Introduction: 3D Printer Made Out of Beech Threshold
I have always been a fan of the Prusa i3. I love the design and simplicity. It is a great 3d printer for beginners because it is not too complicated to put together and it has a wide range of materials that you can print with. For a long time, I was thinking about how awesome it would be if you could create printed parts of the printer out of wood. So, I did some research and found out that most of the parts need little to no adjustments, to be made out of timber...or just a European beech treshold.
I know about 3D printer designs that use wood, but there aren't many DIY printers which don't use printed parts at all! Why not take this to the next level, and make this project "No printed parts Prusa".
There are three axes to assemble and an extruder when building Prusa MK2. I will go through the MK2 manual step-by-step and check all the printed parts, that I need to cut out of the wood.
Link for the manual:
https://help.prusa3d.com/en/guide/2-y-axis-assembly_79992
To get the dimensions of the parts, I used the official Prusa GitHub.
https://github.com/prusa3d/Original-Prusa-i3/tree/MK2
I also found this 3D model made by Tobias Hansen, he did really good work. I used it to get a better understanding of how parts fit together.
https://grabcad.com/library/prusa-i3-mk2-2
Equipment:
You need something to drill straight holes. A saw that can make straight cuts, and a way to mark your material precisely, for example, calipers. I used these tools:
- Drillpress
- Miter saw
- Tablesaw
- Calipers
But you can get away with using handsaw and chisels if you are careful (and don't mind spending a LOT more time on this).
Supplies
We will need:
- Nema 17 stepper motors
- 3D printer Bed and frame (these can also be made out of wood, but my treshold was not enough material)
- Guiding linear rods (i salvaged them from old broken inkjet printers)
- 2 pcs 320mm
- 2 pcs 330mm
- 2 pcs 370mm
- Threaded rods M8, M10
- 4 pcs M8*220mm
- 2 pcs M10*350mm
- Bunch of M8 and M10 nuts and washers
- Cables for steppers, heated bed, and PSU
- PSU (can be ATX)
- 3D printer electronics - I used old RAMPS 1.4 with Arduino mega
- e3D V6 hot end (I have a cheap clone, with a fan)
I also printed some blueprints, so I don't need to bring my computer to the shop. Most of them are attached in the corresponding chapters of this instructable.
Step 1: Parts We Need for Y-axis Assembly
The y-axis is the one that moves the printbed forward and backward. It has five kinds of 3d printed parts we're gonna make from wood.
- Y-axis-corners
- Four of these form the basic structure of the frame
- Y-idler
- holds the wheel on the opposite side of the
- Y-motor-holder (mount)
- Holds the stepper motor, that moves Y-axis
- Y-belt-holder
- This part is mounted to the Y-carriage, holding the GT2 belt, ensuring it moves when the stepper motor spins.
- PSU-Y-part
- I decided, that this one can be skipped (Yolo)
Step 2: Carving Y-idler
I did the Y-idler part first since it seemed to be the easiest one. The original dimensions of the part weren't that critical, but one was important: the distance between the holes. So I cut a larger part of the doorsill than the resulting piece and drilled the holes. Both with 3mm drill bit and then I enlargened the bigger one with 8mm bit.
I used an old DIY table saw, to make a groove. Since I had the bigger piece, it was much easier to operate during the cut. After the groove was made, I cut it to size with my miter saw.
Btw. you don't need a table saw to make this groove, you can use a handheld router, or just a drill, handsaw, and chisels.
After I finished the part, I put on the idler wheel and tried to place it onto a threaded rod.
I haven't used a blueprint for this one, but I figured it might come in handy if someone wants to replicate this project. So I made a blueprint for you, which you can print on standard A4 paper.
Attachments
Step 3: Jig Drilling Y-axis-corners
This is just a bunch of holes, drilled into a right-sized block. I adjusted the design slightly (but the included blueprint is for the original part, tho) - the holes for the linear guide rods are not a snap-in kind of deal anymore. I instead kept the hole whole and made sure, the parts are not intersecting with Y-carriage, which they don't.
I also left out the grooves for the washers - I just use longer threaded rods.
To make holes uniform on every part, I created a simple jig, by clamping square pieces to my drill press table, which functions as endstops. Fun fact, the doorsill act as a material AND as an end stop here :-).
Attachments
Step 4: Y-motor-holder
This part shares the hole dimensions and even position, with the corners I made previously. So I used the jig to drill the holes into this part as well. The holes I drilled with the jig, are for mounting onto the frame, next I need to find out, how to precisely mark and drill the holes for the Nema17 stepper motor.
