Introduction: A Kitchen Window Seat and Hutch
For about five years my wife and I have talked about how nice it would be to have a window seat in our kitchen where the morning sun streams through the house. We also talked about having more storage space for the kitchen for pots, pans, lids, wine, mixers, and other kitchen tools that we use all the time. We also thought it would be just fantastic to have a better system to store recyclables and hide the trash. Hey, and how about a nice standing desk too so we can set our computer down and play music from it. So two years ago I measured the space where this most magical thing would go and I designed a scaled drawing of exactly what we wanted... and the plans got rolled up and stored for two years. In January of 2020 I thought I would resurrect the plans and get the ball rolling for the kitchen window seat and hutch I am going to show you here.
The purpose of this piece of furniture was as follows:
- Make a window seat to read or just watch the birds through
- Make a flat surface for a fruit bowl, standing desk, toaster, and serving station when we have larger dinners
- Store wine, liquor, and such neatly and safely
- Store all of pot and pan lids
- Store a slow cooker and mixer along with all their parts
- Store napkins and other kitchen utensils
- Store and organize recyclables and trash
It has honestly been the best piece of furniture in the house and has been insanely useful for our day to day tasks in the kitchen and for kids doing homework or just a quiet place to sit and read a book.
I built the cabinets and drawers using mid-grade birch plywood and built the tops, face frames, doors, drawer fronts, and paneling from locally harvested red oak. I used two sheets of 3/4" birch plywood, one sheet of 1/2" birch plywood, and about 50 board feet of oak lumber for the entire project. The drawer slides and hardware were ordered from www.leevalley.com and I bought the trash cans locally. The total cost for the entire thing was just under $500 from start to finish. I used mostly basic case and face frame construction techniques to build it and required the use of a table saw, band saw, jointer, planer, drill press, sliding compound miter saw, hand drill / driver, pocket hole jig, router with rabbeting bit, dado set for table saw, tenoning jig, and lots and lots of clamps!
The purpose of this instructable is not for you to build what I have built to the "T" but to give you some ideas to build something that has so much utility as what I have built. I hope you find some inspiration with the project and please do not hesitate to ask any questions.
Step 1: Measuring Your Space and Drawing Up Your Plans
The space we were working with was always a bit awkward and begging for something a bit more organized. I wanted the piece I was to build to match up nicely with the bookcases I had built a number of years ago both in form and function. I also wanted the final result to use as much of the wall space as possible while not looking big and bulky and ultimately being in the way. I first measured the wall space with the bookcases and created a scaled drawing of the entire wall. This allowed me to determine the exact dimension of the final product on paper before making one cut in the wood. I made the window seat 5' long with three large drawers underneath it hold pot and pan lids, wine bottles (I know they should be on their side but we are not that fancy), and other large heavy items that never find a good home in the kitchen. The hutch is also 5' long and has two deep and wide drawers that allow for a lot of square footage while being proportionally pleasing to the eye (go golden rectangle!). There are two doors on the hutch, one on the left and one on the right that house everything from china to an instapot and then the center "door" is actually on slides to pull out and act as a trash and recycling center.
I wanted everything to be proportional and attractive yet still have all the utility and function necessary for a daily-used piece of furniture. I wanted both form and function and I think I got them pretty close together on this project.
Step 2: Deciding on Wood Species and Sheet Goods
I decided to use birch plywood since it is readily available at our local lumber yard. The stuff I bought was about twice the price of what you would buy at the big box stores and was about twice the quality too... which honestly isn't say that much. At about $75 for a sheet of 3/4" I was a bit disappointed in the thickness of the birch veneer. It was nearly paper thin and splintered like nothing else. A local cabinet-quality lumber provider was selling much higher quality birch plywood for another $20 more per sheet. Although I wanted this project to be beautiful I didn't think that I needed that level of lumber since much of the edges of the panels were going to be either in joints or covered up with red oak.
