Introduction: 3D Printed Quadcopter With Arduino
Lately the news has been buzzing with stories of drone technology. Be it for delivery, recreation, or military purposes, unmanned flight is the future of aviation. Beginning in December 2013, I began working on a drone with several of my friends. We have created a drone that is 100% our own design. Using Autodesk Inventor we designed, drafted, and printed each part of our copter's frame. We converted our files from .IPT to .X3G file, allowing us to print our frame on a Makerbot 2x Replicator. All of the external wiring was done and reviewed by each person working on the copter. The three other people who created this design have the Instructables accounts BobBurghart, CoreyOrlovsky, and RichardP4.
Step 1: Acquiring Components
Before any of the frame could be designed, we needed to consider the size, shape, and placement of all components. Our design is centered around an ArduPilot 2.6. In addition to this, we have one power distribution board, four speed controllers, four motors, and an FM receiver that must stay safely on the copter. All of these parts, with the exception of the GPS and FM controller for signal reasons, are kept safely inside of our frame, and will not be vulnerable to crashes.
Below is a list of all purchased components on our device:
APM 2.6:http://store.3drobotics.com/products/apm-2-6-kit-1
Radio Set (Android Compatable):https://store.3drobotics.com/products/3dr-radio
Compass Kit:https://store.3drobotics.com/products/3dr-gps-ublo...
PDB: https://store.3drobotics.com/products/quadcopter-p...
Motors:https://store.3drobotics.com/products/motor-ac2830...
Speed Controllers: https://store.3drobotics.com/products/esc-20-amp-S...
Propellors:https://store.3drobotics.com/products/apc-propelle...
Battery:https://store.3drobotics.com/products/4s4000-lipo-...
Power Module:https://store.3drobotics.com/products/apm-power-mo...
RC Reciever:http://www.ebay.com/itm/like/171474770621?lpid=82
Controller:http://www.hobbylinc.com/futaba-rc-fm-radio-4-chan...
All other parts of our device were made in AutoDesk Inventor, and fabricated by us using a Makerbot 2x Replicator.
Step 2: Designing the Center
Our center was designed to fit all components and allow no movement in the event of a crash. The bottom part of our frame is designed to house both the battery and power distribution board. The top of our frame is designed with compartments for our ArduPilot 2.6, FM Receiver, and GPS. Both were designed on Autodesk Inventor and printed on a Makerbot 2x Replicator under high quality settings with the bed heated to 100 degrees Celsius and the extrusion head at 240 degrees Celsius. We used PLA plastic instead of ABS because the PLA printed from our printer was found to be more durable. In step 8 are the files for the center of our quad copter.
Step 3: Designing the Arms
Our frame and arms are designed to fit together using three 4" long 1/8" thick screws per arm. Our arms are 21 centimeters long and are designed with trusses to create the strongest structure while also keeping the weight low. Our motor mounts are designed to house our motors if the housings fly off. The motors are attached with screws underneath them. These mounts were designed using Autodesk Inventor and printed using the same settings as our previous prints. The arm file in step 8 is a .stl file of our arm.
Step 4: Printing
Export all files as .STL files from Autodesk Inventor's file type .IPT. From here we open Makerware software and scale all files to 100%. Set to the settings described in Steps 1 and 2, then save the printable file onto a secure digital (SD) card. Put this into your printer, and wait for the prints to finish.
ALWAYS HIGH QUALITY! ALWAYS WITH RAFTS ON!
Step 5: Wiring
Plug the Battery into the PDB and the PDB into all speed controlled motors. Make sure that the polarity is swapped on the "push motors ( motors on opposing corners with pull propellers) The wiring is quite straightforward:
1) Plug battery to APM Power Management cable, and APM power cable connected to the APM power input, the Deans connector should be out from Power Management cable to the Quad copter Power Distribution Board
2) ESC are to be hooked into the Quad copter Power Distribution board
3) The PDB should lead to all speed controllers and motors
4) The receiver should be plugged to the APM, Set all control components and plug them into their corresponding ports.
Many copters have been made using this setup.
Step 6: Propeller Setup
All propellers rotating clockwise should be push propellers (motors 3 and 4 in the diagram), and all props rotating counter clockwise should be normal propellers ( motors 1 and 2 in the diagram). Ensure that you have proper motors for your copter and proper propellers for your copter. Our propellers are 10.5" props that have effectively lifted our machine.
Step 7: Flight
Now that you've created your quad copter, it is time for flight! Our machine is flyable by either GPS or FM transmitter. Have fun!
Step 8: Compatable Files
There were some complaints of non-Inventors designers being unable to view or edit my files. I reformatted our parts as .stl files, and hope that they are usable by all.
If further problems occur, please post a comment and I'll be sure to respond as fast as I can.
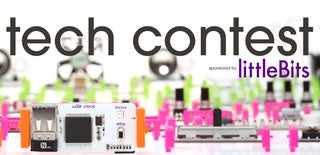
Participated in the
Tech Contest
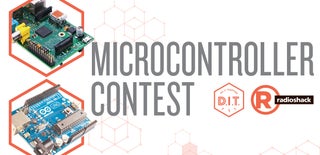
Participated in the
Microcontroller Contest
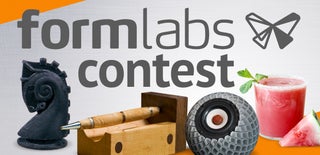
Participated in the
Formlabs Contest