Introduction: Warcraft Doomhammer
Inspiration
When making game props, there are so many amazing examples and artists now to draw inspiration from. For me, I still hold Volpin Props up as one of the very best, and anyone who has followed him for some time will remember his amazing Doomhammer.
After seeing his work several years back, this iconic weapon has been on my wishlist to build ever since. With several versions appearing in games and on screen, I think it's fair to take some creative liberties with this massive hammer, so I added a few details, though the fundamental design is still at the core.
Overview
The bulk of the hammer is made from wood, with details added through 3D printing. This wasn't my original plan, but even this human-sized version is still quite large and trying to 3D print the head alone was projecting 40+ hour prints for each half, which I did not want to do. I went instead to the shop and created a wooden core, which gives the hammer a wonderful heft, though is probably not allowed at many conventions.
If you don't have woodworking tools, I think a great alternative would be rigid foam, which cuts with simple hand tools and weighs far less. The basic process would be the same, though a strong handle would still be necessary.
I didn't make this for a Thrall or Orc cosplay, I just wanted to make this hammer, and definitely enjoyed the journey of doing so.
I also have a video of this build here:
Step 1: 3D Modeling and 3D Printing
Modeling
To help plan the overall build, and certainly to create the 3D printed details, I turned to SketchUp for modeling.
Modeling the basic shapes are simple enough and easily done at the real scale. When modeling finer details though, it helps in SketchUp to scale up your geometry by a factor of 10 or more. SketchUp is more of an architectural tool and just works better on larger scaled objects while editing them. Once complete though, scale your geometry back down to the size you need and you are ready to go.
For 3D printing with SketchUp, there are a few plugins that are essential, and fortunately, also free. These can be found in the Extension Warehouse. The first is the STL importer/ exporter from the SketchUp team. Beyond that, grab 'Solid Inspector' from Thom Thom. Solid Inspector will examine your groups and check if there is stray geometry or missing faces, and when possible it will try to fix them. This is important for 3D printing.
STL files
All the parts for this hammer are available here on Thingiverse . If you want to fully print this hammer, all the files are available. The parts are designed to fit together, just keep in mind that the hammer head and handle will require a lot of material and time.
Finishing the printed parts
After printing the pieces I further smoothed them by applying some wood filler, thinned with just a bit of water to help it spread easier. This filler goes on purple and dries to white, so it's easy to know when it is ready for sanding. A bit of hand sanding, and a sanding mop is also helpful to give it a nice surface. Finally, all parts were sprayed with a filler primer.
One final note. You'll see that I left the small knobs and wolfs head on their 3D printed rafts. This was very helpful in all the prep and initial texturing so I wasn't trying to hold and finish a bunch of small parts individually.
Step 2: Constructing the Hammer Head and Handle
Hammer Head
In the interest of simplicity and cost, I made the head from 2x6 dimensional lumber. Choose as straight a board as you can find, and rip each side down to achieve the final size, around 5 inches. This also helps to remove the rounded edges that come from the store. To build the final width, I laminated 3 boards together.
The chamfered side on each end was also made from the 2x6 board, cut at 45 degrees. Cut it a little large then creep in on the final size so it matches the center of the hammer head.
Each side of the center was also chamfered with a 45 deg cut.
(Note, this is where I think pink rigid foam boards could be used if you don't have woodworking tools. It comes in varying thicknesses, can be cut with a simple knife and can be sealed and then covered with resin or bondo to give it durability.)
Handle
I used oak and turned it on a lathe. Granted, I'm fortunate to have this tool, but this is just a round handle, so a combination of PVC and pipe wrap could be used to create the proper size as well.
Turning dry oak is tricky at first, especially if you don't round over your corners, so I highly suggest taking the corners off. After that it was a matter of turning it generally to the final size, measuring as turned to fit the 3D printed parts. The handle widens slightly toward the base, and I also made it slightly longer than the typical game version, just as another personal preference and way to make this unique.
A forstner bit was used to drill a mortise for the handle tenon and the size of the tenon could vary to fit whatever material you use.
The parts were joined with long screws, which will be covered over in the next step. To make sure the alignment was correct, I did glue these pieces first, but in this case, it's gluing to short grain in the wood, so that is not a strong connection, thus the real strength is added with the screws.
Step 3: Adding Details to the Hammer Head
Hammer ends
The hammer head steps down several times, so I stuck with wood in creating these as well. A thin layer was added, using a block and weight to hold it flat while gluing, and then a final endcap was also glued after cutting it to size and chamfering the edges. As these are long-grain to long-grain surfaces, the glue will be all that is needed, and now our screw holes from earlier are hidden.
