Introduction: A 'Changing Faces' Sculpture
Six faces of this sculpture represent, in their initial state, six basic emotions: joy, surprise, anger, fear, sadness, disgust (see Reference). However, each face is divided in four horizontal slices that can rotate thus creating new expressions by combining elements of different faces. I think it might be interesting to create a new expression and try to interpret it.
Supplies
Materials
2 mm thick cardboard
1 mm thick cardboard
printer paper
salt dough
a piece of 8 mm thick plywood
a piece of 4 mm diameter steel rod
10 mm thick styrofoam
filler (optional)
white paint
varnish (optional)
glue
lubricant (e.g. liquid soap)
Tools
Xacto knife
fretsaw
drill with 4 mm drilling bit
saw for wood
brush for glue
brush for paint
sculpting tool (mentioned later in the text)
dough roller
sandpaper
pencil
Step 1: Pattern for the Faces
I drew a profile and then cut it from 1 mm thick cardboard; I also made a pattern to control the shape of the forehead of the model. After that I cut 5 profile pieces from styrofoam, glued them together and drew the contour of the face on the assembly.
The final shape of the pattern was made by cutting and sandpapering. It’s advisable to put filler on the pattern to cover pores in the styrofoam; the surface treated with the filler will be sandpapered and painted. I used thick flour glue as filler.
Step 2: Sculpting
I used salt dough to create faces. To prepare this dough I mixed 1 part salt with 2 part flour and 1 part water; the resulted dough should not stick to your hands. A 3 mm thick sheet will be made of this dough by using a dough roller.
I used one pattern to make all faces consecutively. The pattern will be glued to a flat piece of wood or plywood; a lubricant will be put on the pattern before applying the sheet of dough onto the pattern. Two or three drops of glue would suffice to fix the pattern on the board, it’s just to prevent the pattern from displacing when you sculpt the face. Then I put the sheet of dough onto the pattern and pressed the dough with my fingers to make the it repeat the shape of the pattern; then I cut the contour of the future sculptured face with an Xacto knife.
I marked the facial features with a pencil and sculpted them by using a tool made of a thin plastic stick shown in the picture; you are free to use different kind of sculpting tools. It’s advisable to follow the pattern attached here when sculpting the features to keep their proportions.
Fine sculpting will be made after the dough is dry and hard; I used an Xacto knife for this operation.
Step 3: Drying the Moulded Items
The same pattern was used for all faces, that’s why my proceeding was as follows:
put the item (the pattern with the roughly sculpted face) into an oven heated to about 70 deg Celsius (158 Fahrenheit) and keep it there until a crust forms on the surface, it takes about 40 minutes; however, the entire dough is not still dry
take the item from the oven, detach the face from the pattern and put it onto a hard flat surface (e.g. a table top) for final drying
The moulded 'face' should be fixed to this hard surface with pieces of adhesive tape to prevent the deformation of the 'face' when it's drying. After the face is hardened, it's necessary to check whether its back edges are flat. It might be necessary to sandpaper these edges to flatten them.
I proceeded this way because I believed that it would be easier to detach the face from the pattern when the inner surface of the dough is still soft. Indeed, the face detached quite easily.
Step 4: Final Sculpting
After the faces are dry, the fine sculpting will be made. I used an Xacto knife for this operation.
Step 5: Support for the Faces
The support consists of 4 hexagonal boxes that can rotate around their axis which is fixed in a base; the following sections provide more details about the support.
Step 6: Base and Axis
The base is a hexagon with the 40 mm side made of 8 mm thick plywood, the axis is a piece of 4 mm diameter steel rod with the length of 70 mm. It’s advisable to make some small grooves on the end of the axis that enters the hole in the base, to fix it better by gluing.
Step 7: Boxes
The base of each box is a hexagon with the 50 mm side made of 2 mm thick cardboard; I made a paper pattern to simplify the marking of the bases. The side walls of the boxes have different heights depending on which part of the face will be fixed to the box. The length of each wall side is 53 mm; the heights are: 20 mm (the ‘chin’ box), 14 mm (the ‘nose’ box), 16 mm (the ‘eyes’ box), 17 mm (the ‘forehead’ box).
At each end of the side wall chamfers are made to provide a clean junction of the walls; the drawing shows how to mark the piece for making a 60 deg chamfer. Thus, the inner surface of a side wall will be 50 mm long. I made the chamfers by sandpapering the edges to be cut (use sandpaper glued on a small wooden bar).
The junction should look as a line when seen from outside; if the chamfered edges don’t make a perfect match inside, the gap could be filled with some filler (I used thick flour glue).
The side walls should be perpendicular to the base; to assure this feature, you could use the technique explained in the picture.
Step 8: Making Slices
Each face will be cut in 4 horizontal ‘slices’, according to the pattern. I proceeded this way:
put the ‘face’ onto the pattern so the ‘pupils’ be on the horizontal dash-and-dotted line
mark the points corresponding to each horizontal cut line on both sides of the ‘face’
put a strip of paper to the points corresponding to a cut line and mark the line on the face with a pencil
cut the slice with a fretsaw
Step 9: Fixing the Face to the Support
The section explains how to install one face; the other faces will be installed the same way.
It’s advisable to draw a middle line on the side of the assembled structure, this line will serve as reference for positioning the face on the side. Otherwise, you could draw the contour of the face to assure its positioning in the middle of the side.
The slices of the ‘face’ will be glued to the side of the structure to form a ‘whole face’. After this, detailed facial features will be drawn with a black pencil; of course, you are free to colour the face as you wish.
Step 10: Varnishing
The assembled faces will be varnished to avoid that pencil-drawn features be slurred during the use of the object. I think it’s not compulsory to varnish the object if you draw the facial features with a paint; however, the varnish will make the object nice looking (in my opinion).
Step 11: Reference
That's an article about facial expressions:
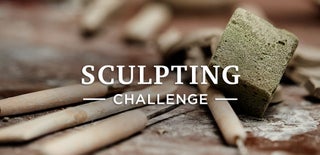
Participated in the
Sculpting Challenge