Introduction: Acrylic Bending Tool
In this instructable / video I am going to show you how you can make simple, cheap and very useful acrylic bending tool. It opens new possibilities and ways you can work with acrylic.
Provided Amazon links are affiliates
Tools You'll Need:
- Router (optional) https://amzn.to/2DVXXZC
- Drill: https://amzn.to/2U5QQmL
- Jigsaw https://amzn.to/2rg4uXx
- Clamps https://amzn.to/2E8EBkQ
- Tape measure https://amzn.to/2rfS4Ph
- Speed square https://amzn.to/2Ee6lDh
- Acrylic cutting knife https://amzn.to/2TZ1645
- Digital Multimeter https://amzn.to/2rf0EO3
- Power meter https://amzn.to/2TB8T2G
- Soldering kit: https://amzn.to/2Q613Bf
Materials You'll Need:
- Plywood or MDF (local hardware store)
- Acrylic / Plexiglass sheet https://amzn.to/2FzPb3B
- Aluminum profile (local hardware store)
- Bolts, washers, nuts (local hardware store)
- Medium tension spring https://amzn.to/2OqQkxj
- Hinges https://amzn.to/2UUHIBr
- Nichrome 80 24AWG heating wire https://amzn.to/2YsuFcD
- Wires (local hardware store)
- 19V 4.74A 90W power supply (buy used one)
- 10A PWM controller https://amzn.to/2TZMbXi or
- 8A Buck converter https://amzn.to/2Yq48gd
You can follow me:
- YouTube: https:// www.youtube.com/diyperspective
- Instagram: https://www.instagram.com/diyperspective
- Twitter: https://twitter.com/diyperspective
- Facebook: https://www.facebook.com/diyperspective
Step 1: Preview
With this acrylic bending tool you can easily make accurate 45, 90 and 135 degree bends. It has integrated 90W power supply from an old laptop and the integrated power control.
Like what I do? Consider becoming a PATRON! This is a great way to support my work and get extra benefits! https://www.patreon.com/DIYPerspective
Step 2:
For this build we will need to cut (from 9mm thickness plywood or MDF) these parts:
- 1x 60 x 45cm
- 2x 45 x 22cm
- 4x 19.5 x 4.5cm (2 pieces just for better look)
Also we will need:
- 45cm length aluminum U profile/channel (height slightly lower than plywood or MDF thickness)
- M6 bolt with nuts and washers
- M4 bolt with nuts and washers
- Tension spring
- Nichrome heating wire (in my case 52.5cm length)
- Pair of hinges
Step 3:
In the one of 45 x 22 cm part we need to make a groove for an electrical wire.
Then this piece can be screwed to the base part (60 x 45cm).
Next with few drilled holes in the aluminum profile, we need to secure it on the base.
Now we can place other 45 x 22 cm part and secure the hinges.
Step 4:
We can cut out part of the plywood to slightly hide the hinges. It is not necessary, if you want less work just cut those pieces slightly shorter.
Step 5:
But what is necessary is to place the left bottom guide perpendicular to the aluminum profile.
And the top left guide in line with the bottom guide. This will give accurate bends without possible tilt to one of the sides.
Step 6:
In the left side we need to drill a hole for the M6 bolt and in the right side hole for the M4 bolt.
Next we need to cut a triangle which will limit bending angle at 135 degrees.
Step 7:
We can secure it with two screws. One thing that I changed - I made this piece from the plywood as it is more durable than a soft pine wood.
Step 8:
Without any pieces attached we get 135 degree bend.
With other simple pieces attached we get 45 and 90 degree bending angles.
Step 9:
Now we can secure heating and electrical wires between two washers in the left side. In the right side we need to wrap the heating wire around one end of the spring, and tighten the spring to the M4 bolt between two washers.
Make sure:
- That spring have enough tension
- Heating wire is tight between two bolts
- Heating wire is in the center of the aluminum profile.
Heating wire MUST NOT touch the aluminum profile or it could cause short circuit.
Step 10:
For additional safety we can add two nails. They should be at least 1mm from the heating wire.
They are not the guide, they are just for the safety that heating wire wouldn't touch the aluminum profile in any case.
I wrapped other electrical wire around the one end of the spring, that it wouldn't touch the heating wire. By securing wire here, I even could add solder to it. As max temps there were just around 60C after 5 minutes of use.
Step 11:
To power this tool we can use very common 19V 4.74A 90W power supply from an old laptop. As you can get these really cheap it is pretty good power solution for this inexpensive build.
But we can't just directly connect it to this tool. With 19V and 3.4 Ohms resistance between wires we should get current of 5.6A (19/3.4=5.6). This can trigger over-current protection or overload the power supply.
So we additionally need to use the 10A PWM controller or the 8A Buck converter.
Step 12:
I done some efficiency testing and it looked that 8A buck converter is the way to go, especially when it had proper turn off click at the beginning of the rotation.
But I chose the 10A PWM controller. The reason why is that no matter what voltage you put in (12-40V) you have full range of the precise control without any dead zone on the knob. Meanwhile on the 8A Buck you have less rotation with a quite big dead zone at 19V input.
Step 13:
Now we can cut small piece of acrylic, temporary connect the PWM controller and make this simple holder for it.
Step 14:
In it we need to drill holes for the controller, for quick heat escape on top and for screws in the sides.
Step 15:
We need to connect electrical wires from the heating wire to the connectors on the controller where MOTOR is written. And power supply wires goes to connectors where POWER is written.
We can secure power supply wires and power supply itself on the base for full integration.
Step 16:
Finally, with the power meter we should mark different power states. I marked:
- Lowest point as OFF
- 60W as LOW
- 90W as High
- Max point as MAX
We shouldn't use more that 90W of power from a 90W power supply as it could damage it over time.
Step 17:
90W of power is more than enough for acrylic to bend from what I tested. So that's basically it.
I hope this instructable / video was useful and informative.
If you liked it, you can support me by liking this Instructable / YouTube video and subscribing for more future content. Feel free to leave any questions about this build. Thank you, for reading / watching! Till next time! :)
You can follow me:
- YouTube: https://www.youtube.com/diyperspective
- Instagram: https://www.instagram.com/diyperspective
You can support my work:
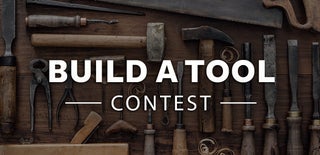
Grand Prize in the
Build a Tool Contest