts for the DSO module is needed, not both. Similarly, the "end-mod" (which holds the smaller breadboard) and the base also have a left or right version. The small modules are interchangeable between left and right sides, as are the buttons, latch parts, and Dupont holders.
The following parts have areas that need special attention since there are small pockets where supports could be a pain to deal with. They are:
MBBKV2-D10-DSO-RIGHT-TOP -and- MBBKV2-D11A-DSO112A-LEFT-TOP
(4th pic) I printed these so the top was flat to the build plate (rotated 180 degrees). There is a pocket where the door latch will catch, and another small enclosed pocket on the cable management tab, supports in these areas should be checked in the slicer before printing to make sure they will be removable. Using tree supports will avoid most problems. If you use Cura, the support blocker feature can also be used to insure there are no supports in an area.
All the parts should be rotated and oriented for minimal supports. I found that the tree supports in Cura worked out well. If you use tree supports, I suggest that you also "enable support brim" and use at minimum a skirt with several lines, that will help with the adhesion of the tree supports to the build plate.
STEP file is included if you want to make your own modules.
I do not have S3D or other slicers, so if you have a problem, try slicing in Cura (which is free :D).
UPDATE - FEB/28/2019 9:19PM GMT - I found a problem with a label on the following part, which I have updated to correct:
MBBKV2-D10-DSO-LEFT-TOP
The corrected part is called:
MBBKV2-D11A-DSO112A-LEFT-TOP
The STP file has also been updated with the correction.
Attachments
MBBKV2-D10-DSO-LEFT-HANDLE.stl
MBBKV2-D11A-DSO112A-LEFT-TOP.stl
MBBKV2-D10-DSO-LEFT-BASE.stl
MBBKV2-D10-DSO-DOOR-LATCH-B.stl
MBBKV2-D10-DSO-DOOR-LATCH-A.stl
MBBKV2-D10-DSO-RIGHT-HANDLE.stl
MBBKV2-D10-DSO-RIGHT-TOP.stl
MBBKV2-D10-DSO-RIGHT-BASE.stl
MBBKV2-D10-button.stl
MBBKV2-D10-mod-mom-toggle-switch-TOP.stl
MBBKV2-D10-mod-mom-toggle-switch-BASE.stl
MBBKV2-D10-mod-2xmom-switch-TOP.stl
MBBKV2-D10-mod-2xmom-switch-BASE.stl
MBBKV2-D10-base-plain-RIGHT.stl
MBBKV2-D10-base-plain-LEFT.stl
MBBKV2-D10-base-Stanley-LEFT.stl
MBBKV2-D10-base-Stanley-RIGHT.stl
MBBKV2-D10-end-mod-LEFT.stl
MBBKV2-D10-end-mod-RIGHT.stl
MBBKV2-D10-mod-dupont.stl
MBBKV2-D10-mod-LG-LCD-TOP.stl
MBBKV2-D10-mod-LG-LCD-BASE.stl
MBBKV2-D10-mod-SM-LCD-TOP.stl
MBBKV2-D10-mod-SM-LCD-BASE.stl
MBBKV2-D10-mod-pot-TOP.stl
MBBKV2-D10-mod-pot-BASE.stl
MBBKV2-D10-comb.stl
MBBKV2-D10-comb-B.stl
MBBKV2-D10-comb-A.stl
MBBKV2-D10-dots-quarter.stl
MBBKV2-D10-dots-half.stl
MBBKV2-D10-dots-full.stl
Breadboard_Kit_V2_D10_Print_list.txt
MBBKV2-D11A-DSO112A-ALL.stp
Step 3: Putting It All Together
I'm gonna break this part down into several parts, with instructions for the modules first, and then how to assemble the whole thing. Before assembling, please clean up the prints and remove the "elephant foot" (blow out of melted filament which is typical on the edges of the first layer of a print), since the fit is tight on these parts. A deburring tool works great for this.
There are quite a few M3 inserts used in this project, and they should be heat set, but I glued them in on my kits. I decided to glue them in using clear Gorilla Glue since I have no experience with heat setting them, and I feel that with glue they wont get set in askew. I had to be careful to let the glue cure/set fully before putting the screws in and didn't over tighten the screws since the glue will be weaker than melting them in place. I found it helpful to use a 20mm or so M3 screw as a tool to help install the inserts (see the 2nd pic which is from another project but shows how I install them with glue). Inserts should be flush or sit below the surface of the part, none should stick out from the parts.
There are quite a few words in these steps since I wanted to cover the details as best I can. Some modules can probably be assembled just by looking at the pics however, others not so much. In any case, please insulate all the connections with heat shrink, electrical tape or liquid electrical tape, and tidy the wires up as much as possible so they are not pinched when closing the cases.
