Introduction: A Commuter's Electric Bike
I thought that it was about time that I share my electric bike build that I have been using for the past 4+ years to commute to and from work. I know that I don't have all of the steps here to build this bike from the ground up but I thought it would be cool to share some of the things I have learned along the way while I have worked the kinks out of the bike. At this point I have put 3,400 miles on the bike with the current batteries. I have gone through four rear tires, three front tires, three sets of pedals (out of choice), three sets of brake pads, and have added new lights and other small fixings along the way. Much of the bike was built with reused and repurposed materials; the batteries, the battery boxes, the battery balancing cables, the racks, pannier bags, and the bike frame itself. This helped keep the total cost down to about $400 to build the entire bike.
Step 1: Find a Bike
The first step in building your electric commuter bike is to find the actual bike you want to use. I was lucky to find a 23" steel Trek with a Rockshox front suspension for only $75. You are going to want to look for something that is sturdy, affordable, and comfortable for day-to-day travel. I took some snapshots of a few examples available in my area right now. I preferred to use steel since it is more apt to handle tension and compression without fatiguing the metal, it also has a bit more give on bumpier sections of road. One of the most important factors for my bike choice was the center triangle of the bike frame. I needed plenty of room to build my battery storage box which holds not only some of the batteries but also the motor controller, a shunt for the computer, and the battery management system.
Step 2: Determine the Motor Type / Wattage
I decided that I wanted the motor to be a hub or "pie-pan" motor where the wheel itself is driven by a brushless DC motor. I also wanted the motor to be mounted in the rear since I was planning on having a fair amount of mass up front with batteries and my panniers to hold my work stuff. There are, of course, loads of options when it comes to selecting a motor to power your bike. You have all types of mid-drive, friction, and hub motors to choose from. I selected a rear hub motor since they are notably trustworthy, simple to install on a non-electric-specific bike frame, and are relatively inexpensive compared to other options. I purchased a 1000 watt motor with the intention to push it a bit beyond the 1000 watt rating and closer to 1,500 watts. This would be enough power to get me up the multitude of hills in my area while allowing me to do some nice cruising along the roads without pedaling too crazy. The motor I purchased four years ago is no longer available under its previous name "Aosom" but I am sure that there are plenty of other options out there. I posted a snapshot of my current motor, the order I placed for the motor four years ago, and something that should be comparable that is currently available.
**Note** Using a motor of this capacity might be illegal without proper registration and paperwork in your state. Just saying...
Step 3: Find Some Batteries
A friend of mine is extraordinarily well versed in the world of lithium ion batteries and was given a pile of batteries from a number of wrecked Ford C-Max hybrids. He went through preliminarily testing the majority of the batteries with a multimeter to determine which ones were holding a constant charge and put aside the ones that seemed to be a bit less than adequate. The "less-than-adequate" batteries still were plenty useable but might have been a bit puffed out or were holding a bit of a lower voltage than the others. They were not suitable for another larger electric vehicle but would be plenty suitable for smaller applications... say, an electric bike?
My friend gave me a fair amount of batteries that I could go through and load test. I needed 26 total cells for a 2P13S battery. That means that I wanted to connect two cells in parallel to each other to produce a battery with a greater capacity and then connect thirteen of those pairs together in series to produce the correct voltage to run my bike's motor. Since the batteries have a max voltage of 4.2v, a 13 series battery would produce 54.6v total. Although, my motor is 48v a max voltage of 54.6 is acceptable to power the motor and will cause no damage as long as you are not running the motor at that voltage for long periods of time... which you can't because the batteries drain as you run the motor.
I ended up testing each battery by setting up a simple load test using a piece of nichrome wire with alligator clips on either end. I would short the battery with the nichrome wire and use a multimeter to see how the voltage dropped over 20 seconds. Any batteries that took a significant dip in voltage from fully charged would be marked with an "X" and put to the side. For those of you battery gurus out there, I am sure that this is crude and very rudimentary but it worked great for my purposes and has worked well to determine which batteries aren't up to snuff for my bike. I ended up pulling out about 40 decent cells that could be used with my system. I used 26 of those 40 and put the rest to the side for backups later on down the road. If everything went as planned I would have a nearly 55 volt, 24 amp hour battery pack that could easily power my bike for at least 10 miles.
Step 4: Build the Battery and Test
As I mentioned earlier, I built the battery with two batteries in parallel (doubling the capacity) and then 13 batteries in series. I ended up cutting 18 gauge insulated wire in 3.5" sections, stripped the ends off of them and then used 1/4" eye connectors crimped on to both ends of the wire. The eye connectors slip over the top of the batteries stud and then the nut is tightened down on top of that but before I did that I needed to also have a jumper cable that would go from one pair's positive lead to the next pair's negative lead, wiring them in series. I also needed to add in a longer lead for a battery management system (BMS), which I'll explain in the next step. I used a long piece of silicon insulated cable for the final connectors that will be plugged into the charger and/or the motor. This long wire will come from the battery's negative terminal and positive terminal and was then soldiered to an XT60 connector. The connector's female side was soldiered onto the charger I decided to use, a Luna Cycle 48v charger to charge the entire battery. This would not only allow me to adjust the rate of charge (1amp - 5 amp) but would allow me to decide on the capacity of the charge and would also work with the BMS to balance the batteries at the end of the charging cycle.