I went with red oak as the main lumber because it is readily available and a local sawyer mills it up, dries it (air), and stickers it for anyone interested to file through. At $1.00 per board foot it is a steal and I love supporting someone who is locally harvesting timber. Oak is somewhat forgiving and it matches the oak cabinets we already have in the kitchen I had built a number of years ago.
Step 3: Building the Cases - Cutting the Dados
I am not going to go into extreme detail here on every dimension cut but rather an overview on how I built the cases for the cabinets. I built the window seat and hutch as two separate cases. When I brought them up into the kitchen I then attached them to each other.
I used my table saw to cut the case components to size based upon my original drawings. I planned on using simple dado joints to join everything together. A dado is basically a groove sawn down a board so that another board can fit into it. I used a dado blade on my table saw to make the cuts and test fitted a number of pieces to get the fit tight but not so tight you need to use a hammer to put them together.
All of the dados were cut after I marked exactly where I planned on joining the pieces together. I planned to use glue, screws, and a countersink bit to bring the whole thing together.
Step 4: Building the Cases - Dry Fit the Parts
After I had all the components cut to size and dadoed in the correct spots I moved on to dry fitting all the parts to make sure everything was square and fit together properly. If you need to pound things together with a mallet your dados are too tight. You can see the stretchers at the top of the cases in the second picture. These are there to connect everything but didn't need to be a big sheet of plywood since I am installing a solid wood top on both cases. I left a kick space at the bottom of both cases since I planned on making an arched rail at the bottom of both cases.
With the right fit the cases should stay together on their own during the dry fit.
Step 5: Building the Cases - Sand and Finish the Parts
Before you glue and screw everything take the time now to sand everything to at least 220 grit and then finish them. I used both Vermont Naturals whey finish and Minwax Polycrylic since both have super low to no VOCs and I can finish everything in my house or shop... depending on which one is warmer :)
With these types of finish you need to sand the first and second coats lightly to remove the raised grain and then clean off the dust and put subsequent coats on from there. I did about six total coats. It's more coats but no smell and the stuff dries in a couple of hours unlike polyurethane.
Step 6: Building the Cases - Glue and Screw the Parts Together
I used a square to mark where all of the screws needed to go in line with the dado joints. I then used a counter sink drill bit to drill the holes in the correct locations. I then used a small glue brush to glue all of the dados on all tree sides and put the cases together. A few clamps can help tweak things to get them straightened out completely and square and then the screws are used to pull it all together. I was able to use screws since all of the joints would be covered up by false panels, the top, or were not exposed at all. This is a rock solid method to build cabinet cases.
Step 7: Building the Face Frames - Inventory Materials
Once the cases were built it was time to get the stock together for the face frames. I used 7/8" red oak stock to make the face frames. Most of the frames were 1-1/2" wide and 1" wide with the bottom rails of both cases being 2-1/2" wide to accommodate the arches and to give the entire thing a solid footing in appearance. I planned on having the drawers and doors inset into the face frame.
I had to determine how many of each piece I needed for the final face frame by using my original drawings along with the finished cabinet cases. I cut enough stock to build the face frame with a few pieces to spare. I set up the stock I was planning to use for the face frames and then marked out which pieces went where by labeling each piece on my drawing, on the cabinets, and on the piece of wood I planned on using for the face frame. I inventoried this all on a sheet of paper so that I could clearly determine what pieces I needed and insured that each piece had a specific home with the face frame.
Step 8: Building the Face Frames - Marking and Cutting the Arches for the Bottom Rails
The bottom rails of the face frame are arched giving the entire piece a lighter feeling. To mark the arches I used a nifty trick to make the template for both bottom rails. Here's what I did:
- You'll need your template stock. I used 1/4" plywood that was the exact size of my bottom rails (both length and width).
- You'll need a backing board that you will attach your template to with screws. I used a piece of 3/4" pine. The screws will mark the bottom left of your arch, the center point of your arch, and the bottom right of your arch.