Good luck, so here we go...
Step 4: Potentiometer Module
Parts:
- 2 potentiometers with knobs, and their washers and nut, with a 15mm shaft (knurled part is approx 8-9mm)
- 2 Mini 25 Point Solderless Breadboards
- M3x8mm screws (2)
- M3x12mm screw (1)
- M3 4mm x 4.3mm brass inserts (3)
- the following printed parts:
MBBKV2-D10-mod-pot-BASE
MBBKV2-D10-mod-pot-TOP
Assembly:
- Poke the 3 leads/prongs from the potentiometer into one of the short ends of the 25pin breadboard and then rotate the potentiometer 90 degrees so it looks like assembly in the 2nd pic.Gotta do this for the other one too.
- Push the potentiometer and breadboard assembly into the top of the module and secure the nut (3rd pic). If it is tight, please clean the "foot" from the parts (the fit is snug, but not impossibly tight).
- To assemble the module, install the M3 inserts as shown in the 1st pic, for every screw, there will be an insert.
- Follow the 1st pic to install the screws, you can wait to install the M3x8mm screws until later when doing the final assembly. The two pegs in the bottoms of the mini breadboards will seat into the holes in the base of the module, if they do not, clean up the parts with a deburring tool to remove the "foot" from printing.
Step 5: LCD Voltmeter Module
Parts:
- Mini 2 wire LCD volt meters (2)
- one pin female Dupont connectors (4)
- M3x8mm screws (2)
- M3x16mm screw (1)
- M3 4mm x 4.3mm brass inserts (3)
- the following printed parts:
MBBKV2-D10-mod-SM-LCD-BASE -or- MBBKV2-D10-mod-LG-LCD-BASE
MBBKV2-D10-mod-SM-LCD-TOP -or- MBBKV2-D10-mod-LG-LCD-TOP
MBBKV2-D10-mod-dupont (4 of these)
Note: Most of these small volt meters have a pot on the back that can be used to fine tune them if they are not reading correctly. I only had to adjust mine slightly so it hopefully is not a big deal, but may be worth checking before assembly.
Assembly:
- First install the Dupont connectors on the 2 wires attached to the LCD Voltmeters. You should leave about 1.5" to 2" of tail on these (see the 1st pic and the 2nd pic of the partly assembled LCD module). You need enough to work with, but these will eventually need to be tucked into the housing so keep em as short as possible. You may want to add some glue to where the wires attach to the boards since that is an area where they could break. Alternatively, if you do not want to deal with crimping the Dupont connectors, you can get jumpers with the female Dupont connectors, and just cut one end off and solder that wire to the LCD voltmeters in place of their existing leads.
- Glue the Dupont connectors into the "MBBKV2-D10-mod-dupont" parts (1st pic). Use just enough glue around the sides to hold the connectors, but not too much that oozes out. The front of the Dupont connector should be flush with the top of the part and should not stick out. Allow these to dry before moving on.
- Install the LCD Voltmeters in the module, and take note of their orientation (you don't want them to be upside down when you look at them). They will be a tight fit, and if you find they will not go, you may need to clean up the "foot" on the part or lightly sand the inside of the part.
- Install the Dupont connectors into the holes in the top module parts (see the 2nd pic of the partly assembled LCD module). Don't use glue on these. They will be a snug fit, but if you run into a problem it is probably easiest to lightly sand the outside of the Duponts and clean the "foot" from the openings in the "top" module part where they need to go through.
- Once the Dupont connectors are all installed, the wires from the Duponts should be arranged so they will sit in the small gaps provided for them next to where the Duponts go in, and then coil or flatten the remaining wires so the case can be closed up. Be careful not to pinch the wires when closing it up. It may help to use some hot glue to hold the wires down.
- To assemble the module, install the M3 inserts as shown in the 3rd pic, for every screw, there will be an insert.
- To close up the case, the wires will need to be arranged so they do not pinch (a lot of excess wire can be a problem here and may need to be re-worked with shorter wires). The wires that go to the Dupont connectors should be arranged so they do not pinch and are set in the corresponding grooves in the top part of the case (see the 2nd pic where one of these is highlighted). When the wires are situated out of the way, the case can be closed up using a M3x16mm screw through the top of the case, into the insert embedded in the base. The M3x8mm screws can wait until later, when doing the final assembly.