I used the tape trick for this. I wrapped the mounting face of the motor with duct tape, punched holes through the tape in matching positions to where the actual screwholes were, took off the tape from the motor, and reattached it to the actual wooden part. The tape then served as a marking of the hole positions.
To make a room for the belt (which would interfere) I cut one-fourth of the part.
Design note: The original y-motor-holder part does not touch the ground (unlike the corners), I think that this is to prevent vibrations from the printer. To make my production easier I decided to keep this section.
Step 5: Sawing Y-belt-holder
Any belt holder part can be two screws screwed into the material - and a GT2 belt zip-tied to these. However, since this project is just a challenge more than anything, I decided to make the Y-belt-holder as similar to the original printed part as possible.
The original Prusa carriage I wanted was not available, so I got a different one. It's not as good as the other one, but it still works well. This carriage doesn't countersink the lmu8 bearings and because of that, the bed is a little bit higher which means that it doesn't interfere with my taller corners.
I first drilled the screwholes with an m3 drill bit - the design of my belt holder involved using these screws to wrap the GT2 belt around them instead of printed plastics. I used a Forstner bit to drill a 12mm deep hole into the part. I then followed this by cutting out a groove for the belt using my table saw.
To make the whole thing more sturdy, I made something like a cap (just a block of wood), it also serves a purpose as a place for screws to rest on (on the photo yet to be drilled)
Beware! This next blueprint is adjusted to my taller bed settings.
Attachments
Step 6: Y Axis Assembly
As I mentioned, I do not have the original Prusa carriage, the one I have comes with printed holders for linear bearings. Since I don't want to use printed parts, I installed my 8mm linear bearings with zip-ties and removed the included prints.
Step 7: X-axis Parts Requirements
There are only three parts, that we need for X-axis build.
- X-end-motor
- X-end-idler
- X-carriage
But boy, oh boy, it was not easy. There was a lot of trial and error. It's clear from these parts that they were designed to be 3D printed. For other types of manufacture, we'll have to invest a lot of time and effort and make our version of them.
How are we gonna do that? Let's start with a quick analysis.
We can say, that parts starting with X-end have multiple purposes:
- Handling GT2 belt for the extruder
- X-end-motor holds the stepper for moving the printer head with a plastics extruder
- X-end-idler as the name suggests holds the idler, just like Y-idler we built
- Holding X-axis linear guides
- Sliding on a Z-axis
- These X-parts hold another set of linear bearings which slide on Z-axis guides
- For the printer to be able to move Z-axis, trapezoid nuts are built into the X-end parts.
To make the whole build process a lot easier I decided to split mentioned parts by functionality onto more manageable pieces. Each X-end part will consist of two...
Step 8: X-axis-Z-holder
This is the first of the two and It's my original design, for a change. Its job is to hold onto the trapezoid screw and guide rail of the Z-axis. It's a component and can be used for both sides. The large flat side will be then screwed and glued onto parts responsible for the X-axis. I made two of these, one for X-end-motor, the second for X-end-idler.
It's a block of wood with two holes, one for the trap screw and one for the bearings. I first predrilled both of them with an M10 drill (trap screw fits into the M10). Then I used the M15 Forstner bit for the bearings pocket. I didn't drill all the way through. This way the bearings won't fall through, but the rail can go in, thanks to the predrilled hole. To drill M15 to the exact same location as the M10, I used the clamping jig again.
To hold bearings in place, I cut the block from the side and drilled M3 holes for clamping screws. When tightened, wood clamps the bearings in place.
Sliding on a Z-axis... ✓ done
Attachments
Step 9: X-end-motor Build and Completion
We need holes for the stepper motor mount and the linear guides. On top of all of that, we need a groove for the belt! This groove is actually a hole in the original design, but since we are building X-end-motor from two parts anyway, we can groove this side, and then glue them (X-axis-Z-holder, and X-end-motor) together.
Holes for the motor mount were made with the tape method, mentioned earlier. Drilling for the linear guides was quite dramatic (since it was drilling from the tallest side) and I clamped the part with another block of wood, to ensure the guide holes won't be drilled crooked.
Sadly it is quite hard to find dado blades in Europe, so I had to make the groove by multiple passes on a table saw (there was no router table available).
To mount the X-end motor onto the X-axis-Z-holder, I reused Nema 17 mounting holes and drilled these as clamping holes in the Z-holder. This way I can get away with less used screws. Now we have our X-end-motor completed!