- I planned on having my arch start 3" in from each end of of the rail and 1/2" off the bottom. I marked this spot on the left and right sides of the template and then put a screw through the mark on the template into the pine board leaving about 1/2" of the screw shaft sticking out.
- I then found the center of the template and marked exactly how high up the rail I wanted the arch to go. I put another screw in at this point with about 1/2" of the shaft sticking out.
- Now you need two straight sticks of scrap wood. I used a couple of pieces of 1/2" thick scrap that were ripped to about 1" wide. Take the first one and put one end on the bottom left screw shaft and the other end on the center screw shaft. Try to make it so the end at the center screw just hits the screw shaft.
- Now take the other stick and run it straight out from the stick ending at the center screw shaft. Make sure it is perfectly parallel to the bottom of your template by using a ruler to measure it.
- Finally, use a piece of scrap wood to hot glue the two sticks in exactly this position.
- To use the jig you need only put a pencil in the notch where the two sticks meet and carefully move the jig over the screw shafts with your pencil moving with it.
This guy does it a bit differently than me but it's pretty much the same idea and might help you more with a video.
I then used my band saw to cut out the arches and put them in my tail vise to sand them in tandem with a belt sander. I used a orbital sander to finish sanding them to 220.
Step 9: Building the Face Frames - Drilling Pocket Holes
I used a Kreg pocket hole jig to attach the face frames (along with glue) to each other. All rails were pre drilled with pocket holes to meet the stiles. You could use biscuits, mortise and tenon, or a number of other methods to join the face frame pieces to each other. The pocket holes and screws were more than adequate and allowed for some wiggle room when it came to squaring everything up, especially since this face frame was ENORMOUS!!
Step 10: Building the Face Frames - Assembling the Face Frames
Assembling the face frames was a feat upon itself. I made the face frame for the 5' long window seat and 5' long hutch all one single face frame manufactured in my shop and then brought upstairs to be adhered to the cases. I wanted a uniform, unbroken appearance to the entire piece but it required some planning and patience. I first assembled the hutch face frame and clamped it to my work bench. I then attached the window seat frame to the hutch frame using my workbench as an anchor point. Make sure you plan everything out before you dive into putting it all together. You'll need all the clamps you plan on using along with all the glue and screws cued up and ready to go.
Step 11: Building the Face Frames - Adjusting Frames to Fit Cabinet Bodies
At this point I was able to test fit the face frames to the cabinets and could make any minor adjustments as necessary. Luckily I was pretty spot on and only had to readjust a bit here and there to get everything lined up. You might need to take a few shavings off with a chisel or even unscrew and move something completely but as long as you took the time to plan out all of the components and did some test fitting prior to glue up you should be pretty close to what you need. This face frame was 10' long and 48" tall... so the room for error was definitely there.
Step 12: Attaching Face Frames to Cabinet Carcass
You're going to need a lot of clamps!
Before I got started I ended up putting a couple of blocks of wood under the cabinets to help keep the entire thing that much more rigid. Probably not necessary but I figured it wouldn't hurt with their significant size and people sitting on the window seat.
To attach the face frame I used every clamp in my arsenal. You could use biscuits or dowels to adhere the face frame to the cabinets but I simply used glue and a few well placed inconspicuous nails... and a crap load of clamping pressure. Make sure you use some cauls to distribute the clamping force more evenly across the joining areas. Take a look at the pictures how I clamped up.
Step 13: Making the Tops - Inventory
The tops of both the window seat and the cabinet are solid oak edge joined with biscuits. The ends are also biscuited to a perpendicular piece of wood making breadboard ends. It's best to select stock that isn't too wide (5" - 6" wide at the max) and that can be stable in it's expanding and shrinking movement it will go through during the year. The tops are not screwed down tight to the cabinets but instead are allowed to move while the tops expand and contract. When selecting your stock think about how you can help minimize the extremes of the seasonal movement by alternating the direction of the grain the wood runs in. Have one piece with the grain running straight out and down while the next runs straight out and up (cup up and cup down). This will minimize the effects of seasonal movement.
