Introduction: 7 1/2 Gauge Rideable Flat Train Car
My name is Jacob Nord, I am 15 years old and I live in Klamath Falls, Oregon. I am in 9th grade and home-schooled.
As of the middle of June 2022, I have gotten into rideable model trains, it is a very expensive hobby to get into, but if you build your own equipment it makes it more affordable.
For this contest entry, it is a step-by-step instructable/process of how I built this train car; and you could give it a try if you have the right materials.
I haven't been able to pull it on the rails yet because the locomotive is still being built... slowly. Also, we haven't been able to get ahold of some couplers yet, but a draw-bar could be used until then.
I used Tinkercad for most of the picture/presentation because it's easier to do so than to do it in real time as the project is being built because, it's a hot, and dirty process. So taking pictures was difficult when in the middle of the process of building. With screenshots, it should be easier to see small details, rather than pictures.
Above I put a short video that will give you a little idea of what this hobby is about. At the bottom of this instructable, I put the full/whole version of this video. So please check that out!
Train Car
Supplies
Power Tools:
- Angle grinder, with abrasive blade and a polish/sanding blade.
- Metal chop saw
- Sawzall, with metal cutting blade.
- Lincoln wire welder
- Miller stick welder 225v
- Metal band saw
- Wood chop saw
- Drill
- Drill press
- Tabletop grinder
Hand Tools:
- Hacksaw
- File
- Sandpaper
- Ratchet
- Brush
- Clamps
- Square
- Tape measure
Materials for the Build:
- 4'' wide x 1/8th'' thick x 89.5'' long Metal Bar stock (2x)
- 2.5" wide x 1/8th" thick x 15.25" long Metal Bar stock (2x)
- 1" wide x 1" thick x 15.25" long Metal Square tubing (7x)
- 1" wide x 2" thick x 89.25" long Metal Square tubing
- 1" wide x 2" thick x 2.5" long Metal Square tubing (4x)
- 1.5" wide x 89" thick Metal Angle Stock (2x)
- Plywood for Wooden deck
- 11" wide x15" thick x 20.5" long Wooden cargo boxes (2x)
- wood stain
- wood sealer
- red and black spray paint primer
Step 1: Building the Framework
After the angle iron is cut to 89'', then two pieces of square inch tubing were cut to 15''. Then we laid out the pieces as shown above. I clamped all the pieces, we started to weld but found out it was too hard to weld on the ground, so we built a welding table the next day (Highly recommended!). Make sure all of the pieces are clamped together and clamped down to the table, to prevent warping from the heat of the welding. Once the metal had cooled down, we cut two pieces of 1.5'' angle stock at 5.25'' and clamped it down, then welded them together. (As shown above in the last picture)
Step 2: Installing the ''ribs''
Once the outer frame was constructed, five pieces of 1'' tubing were cut to 15'' and placed 12'' apart. The pieces were clamped together individually then welded together with the outer frame.
Step 3: Installing the ''Bolster Mounts''
Once everything cooled off, two 1''x 2'' tubing pieces where cut to 15''. This was welded into the right location for our purpose, meaning, we built the frame so the trucks ( the set of wheels for a train car) will fit properly. This is basically a beefed up 'rib', this is where the trucks are going to be mounted (this will be shown in the steps ahead).
Step 4: Adding the Spine
After all of the ribs and bolster mounts were installed, we needed a spine that would support a lot of the weight of the load of the car and also is where the coupler will be mounted.
The 1'' x 2'' tubing was cut 89.5'' long, it gives. This gives .25'' on each end of the car. We centered it in the middle of the car (as shown in the pictures above) and welded it down with some sturdy welds. This spine is going to be the main part of the car that is going to be pulled on the most, because it is where the coupler is going to be mounted.
Step 5: Adding the ''fishbelly''
We used two 4'' by 89.5'' flat bar stock on the sides of the car the ''fishbelly'' side supports. There are many styles of ''fishbellies''.
We had the skinny end go all the way to the bolster, then tapered down from there. We used a sawzall to cut these pieces into shape, a heavy-duty jigsaw could do the job. We also had to do some light grinding to achieve the desired shape.