Attachments
Step 10: X-end-idler Completion
First, I drilled holes for the linear guides. I again utilized the same clamping as for the X-end motor. This part uses my custom Z-axis holder as well and should have a groove just like the X-end motor. But unlike with the X-end motor, this groove does not need to be all the way through. I tried to cut it halfway with the table saw and clean it up with a handheld router, but it ended up a bit rough. The dimensions are spot on tho.
The space left off by the groove was put to use for holes, which are to accommodate the Z-axis holder. Thanks to the roughness of the surface, I will need to use more than one washer with the idler wheel, against the wooden wall.
- Handling GT2 belt for the extruder...✓ done
- X-axis linear guides...✓ done
Attachments
Step 11: X-carriage
The carriage serves two purposes
- It holds the X-axis bearings
- Holds a GT2 belt.
And It's of course foundation for the hot end and extruder stepper motor. I went for the easiest design possible, which means block with two grooves for the bearings.
I started making grooves with my table saw, but I ended up cutting them too tight. This must've made it so the bearings wouldn't fit. Instead of cutting them larger, I decided to tilt the blade and made a kind of dovetail groove, which made bearings fit snugly. They were in there so tight, I have to persuade them with a hammer :D. After that, I did not even need zip ties, to hold them in place.
During the assembly I drilled some extra holes, to mount the extruder motor and made grooves for the GT2 belt, which I was not sure, where it will end :D.
Attachments
Step 12: What Do We Need for Z-axis?
Compared to the previous X-axis, this one is a breeze. There are only two types of printed parts:
- Z-axis-top
- This one holds a smooth linear rod for the Z-axis and has a hole for the trapezoidal lead screw to live in.
- Z-axis-bottom
- Holds stepper for the lead screws and another end of the guide rod.
There are two pairs of each of these, mirrored for each side.
Those mentioned parts fit into the Z-axis frame, which we also need to get somehow...
Step 13: Z-axis Frame
I first tried to cut the Z-axis frame from OSB, and yes I was inspired by Thomas Sanladerer and his cheapest possible Prusa printer build. On the link, you can find plans for the Z-axis frame and his take on the printer build. But the OSB version was only to try out how to cut the part - I still planned to cut this from the beech threshold. I first drilled corners of the inner circle and the section that mounts onto the Y-axis frame. The inner square of the frame was plunge cut with my table saw. Minor details were shaped with a rasp. I was also able to paint it black (since I couldn't find the red door :-) ).
My original plan was to cut a version of this frame from the beech threshold, but since I had messed up some of the parts, I didn't have enough material for the z-axis frame. This was one of the low points of this project. To be still able to participate in one board challenge, I found used the original Prusa MK2 frame online and I used it for this project. I also bought some vinyl wrap and with help of my trusty heat gun, I wrapped the aluminum frame, to match the theme of this printer. I even resticked the original warning sticker, to the wood vinyl.
Step 14: Drill All Z-axis Parts at Once!
Rather than using a fancy, Z-axis-bottom design meant for 3D printing, I used just blocks of wood.
All of the Z-axis parts have two main holes. One for the guide rail and one for the leadscrew. The motor parts also have mounting holes for Nema17 motors, which is the perfect opportunity to use our tape trick again ;-D.
Drilling the main holes was easy because I had to set up my drilling jig only once (the jig was with two end stops). Holes on all four parts are the same distance, and I drilled them on the same-sized wooden blocks.
Although the jig was the same during the whole drilling process, I had to change drill bits quite a lot. I first predrilled both holes with the M8 (guide rods are 8mm), then I geared up to the M20 Forstner bit. The last touch on these holes was M22 Forstner two millimeter drilling on the larger hole of the motor part (so the stepper motor lip will fit).
Step 15: Extruder
This is the part, that is responsible for melting the plastics and extruding (hence the name) them from the nozzle. The so-called hot end, (the shiny part, which looks like a radiator), is responsible for the melting. The plastics also need to be pushed through, and that's what the extruder stepper motor is for.
It would make complete sense, to make extruder Bowden type (stepper motor sitting outside the moving extruder part). The wood is quite heavy, opposed to plastic (the lighter the better, faster), but you know, I want to have it as similar to the original as possible, so I stuck to the original design even in this case.
The original Prusa mk2 design extruder is split into several pieces.
- Body
- Holds the extruder stepper which feeds a filament into the hot end, and holds the hot end.
- Idler
- Applies pressure to the filament, so it can be moved by stepper, towards the hot end.
- Body cover
- covers hot end, provides mounting holes for fans
Yet again, I had to make a couple of changes to the design before I built it out of wood. First, my wooden body will only take care of holding the stepper. There will be another wooden part, responsible only for clamping the hot end. The probe and the fan will be hacked into the extruder body somehow, sometime later.
