Introduction: A-Frame Wine Rack
While on a winery tour a couple of years ago a friend of mine was admiring the A-Frame wine racks some of the wineries had. It just so happened that he was turning 50 soon so I decided that a smaller version of one of those would make the perfect gift (after checking with his wife for the available dimensions of course).
The construction seemed simple enough and I had a hole saw set I purchased on a huge sale the year before that I was dying to try out so this seemed like the perfect opportunity.
Step 1: The Hole Saw Set
This was the tool that matched the job - a case with an assortment of heavy-duty hole saws. Not something that a home hobbyist would usually use but at 90% off I couldn't resist, and figured I'd find a use for them later, and here it was. I wouldn't recommend using the flimsier multiple blade style hole saws you normally see in cheaper sets as I found they take a lot more patience and a lot cleaner working area to make work for anything larger than the smallest holes.
Step 2: Sketching It Out
I'd only seen the wine racks briefly and didn't have much of an opportunity to check out their construction so I sketched out how I thought it would work. I drew up a plan for a little test to see if I could make it work, as well as the rough outline of the parts, and how I thought the hole drilling would work.
Step 3: Testing the Holes
In one photo I saw on the internet the construction was done with two thin sheets of wood using straight holes, offset between the front and back pieces. A quick test told me that this was less than ideal because the wine bottles would have two small lines of stress rather than one bigger one. It might have worked in a pinch with a small rack, if you were working under the constraint of only being able to drill vertical holes.
I decided that I would try to go for the premium arrangement and drill through heavier wood on an angle. To see how it would work I drilled an assortment of hole sizes at a few different angles and tried the bottles out in the wood.
With the few sample holes I was able to guesstimate the amount of space required between the holes for clearance both for a bottle and a hand to fit in to pull it out, and noticed that the angle of the hole had to be greater than the angle the wood was tilted so that the bottles sat with the majority of the weight downwards, with enough counterbalancing upwards to hold them in place.
Step 4: Sizing the Project
Once I knew the formula for determining the hole spacing and angle I could decide what the rack capacity would be. The width of the bottles and depth of the holes required 2"x6" boards for the fairly steep angle I needed to fit into the available space. Spacing the bottles 4 1/2" vertically gave me enough for 12 rows, and the width available was just a little over 2 feet so I could make it 4 boards wide.
That gave me a total capacity of 48 bottles, doubled because I was going to do the same thing on both parts of the A-Frame as it seemed that would give it the most stability. Not being especially adept at joinery I decided to use back and bottom supports to hold everything together. That would also contribute to the rustic sort of look I had decided to go with.
Step 5: Cutting the Pieces
This was probably the easiest part of the project. A simple mitre saw combined with a two-ended file and some rough sandpaper was all I needed to create the main boards and the support pieces. I kept everything kind of rough to help contribute to the rustic look.
Doing the math a bottle of wine weighs just under 3 pounds, and there could be up to 96 bottles in it at one time we we're looking at 300 pounds plus the weight of the rack itself, which was probably around 50 pounds. So I overengineered the supports as well as I could without detracting from the look. That's why I went with 2"x3" rather than strapping or metal plates. (Were I a joinery expert I'm sure something even fancier could have been accomplished.)
Step 6: Assembling the Main Pieces
The next easiest step was assembling the two halves of the A-frame.
Only two little gotchas here that I fortunately caught before I had to undo anything.
- The bottom support had to be angled so that it wouldn't catch on the carpet if it were dragged across. (And this sucker was going to be heavy so it would almost certainly be dragged.) I could also have put a little metal plate of something across that corner for even more stability.
- The spacing of the supports turned out to be not quite even. The reason is because of the holes, and the fact that they were angled. Before positioning the supports I used a pencil to mark where all of the holes would be, front and back, and then positioned the supports to be between them, but as evenly spaced as possible.
Step 7: Paint Test
Why paint now when I was nowhere near finished? It's because of the rustic look. The easiest way to make something look distressed is to put it through actual stress. I figured if the paint was in place while I was working on the rest of the project then it would take a beating, making it fit in with the general look.
