Introduction: Quick Shifter Under $50! Kazeshifter Arduino Adjustable Quick Shifter
Hi Superbike or motorcycle lovers!
On this instructable, I'll share how to make your own Quick Shifter for cheap!
For people who lazy to read this instructable, just watch my video!
Note : For some bikes that already using Fuel Injection System, sometimes Check Engine indicator light up. You need a resistor to make sure the ECU / ECM not thinking your ignition coils was bad or broken.
Enough intro just go to the steps!
Last updated : Feb 4, 2021 (added multi-cylinder wiring diagram).
I don't make changelog coz am lazy, it's too much
Support me on Patreon !
https://www.patreon.com/kazemito
Subscribe to my Channel !
https://www.youtube.com/c/KazemitoHaruhi
Step 1: 1. What You Will Need? How About the Schematic?
READ THE SCHEMATIC FIRST, MAKE SURE YOU ARE NOT FOLLOWING WRONG SCHEMATIC.
OLD SCHEMATIC WAS REMOVED SOME PEOPLE HAVING TROUBLE WITH I2C LCD.
So here is the parts that you will need :
- Schematic(READ THE SCHEMATIC MAYBE I FORGOT TO INCLUDE SOME PARTS)
- Arduino Nano, or anything smaller than nano if you want
- ON OFF Switch (for bypass switch)
- Relay module
- 100uF/25v and 1uF/16v Capacitor
- 150 ohm Resistor and 1 LED for indicator
- 330 ohm to 1K ohm resistor needed for EFI (injection) bikes to eliminate check engine error!
- PCB (small is enough)
- Small Multipurpose Box
- 1N4007 Diode or any kind of
- Rear Brake Switch with the spring or use Reed switch with magnet (easier to install and adjust)
- Steel Bar for making the spring holder and brake switch
- Pin Headers
- small 1K ohm Variable Resistor (some people call it trimpot or trimmer)
for the brake switch, I'm using switch for Honda Grand because it's cheap
I don't use MOSFET because it cause problem last time, and I have no idea why. You can try it if you want and don't forget to change the code.
Step 2: 2. Code? Here Is..
I've made some revisions on this code, just check up my Github Gists page!
Here is the Code. No display version because a lot of people got problem with the LCD not displaying anything, and most of them don't know how to find the LCD Address, so stick with no display version.
Sorry for giving the code on other website :(
Step 3: 3. Solder All Components Into the Board!
Make sure you use small and tight fit all components inside the box, so you can get compact fit on your motorcycle and not use much space on it!
This pictures is early build of my project, so I hope you can ignore mess that I made and it uses MOSFET (before accident happened.) lol actually no accident just FET is blown.
To set the timing, you should edit the code that I've mention on the code, usually uses 60ms - 100ms, and it depends on your motorcycle! make sure you use higher first then slowly decrease it 5 by 5 (100, 95, 90, etc).
Step 4: 4. Sensor/Switch Mounting
(Update) First things! You need to lubricate the brake switch, so it won't stuck if it's get wet and dry many times and keeps it smooth. Any lubricating liquid will work fine.
For the spring holder, I used the steel bar and you can place the spring holder anywhere do you want, or just mount it on the bolt that near on the footrest.
but I'll mount it and use the spring holder under the footrest
and route the spring behind the pedal rod linkage. (am I right?)
anyway, for the placement of the switch, i mount it on the shift linkage rod and I fix it with Zip Ties after I set the sensitivity
ah, you need an LED (12v or whatsoever) to know where the sensitivity is, just connect the LED to the switch and begin setting the sensitivity.
you might need to reset the sensitivity when you test it on the road. don't too sensitive or it might ruin your day (but for what I made the bypass switch?)
when routing the cable, give it a small excess of the cable or whatever it called. don't tighten the cable or you won't be able to downshift
Step 5: 5. Connect Everything!
First thing is place the module under the seat and remove bolts from the tank, route the cables from the relay on the module under the tank, make sure isn't pinched by the tank and keep away from it. then find the ignition coil.
after you found the coil, unplug 1 cable from the coil, then connect 1 cable from the relay on the module to the coil. and connect other cable from coil that has been unplugged from the coil to the other cable from the relay on the module
Route positive (VCC) and clutch cables from the module under bike frame, make sure isn't pinched by seat.
For the positive input (VCC) I connect it to the blinker relay, because it goes directly to the ignition key and every motorcycle is different wiring so you should search the nearly power source from the ignition key
and clutch cable (from the module) I connect it to the Clutch Relay
Negative cable? just connect it directly to the battery or the bolt on the bike frame (Ground)
don't forget to connect the switch relay! or it might not work
Step 6: 6. Wiring for Multi-Cylinder Motorcyles (EFI ONLY, CDI EXPERIMENTAL)
This is wiring diagram for Multi-Cylinder EFI bikes, CDI may work and this is experimental. Testing the cables also same method.
You need a multimeter or multi tester or 12v LED to test the ignition coil socket pins.
Select 20V range or just leave to auto range if your multimeter had this feature
unplug 1 socket from ignition coil
put the negative probe to the chassis or straight to the negative terminal on the battery if your probe cable long enough
turn the ignition key ON and disable engine kill switch (I mean engine enabled position on the switch beside the throttle)
test each pin on the ignition coil socket with positive probe and make sure you got 12v - 13v range (not 0v) or the LED lights up which means you had common anode wiring on the coils.
if you are not getting any voltage try to flick the engine kill switch to another direction, and if still not getting any voltage try the next step. otherwise skip to step 12
Connect positive probe to positive terminal on the battery
turn the ignition key ON and disable engine kill switch (I mean engine enabled position on the switch beside the throttle)
test each pin on the ignition coil socket with a negative probe and make sure you got 12v - 13v range (not 0v) or the LED lights up which means you had common cathode wiring on the coils.
If you are not getting any voltage try to flick the engine kill switch to another direction.
cut all common cable from your ignition coils or the sockets (anode means positive and cathode negative)
connect the common cable that you cut to the relay common pin (you just need 1 common cable from ignition coil / socket since it's common anode)
connect the Normally Closed (NC) pin from relay to all those ignition coils / sockets common cablethat you cut
you're done. You can test it and make sure you attach the resistor across the NC and Common pin for your EFI Bike
Step 7: Test It!
That's it for this project, I hope you like my creation and forgive my lack of information telling detailed information about mounting, circuit, schematic, etc. because I have no idea last time and don't know how to perfectly make a tutorial video. This project maybe started on September 2018 and that's why I new at video making and tutorial video
Come and support me !
Support me on Patreon !
https://www.patreon.com/kazemito
https://www.patreon.com/kazemito
Instructables
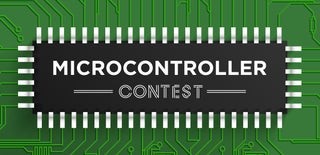
Participated in the
Microcontroller Contest