Step 16: Hot End Clamp
As you might already know, I like to start from the easiest. This one was supposed to be the case. But let me correct - that one was the easiest if I hadn't messed up a bit.
For this clamp, to be able to hold the hot end, it needs a hole with three sections, 16mm sections at the edges, and 12mm in between. To do that, I first drilled the M3 pilot hole, then again switched to Forstner bits. Both sides with 16mm and the rest of the material in between with 12mm bit. Now the part where I messed up, to get hotend in, I had to cut clamp in half. I should've cut it first, clamp it together and drill at the seam. The Kerf was too wide, even tho I cut it on the bandsaw with a narrow blade. It's not the end of the world, I can fix it by gluing in some offcut material or using washers in between the pieces.
Attachments
Step 17: Extruder Body
Drilling holes for NEMA 17 stepper is always a pain, even with the tape trick, but in this case, it went rather well. But before I drilled the main shaft hole for the stepper, I first drilled a hole for the filament. It goes from the top and I had to buy a new bit, that was long enough.
The hole for the filament was first drilled with 2mm bit (filament is usually 1.75mm) and then with 4mm bit, with a few millimeters offset, from the original hole. This way, I can feed the PTFE tube into the hole and it will meet the 2mm taper and won't go any further.
After that I drilled two intersecting holes, I had to use another piece of wood with a hole, as a guide, to prevent the drill bit from wandering into the first hole.
The part was almost complete, so I could cut out almost a quarter of it, so I will make space for the extruder idler.
Attachments
Step 18: Extruder Idler
My extruder idler holds two 8mm bearings and since they have chamfer at the edge, together they make great grooved bearing to tension the filament. There were two iterations in making of this part, at first I for whatever reason decided to drill small holes of the idler at the end so I cracked the part. Drill small holes first! :-)
After drilling the small holes, I took an 8mm drill bit and drilled perpendicularly, to make room for the bearings. Then the L shape could be sawed.
This part mounts to one of the stepper motor mounting holes.
Btw. plans for this part look different, they are for the second version of a tensioner.
Attachments
Step 19: Assembly
Since we have all the parts we need, we can step forward and try to assemble the whole thing. Most of the parts have the same instructions as the original Prusa manual, but there were still some problems and differences against the manual that needs to be addressed.
The first thing that differs from the manual is the Z-axis stepper motors. I didn't have the fancy motors with integrated leadscrew, so I had to use cheap NEMA 17s with coupler, 5mm to 8mm coupler to be precise.
The second issue arose, when I fully build the Y-axis, It seemed like there is plenty of clearance between the Y-carriage and Y-axis-corners (the blocks I cut as the second part of this build), but there was not. There were extra ~2mm which prevented free movement of the bed. Since the build of the Y-axis took a large amount of time, to build it square, I instantly rejected the thought of taking it apart again. I instead build some LMU8 holders out of the threshold offcuts. It's just a block with a V-shaped groove. Those risers provided enough clearance and ensured free movement of the bed.
In the case of the extruder, which was more or less custom-built, it was a matter of fastening the extruder body onto the X-carriage. I drilled (again) NEMA 17 holes into the X-carriage and put screws through X-carriage and extruder body, so they screwed into the extruder motor. I mounted the hotend holder just under the extruder body, so I could feed the PTFE tube sticking out of the hot-end to the predrilled bottom section of the body. This way, the filament won't get stuck between body and hotend.
Step 20: Electronics
For electronics I have used what I had laying around ever since I wanted to build 3D printer by myself (which is like 8 years ago). The main board is good (...ahem...) old RAMPs v1.4, with A4988 stepper drivers and the power supply is old 200w ITX computer PSU. The electronics part of this build could be whole new instructable, but luckily there already are couple of good ones.
Step 21: Finished!
Yay! We did it! It doesn't print extra fast or extra pretty, but I am still extremely pleased that It is possible to create a 3D printer without extra precision tools, and from the door threshold! The next logical step would be to treat the wood with some epoxy, to prevent warping under the heat, or some other kind of varnish.
It was not THAT hard after all, and since half of the work (blueprints) is completed, you can easily make your own! How about with different materials (aluminum?).
In any case, thanks for reading this Instructable I hope you like it!
Cheers
Kudlas
P.S.: I will try to add some video with printing, later.
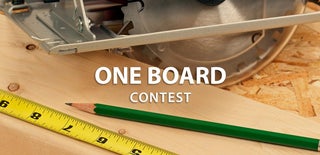
Participated in the
One Board Contest