We made the fishbelly extend up .75'' above the deck level, this allows the plywood to slip right in perfectly, and provides protection for the edge of the plywood. (I will address that in the following steps)
On real railroad railcars, the fish belly frame provides an optimal distribution of tension and compression forces from the center of the car to the bolsters. For model cars like this one, it doesn't give it that much extra support, but is scale to the real thing and is visually appealing.
Step 6: Bumper
When you get to this point of the project, you will be thankful when everything is straight and square, because you clamped everything down when welding. The bumper was one of the last major metal outer parts for this project. We used 2.5'' by 15.25'' long flat bar stock, as you can see in the picture above, there was some grinding involved so it could fit properly, the corner edges were ground down to taper nicely to match the side fishbelly.
For a lot of these pieces, minor grinding adjustments are needed so they can fit properly. (unless you have a CNC laser, then everything will fit perfectly!)
Step 7: Finishing the Bolster Mount
We cut four 2'' by 1'' by 2.5'' long tubing and welded them onto the spine, (as shown above). These will vary, depending on the type of truck you use. The truck (the last picture above) has a center pivot mount that is higher than the two ''shoulder nubs'' on the sides by 1/8''. Since the center pivot is higher than the 'shoulder nubs', the car will teeter back and forth as you go down the rails (it is very important to have this movement, because you will de-rail often without this movement, because the rails aren't always perfectly flat and straight.) These two pieces of tubing provide the needed flexible and strong contact between the trucks and the frame of the car.
Step 8: Painting
Underneath, we painted the car with black primer so it would not rust. The sides of the car we painted with flat red primer and decided that it was the right color for the car.
Step 9: Installing the Deck
After all the paint was dry, we measured the inside diameter of the deck location, cut it, fit it, drilled it, then bolted it down. We just used plywood because we had it on hand at the time.
Step 10: Trucks and Couplers
At this point the trucks are ready to be mounted onto the car. Just drill a hole in the middle of the bolster mount, and lightly bolt it down.(do not bolt it down too tight, otherwise it will not be able to pivot/turn on the rails, or teeter freely as it needs to!)
Couplers will be mounted onto the ends of the spine.(we haven't gotten our couplers yet.)
Step 11: Seat Boxes
There are many different ways to build seat boxes. You can have a ''to-scale'' lumber pile, freight boxes etc. We used the cheapest materials we could get ahold of. It looks like a wooden shipping container. As shown in the picture, it has a hinge on the seat so there is extra storage on the car.
After all the wooden components were assembled, we stained the wood, then put a clear wood sealer over it.
Step 12: The Finished Product/Conclusion
It took quite a few days to get this car done but it was a fun project.
Above are some pictures of it on the rails!
I am building a locomotive also, but it is taking a very long time to build, and I haven't been able to get the car on the rails yet, so I had to take the pictures in the shop. Above is a screenshot of my CAD drawing of the locomotive we are trying to build. (shown above) I also will give a link for you to look at the locomotive on Tinkercad...
Down below I put a short video of me driving a friend's train to give you an idea of what it is like to ride these trains.
SW1500 Locomotive
Attachments
Step 13: Where I Ride 7.5 Inch Gauge Model Trains...
An hour north of where we live, is the worlds longest/largest 7.5 inch gauge rideable model train railroad in the world. Last year we were introduced to the hobby and built this train car, and are in the process of building a locomotive. I will put up a video that gives a good look at how great this place is, it's a long video but it is well worth watching. Also it's now free to watch on YouTube. I did not make the video, but last year a talented camera crew/train-enthusiast, came and made a great video of Train Mountain.
Good luck fellow contestants with your entries!
-------------------------------------------------------------------
Videos done by; 7idea Productions --- https://www.youtube.com/@7ideaproductions
Location; Train Mountain --- https://trainmtn.org/tmrr/index.shtml
Pictures by; Eli and Jacob Nord
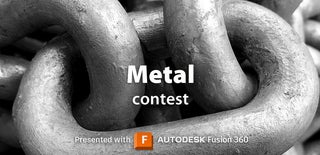
Participated in the
Metal Contest