Introduction: 3D Printed Clamps for Programmable Sewing Machines
Computer controlled cycle machines, or more commonly known as programmable sewing machines are vital to any cut and sew facility or textile manufacturer. They take complex slow sewing steps and turn them into fast, accurate and repetitive steps. This reduces time spent and allows manufacturers to be more competitive when estimating work for customers.
But they have one flaw. They require clamps to hold the material in place while the sewing operation happens. This means that for each unique sewing program, there will be a clamp to go a long with it. There are some situations where you might have similar programs making use of the same clamp but that is the exception not the rule. You can normally get these clamps custom made through your local parts dealers but the prices are astronomically high. On average, each custom clamp and program costs me $600. When you make 15-20 clamps each year, this can add up very quickly.
So what do you do to circumvent this high price for clamps? Most would just add the cost of the $600 clamp into the estimate. This is fine for most but there are situations where a $600 bump in the estimate could make or break a project. If you see these machines in China, they make their own clamps out of cardboard. But then they have to apply additional pressure with their fingers to ensure the material is clamped down.Which is extremely dangerous and far from ideal. This is where 3D printing comes in. If you have access to a 3D CAD modeling software and a 3D printer, you can turn your $600 per clamp cost into less than $10.
There are some issues with 3D printed clamps though. They are less durable than an aluminum clamp, which means eventually they might wear out or break from use. The good news is that a replacement clamp is only another $10 and several hours of printing time away. You also might run into situations where you have to get very creative with your clamp design in order to achieve the proper end result. This is a trial and error process that will take time to perfect.
The upsides outweigh the issues. By creating your own clamps, you will learn what works and what doesn't. You will find yourself utilizing this machine far more than before. And the best part is, if your idea doesn't work, you aren't out $600. All you have lost is a couple hours of your time and some 3D printer filament.
Step 1: Remove Metal Clamp From Your Machine
Most clamp setups with have 2 machine screws on each arm and 2 machine screws holding the base plate in place. You do not need to remove the screws for the base plate completely. Simply loosen them enough for the base plate to clear the locating pins.
Step 2: Use Metal Clamp As a Template
Pull your necessary dimensions from the metal clamp you have on hand. You will need to measure and record the hole layouts on the arms and base plate. You will also want to measure the distance from the mounting point on the base plate to the actual clamping surface. This dimension will not change no matter what style of clamp you use.
Step 3: Model Your Clamp in a 3D CAD Software
Once you have your necessary dimensions, model your clamp in a 3D CAD software. I use SolidWorks but any 3D software capable of creating an STL file will work. If you need free 3D CAD software, you could use Google Sketchup but you will need to install the correct plug-in because Sketchup doesn't export STL files natively. I won't go into detail on this. Just do a simple Google search to find the information needed to use Sketchup.
You will need to know the part size capabilities of the 3D printer you are using in order to build your model. A friend was printing my clamp on a Prusa I3 so I was limited to a work envelope of 200mm X 200mm X 200mm. The length of the base plate was too long to fit inside the work envelope so I made it a 3 piece design.
Step 4: Print Your STL Files
I won't go into detail about the printing techniques. There are many instructables for 3D printing. This is a good one:
https://www.instructables.com/id/3D-Printing-1/
The 3D printer was not set up properly when my clamp was printed. This was only the fourth or fifth item he had printed and he was still learning. I expect better results with my next clamp as I am more familiar with the tolerances used.
Notice how the knurling on the clamping surfaces did not print out properly. The next clamp I make, I will use a larger zig zag tooth feature instead of the knurling in order for a better printing result. The clamp still worked just fine so the lack of knurling did not appear to affect its clamping ability.
Step 5: Install the 3D Printed Clamp to the Machine
Install the 3D printed clamp on the machine and check your clearances. Ensure the clamp and base plate line up properly. Also ensure the clamp arms do interfere with the base plate.
Notice how the base plate has warped. This was due to the printing process. It did not affect the function of the clamp. This clamp was printed in PLA and he did not have a fan blowing on it so the print warped. I plan on printing the next clamp in Taulman Alloy 910 filament to increase strength and reduce warping.
Step 6: Create Your Custom Sewing Program
Now you are ready to create your custom program for this clamp. This will be dependent on the type of machine you have. Newer machines have a touch screen interface on the machine that you can use. Juki makes a computer software called PM-1 which allows you to create the program and transfer it to the correct media for the machine to read.
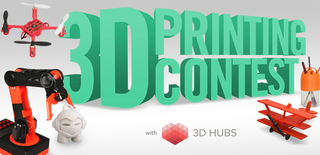
Participated in the
3D Printing Contest