Introduction: Upgrading the 3.5-Channel S032G Remote Control Helicopter's Landing Skids
So this is where the story begins.
Recently a package came via UPS to my humble abode bearing with it the indoor outdoor 3.5-Channel S032G Remote Control Helicopter, and be it that my excitement was greater than the warning not to use it in prevailing winds I decided to see what it could do. Unbeknownst to mother natures disposition towards ultralights, my naive self commenced liftoff into the brute force of the airstream and no sooner than the red dragon started its maiden voyage into the great blue yonder it careened into a mighty pine tree and started to go down. There were no survivors.
Upon further inspection accompanied by cussing and a general state of pure fury, I noted that the frame holding landing skids acquired irreparable damage, which added to my increased disdain towards Chinese manufacturing standards as well as my piloting skills. But upon further reflection with the passage of time I took this seamlessly pointless act of ill fortune and transformed it into a golden opportunity to make an instructable that not only gives me more practice in working in the 3dimesional realm and teaches you how to produce 3d objects tailored towards your own personal needs, but also allows me to take a mass produced object and make it my own.
This instructable will not teach you the basics of using blender, which is the free professional grade 3d modeling program which I'm most familiar with, but I will try and guide you, and I hope to explain it in such a way that will capture your attention and encourage you to further explore the endless possibility's that await you in the field of 3d prototyping.
Materials Needed:
3.5-Channel S032G Remote Control Helicopter
3d Modeling Software capable of exporting .stl files
A 3d printing service
Lets begin shall we...
Step 1: Setting Things in Motion
If you want to prototype your idea you will first need a 3d modeling software that can export .stl files to your favorite 3d printing service. Again I'm using blender but there are other programs available though my familiarity with them is limited, and by limited I mean nun whatsoever, so if you're a complete noob to 3d modeling and haven't been jaded by other programs I would highly suggest blender, and blender is what we will be using today so it would be highly advisable to download it if you haven't do so already, and because what we will be crafting today is fairly simple the scope of what you will be learning is just a fraction of what the program is capable of, so it would behoove you to look up other tutorials on how to use the program if you feel ever so inclined to do so.
Also the hardest part in all of this is making sure that the part that your model you create is in the same scale as your helicopter and that the holes to attach the skids line up with the holes at the base of our aerial vessel. This can be avoided by careful measurements. Other than that it's fairly simple and there really are no limitations to how creative you can get, you just need to make sure that your mesh doesn't have any holes in it.
Step 2: The Map
Before you get down to the nitty gritty of modeling, you can save yourself some unnecessary tears by mapping out what you want your final product to look like. This by no means limits you the that design alone, because I've found that while spending time working on a model your brain has the time to ponder it, and necessary adjustments will inevitably be gotten. So no need to fret if your final product turns out to be something completely different that what you planned, unless it sucks, then you should fret.
So what I usually do is sketch either the front, side or top depending on what exactly I'm doing and work from there. Sometimes even combining two similar ideas into one.
I have attach some sketches if you would like to look at them.
I have also attached photos of the helio itself so you can sketch something out yourself, and if your drawing skills are not where you would like them to be I'd suggest using the internet to strengthen this all important skill. If you want to be an inventor it's imperative that you can present your ideas in a way that people can easily understand what your final vision is.
Step 3: The Model
Next comes the slow and arduous process of modeling. This is way beyond the scope of this instructable but in case you haven't click any links yet, there are numerous well made tutorials out there that discuss this in great detail.
I have attached some blend files so you can play with them if you'd like, there each a little different but still conform to the same standards, and although I didn't deiced to get them printed I wouldn't mind experimenting printing them out with a Up! 3d printer.
The way that I like to model is to first make a general outline of what I want, then slowly shape and add pieces from there. It's similar to the style of box modeling.
Step 4: The Birthing
Next you will need to save you model to an .stl file so 3d printing services can print it.
In blender this involves simply going to File>Export>Stl (.stl) and if your model is manifold it should print the way intended.
If not it might mean that there's holes in the mesh, the problem areas can be determined by pressing ctrl+alt+shift+m, problem areas will be highlighted.
Once you have your .stl file you will need to find a 3d printing service. I used ponoko for this instructable, they gave the option of using centimeters which surprisingly enough isn't usually offered by other 3d printing services, and they're very helpful and patient. They also have bases in the United States which greatly reduces shipping costs and delivery time. When you send your model to market they'll let you know trouble areas that need to be fix.
Step 5: The Package
Now all you have to do is wait for the intricate machine that is the postal service to deliver that which you've so passionately slaved over.
It took about a week to get the model perfect and finding a printing service, about a month for the printing service to get to it, about 4 hours for it to print and about a week for it to arrive.
If I did win a 3d printer it would be put to good use. I have many ideas that I am currently working on, many using a product called D30, and if I had a 3d printer this would allow me to print the D30 molds and implement them into clothing, while waiting for the real D30 molds to be made and shipped.
I thank you for your time and patients and I hope you learned something, or were at least entertained, and if there are any questions please feel free to contact me and I will answer them to the best of my ability's.
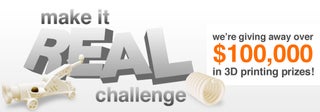
Participated in the
Make It Real Challenge