Introduction: 3d Printed Rocket
"Failure is only the opportunity more intelligently to begin again." -Henry Ford
I have done a lot of failing at this project, but as Mr. Ford would say, I have also gotten a lot of intelligence of this subject and designs like this in addition to learning to use tinkercad. I think I finally got the design right though! This whole project started a while ago I tried to 3D print a model rocket with a design someone else made. It was a rocket based on the Estes “Lunabug.” (Link here, I only ever tried to print the full thing at one time) It does not have a parachute and instead relies on a "tumble" recovery system. When I first flew this design, it nosedove back down. “Well, that’s not supposed to happen...” and it’s not, it’s actually quite unsafe because it could hit something or someone. I tried nearly everything I could in my slicer, adjusted infill, changes the fins orientation and size, made the body longer. Nothing worked. (Now mind you, I did not launch every single rocket I have printed, but I did test them with a string for balance, more on that later.) I now have a surplus of unusable rockets. I failed. A lot. But, I was learning too. The rockets may be able to take an engine, but I would not be able to safely recover them. Eventually I just gave up trying to alter the print settings, but this is how I redesigned the rocket in a way that it won’t nosedive into whatever is below it. My goals are simple:
- Have a fully functional, 3d printable rocket (excluding the motor)
- Be able to recover it safely, ie tumble recovery rather than nose dive
- Do minimal gluing or cutting after I print it
- Be able to hold an "A", "B", or "C" engine (all of which are the same size)
Disclaimer: I will not be held responsible for any damage caused by this project. It involve 3d printing with a hot nozzle, and sending an object high into the sky, which could harm people, animals or property on its way down.
Supplies
To design the rocket:
- A slicer- I use Cura
- TinkerCad
- A 3D printer (or access to one)-mine is an ender 3 pro
- 3D printer filament - I use hatch box pla
- A few feet of string
- Possibly a knife (be careful)
- Possibly a straw
- Possibly super glue
- Possibly sandpaper
- Possibly a putty (or something similar like chewing gum)
To actually fly your rocket:
- A battery, the minimum you can use is a 9v, I use a 12v motorcycle battery
- Rocket engines and igniters, you can find these at hobby lobby (and other stores I imagine, I have only ever bought them at hobby lobby though)
- A launch pad and launch controller (The controller is basically just a switch with a safety built in, and the launch pad is basically an 1/8 inch rod that has a deflector shield at the bottom. You could probably replicate the deflector with a pie tin)
Step 1: Things I Learned From This Project
About TinkerCad:
- Unless you absolutely have to, leave the snap grid as big as you can. Only change the size if you absolutely need to. If you do end up having tho change it, change it back as soon as you can.
- When you need a hollow cylinder, use a tube, don't fill a cylinder with "hole"
About my Ender 3:
- Check the Z axis often, I failed several prints because my Z axis motor was loose up against the printer
- In addition to checking the Z axis motor, check the coupler that goes to the incline plane for the z axis, this can also become loose.
Step 2: Getting Started: Basic Rocket Science
In the introduction I said that I did not launch every single rocket I printed for the design I found on thingiverse. This is absolutely true, in fact I only ever flew one. There is a way to test a rocket's stability without actually flying it. It works like this:
- Find the point around which the rocket balances (called the center of mass).
- Tie a string around the rocket at this point (if there is not a hole so that you can try a string, you may need to drill a small hole).
- Hold the long end of the string, and twirl the rocket over your head like you are a cowboy with a lasso.
- If the rocket stays straight for the most part (other than a little wobbling) it is balanced correctly. If it does not stay straight and is very wobbly, it will not fly properly and the balance needs to be adjusted.
- Science: If the center of pressure (center of all surface area on the rocket) is in front of the center of mass, the rocket will be unstable. This is what we are trying to achieve with our rocket as it falls/tumbles during recovery.
I decided have the nosecone come off at the apogee when the ejection charge fires, because the nosecone has a lot of mass and it is in the front. The spent engine adds mass to the back, moving the center of mass, so it is probably a good idea to leave the engine in. This could be done with an engine clip, but before adding one to the design, I am going to try it without the engine in the rocket for recovery. I found after testing my design that as long as the nosecone came off, the rocket would tumble for recovery.
The goal for a rocket using a tumble recovery system is to have it be balanced on its way up, and unstable (ie tumble) on its way down. There are several ways to accomplish this but I am going to have it fly up and the at its apogee (its highest point) when the ejection charge fires, have the nosecone pop off. This means it will need to be printed in two pieces, the nosecone and body. For more info on balance see this link.
