Introduction: 3d Printed Electronical Gear Ratio
This project is made for a contest: CNC student design challenge
My school is: Emerson Park Academy
What I have made this project for is to see if I can get a gear to spin fast enough to cause it to generate enough current to keep the first gear spinning I have gone through multiple iterations of this some which have been scratched, sadly I don't have any photos of however I have the refined second iteration still with me (picture 3) however the bearings meant to reduce friction would not spin without resistance.
This was all edited on fusion 360 due to having to change many aspects of the original of someone else's design however the changes i made to the design are in step 1 https://www.thingiverse.com/thing:4727867 - other persons design
Supplies
What I used:
- A 3d printer (Mine was a ender 3 v2 neo)
- Superglue to join some parts together
- Metal rods from a dvd reader and writer or use wooden sticks like in the original thingiverse
- A high torque motor
- A 12 volt brushed motor to produce 12 volts for the motor
Optional:
- Holders for the motor and generator
- Capacitors to make the voltage from the generator more stable and more reliable
- If your generator produces enough current you could hook up some 12 volt fans to cool it
- Charge a battery from the generators power
Step 1: 3d Print the Parts
For this I used fusion 360 to modify the files to allow my metal rods to fit in the holes of the original design along with changing aspects to allow it to support being used electronically. and some parts that didn't fit together well
I did have to change some settings in my slicing software (cura) such as making it do the outside walls first for fitment and accuracy however this makes overhangs worse. The parts were printed with a 20% infill in PLA this gives it some flexibility while still being quick easy and safe to print without a enclosure.
Step 2: Assemble the Parts
Firstly, you attach the files part gear initial and body front which connects to the motor as seen in picture 1
Next, you attach gear connect which has the longer smaller gear to the long pole on the front body shown in picture 2
Thirdly, connect the body middle file to the main gear this is a good time to put the metal rods in and attach to the main object shown in picture 3
Now, the parts, shaft and gear main connect then connect to the rest of the parts making sure the gears all interlock pictures 4 and 5
Lastly, add the back plate to hold it all together and generator it should now look like picture 6 and 7 and spin freely and not seize when the handle is turned however there will be some pressure as it is trying to turn the handle due to the gear ratio
I have added super glue in places to make it stronger
Step 3: Electronics
In photo one these are the items i used to power the project, the high torque motor has enough power to turn the initial gear with my motor running at 100 rpm. This other dc brushed motor can be used as a generator, since its a brushed motor it produces dc voltage however if it was a brushless motor that would produce ac voltage usually 3 phase. The voltage the motors produce is as much as you need to power the motor so if the motor is 12 volts than it will produce 12 volts. you can test this if you have a 3d printer which you need for this project and move the bed back and forward very fast the printer turns on
Since my generator outputs the right voltage all I done was soldier the wires from the generator onto the motor without the need for and ac-dc circuits or resistors just soldier the positive and negative
However i ran into a problem of how to start the motor in the first place. In the end I opted to use a 8 1.5 volt batteries in series to produce 12 volts and 1-2 amps due to high resistance this has enough power to start the motor.
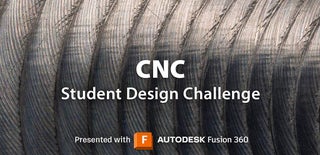
Participated in the
CNC Student Design Challenge