Step 14: Making the Tops - Flattening and Sizing the Stock
I used a jointer, table saw, and planer to flatten and size the stock. First use your jointer to joint one face and one edge of each board so that they are square to each other. Then use the planer to flatten the opposite face of the one previously jointed so that both are parallel to each other. I milled my stock to 7/8" thick and then used my table saw to square up the other side that was not joined.
Step 15: Making the Tops - Biscuiting the Tops
I used a plate biscuiter to join the boards to each other with #10 biscuits. I laid out each board that would make up the top and marked the edges with a letter so I knew which edge matches up with each other (also so I wouldn't mix up which top went to which cabinet. To mark the biscuits I simply make a tick mark across the two edges where I want the biscuits. I placed them about every 8" on center. They are not particularly structural, they just help line everything up and give you more gluing surface.
I put the biscuits in a metal tray and put them on top of my wood stove for a little while to help suck all the moisture out of them making it immensely easier to put them into their little slots made by the plate biscuit cutter. I used a glue roller along with a small brush to apply the glue to both edges. I then used cabinet clamps every 8" to clamp the tops together.
Step 16: Making the Tops - Adding Breadboard Ends
I made sure to hand plane and sand the tops so they were perfectly level and flat. I then cut the ends of the panels completely square to the edges. The breadboard ends are attached to the panels using a double layer of biscuits. I made sure to put a slight relief in the center of the breadboard end by using a small block plane. This allows the ends to pull tight against the panel making a more seamless connection, it's called a spring joint.
I first glued the biscuits in place in the ends of the panels and let them dry. This is necessary so I can use dowels as pins to hold the breadboard end to the edge of the panel while allowing for adequate movement.
Since I didn't have clamps long enough to pull everything together tight I clamped the panel down tight to my workbench and used the bench dogs as a stopping point where I used two wedges to "push" the breadboard end tightly up to the end of the panel.
To keep everything pinned together I used bamboo shish-kabob skewers as the doweling pins. They blend in beautifully with the oak and allow for adequate seasonal movement. The skewers need to pass through the two outside biscuits on the breadboard. You will apply glue to keep them pinned into place. As for gluing the breadboard to the panel. You need only apply glue to the middle biscuits and the middle of the edges of panel and breadboard. This allows for seasonal movement of the panels unrestricted by the breadboards. They might be lined up perfectly now but you will have about 1/4" of swelling per linear foot of your panels which will translate to the breadboards sticking past the panels edge during the winter (especially if you run a wood stove as we do) and the panel running flush to the edge of the breadboard ends during the summer's humidity.
Step 17: Making the Ship-lapped Panels for the Doors and the False Panels
I used the same 1" rough oak stock to make the ship lapped panels for the false panels that went over the exposed cabinet faces and the door fronts.
I selected stock that was free of voids and loose knots but I was not opposed to some character with the panels since they were such a visual part of the cabinet.
I used my bandsaw with a 1-1/4" resaw blade to resaw the selected stock into 3/8" thick strips between 2 and 5" wide. After planing the stock completely to 5/16" thick I used a rabbeting bit on my router to make the ship lap on the edges of the boards.
Step 18: Building the Doors and False Panels
The doors and false panels are built using tenon and groove joinery. I used stock with the straightest most uniform grain for the door rails (horizontal pieces) and stiles (vertical pieces). The interior edges of the rails and stiles are dadoed to receive the ship-lapped pieces. The tenon cheeks are cut using a tenoning jig and the tenon shoulders are cut with a backer board and the table saw blade set to the correct height. The groove that was dadoed out goes the entire way around the interior edge of the door or panel. I cut the dado 1/2" deep to accommodate the ship-lapped pieces and their seasonal movement. Check out the pictures for more details on this whole process.
Step 19: Finishing the Doors and False Panels
Before assembling the false panels and doors it is important that you completely finish all parts. This allows all the edges of the ship-lapped pieces to be coated in finish before putting them together. This not only makes finishing easier on a whole but also insures that when things do move (which they will) you will only have finished pieces of wood exposed.
