Introduction: 3D Printed Omnidirectional Bluetooth Speaker
Hello everyone,
This Instructable has been in the making for quite some time. When I first finished building my 3D printer I wanted to take on a large print so I started designing a freestanding bluetooth speaker, it had to have room filling sound out of a small enclosure and it needed to be battery powered as in South Africa we have a lil thing called loadshedding so we are regularly without electricity for hours at a time.
As time went by my first basic designed morphed into something more complex as I got more comfortable with design and printing.
This "final" design still incorporates the original body that I started with and I am quite happy with how it all turned out in the end.
Please join me on the journey of my first big 3D printed project.
Step 1: Everything That's Needed:
Here is a list of all the components that I used with links:
- 5W+5W Bluetooth MH-M38 Amplifier - Mh-M38
- 18650 Battery - 18650 Samsung
- TP4056 Lithium charger - Charger
- 4A 3.7V Battery BMS - BMS
- TTP223 Touch sensor - Touch sensor / Mosfet
- 5mm LED of your choice with 50ohm resistor
- 2x 50mm x 90mm Passive radiator - Passive Radiators
- 2x 30mm x 72mm Passive radiator - ^ ^ ^
- 10cm/4in Full range speaker driver - e.g. Good full range candidate
- 4cm/1.5in Tweeter - e.g. 1.5in Tweeter
- 10mm Aluminium pipe - salvaged mine from an old antenna
- 3x M5 45mm Screws
- Access to a 3D printer
- CA Glue
- Bondo filler
- High filler primer
- Sanding paper
- Spray paint
- Silicone sealant
- Soldering iron & solder
- 4.7uf capacitor if not included on your tweeter
- Power switch if not using ttp223
Step 2: 3D Printing:
This step will take the longest luckily a machine will be doing it all for you....oh what a time to be alive!
All the printed parts needed for the speaker was made in TinkerCAD and is very simple to modify to fit your own components. In the future I will be adding additional files to support a wider range of speaker drivers, feel free to leave me a comment if you would like me to make one to fit your parts.
The maximum size is 160mm x 160mm so most 3D printers should be able to print all the necessary parts.
I recommend using ABS or PETG filament to print all the parts as my first attempt was in carbon fibre PLA and after I accidentally left it on the table in front of a window it got a bit...uhmm...out of shape.
I printed using a 0.6-0.8mm nozzle, no supports are needed on any of the parts and the larger pieces can be printed with a brim if you have problems with warping.
The last piece ( number 9 ) was printed using TPU to give it a nice soft base but if you don't have some TPU available you can just stick some rubber feet on the bottom to prevent any unwanted rattling.
Step 3: Hard Labour...
Now that the machines did all the heavy lifting it's time to put in some elbow grease...
This was the most time consuming step on my part, all the printed parts had to be finished off to get rid of those pesky layer lines and give a nice smooth finish.
First you need to use some CA glue to stick part 1 and 2 together ( Align the small hole on part 1 with the angled hole on part 2 ) to form the top of the tweeter enclosure and then part 4 and 6 to form the top of the woofer enclosure. ( Parts 4 and 6 have 4 holes that can be used to align the parts )
I then took some Bondo filler ( mixed to manufacturers instructions ) and covered all the pieces except 9. Don't go overboard with the filler or you'll regret it later when it is time for sanding.
Give the filler a few minutes to set up and start sanding away all the excess with 80-220 grit so that you are left with parts that are mostly free from defects.
Personally I don't leave my filler to dry completely before starting to sand as it makes the process a lot easier.
Here is a great Instructable by BrittLiv to smooth out your prints: How to Smooth 3D Prints
After the filler you want to spray your parts with some primer, do this in thin coats and wait for each coat to dry completely.
TIP: Spray a very light coat of matt black paint over your primer before sanding, this will highlight any imperfections as you are busy sanding.
Time to get sanding again... sand the primer with water and some 400 grit paper to get rid of as many imperfections as possible and leave you with a nice smooth base for your paint.
When you are happy with the look of your primed and sanded parts you can go ahead and give them a few coats in the colour of your choice, I chose a classic satin black for mine.
Step 4: Start Assembling...
Now it's gonna get exciting as all your hard work starts to take shape!
Start by cutting your 10mm aluminium pipe into 5 pieces 1x 50mm and 4x 25mm.