Step 6: Momentary Button and Switch Modules
Parts:
- momentary switch and cap (qty 1 or 2 depending on the module)
- small toggle/rocker switch AC 250V 3A/125V 6A (qty 1 - or none depending on the module)
- one pin female Dupont connectors (4)
- M3x8mm screws (2)
M2x16mm screw (1)
M3 4mm x 4.3mm brass inserts (3)
the following printed parts:
MBBKV2-D10-mod-2xmom-switch-BASE -or- MBBKV2-D10-mod-mom-toggle-switch-BASE
MBBKV2-D10-mod-2xmom-switch-TOP -or- MBBKV2-D10-mod-mom-toggle-switch-TOP
MBBKV2-D10-mod-dupont (4 of these)
Assembly:
- To assemble the module, install the M3 inserts as shown in the 1st pic, for every screw, there will be an insert.
- Install the Dupont connectors on the 2 wires attached to the momentary switches and/or toggle/rocker switches. You should leave about 1.25" to 1.5" of tail on these (see 2nd and 3rd pics). You need enough to work with, but these will eventually need to be tucked into the housing so keep em as short as possible. You may want to add some glue to where the wires attach to the switches since that is an area where they could break. Alternatively, if you do not want to deal with crimping the Dupont connectors, you can get jumpers with the female Dupont connectors, and just cut one end off and solder that wire to the switches.
- Solder wires with the Dupont connectors to the momentary switches and/or toggle/rocker switches, and insulate the connections with heat shrink, electrical tape or liquid electrical tape.
- Install the Momentary switch by snapping it into the "top" part, be careful however since the tabs are fragile (see the last 4 pics).
Install the toggle/rocker switch, it should press into place and latch.
- Glue the Dupont connectors into the "MBBKV2-D10-mod-dupont" parts (2nd pic). Use just enough glue around the sides to hold the connectors, but not too much that oozes out. The front of the Dupont connector should be flush with the top of the part and should not stick out. Allow these to dry before moving on.
- Install the Dupont connectors into the holes in the top module parts (see the last pic for the LCD module which is similar). Don't use glue on these. They will be a snug fit, but if you run into a problem it is probably easiest to lightly sand the outside of the Duponts and clean the "foot" from the openings in the "top" module part where they need to go through.
- Once the Dupont connectors are all installed, the wires from the Duponts should be arranged so they will sit in the small gaps provided for them next to where the Duponts go in (see the 3rd pic where one of these grooves is highlighted). Then arrange or flatten the remaining wires so the case can be closed up. Make sure the wires will not get pinched in the case or by the screws. It may help to use some hot glue to hold the wires down prior to closing the case.
- Close up the case, but do not pinch the wires. Use the M3x16mm screw through the top to hold the case together. You can wait to install the M3x8mm screws until later when doing the final assembly
Step 7: DSO112A Module
DSO112A + DC-DC Buck Converter Module
Parts:
- Rocker Switch - rated for 6A 250V;10A 125V,10A 12V (qty 2)
- DC 2.1x5mm panel connectors (qty 3)
DC DC Buck converter The ones I used have a 5-23V input and the seller stated they have a 3A max - but under 2A is recommended (cheaper on Ebay) (qty 2)
- DSO112A (qty 1)
- M3x8 (qty 5)
- M3x16 (qty 2)
- M3x30 (qty 2)
- M3 nuts (regular, not locknuts) (qty 2)
- M3 4mm x 4.3mm brass inserts (qty 7, get some extras though)
Fuse to protect the DC-DC converter, I used a 2.5A since that is what I have on hand (and my power supply only does 2A anyway).
- Glue, double sided tape, velcro or M3x8mm (qty 4) screws to mount the DSO112A
- the following printed parts:
MBBKV2-D10-DSO-RIGHT-BASE -or- MBBKV2-D10-DSO-LEFT-BASE
MBBKV2-D10-DSO-RIGHT-TOP -or- MBBKV2-D10-DSO-LEFT-TOP
MBBKV2-D10-DSO-RIGHT-HANDLE -or- MBBKV2-D10-DSO-LEFT-HANDLE
MBBKV2-D10-DSO-DOOR-LATCH-A
MBBKV2-D10-DSO-DOOR-LATCH-B
- To assemble, first install the M3 inserts according to the 1st, 5th and 6th pictures. Make sure to fully seat the inserts, none should sit above the surface of the part, and the inserts for the 16mm screws should go in several mm before they bottom out. It can help to use a longer M3 screw as a tool to install them.
- Next install the switches and DC connectors, you can pre-wire some of these which may make it simpler. All the DC connectors can be secured with the backing nuts. See the 2nd and 4th pics for details.
- The 2nd pic also shows how I connected the wires. However, this is where you can let your creative energies run wild, before the electrical type does. Since I am just a simple cave man (and not an expert), I chose to add a single fuse to protect the DC-DC converter, but you can add other circuit protection if you wish (fuses, diodes, PTC's,etc). What I did was; I ran the positive from the DC input through a fuse, and then to the toggle switch to turn the DC converter on or off. The outputs are wired directly to the DC jack on the output side. I recommend insulating the connectors with heat shrink, electrical tape or liquid electrical tape on all exposed connections.