After I finished all of the pieces I was ready to assemble the doors and panels. To help keep the ship-lapped pieces centered and tightly held in place to prevent any rattling during the winter I used small pieces of foam (like from a couch cushion) set into the grooves of the door rails and stiles. Apply glue to the tenons shoulders and cheeks only and then clamp the panels / doors together.
Step 20: Installing the False Panels
After the doors and panels were completed I prepared them for installation. The face frame that I had built had 45 degree edges on any areas that were going to intersect with a false panel. I made sure to take care of this important detail before adhering the entire face frame to the cabinet. I cut the false panels with a 45 degree angle along one edge and then used glue along the mitered edge and clamps to hold it tightly in place. I used screws drilled from the inside of the cabinet to attach the panel tightly to the cabinet body. You will never see the screws since drawers will be installed in the window seat cabinet.
Step 21: Building the Drawers - Inventory
I did not use any complex joinery for the drawers. I used 3/4" plywood to build the bodies of the drawers and laid out all of the components on a sheet of plywood to utilize as much of the plywood as possible with a minimal amount of waste. The drawer fronts were made from solid Red Oak lumber. The bottoms of the drawers were made from 1/2" birch plywood and were glued in the grooves they rest in. The drawer boxes are indestructible but since they are made from plywood it was important to cover up the edges of the plywood. I used thin strips (about 1/8" thick) of red oak cut to a width of 1" wide to act as edge banding on the drawer edges.
Step 22: Building the Drawers - Cutting and Layout
As you determine your dimensions for each drawer lay out the pieces bottom corner to bottom corner so that you can clearly mark where each piece will go. This will make it much easier to know exactly where dado cuts need to be made and what end will be the front or back of the drawer body.
Step 23: Building the Drawers - Rabbeting and Dadoing / Building the Joints
The front of each side of each drawer box needs to be rabbeted (a square cut on the edge) to receive the front piece of the drawer box. The sides also need to have a dado cut along their inner face to receive the back piece of the drawer box. You should set the back piece inwards by about 1/2" for structural sake. The final dado cut for each piece is the groove that will retain the bottom of each drawer. This groove should be about 3/8" deep (just as the other ones are) and runs the entire bottom edge of all four drawer box pieces. I used my table saw with a dado stack to cut all of these parts. Once again, check out the pictures for even more detail... I hear a picture says a thousand words.
Step 24: Building the Drawers - Cutting and Fitting the Bottoms
You will have to put the boxes together before determining the exact dimension of your bottoms. If you used 100% plywood as I have up to this point you can cut them to fit exactly, which will make for a really rigid drawer.
Step 25: Building the Drawers - Finishing and Gluing Up the Drawers
Before moving on to glue up the drawers you will want to completely finish them. I taped off any of the edges that were going into grooves to be glued so that the glue would be most effective. I needed A LOT of space for all the parts and my shop was too cold anyhow so I decided to just finish everything upstairs right on the cabinet I was building. Once again, I was only using the Vermont Naturals Whey Finish at this point, so there are no VOCs to cause drain bramage!
Step 26: Building the Drawers - Edge Banding for the Exposed Edges
Once the drawers were finished I glued their edges and clamped them up to dry. I did end up using small pin nails with my nail gun to help pull the boxes together even tighter.
I then used small 1/8" thick x 1" wide strips of red oak and cut and fit them to the top edges of the drawer boxes. I applied glue to both the drawer edge and the little strip of wood and used tape to tightly pull everything into place. It was actually easiest to just put the drawer boxes into their respective locations to let everything dry. I was able to lightly sand the edges of the strips to meet the outside edges of the drawer box and then put a finish on the little strips.
