Introduction: 3D Printed STEM Racers
These 3D printed STEM race cars are the perfect project based learning tool to help teachers get kids excited about science, technology, engineering, math, and nutrition to boot! The racers I show you how to make in this instructable will provide an opportunity to turn almost anything (no kittens or other live things please) into a race car – allowing different sized and weighted objects to illustrate mechanical physics concepts like mass, friction, force, speed, distance, and gravity!
Will the larger, heavier squash win? Or will the lighter and more streamlined carrot cross the finish line first? What a fun way to find out!!
Ok, let's get to making a thing...
Step 1: Supplies
Here are the lists of what you'll need to make TWO racers:
General Supplies
- Assorted sizes bag of rubber bands*
- Set of 8 skateboard bearings (enough for 2 racers)
- Needle nose pliers
*If you don't have access to this exact bag, try and find rubber bands that are 1 7/8" (approx. 48 mm) long when pressed flat. These are necessary for the size of wheels we'll be making.
NOTE: All the pieces of these racers have been designed to press fit together, so there's no need for glue or any connectors!
3D Printing Supplies
You can absolutely follow along with this project without actually 3D printing anything (i.e.: you can just do the 3D modeling part), but if you do want to end up with a physical version of your design that you print yourself, here are the tools and supplies you'll need in order to make it.
- 3D Printer*
- PLA filament that is the right size for your printer
- Wide painter's tape
- Credit card for smoothing out the tape on the print surface
- Rubbing alcohol or an alcohol based lens cleaner (optional)
- Sharp chisel (optional)
*To read a great overview of good quality hobby 3D printers, read through lesson 1 of JON-A-TRON's Easy 3D Printing Class!
NOTE: If you don't own a 3D printer, no problem! There are several 3D printing service companies that will print your design for you (and mail it to you) for a very reasonable price, like Shapeways and Ponoko.
Different Weighted and Shaped Objects
The purpose of this project – other than the pure fun of racing – is to provide a 'vehicle' to help demonstrate the concepts of mechanical physics by racing a variety of objects.
Produce offers a wide array of weights and shapes AND fun colors. I recommend racing produce, because:
- Salad Speedsters*
- Veggiemobiles*
- Garden Go-Cars*
- Fresh Formula One Cars
The name game with produce is strong... :D
*Thanks to Randofo for these suggestions!
Step 2: Using Tinkercad
To design/model this project, I used Tinkercad– a FREE browser-based 3D modeling program by Autodesk – which is very simple to use, even if you're a complete newbie!
NOTE: I won't be covering Tinkercad navigation tools or program functions in this instructable. If you're completely new to the program and either don't know where to start, or are having trouble following along, have a quick read through Lesson 2 of my co-worker JON-A-TRON's Easy 3D Printing Class. It covers everything you need to know to get started from scratch in Tinkercad!
Sign in to Tinkercad and Create New Design
Go to the Tinkercad website and sign in if you already have an account, or sign up if you don't.
Once you're signed in, click on create CREATE NEW DESIGN to generate a new project workplane.
The page will come already named with funny made up words. Highlight the name by clicking on the words and change it to something project related, like 3D Printed STEM Racers. (The above image is from my LED Egg Night Light project!)
Now we're ready to model our project!
Step 3: Modeling the Wheels
Since the chassis was a bit of a complicated design, I'm going to just supply you with the STL file in the next step so you don't have to go through the hassle of making it.
I will however, go over how to model the wheels! The above video shows the whole process at real time speed, and below, I'll break down the process using still images.
Let's go!
- In your fresh new Tinkercad workplane, click and drag a cylinder onto said workplane.
- Change the cylinder settings to the following:
Sides* - 64
Bevel - 2.5
Segments - 5
*NOTE: If you don't change the SIDES setting to the highest possible number, you will end up with a faceted, non-smooth rolling wheel. This will seriously slow down your racer.
- Resize the cylinder to be 50 mm x 50 mm x 15 mm High
- Change its color if orange isn't your jam. (Optional)
- Bring in another cylinder and increase its SIDES setting to 64. (IMPORTANT!!!)
- Resize it to be 22.12 mm x 22.12 mm x 20 mm high.
- Make it a HOLE.
We will be using this cylinder as a HOLE to create a space down the center of the wheel where the skateboard bearing will go. It needs to be this exact dimension so that the bearing gets a snug press fit into the wheel, which will keep us from having to use any glue.
- Select both cylinders and ALIGN them by clicking on both middle black dots on the workplane.
- Once aligned, select both cylinders and GROUP them.
This creates the center hole for the bearings.
Now we are going to create a ridge inside the bearing hole as a 'stop' so that the each bearing will sit in the exact center of wheel.
- Make the wheel shape TRANSPARENT.
- Bring in another cylinder and resize it to be 24 mm x 24 mm x 2 mm high.
NOTE: It isn't necessary to increase the SIDES of this one, as the outer edge will be buried in the body of the wheel.
- Bring in a HOLE cylinder and increase its SIDES to 64.
- Leave the cylinder at its original 20 mm x 20 mm x 20 mm high size.
- Select both the small flat 24 x 24 x 2 cylinder and and the new cylinder HOLE and ALIGN them.
- Select both shapes again and GROUP them, leaving a small ring shape.
- Select both the ring and the wheel shapes and ALIGN them.
- Go to a SIDE ORTHOGRAPHIC VIEW.
- Select just the ring by highlighting both shape, holding down SHIFT, and deselecting the wheel.