After the tests the watered down paint looked to be the best option. It got the colours across but didn't pop out at you.
Step 8: Transferring the Art
The art projector I used is a simple light-based mirror system. The downside is that you need a dark room for it to work, but the upside is that it's dirt cheap! If you have an LCD projector you could use that and get a better image. Kickstarter has quite a few these days.
Once projected onto the wood it was easy enough to paint the logos on. They were left exposed for the "distressing" to come.
Step 9: Jig Test
Next up was creating a jig that would let me create the holes in a nice even way. They had to line up both horizontally and vertically fairly well as any small differences would be magnified by the bottles being in them.
For this first test I used a small jig with just one hole in it, with the hole set to the angle I wanted using a simple angle tool. Notice two bits of cleverness in the jig design:
- The front part is angled at the same angle as the hole, so that I could drill the jig holes vertically and keep them in line (not to mention keep the hole depth minimal so that my hole saws worked properly). If I had a Forstner bit and a drill press I wouldn't have to go through that effort, but I had a hole saw and a hand drill so this was good.
- The rails were fit tight to the slat, so that vertical alignment was guaranteed.
However, as you can see by the test that the bottles didn't quite line up horizontally, due to small discrepancies in where I positioned it over each piece of wood.
To cure that I decided to make a larger jig.
Step 10: The Big Jig
To guarantee horizontal alignment I decided to make a jig that fit over all four slats at the same time. That also let me leave the two body pieces assembled while I worked on them, a definite bonus.
As with the smaller jig I cut the face on an angle to provide a vertical hole for the jig drilling. Unlike it though I couldn't use a simple angle tool to judge the hole angle as all four had to be identical. To manage that I enlisted the aid of a small drill guide I had. It wasn't sturdy enough to handle all of the drilling, as a drill press might be, but it was good enough to get 4 holes at a consistent angle.
The pilot holes were something I thought to be particularly clever. The only thing the jig didn't yet provide was a way to evenly space the rows. In a previous Instructable I solved this by creating a two-level overlap so I used that general approach here as well. By creating a small pilot hole that exited exactly 4 1/2" away from the main hole it would provide the location for the next row to be drilled, as well as the pilot to ensure those holes started correctly aligned. It worked extremely well for something so simple.
The final image shows the jig in action. I did it all freehand - the depth of the jig hole provided enough guidance to keep the hole angle consistent.
Step 11: Finishing the Holes
After working my way down the piece drilling all of the holes I had to flip the whole thing over as the holes didn't quite go all the way through.
This turned out to be a good thing though, as the little bit of drilling I had to do on the back made it very easy to get the wood plugs out of the hole saw. And as an added bonus I ended up with dozens of nice wood cylinders for the fireplace.
Another quick test to confirm everything worked well and I was ready for the final phases.
Step 12: Finishing
Final finishing was also quite easy (sensing a theme?) as all that was really left to do was apply the stain over the finished wood.
In addition, my friend's wife had mentioned that they probably wouldn't have more than 60 bottles at any one time so I thought I'd make part of the bottle storage into a removable message board. Some thin board painted with chalkboard paint was fit tight to the main piece and you'd never know it concealed space for 12 more bottles.
Step 13: Keeping It Together
Finally the two pieces were brought together. The piano hinge at the top served the dual purposes of holding the angle between the slat from shifting back and forth. Since the screws went in the ends they were put in deep (2 1/2" #10).
Lastly the chains were added. The attachment points were made solid, but removable, in case the chain size didn't turn out to be sufficient for the weight. Using the angles between the pieces I had calculated earlier I added a little extra to the chain length so that they would hang down in that natural looking curve.
As it turned out I needn't have worried. The rest of the construction was so solid that the rack barely moved when it was put in place.
Step 14: The Final Product
Seems like it's missing something... like about 60 bottles of high quality wine. (French would be appropriate, don't you think?)
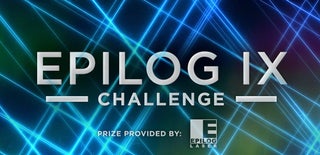
Participated in the
Epilog Challenge 9