Step 3: Designing the Body Tube
Originally I used two cylinders to make the body tube. One was solid the other was hollow. Eventually I realized this was not ideal because I could not adjust the wall thickness. After realizing this, I switched over a "tube" for the body. I needed to make it able to hold a rocket engine, with a little bit of wiggle room (I found that 0.4mm works well, you may see differently though and decide to have more wiggle room for your rocket. I will say that the engine was snug in the body tube). I also wanted it to be thin, but not too thin (the thinnest my printer will print is 0.4mm so I decided to go up to 0.5mm for wall thickness. The print was a little fragile, but it held up to the flight well). I am going to use an "A, B, or C" (which are the same size) rocket engine. They have an outer diameter of ~17.6mm. So the outer Diameter for the body tube will be 19mm (17.6 + 0.4 + 1 [engine diameter + wiggle room + (wall thickness x 0.5) = outer diameter]). In case you are wondering, the reason we need to double the wall thickness is that there are two sides on this wall. I made the mistake of overlooking this in one of my test prints, and it did not fit because it was too small.
Inside the body tube approximately 10mm down from the top, I installed a ring to keep the engine from shooting out the top of the tube. It is 2 mm thick so that it doesn't break and prints well, I measured the outer paper layer of the rocket engine (the part which holds it and stays in tact). It is about 2.5 mm thick, so just to be safe I made the wall thickness on this section of tube 3mm. I needed the gas from the ejection charge to be able to get through though, that's why I chose to use a tube (because I needed the hole in the center) rather than a cylinder.
Attachments
Step 4: Designing the Nosecone
After a few prints I decided to have the nosecone sit over/on top of the body rather than inside it. This improves the aerodynamics so that the nosecone will break all of the wind and air rather than having the air go around the nosecone and run into the body. To create the nosecone I just used a tube with a wall thickness of 2mm and is about 16mm tall. To have a rounded top I added a paraboloid which is 20mm tall. Both shapes have the same diameter (more on the diameter later). The paraboloid sits on top of the tube so that the tube can fit over the body. I want the fit to be snug so that it is secure on the body, but not too snug to a point where it will not come out. I mentioned before about my test which showed that an extra 0.4mm in diameter is a pretty good amount of wiggle room (if you make a spin off of the design, which I encourage you to, you may want more wiggle room for the nosecone because mine was very snug).
So, the inner diameter of the nosecone tube needs to be 0.4mm greater than the outer diameter of the body tube. Which means that the inner diameter (of the nosecone)needs to be 18mm because the outer diameter of the body tube is 17.6mm. If the inner diameter of the nosecone is 18mm and I want 0.5mm of a wall on both sides then we need to have an outer diameter (for the nosecone) of 19mm.
Attachments
Step 5: Designing the Fins
For the fins, I used a "round roof" flipped on its side, then duplicated it and made the second one "hole." I moved them together into a position that looked cool. I also was trying to get it to be pretty aerodynamic and have a straight edge so that I could attach it to the rocket body tube.
I duplicated another one of the fins and shrank it. It was also a hole. If you need to have less surface area (move the center of pressure forward) you can change how hollow the fins are. I ran into a problem with the fins after I had put the rocket together. (eventually I had to abandon the cutouts in the fins because of an issue I was having. I don't think they caused the issue, but I never added the cutouts back in.
In Cura, the fins had a lot of excess stuff (I don't know how it got there) that would not go away and should not have been part of the design. I don't know for sure what I did to get it to go away (it may have had something to do with something I did with the fins), but I think I fixed it when I went back into the fins and made the layer of "hole" in the "round roof" much thicker. I took the cut out part out of the fins at this point and did not put them back in.
I also leveled off the bottom of the fins rather than have them curve to a point. I did this so that I would have more surface area on the bottom of the fin so that I had better bed adhesion and so that the fins would not fall over during printing. I decided to thicken the fins after my first print because they not hold up well to the print as a result of some stringing and getting hit buy the extruder. I thickened them to 1.3mm. They still aren't printing perfectly straight, but they work fine, if you have any tips on how to get the fins to print better, please leave a comment to explain how to fix this.
Step 6: Designing the Launch Lug
The launch Lug was pretty simple to design, it was an oval that measured 5mm by 5.5mm (on the outside). On one of the sides (the 5.5mm side) was a box that was "hole" to open one side up. The wall thickness of the main tube in the launch lug was 0.4mm. The end that was left open just sits up against the rocket. This piece is very important because it will be the piece that holds the rocket on the launch pad, and makes sure it goes up, rather than somewhere else. If I can't get the launch lug to print, I will take a section of a straw and glue it to the side of the body tube. Sorry I don't have a picture of that, but i think if you look at the rocket design where the launch lug is, you will understand what I mean.
Attachments
Step 7: Putting It All Together
In TinkerCad before you download the file, put the parts together. If you chose to use 3 fins like me, they should be 120 degrees around the rocket from each other. They should also be on the outside of the body tube. The launch lug should be placed either up against a fin, or opposite one of them. The nosecone should be printed by itself, NOT on top of the body tube. You will probably have to adjust the snap grid down (I changed mine to 0.25mm) to place the fins correctly.
When you put it together, it is important that the bottom of the body tube is touching the fins. Even being off by 0.5mm here can mess up your print. Originally, I did not have it like this and it caused stringing and unnecessary extrusion of filament (it is hard to extrude something on nothing) which connected with the fins, however this was bad because the extruder would hit the excess filament and knock it over. Moving the fins from their original position and making them useless. Also make sure the fins are all the way up against the body tube.