Step 5: Gonna Need to Store Those Batteries!
With 26 of my batteries put together to make my completed bike battery I now had the problem of safely storing them but still making them accessible to check in on them from time to time... they did come out of a wrecked car after all (yes, I know, lithium ion batteries can "vent with flame" if not properly cared for). The batteries are heavy and add a fair amount of mass to the bike. I planned on putting a pannier rack on the front of the bike with all of my work clothes, lunch, and what not, so that location was out of the picture. Also, the front end is a particularly bumpy area of the bike and half of my commute is on bumpy dirt roads with lots of hills. The motor in the rear weighs a fair amount, so I didn't want to put ALL of the weight back there with the motor... think wheelies. I needed to put some of the mass more near the center of the bike so I started with building a box in the center triangle of the bike frame. The box has to fit the depth of the batteries (3.5") but also cannot be so wide that your legs are going to hit or you are going to be uncomfortable pedaling the bike. The box was just shy of 4" wide which left enough room for the batteries and connectors but didn't impede my pedaling. I used U-bolts to connect the top board to the frame. I slipped an old piece of pneumatic hose on the U-bolt to help prevent marring the frame too much (it is steel and I didn't want it to rust). I also attached the bottom board with one U-bolt and then used one of the existing water bottle cage braze-ons to attach the bottom of the board. The front vertical board was screwed to the top board and then I made an "L" bracket out of some stainless steel strapping I found for free to attach the bottom of the front board to the bottom board. I did the same thing for the back board, closest to the bike seat. This made for a nicely rigid box that fit SOME of the batteries, 12 out of 26 to be exact. To hold the batteries in place and to prevent bouncing around I used a couple of pieces of foam that came in the box I received the charger in (waste not want not!) and put them below the batteries to prevent jarring them. I then I used a piece of hook-and-loop strapping from an old sleeping bag stuff sack to make a retaining system for the batteries. I epoxied both ends of the strap to the box so that they could wrap neatly around the batteries in the box and hold them in place.
So... 12 out of 26 batteries fit in the center box along with the motor controller, the shunt for the computer, and the BMS. That means 14 more batteries needed to find a cushy home to call their own. I had a pile of scrap plexiglass that a friend gave me that I thought would make a rigid, lightweight storage box for the back of my bike. The motor came with a somewhat cruddy, but solid pannier rack which happened to fit perfectly on the back of the bike. I attached a piece of scrap plywood to the top of the rack and then began the design of the plexiglass box. I used the same scrap foam in the box to help insulate the batteries from bouncing around and used a heat gun to fold and form the plexiglass to shape. I then used some Gorilla tape (honestly the stuff is amazing) to help seal the seams up tight. The cap for the box is also made from a piece of plexiglass and some velcro holds it tight to the box. I drilled one hole in the cap so that the cables can come out of the box. You'll see in later steps that I had to modify this so that I could run the BMS wires out of the box, a really cool step by the way. The plexiglass box has a small, thin board on the interior that helps make it even more rigid and allows a stud to pass through it, then through the plywood on the rack so that a large hand nut can be tightened on to it holding everything in place but still really easy to remove. The whole thing is water tight, insulated, and overall a perfect fit for the bike.
Step 6: Fitting It All in and Closing Up the Box
You can see in the first picture that I placed the motor controller on the top of the center box, above the batteries. This is where the controller has lived since I built the bike. From that point I had to make a few additions to the box including a shunt for the computer and a battery management system to keep the bike from randomly catching on fire as the lithium ion batteries "vent with flames" (I just love saying that). I went totally low-tech on the door for the box and just used a couple of strap hinges and a piece of plywood as the door. I used a long bolt and a wing nut at the bottom to keep it all closed up but easy enough to open and charge the battery. I ended up painting it all with some leftover Rustoleum aluminum colored paint, which has done a nice job keeping it all preserved.
Step 7: Computer Monitoring System
I needed some way to keep track of how much juice my battery had while I was riding it and also what the current state of charge was for the battery before taking the bike out for a ride. There were some really nice computers out there such as the cycle analyst but I couldn't justify spending $100+ on a simple device. I found this nice Bayite computer on Amazon for a walloping $15. The computer came with a 100 amp shunt that worked perfectly with my set up. It is not weatherproof so I needed to do some modification and ended up building a really simple case to hold onto the computer and keep it mostly waterproof. I used some more leftover Plexiglas along with some bolts and stainless steel piping I had kicking around. It is attached to a sturdy base that was attached to my bike's stem. It is removable but I have never had the necessity to take off the computer. A sample of the batteries state of charge is taken through the shunt, which is found in the center triangle box (see the wiring in the image but use the directions that come with the computer).