- Use the small black arrow to raise the ring 2 mm (from the bottom edge) off the workplane.
- Select both shapes and GROUP them.
Now we're going to make the ring HOLES that we'll use to create the 'track' indents that will act as guides for where the rubber band 'grips' will go.
- Bring in a cylinder and resize it to be 56 mm x 56 mmx 3 mm high.
Note: There's no need to increase the SIDES as this outer edge won't be touching the wheel.
- Bring in one more cylinder (the last one!) and resize it to be 49.65 mm x 49.65 mm x 20 mm high.
- Increase the SIDES to 64.
- Make the inner/taller cylinder a HOLE.
- Select both shapes and ALIGN them using both middle black dots on the workplane.
- Reselect the same two shapes and GROUP them, leaving a large ring with a smooth interior wall.
- Select the ring and the wheel shapes and ALIGN them.
- Go to a SIDE ORTHOGRAPHIC VIEW.
- Make the ring a HOLE.
- Raise the ring up, using the little black arrow, until it is 9 mm off the workplane (from the bottom edge).
- DUPLICATE the ring and using the little black arrow, lower the duplicated ring until it is 3 mm off the workplane.
NOTE: I accidentally made the wheel a HOLE when making my wheel (which I fixed in the next step), so be sure that you don't copy my mistake – keep your wheel shape TRANSPARENT! :)
- Select all three shapes; the wheel and two rings, and GROUP them.
You are now done modeling the wheel. Nice work!!
The only thing left to do is EXPORT the wheel as an STL FILE by selecting it and clicking the EXPORT button. STL is one of the 3 options. This will be saved to your DOWNLOADS folder.
Step 4: Chassis File for Download
Here is the file for the racer chassis (body). Download it to your computer so that it can be uploaded to be 3D printed in the next step.
Pssst.... I also included the wheel file in case you had trouble with the modeling in the last step.
Step 5: 3D Print Your Parts
Now it's time to 3D print your parts. Make sure that you print two chassis and 8 wheels so that you end up with two race opponents!
Print the CHASSIS at: 75% fillwith supports and the WHEELS at: 30-35% fillwith supports as optional.
*I didn't print with rafts for either the chassis or the wheels.
- Use a chisel to carefully remove the printed parts from the print bed.
And then this is where the needle nose pliers come in! Use the pliers to carefully remove the supports from the chassis.
HINT: It's the most fun when you print each set of wheels in a unique color!
If you've never 3D printed before, read through Lessons 3 & 4 of my co-worker JON-A-TRON's free Easy 3D Printing class. He takes you step-by-step through the process of slicing and printing. Yay JON-A-TRON!
Step 6: Assembling Your Racers
Now that you've 3D printed all your parts – or had them printed and mailed to you – it's time to put all the parts together!
Pssst... We're getting sooo close to race-ability!
BUILDING THE RACERS
- Go through the rubber band bag and pick out 16 of the small red bands. (When they are pressed flat in half, they will be about 1 7/8" (47.62 mm) long.)
- Unpack your 8 skateboard wheel bearings.
- Press fit the bearings into the hole in the center of the wheels.
- Make sure they are all the way in, until they are hitting the small stop we added.
- Add one bearing to each of the 8 wheels.
Now it's time to add the traction to the wheels, aka the rubber bands! Each wheel gets two rubber bands that will follow the indented 'track' guides we added to the model.
- Pre-stretch each band.
- Put two bands on each wheel that line up with the tracks.
They will look something like this!
NOTE: Hold onto your bag of rubber bands, as rubber bands tend to age (ie: crack) over time and you may need to replace them at some point down the road.
The wheel bearings are designed to press fit securely onto the chassis.
- Gently, but firmly press a wheel onto each 'axle' end of the two chassis. The bearing stop side of each wheel should face the body of the chassis.
*Make sure the the bearing of each wheel is flush up against the stops on the chassis, like pictured above.
Ta da! You should now have two completed racers!
ATTACHING THE OBJECTS
Once you've decided on the objects that you will be using as the body of the racers, place their approximate point of center of gravity in the center of the chassis.
HINT: The circle cut out of the chassis cradle is the center of the racer.
- Sort through the bag of rubber bands and find two that are long enough to hold the object snugly in place without being too tight, as to damage the object.
- Holding the object in place with your non-dominant hand, use your other hand to loop one end of the rubber band around one of the 'hooks'.
- Stretch the band across the object and loop the other end of the band around the hook on the mirrored opposite side.
- Repeat for the other rubber band and two remaining hooks.
TIP: To best secure smaller or round objects like the orange above, hook the rubber band to opposing diagonal hooks (like the lemon car above).
Step 7: Exploring the Science of Physical Mechanics
The last thing left to do is use your sweet new cars to prove some scientific theory!
TIP: Building a small ramp to 'release' start the races on will keep the force consistent for each car, allowing for proper baseline science-ness comparisons.
OR just challenge your friends to some too fast, too furious broccoli drag races. :D
Have fun friends, and PLEASE post photos of the racers you make in the comments section so I can ooohh and aahhhh. :D
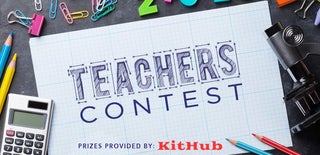
Participated in the
Teachers Contest 2017
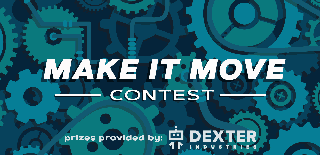
Participated in the
Make It Move Contest 2017