Next you can glue the tweeter into it's enclosure, and then glue the 50mm aluminium pipe into the angled hole of the tweeter enclosure. Feed the tweeter wires through the pipe and then glue the bottom cap (3) on to complete the enclosure.
To assemble the woofer enclosure... Screw your driver into place and seal all around it with silicone sealant to make sure that it is airtight. Next you need to push the driver grill (5) into place, it should be a tight fit but I would also add a drop of glue to make sure there's no rattles. Now you can feed the tweeter wires into the woofer enclosure and glue the aluminium pipe from the tweeter enclosure into the angled slot in the woofer enclosure.
Feed both drivers wires through the back right screw hole on the bottom of the enclosure.
Now the radiator plate, add a bead of CA glue around the lip of your passive radiators and stick them in place, they can go either way around.
We can now close up the enclosure, I stuffed some polyfiber into the enclosure to dampen some of the unwanted noise but this is completely optional.
Add a bead of sealant around the inside lip of the enclosure to ensure an airtight seal when we press in the radiator plate, feed the wires through one of the holes in the plate (7) and then press in the radiator plate making sure all of your holes line up.
Screw the 3 bolts with the 25mm pipes on into the remaining holes. The remaining 25mm aluminium pipe goes around the wires so that it looks the same as the screws in the end.
Next is the bottom electronic enclosure (8)
One of the 4 holes in the enclosure has a hole that you can now feed the wires from the drivers through.
Push the electronic enclosure (8) onto the screws of the woofer enclosure (6), as before if you prefer you can add a drop of glue before pressing it together.
Now that parts 1 to 8 are all one piece we can move onto the electronics.
Step 5: The Electronics:
We start by preparing our battery, for safety and to make sure the there is not a bottle neck at the charging boards protection I added a separate 4 amp BMS to the battery so that I use the TP4056 board only for charging.
Following the schematic:
Starting at the TP4056 board we solder wires onto the B+ and B- points on the board, I will not be using the P+ and P- as i'm using the external BMS. If you will be using a lower powered amplifier like a PAM8403 you can use the TP4056's onboard BMS that is rated for 1-2amp and omit the 4amp BMS from the build.
Pay careful attention to the silkscreen that's on the boards that you are using as it may differ from the ones I used.
The wires coming from the TP4056 now gets soldered directly onto your 18650 battery, B+ from the board goes to the top (vented side) cap and the B- goes to the bottom flat side of the battery. If you are unsure of the polarity of the battery you are using please search the model number online first to make sure before soldering.
"Hazards
Lithium batteries are generally safe and unlikely to fail, but only so long as there are no defects and the batteries are not damaged. When lithium batteries fail to operate safely or are damaged, they may present a fire and/or explosion hazard. Damage from improper use, storage, or charging may also cause lithium batteries to fail. Testing batteries, chargers, and associated equipment in accordance with an appropriate test standard (e.g., UL 2054). NRTL certification (where applicable), and product recalls, help identify defects in design, manufacturing, and material quality.
Damage to lithium batteries can occur immediately or over a period of time, from physical impact, exposure to certain temperatures, and/or improper charging.
Physical impacts that can damage lithium batteries include dropping, crushing, and puncturing. Damage to all types of lithium batteries can occur when temperatures are too high (e.g., above 130°F). External heat sources (e.g., open flames, heaters, etc.) can also accelerate failure in cells with defects or damage from other causes. Damage to lithium-ion batteries can occur when the batteries themselves or the environment around the batteries is below freezing (32°F) during charging. Charging in temperatures below freezing can lead to permanent metallic lithium buildup (i.e., plating) on the anode, increasing the risk for failure. Charging a device or battery without following manufacturer’s instructions may cause damage to rechargeable lithium-ion batteries. For example, some manufacturer-authorized chargers will cycle the power to the battery on and off before it is fully charged to avoid overcharging. Since ultra-fast chargers may not cycle power, do not use them unless the manufacturer’s instructions include them as an option. Heat released during cell failure can damage nearby cells, releasing more heat in a chain reaction known as a thermal runaway. The high energy density in lithium batteries makes them more susceptible to these reactions. Depending on the battery chemistry, size, design, component types, and amount of energy stored in the lithium cell, lithium cell failures can result in chemical and/or combustion reactions, which can also result in heat releases and/or over-pressurization.