I ended up ordering my BMS from Aliexpress since I was having a really hard time sourcing one from any other location. It was darn inexpensive and showed up in a few weeks. It's pretty self-explanatory but the overall premise is that you have a lead from the BMS to each individual cell of your battery (remember that I doubled the capacity and made two cells into one by wiring them in parallel). The BMS monitors and balances the entire battery system by drawing down the voltage of each cell so they are all equal at the end of the charging cycle. By the way, you need to have a charger that can handle this type of balancing. The Luna Cycle charger does handle this with no problem and you will see the voltage dropping while it remains plugged into your bike after it is done charging. The charger I received with the motor DOES NOT balance the battery but will instead charge it in bulk until the battery with the highest voltage hits the threshold allowed by the BMS. This does limit the overall charge of your bike but it prevents the oh-so-scary "venting with flames" and also gives a world of extra life to your bike. Get the right charger! I ran the BMS' leads to the back battery using a 16 pin connector that was reused from a wrecked Honda insight. I was able to soldier the leads from the cells to the female end connected to the box and then ran the leads to the male end leading to the box... looks really cool and has been extremely functional, especially when I have had to take the box off to change out cells (which has only happened once).
Step 8: Fixings to Make Your Ride That Much Better
There have been a lot of things I have learned about commuting to work on a daily basis using my electric bike.
Lights: One of the most important things I have learned is visibility, you can NEVER have too many lights or reflective things on your bike. I have a nice bright blinking red light on the back of my bike from Planet Bike and two blinking lights on the front of my bike, one attached to my mirror and one additional one on the handlebars. I also use my large light for night time mountain biking to light the way. More light is better, no matter what.
Pedals: I have a mostly rural commute with three miles of dirt roads and lots of hills and then three to five more miles (depending on the way I go) of moderately busy roads. It's nice to have some very sturdy pedals, especially with how heavy the bike is with the motor, batteries, and work stuff that I bring with me. I was able to scavenge some heavy-duty BMX pedals from a bike being tossed out on the curb. Sturdy pedals make you feel more comfortable and confident.
Mirror: I like to know who is behind me at any given moment and a mirror is really the safest way to check it out. I ended up getting the little mirror I use on my bike as a gift a number of years ago but never put it to good use. I like it because it folds out and gets out of the way when needed and it also has a small blinking LED light that works great as a backup just in case one of my other ones kick it.
Kickstand: The bike is not light and with a fully loaded set of panniers it can tip over easily with a conventional kickstand. I ended up purchasing a really nice kickstand on Velo Orange for about $30. It is worth every cent.
Panniers and Pannier Rack: The beauty of using this bike is that I can bike in with my work clothes on (I am a middle school teacher, so they are not too fancy) and not end up a sweaty mess. I still need to carry a lot of stuff into school and I needed something sturdy but easy to remove. I had an old rack that I recovered from a junky bike I found on the side of the road. I was able to retrofit it to fit the front of my bike using a bit of stainless steel strapping and a longer skewer for the front wheel quick release (I ended up using a rear-wheel quick release). The pannier bags are vintage from the late 90's but they work great and are made really well. I am sure you could score both a rack and a set of bags used or on sale.
Tires: The final thing I want to remark on are the quality of your tires. I have had this bike up to 40 mph on flat ground and with its inertia you don't want a random exploding tire. Recently I started using Schwalbe Marathon Plus tires. They are not cheap at $50 but they are well worth the piece of mind. Seriously, I spent more on one tire than I did for the BMS, computer, and kickstand combined.
Staying Warm: Even on a relatively warm morning moving at 30 mph can make a 50 degree air temperature feel like it is well below freezing. I have taken my bike out while the air temp was in the single digits and you can imagine how cold it gets. I use all different pairs of gloves, coats, and hats depending on the temperature. When it is really cold I use super insulated mittens, a balaclava and thin hat over that, fleece pants over my work pants, two coats, and ski goggles... I think you get the point. Stubborn? Yes, but that is half the fun!
Step 9: Ready to Roll!
I hope that this instructable gives a good picture of what I think works as a fantastic electric bike for commuting to work. I have put a lot of miles on my bike and can honestly say that, even on the coldest days, I enjoy riding to work much more than driving. There's something to be said about seeing the sun rising through the woods while you are noiselessly cruising on a dirt road. You get a bit of workout to wake you up before you arrive to work and have something to look forward to when you need to head home. If you have any questions or comments do not hesitate to reach out to me. Thanks for reading!
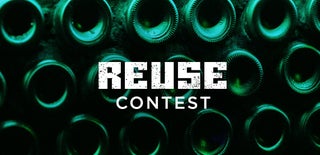
Second Prize in the
Reuse Contest