Banding
The banding around the head was also created with strips of wood. Because of the chamfer on the hammer, these are cut at an angle of 22.5 degrees. There are 3 basic sizes for the height, width and corner of the hammer, so after marking the sizes, I cut several at once, then fitted them, tweaking the length as needed for a close fit. Some wood putty can help fill any gaps. These also will be glued on, which will be plenty strong. They were tacked in place with brads to hold while the glue dries.
Authentic battle damage!
In Warcraft lore this hammer has been used and passed along to multiple mighty orcs, and over its long life will have amassed a wide array of scars. Nothing in Warcraft is subtle, so I wanted the many dents and scars on this hammer to reflect that. I took a large metal hammer and beat dents all over the wooden hammer and then took files to carve in dozens of scars. This was fun, it's starting to look cool.
I added similar scars to all the 3D printed parts as well in a later step.
Step 4: Masking
Masking the hammer
Before painting and weathering the hammer, I wanted to mask off areas where the printed parts will glue. I wanted the glue to attach directly to the wood, rather than to paint, so I taped off areas, traced the location of all parts, then cut inside those outlines to protect that area.
Finally, I can spray the hammer with primer, and after that dries, a dark metallic bronze as the base coat.
I wondered about creating more contrast in the details on the hammer by masking and adding some gold color but ultimately decided to keep things looking almost monochromatic.
To add scaring on the 3D prints, I did try a Dremel, which worked fine, but ultimately went back to a file for the most part as it just worked the best.
Step 5: Weathering
The hammer is your canvas
Using some basic acrylic paints, I blotted and rubbed in a mix of grey and black paint all over. Blot it on, rub it off, get it in the corners and all over till it looks old and awesome.
In the pictures, the hammer still looks fairly reflective because the garage opening was behind the camera, so it's casting a lot of light on those surfaces, but it actually was fairly dull when all the paint was dry. To bring back some amount of metallic shine, I dabbed on some silver paint, then buffed it around to act as a light coating all over. This created a bit of shine and depth.
Finally, taking a foam brush (or any brush, I just happened to have a foam brush nearby), I lightly scuffed the edges and corners with silver paint to highlight and add extra wear on those areas. This is a well-known method for a great weathered look.
Similar weathering was added to the large printed parts and the area of the handle that would be visible. (Most of the handle will be wrapped in leather.)
Step 6: Main Assembly
Glue time
This is quite straightforward, you are gluing the main parts together. The main consideration is to have the collar and other details on the handle before gluing it to the head, otherwise, you won't get them on later. I used wood glue for the handle and head, and cyanoacrylate glue for all the printed parts. I was going to use epoxy but found my bottles had dried. No worries, the cyanoacrylate glue is plenty strong for this.
Step 7: Adding the Printed Details
Details, details, details....
Things are getting exciting now, the hammer is assembled, feels awesome to hold, and ready to add in all those sweet looking details!
All the masking was removed, and parts glued on with cyanoacrylate glue. This goes fairly quickly if you have an accelerator as well, so I sprayed the accelerator on the wood, applied the glue to the part and then held it down for just a few seconds to bond. Rinse and repeat.
The accelerator and glue can create some fumes, so it's good to do this in a well-ventilated area.
After gluing all the parts together, I used a bit more paint and weathering just to hit the edges. The details were finished with a darker spray paint, so have just a bit of contrast from the mass of the hammer.
Step 8: Wrapping the Handle.
Wrap this present up and give it to an Orc
So close to the finish line now. I cut strips of faux leather and started wrapping them around the handle, with a bit of glue along the way. The faux leather has a bit of stretch to it, so it works well to pull and stretch it just a bit while overlapping as you go for a tight fit. Cut a steep angle into the strip at the top and bottom to help start and finish the wrap.
Ideally, I would have had a piece long enough for the entire handle, but didn't, so completed it in two strips of leather.
With more grey and black paint, the handle was also given a lot of grunge weathering.
Step 9: It's So Pretty!
I couldn't be happier with how this turned out. It feels amazing to hold and adding some personal details makes it feel unique. Although some people confuse this with Mjolnir, Thor's hammer, any true Warcraft fan knows immediately what this mighty weapon is.
If you make one, please share, would love to see how yours turns out. Cheers, and....
FOR THE HORDE!!!!!
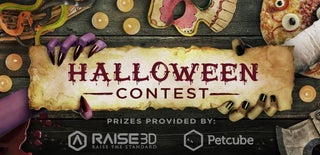
Third Prize in the
Halloween Contest 2017