Introduction: Tips to Great/Quick DIY PCB Etching You'll Love
Background
There are many great instructional posts about various methods of etching PCB boards. Most merely describe the process, give a couple pointers but are not very robust and you may end up like me; underwhelmed with your results wondering why you wasted 4 hours on a useless semi-copper plated piece of trash.
Goals
GREAT accurate PCB boards every time
FAST; I can make a board from artwork to drill press in about 30 minutes.
For these reasons; I'm focused on traditional photo-sensitive exposure/fix & etch method. I've tried many other techniques, here why I don't use them;
Pen/Vinyl: IT's an ok technique, but slow, hard to consistently make .024 pitch or better and I'm even a good draftsman. Finally the results look too amateur hour.
Toner Transfer: I've seen great results with this method online, but honestly, I can't reproduce them. I just get a pulpy mess that doesn't etch well. I also think it has more harder/messier steps and pre-sensitized boards are only about 20% more than copper.
Laser Printer/CNC cutting: Too much hardware to keep around. However, direct copper laser printer could persuade me if it was off-the-shelf.
So now that we know I'm talking about traditional exposure-develop-etch technique... By the way, those big professional board shops still make boards this way. It's just hard to beat.
It takes practice to get good at anything, and don't be afraid to fail.
Step 1: Make Your Boards With Great B I G Traces and Trenches.
I've made boards with .012 traces and I consistently threw 20% of them away. We DIYers can definitely make .012 pitch traces... it's not about that. Be humble; own your DIY status and internalize the practical limit of 0.024. Now all boards are good or fixable. You'd be surprise how small you can still make your boards with 0.024. Most of my boards are still postage stamp sized < 1" square.
Step 2: Single Side
If you're going to etch at home, save yourself a lot of headache and just single side. If your board is too complicated for that, you've probably left the realm of DIY and you need a daughter board or... just go bigger.
Step 3: Auto-routing Is Not Very Helpful
Auto routing is neat, in theory, unfortunately in practice I find it never produces results I like. This is because part-placement most significantly and dramatically influences a good layout. The actual routing itself is just the icing. If you route by hand you'll quickly re-arrange and find those great layouts that make it all fit together nicely and you'll make sure that the circuit behavior is maintained. Long or oddly placed leads on sensitive lines cause weird behaviors.
Do it by hand, you're DIY right?
Step 4: Design Backwards
This is a bit obvious after you've made the mistake once, but... your through-whole components go on the back side of the board. IE, you want to solder them through the whole not no the copper. So everything is typically backwards. You have two way to do this.
When you have more through-whole components than SMD; keep your components on the front side and wire everything on the back side only.
When you have more SMDs than through-whole; flip it and put all the work on the front side and put the few through-whole-components on the back side.
WORD TO THE WISE: Quadruple check which side all your components are on.
Step 5: Design Your Board With a Back Plane
Two great reasons; It provides a really solid ground plane which electronically is awesome in any application and you use less etching chemical.
Step 6: Switch to 0805 SMDs
It's faster and cheaper. There's less drilling. You can easily solder them by hand, wave or re-flow (toaster oven). For the complex components; I can easily solder anything over a 0.01 or 1mm pitch by all of the above methods. I avoid GBAs and QFN packages; anything you can't see, you can't easily and correctly align by hand. Few chips are exclusively this package.
With the right technique SMDs are not hard. You have to remember a couple things.... solder is very sticky, use the right equipement. The tricks;
- Use a good soldering iron station and a medium fine chisel tip, they aren't expensive anymore. I use 350C for SMDs (on the cooler side)
- Keep the tip very clean all the time
- Pick the smallest trace first; not the ground plane if you can help it. Small traces are easier to control.
- Make a small ball of solder on the smaller trace's pad.
- Place the part.
- Heat the wire behind the part and allow the solder to re-flow under the part. Remember that solder flows TOWARDS a heat source, this is actually a back-flow, but it does work if you're careful.