Step 8: Printing the Pieces
Once you have your design ready, slice it! We are almost there, I can almost smell the burning sulphur fro the engine. All we have left is to print, balance and fly! Now upload the file to your printer. I created a profile for this project in Cura because of the amount of printing I have done with it. For right now my settings are:
- Infill-20%
- Quality-Super Quality-12mm
- Raft for bed adhesion on the body, skirt on the nosecone(to save filament) [I have tried the body with a skirt, but the fins don't stick well enough to the bed, nor do they have enough support, so I decided to move to a raft. I tried adding a raft to the one with point fins, but it won't work for me (it may be because the fins are points) with no luck, so I decided to leave that one as is.]
- And I am printing in PLA
I think those are all the settings you need. If you decide to use the Flat Fin body, you can use the attached ".gcode" file. the nosecone should work for both the "point" and "flat" fin bodies. You will need to print both the nosecone and the body. I decided to separate them while I was experimenting with the file so that I could save filament by printing one at a time.
Step 9: After Printing
After your rocket prints there may be a few changes you need to make for example:
- You may need to trim off excess filament from the bottom of the body to allow the engine a clearer way to go in and a clearer fit. You want your engine to fill most of the hole with a little room for getting it in and out. It may be difficult to get the engine in if there was stringing at the bottom of the body tubes opening.
- Glue a section of a straw where the launch lug should have been. This will be necessary if your printer (like mine) did not print the launch lug. I know it would be difficult to print as it is hard to print something on nothing.
- Drill small Holes in the fins around the center of mass to be able to test the rocket's balance.
- You also may need to hollow out the part in the body that is designed to hold the engine in. Mine did not print perfectly, and the hole was partially covered. Be careful when you do this, the body is very fragile and might break. The piece that holds the engine in also might break and it is one of the most important pieces in the rocket. Be very careful.
Step 10: Testing Your Rocket
Before you fly your Rocket, You will need to follow the procedure explained in step 2.
- Tie a string around the center of mass in the rocket
- Spin it around your head like a cowboy with a lasso
If it flies straight with a nosecone on and an unused engine, and tumbles without a nosecone and a spent engine/no engine, then you are ready to go. For more information on this, this link has good information about balancing a rocket.
If it does not stay straight with the nosecone and an unused engine, there are a few things you can do. To have it straight, the center of mass needs to be in front of the center of pressure. If the rocket is not straight, you need to add mass to the top of the rocket (ie the nosecone). This is where you can put putty (or gum if you are in a hurry) in the nosecone. the other thing you can do if you have more time or want to print the nosecone again is add more infill to the nosecone, this also adds mass to the front. You could also go back into the design and start taking cutouts of the fins. I would recommend trying to add mass to the nosecone first though
To fly your rocket:
Before launching your rocket: Make sure you are a safe distance away and that there are no people wandering near your rocket. These can be dangerous. Also make sure you are in an open area and that your rocket will not get caught on anything.
- Put your rocket on the launch pad
- Load an engine into your body tube
- Stick an igniter into the hole in the back of the engine
- Put a plug in the hole to hold the igniter in
- Attach the leads from your Launch controller to the igniter
- Connect power to the Launch controller
- Give a countdown and
- Launch your rocket!
Step 11: In Closing
Thank you for reading this far. In this instructable, we have only scratched the surface of how the amazing machines called rockets work. If you are interested in rockets and want to learn more about the science behind how they work, this link should help you get started.
This link/guide served as a guide for me as I got started with rockets. It is a good starter guide and explanation of concepts like Newtons laws of motion that are applicable to rockets, and how rockets work.
If you still want to learn more I would recommend searching something like "how do rockets work?" there are a lot of excellent guides out there. I hope I have helped you get started with rockets and have fun. I want to circle on my three main goals from the beginning of this instructable. They were:
- Have a fully functional, 3d printable rocket (excluding the motor)
- Be able to recover it safely, ie tumble recovery rather than nose dive
- Do minimal gluing or cutting after printing
The rocket I designed is fully functional, you can actually launch it. I successfully launched one of these rockets twice. After the first launch, the top of the body tube had melted a little and was slightly misshapen, but the nosecone fit on the top, so I was able to fly it again.
It is safely recoverable. I have seen several model rockets before which come down nose first. A nosedive is dangerous for recovery because it puts people or animals which are on the in danger of being hit and injured (or killed). That is why it is very important the rocket is balanced correctly.
There is minimal cutting and gluing involved.
And I was able to fly this rocket with an "A" and "B" engine. (I didn't get to try it with a "C")
It took several tries and lots of experimentation for me, and I hope you have learned from my mistakes, and failures. However, whenever you decide to experiment with something, remember that you are experimenting when you experiment you will mess up. Fail. We should learn from our failures, not despise them. Failure brings us closer to our goal. Henry Ford put it best "Failure is only the opportunity more intelligently to begin again."
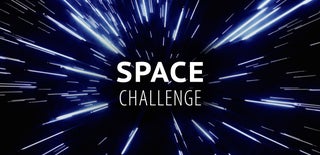
Participated in the
Space Challenge