Step 27: Installing the Drawers - Setting the Slides
I ended up using a slow close 100# capacity drawer slide purchased from Lee Valley. These have been able to withstand 20 bottles of wine or a dozen heavy cast iron lids with no problem at all. You'll need to follow the directions that accompany your specific drawer slides but most of these newer slides have enough adjustability and are easy enough to install that you will be pretty darn successful. I did have to use some shim strips to help get the slides out from behind the little relief I had from my face frame. I used double stick tape to do this and then attached the cabinet portion of the slide on top of the little strip of wood. I used a block of wood set at a specific height to put all of the slides in exactly the same spot for each drawer with identical dimensions.
Step 28: Installing the Drawers - Drawer Fronts
I used solid oak for the false drawer fronts. For the large drawers of the window seat I had to glue these up similarly to how I did the tops for the cabinets. The long drawers of the hutch were able to be made from single pieces of wood since they were not as tall. I used double stick tape to first adhere the false drawer fronts to the drawer boxes and then used screws from the inside of the box into the drawer fronts to hold them in place. I used four screws per false drawer front.
Step 29: Installing the Drawers - Drawer Hardware
To install the hardware I first found the exact center point of where I wanted the hardware to go. I made a crosshair on the drawer front to show this location. I then made a masking tape template of where the screw holes are for the drawer hardware along with the same cross hair at the center mark as I did on the drawers. I just simply measured down from the top edge of the drawer put the tape on the drawer front lined up with the cross hairs and then made sure it was level. I then could drill the holes to install my hardware on the drawer faces.
Step 30: Installing the Doors, Door Stops, and Door Hardware
I used European hinges to install the doors. They come with wonderful instructions that I am not going to try to explain but basically you make a hole in the door to accommodate the cup of the hinge using a forstner bit and then drill the holes to hold it in place with screws. There is SO MUCH adjustability with these hinges and they really went on without a hiccup.
I put stop strips on the doors using 1/4" thick pieces of oak that were screwed to the inside lip of the face frame. I even used the little bumpers they give you when you buy Blum hinges.
The handles went on in a similar fashion to the drawer hardware where I made a template with masking tape. Easy Peasy!
Step 31: Installing Shelves
We decided to just keep things very simple and have one shelf in each cabinet (except the middle). I used strips of wood screwed to the sides of the cabinet to act as supports for the shelf. I then used a piece of 1/2" plywood with a front edge of oak to act as the shelf. Just make sure that everything is level. I used a block of wood again to act as a guide for where the shelf supports go to make sure everything was spot on.
Step 32: Installing the Tops
The tops need to be able to move with seasonal movement. DON'T attach them directly to the cabinet with screws or you will cause significant damage to both the cabinet tops and the top edges of the cabinet itself. I used the grooves that I had dadoed out when building the cabinets to attach the tops. I made a block with two pieces of plywood, one with a lip sticking out that would neatly fit into the groove on the cabinet. This little block first slips into the groove and then got screwed to the top. I used four of these little blocks to hold down each top. They do a great job moving with the changing dimensions of the top. I did have to use a right angle adapter to drive the screws into place... just something to think about depending on how tall your drawer cavity is.
Step 33: Building and Installing the Slide Out Trash / Recycling Station
So... this part was put on hold due to COVID-19. We are 100% fine but the parts didn't get shipped in for quite some time and now I just need to find a cruddy day to build the last parts and install the whole shebang. More details on this final part to follow soon.
And here they are! Got 5" of snow last night and couldn't get out in the garden with all the late season fluff on the ground so I finished up my slide out trash and recycling!
Basically I built another large drawer box like I did before for the window seat and attached it to the cabinet with the drawer slides. I made the box divided again so the trash and recycling wouldn't fight... or it would keep the box even more stable. I then used double sided tape to adhere the front door to the box and used four washer-headed screws to secure the door to the box. Put the handle on right in the center and we are done!
I hope you enjoyed the project and if you have any questions do not hesitate to ask.
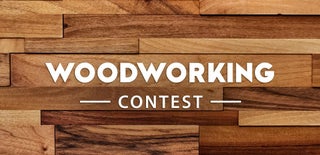
First Prize in the
Woodworking Contest