Introduction: 3D Printed Hat Graphics
I recently saw Becky and Noe, creators over at Adafruit, do a video where they 3D printed custom hat graphics on their 3D Printing Thursday show. As a fan of customizing things to suit my needs this custom had graphic was something I was excited to try. At the end of their video they mention ways to explore this idea more by including lights. Here's how I made custom hat printouts based on their design.
Let everyone know how your roll, with custom hat graphics from your 3D printer!
Ready? Let's make!
Step 1: 123D Design
123D Design is a free and super easy to use 3D modelling program. The best part about 123D for hat graphics is that it has a text function which will make our name graphic really simple to make and modify.
Once installed you can store your models online so you can access them from anywhere.
The interface is similar to other 3D modelling software, and employs the use of your secondary mouse button to navigate the project area. (right-button on 2-button mice).
Step 2: 123D - Add Text
Open 123D and start a new project.
On the top toolbar there's a text tool, represented by a capital "T". Click this, then click on your project area to place the writing cursor.
A new text window will open where you can edit the text to spell out your word. You need to change the text in the window before the word will show up on the project area. You can choose the font you want from a large list, it's all the fonts loaded from your computer. Some may not appear in the 123D interface.
For my letters, I chose a blocky font with a height of about 50mm.
Step 3: 123D - Extrude Text
Once your text is written out we can extrude the letters to build up their height.
Highlight the text on the project area. From the top toolbar find the construct icon, then click on the extrude. An arrow will appear over your text which you can grab and pull. You can also enter in a value for the extrusion height. For mine I chose 4mm.
Step 4: 123D - Move Letters
Navigate your view somewhere above the extruded letters, looking down at the text.
Drag a window around one of the letters, from the toolbar that appears on the bottom chose the move command.
Use the arrows that appear over the highlighted selection to move the letters closer together, overlapping slightly i\to provide stability in the printout.
Step 5: 123D - Delete Reference Text
Once the letters are in the right position we can click the reference text we typed earlier to highlight it, then delete the reference text.
Take a moment now to navigate around your lettering to make sure things look the way you want.
Step 6: 123D - Sewing Wedge Part 1
To sew this printout there needs to be small openings that will allow a needle and thread. To make this we'll use a a the box and cylinderprimitives to create an extruded wedge shape with two pegs underneath; this will be the shape we use to subtract from the lettering to make the sewing channel.
Drop a box onto the scene from the primatives toolbar on the top.
To resize the box start by highlighting the primitive, then click on one surface, this will display a small gear icon which will allow you to modify that property of the model. Click the press/pull and move the surface down which will squish the model. Using the same technique you can resize the box to a small rectangle shape.
Copy this shape and paste a copy next to the original, rotate the copy about a 60 degrees along its long axis. Move the tilted copy over the original to overlap over one of the long edges.
To subtract two models click the combine icon from the top toolbar and then click subtract. Select the model that you wish to remain first, then click the rotated copy to indicate this is the shape you wish to subtract. Press enter to accept and you should be left with a wedge shape extrusion.
Step 7: 123D - Sewing Wedge Part 2
Drop a new primative into the scene, make this one a cylinder.
Click the cylinder, from the bottom toolbar click the scale icon. Drag the arrow on the model to scale it down. We'll use the small cylinder as one of the legs for under the model. These legs will allow the needle and thread to pass through and secure the graphic to your hat.
Click the cylinder model and move it underneath the wedge extrusion. Copy and paste the cylinder to make a duplicate and move it to the other side of the wedge extrusion.
From the top toolbar click the combine icon and merge. Click the wedge extrusion and both cylinders, then click enter to accept the merge.
This combined model will be the wedge shape we subtract from each letter to make an opening for sewing.
Step 8: 123D - Subtract Sewing Wedge
Move the wedge near a flat portion of your lettering. This wedge model will be subtracted from the lettering to make an opening with thread can pass through. Depending on how big you made the wedge, and the font you used, you can conceal these wedge subtractions in some inconspicuous places on your model, making the subtractions less noticeable.
Since you lose the subtraction always copy and paste a new wedge from the original.
Click the wedge model copy and move it into a flat section of the lettering, with the legs poking through the underside of the letters and the square back of the wedge are poking out the back. From the top toolbar click combine then subtract. Click the letter first, and then click the wedge copy and enter to accept. You should be left with an channel opening with two holes in the underside.
If your subtraction is not what you wanted you can undo and push/pull some sides of the wedge model to get the profile you need. Then go back and try to subtract the wedge shape again.
Step 9: 123D - Export
I made 2-3 wedge subtractions for my hat. Once I was happy with the placement I could drag a window around the letters and from the bottom toolbar click the export selection.
Save the file as an STL.
You can download my model with the wedge below in STL and 123D or you can find it online here, and some different designs I did with font here.
Step 10: Print Model
With the STL model saved the model can be printed. As to twist to the original idea I experimented with glow in the dark filament, and illuminating a hat with LED behind.
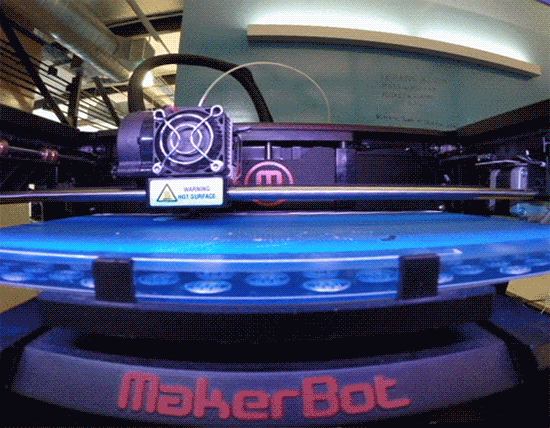
Though I used a Makerbot, my new printer is a Creality 3D printer, which is inexpensive and a workhorse of a printer.
Step 11: Clean Model
After printing you may have to clean your model of any support structure. I used a sharp hobby knife to clean up the edges and give a nice crisp design. Take a look at the sewing channels and ensure there's a clear path for you to sew through.
Step 12: Heat Bend Model
Put a small saucepan of water to boil, then reduce heat to a low boil. Using tongs put the model into the scalding water for about a minute, then use the tongs to remove the model and bend it to the profile of your hat.
The model will be very hot, maybe too hot, try wrapping the hot model in a cloth to insulate your hands before banding.
Repeat placing models into the hot tub to warm them up and bend.
Step 13: Sew Graphic Into Hat
After bending the graphics they can be sewn into the hat.
The trick is to use a thread with 2 needles, threading the needles through each opening in the letter channel. Once the needles have been passed through the holes in each channel they can be tired off from inside the hat.
Step 14: LED Graphics - Sanding and Installing LED's
I also tried making a illuminated hat with LED behind the letters, I think it looks like a marquee.
I lowered the profile on each LED by sanding opposing sides down as close as i could to the cathode/anode inside the plastic LED. I used hot glue to secure the flat face of the LED to the backside of the model, bending the leads upwards and away from the model.
Step 15: LED Graphics - Wiring
The LED leads were clipped and I wired up 3-4 LEDs in parallel. I also too the time to install a switch into the side of the cap to control the LEDs.
Step 16: LED Graphics - Installing Marquee
To pass the wiring through the cap I punched a small hole through with a small awl. The marquee wires were passed through and wired up to the switch on the side of the cap, then to a few small coin cell batteries.
Step 17: You Be Stylin'
Thanks for the great idea, Becky Stern and Noe Ruiz!
I love the new graphics on my cap, and any time I want to update I can print a new one out in about an hour.
Did you make your own 3D printed graphics? I want to see them!
Happy making :)