- Please insulate all the connections with heat shrink, electrical tape or liquid electrical tape.
- Next install the DC-DC converter (2nd pic), but don't forget to connect the wires and drop the buttons in their holes first. The buttons are slanted and should appear parallel with the surface when installed correctly. Use some M3x8mm screws for these and don't over tighten (these do not use inserts and just go into the plastic). Make sure the buttons work freely before moving on.
Now the wires can be tidied up a bit. Please keep the excess wires away from the bottom edge of the DC-DC converter which is a potential pinch point when the case is closed up (see the 3rd and 6th pics). A thin zip tie can be used to help tidy up and secure the excess wires (2nd pic), using the cable management guide (hopefully it is not full of supports).
- Now the DSO112A can be installed using tape, velcro, glue (hot glue) or you and use four M3x8mm screws like I did, which were installed through the bottom of the case into the holes in the bottom of the DSO112A (see the 5th pic). If you use screws, be aware that the holes will need to tap themselves since the holes in the bottom of the DSO112A case are not tapped for screws, but mine were able to self tap using the M3 screws. Using screws will damage the DSO112A case, which is why I used the shortest ones I could.
- The latch goes together using the A and B parts, a M3 insert (which should be installed and allowed to dry if glue was used), an M3x8mm screw and a spring from a cheap retractable ball point pen. See the 3rd and 4th pics. The spring is put on the small "finger" that sticks out of the lower part of the latch, and the other open end of the spring will mount on the case side (where there is also a small "finger" that sticks out of the hole for the spring). Then the top of the latch is dropped on and the screw will secure everything from the bottom.
- Verify all the wiring, and it would not hurt to test things before closing the case but take note of the maximum input voltage of the DC-DC converters, mine have a maximum 23v input (5-23V range). To be safe I used a 19V DC supply with a positive + tip.
- Install 2 M3 nuts (not locknuts) in the handle as shown in the last pic. If you have difficulty, make sure all the support material has been removed from the handles first, also, the nuts go in at an angle.
- Close the case and use the screws noted in the third pic, take care not to pinch the wires in the case, or under the DC-DC converter or switch.
- It's a good idea to re-test the components after closing the case up.
Step 8: Final Assembly
Final (finally) assembly
Gather up the 4 modules you want to use (they should be mostly assembled by now), the end module that holds the 170 point breadboard, the DSO112A module, a wire comb (either the A+B parts of the whole comb), and finally the breadboard base which will hold two 830 pin breadboards.
The assembly will use M3x8mm screws for the smaller modules and a mix of M3x8 and M3x16 screws for the larger module (to see where to use the 16mm screws, see the diagrams for the assembly of the larger module). If you already installed screws in the holes in the large (DSO112A) module where there are rectangular pockets in the base, those screws will need to be removed since they will also hold the breadboard base.
The tabs on the base will insert into the pockets in the large and small modules, if the fit is tight you may need to clean up the tabs on the base with sandpaper to remove any foot or excess material. They will be a tight fit but they should go in.
I started by installing the large DSO112A module onto the base first, next was then the end module which holds the 170 point breadboard and then the smaller modules. The order does not really matter though, the modules can go in pretty much in any order.
After all the modules are installed in the base, the comb can be installed (3rd pic). It will use M3x8mm screws which go through the comb into the small modules and the end module. The comb has a ledge that helps align and hold the smaller modules, if there is a problem getting the screws in, check that the module is seated correctly on the comb and the parts are cleaned of any excess plastic. Once all the modules are installed it should be pretty sturdy, and the breadboards can be stuck in their places using the double sided tape (see the pics).
If you use the base designed for the Stanley 014725R organizer case, you can also print the small "dots" and half dots" and tape or glue those on the other parts that have been assembled if you feel it is too unstable when removed from the case. If you use the flat bases then you will not need the dots.
Please just take note of the specs on the DC-DC converters and LCD modules being used so they don't get fried or the fuses get blown. I am using a 19V 1.8A power supply with mine which seems to work well. Also, since the DC input and DC output connectors are of the same type (the 2.1mm jacks), take note of which is which, and you may want to label them for good measure.
Good luck and if you see something that could be improved let me know. If you like this, please vote for it in the organization contest. Thanks!
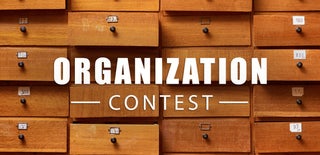
Participated in the
Organization Contest