- Do all remaining legs by heating the top of the leg or the trace and flowing the solder under it. They are always MUCH easier than the first leg.
I wanted to get pictures of this, but my phone couldn't get it, I will need a macro lens for my SLR. Stay tuned!
Even More tips:
For the denser boards, I mix SMDs and a few through-whole components. You can slip the SMDs under and between the pins of larger through-whole and make some very tight designs.
For 0805 RCL's design your board with SMD pads that are wide apart, It really helps routing if you can get traces under the part. It may require a small section of 0.012 trace, no rule is absolute.
Step 7: Scrutinize Your Design
Analyse it, print it... Just check everything logically in your head 10x... Use a checklist:
- Check all components
- Are they the ones I have in my hand
- Are all the legs the right way
- Any missing filter caps (typically on vregs)
- All the line resistors on the (typically on MC IO pins)
- Proximity to high voltage
- Stray wires
- Good ground plane, all the way around the board.
- How can I extend the board to do more things?
Primary reason for throwing out boards is design change.
Second is a design/circuit flaw I can't fix; missing or mis-pinned component usually
Step 8: Never Etch a Lone Board
It takes almost no additional effort to make 4 or 6 boards. You already have the chemicals out... you will probably want another one. I never make fewer than 3 boards. Combine different boards as well.
Step 9: Print on Tracing Paper
Printing your artwork on tracing paper produces the best results. You can purchase paper inexpensively from any craft store 50 sheets for $5. It tends to crinkle near the bottom of the page, so always print near the top.
The pulp fibers wet out much better and solid than transparencies. The result is a very solid single-printed line.
Step 10: Over Expose & Develop
Every poorly etched board I've ever made was under exposed. Of course you can truly over-exposure, but error on the side of over and not under exposing, you can more easily fix gaps than copper that won't etch. So my pre-sensitized board instructions suggest 5-8 minutes. For my florescent bulbs, I found that I really needed 15.
HOW DO YOU KNOW?
- Drop the exposed board into the developer
- The resist should "smoke-off" (like a cloud) between 10 to 20 seconds.
- Then I leave it in for a while longer and brush it lightly just to make absolutely sure as much resist would get off as possible.
Over develop... If the photo-resist didn't see light, it will take hours to come off in developer. Give it a few extra minutes just to make sure.
Actual over exposure/develop starts showing up as little dots of missing resist on the back plane... If continued you'll have gaps in traces... Even this is much more easily fixed than traces that won't etch... Over expose!
Step 11: Heat Your Etching Chemical
It reacts faster and more predictably. I use about 120F; warm to the touch and keep it warm. The real pros use deep baths and bubblers to agitate the etchent, that's cool but it makes a huge mess and I found just swashing a small Pyrex casserole on a heating plate works very nicely.
Step 12: Backlight Inspection Is Awesome
You must inspect the board with Back-light. You can use a flashlight, hold it up to the lights, it doesn't matter, but it shows all the flaws in perfect detail. It's even better than front-light magnification. Light reflecting and refracting off copper can play tricks with your eyes... use back-light; it tells the true story.
I use it to great effect while etching by turning the lights out and placing a flashlight under the etch pan. You can clearly see when the etching is complete and get it perfect.
It's also great for general post etch inspection, flaw corrections and especially complex soldering.
GOOD LUCK!
Step 13: Think About Strength
I like to affix my boards directly to larger parts. This makes for compact designs that work well with nice solid connections. But traces are very structurally weak. They require reinforcement. Not hard, but one more thing to think through in design.
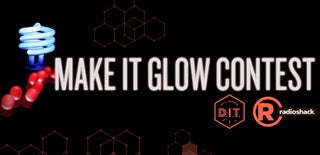
Participated in the
Make it Glow!
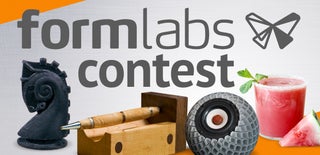
Participated in the
Formlabs Contest