Introduction: Pi-ano Bench
I made this bench just for fun. Despite the title, unsuitable as a piano bench. Its height cannot be adjusted and it is uncomfortable due to its protrusions. When preparing it, I tried to keep the following in mind:
- cheap, from leftover materials found in my environment
- material-saving, small-sized parts - can be made with few tools (this did not work)
- those with a cnc machine can make it even easier
Pi-ano bench parts
Supplies
Used materials:
- A1 size sheet of paper
- particle board (residue)
- 8 mm plywood
- 32 millimeter cylindrical wooden bar
- 200 millimeter cardboard tube (pvc pipe is also good)
- polyethylene foam
- fabric
- wood glue
- double sided adhesive tape
- screws
- varnish or paint
Necessary tools:
- jigsaw
- screw driver
- hand milling machine
- sander machine
- bit and drill for the screw used
- 35 millimeter drill bit
- 22 mm drill bit
- adjustable curved shaping strip
- clamps
- abrasives
- pneumatic stapler
Step 1: The Template
- First, I made a Pi symbol using Tinkercad. (CNC machine users can also use this plan for the simple retrofit.)
- I printed this on paper, then scaled it up and drew it on an A1-sized sheet of paper.
- I glued this drawing to the chipboard and, matching the lines, screwed up the flexible template for routing.
- I put the first screw at the intersection of the circular arc and the straight section.
- I screwed in the straight section (this way the flexible template has a hold in it and can be nicely fitted to the curve).
- I screwed the bend, leaving a little straight line at the other end so that the router would run nicely.
- I took off the flexible template and the sheet of paper.
- I screwed the flexible template into the screw holes formed on the chipboard.
- I drew the line next to the flexible template.
- I repeated this process with each component. I cheated when creating the lines because I couldn't copy the drawing exactly (but it's not a problem). I created the small curves with a drill. A simple and cheap carbon steel 7 piece hole saw set is suitable for the purpose.
- I drilled the small arcs so that the straight line is tangent to the circle.
- I cut out the parts with a jigsaw, with the saw blade shown in the picture.
- I screwed up the flexible template.
- I cutted it to the exact size with a manual router.
Step 2: The Parts
I made the bench from 8-millimeter plywood, glued together in three layers per component. The plywood is ugly because it was the packaging of a vending soda machine. I placed the chipboard template on the plywood and traced around it. Meanwhile, I noticed that if I shape the middle part of the legs differently, I get a more stable, dovetail joint. (I corrected this on the Tinkercad drawings.) I have the six different parts:
- front leg cover 4 pieces
- front leg corer (longer due to the taping) 2 pieces
- rear leg cover 4 pieces
- back leg corer (longer due to the taping) 2 pieces
- upper middle core 4 pieces
- upper mortise middle core 2 pieces
The templates for the legs are suitable for both the cover and the core. I first made the covers using the template of the upper connector. After that, I drilled out the place of the mortises on the template, and then made the upper connecting core with it. I made a 22 mm hole for the inner covers of the legs. I cut 8 mm long tennons to the ends of the 32 mm rod to the size of the holes. It's that big because I used a broken shovel handle. It took me a lot of time to polish it nicely :(.
Step 3: Sticking
Be sure to do a dry test, correct the parts if necessary. Make 6-8mm holes to hold the parts in position with wooden dowels. Unfortunately, I neglected to do this, and the plates slipped on the glue. First, I glued the legs together, corresponding to the left and right sides (mirroring). After that, I smoothed out any unevenness with a flush trim bit with insert knives. In the core of the upper mortise, I inserted the tenons of the legs, making sure that the 22 mm holes are on the inside. After drying, I also smoothed this with the flush trim bit with insert knives.
Step 4: Sanding
There is not much to say about this work phase. Sanding curves is slow and difficult. I used everything I could get my hands on.
Step 5: The Seat Top
The seat became the most complicated part of the bench. Very spectacular, but very dangerous. Several people sat on it reversed. The center of gravity was on the wrong side and the bench tipped over. Therefore, I recommend that you build what is shown in the drawing. I made the seat from a 30-millimeter-thick, three-layer wood panel.
- I made two sheets (bottom and top). I cut its width four millimeters smaller than the net length of the 32 millimeter rod.
- I made a recess on the panel the same size as the wall thickness of the pipe.
- I determined the size and shape of the spacer with a dry test (I cut the ends at 45 degrees).
- I made four 290-millimeter-long French Cleat hangers from 12-millimeter plywood.
- I cut two 290 mm long spacers for the hanger from 14 mm plywood. (This is why the seat top is 4 millimeters smaller.)
- I made the places for the hangers on the board. The lower one is 24×290 millimeters, the upper one is 12×290 millimeters.
- I screwed the hanger onto the top board. (12×290 millimeters)
Step 6: Assembling
- In the 22 mm hole, I inserted the 22 mm drill bit.
- I drilled the location of the screw in the center of the hole (diameter 3 mm), then sunk it from the outside.
- I drilled and screwed the hanger and the spacer onto the legs.
- I assembled the bench.
Step 7: Upholstery
I glueing double sided adhesive tape on the three-layer wooden panel. This is how I stretched the polyethylene foam on the wooden board. The foam must not turn to the side of the seat! I repeated this in several layers. Finally, I attached the Cookie Monster fabric with a stapler.
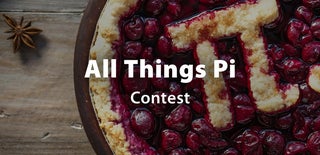
Participated in the
All Things Pi Contest