In chemical reactions, by-products from the electrolyte solution and electrodes can increase the pressure in the cell to the point where the cell walls expand and by-products leak out. Chemical by-products usually include carbon monoxide, carbon dioxide, hydrogen, and hydrocarbons. In many cases, the by-products are also combustible and could ignite. In combustion reactions, a thermal runaway releases byproducts that may ignite to cause smoke, heat, fire, and/or explosion. The by-products from a lithium battery combustion reaction are usually carbon dioxide and water vapor. In some lithium batteries, combustion can separate fluorine from lithium salts in the battery. If mixed with water vapors, fluorine may produce hydrofluoric acid, which is particularly hazardous because workers may not feel its effects until hours after skin exposure. Prevention Workplace injuries from lithium battery defects or damage are preventable and the following guidelines will assist in incorporating lithium battery safety into an employer’s Safety and Health Program:
Ensure lithium batteries, chargers, and associated equipment are tested in accordance with an appropriate test standard (e.g., UL 2054) and, where applicable, and certified by a Nationally Recognized Testing Laboratory (NRTL), and are rated for their intended uses. Follow manufacturer’s instructions for storage, use, charging, and maintenance. When replacing batteries and chargers for an electronic device, ensure they are specifically designed and approved for use with the device and they are purchased from the device’s manufacturer or a manufacturer authorized reseller. Remove lithium-powered devices and batteries from the charger once they are fully charged. Store lithium batteries and devices in dry, cool locations. Avoid damaging lithium batteries and devices. Inspect them for signs of damage, such as bulging/cracking, hissing, leaking, rising temperature, and smoking before use, especially if they are wearable. Immediately remove a device or battery from service and place it in an area away from flammable materials if any of these signs are present. If batteries are damaged, remove them from service, place in fire resistant container (e.g., metal drum) with sand or other extinguishing agent and dispose in accordance with local, state, and federal regulations. Contact a local battery recycling center for disposal instructions. Follow manufacturer’s guidance on how to extinguish small battery fires, which could include using ABC dry chemical extinguishers, Class D fire extinguishers (for lithium-metal), dirt, or sand."
After soldering the charging module to the battery we need to solder in the BMS to protect the cell from over charging/discharging and shorts. To do this we solder a wire from the positive of the battery to the B+ of the BMS board and then a wire from the negative of the battery to the B- on the board.
Next you can solder on a wire to the P+ (this will be the V+ 5V going to the remaining circuit) and a wire to the P- (this will be the circuit ground) of the board.
To turn the speaker on I decided to use a TTP223 touch sensor, 5v and ground are connected to the module and when it is touched it outputs a 5v signal on the OUT pin that can be connected to the gate of a mosfet to turn the amplifier on.
For the module to be used as a locking switch jumper B on the board has to be soldered.
Here is a Instructable by mybotic on how to use a TTP223 sensor: TTP223
^ This can also be replaced by a simple on/off switch ^
I've included a link to a great little easy to use mosfet board that I would use instead with the TTP223.
From the power switch we now need to solder the MH-M38 amplifier. Solder your power from the switch to the VBAT and GND. Optionally you can mount a ~1000uf 10-16v capacitor at these solder points to help keep the voltage stable.
From here you also need to solder on your LED to give you a visual indication that the speaker is turned on, the anode is connected to 5v and the cathode is connected to ground of the amplifier through the 50ohm resistor to limit the current.
Next Solder on your two speaker drivers to the left and right outputs. Make sure that you have a ~4.7uf capacitor in series with your tweeter.
Now arrange everything in the bottom of your electronics enclosure, there are slots for the charging module and 18650 battery to fit into and now it should be ready to turn on!
Step 6: Now the Moment You've Been Waiting For!
Once you're all done you need to connect it to a charger to activate your BMS and make sure your battery is full.
With the first power up you will need to pair it with a bluetooth device, it should display as MH-M38.
Now it's time to flip the switch, sit back and enjoy your creation.
Happy making!
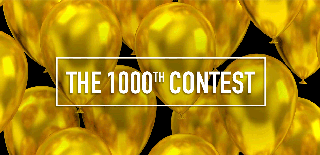
Runner Up in the
1000th Contest