Introduction: Advanced CNC Methods and Wood Clamping
I'm suggesting that you may have advanced to the stage that you can design and tackle CAM operations? This Instructable is not a primer on designing in Fusion 360 or enabling a CAM procedure. That will take some practice on your part. You may have only done cutouts, engraving or one sided machining. It's not a bridge too far to embark on two sided work! With the use of tabs and clamps you can easily make a model as shown in the first two photos. Design symmetry is your friend in these type of instances and having a central reference for XY axis. The Z axis is a little trickier in that you need to flip your model in Fusion 360 after downloading the CAM procedures for one side's operations. Then readjust your Z axis reference to the other side. You'll see the difference in comparing the 3rd & 4th pics. Notice how the model has been turned upside down and the cubic 3d visualizer is upside down in top right of pic?
Step 1: One Sided Mirror Combinations.
Materials:
Titebond 2 glue as a min
8mm dia hardwood dowel.
12mm baseboard
Steel washers 2mm thick
Method
This is where you are going to machine Left hand - Right hand halves, one side only and then glue them together to form one body. This is relatively easy to achieve design and CAM wise. You design one half and then mirror it to form two bodies. Then you need to place each body alongside one another on the same plane, allowing enough room for a milling tool in between.
The tricky bit here is, "How do you hold the two blanks securely? This is where I use 8mm hardwood dowels! In the 1st picture showing the machined stiletto boots, the two right hand models are pairs of mdf blanks glued together to form half the desired model's thickness plus a few millimetres. These blanks are drilled with 8mm dia holes and dowels glued in. The dowels project out one side the thickness of the baseboard plus 2mm. In other words if the blank is 50mm thick, cut dowels 64mm long if using a 12mm backboard. The drilling of the backboard to suit is another body to your design. The reason for the 2mm extra, is after glueing the dowels in your blank you need to glue the projecting part of the dowel into the pre-drilled holes in the baseboard. However, you use a steel washer as a spacer between the top of baseboard and underside of blank. Why do you do this? Coz when it's time to release your machined half from the backboard, you slide a handheld hacksaw blade in that 2mm gap and cut through the dowels. There's a video above where I've finished cutting the dowels and lift off the model. You'll see the washer. I use Titebond 2 glue as a minimum and have never had a failure using this method. Just sand flush the dowels.
In the Easter Island statuette picture (2nd pic) you can see the dowels that are incorporated in the models and all the clamping is done onto the baseboard leaving the milling to continue unobstructed. All the models are sitting up 2mm off the baseboard for easy removal later.
Step 2: Mirrored Two Sided Machining to Form a Vessel
In the 1st pic you can see how I've progressed to milling two halves but each side of each half. They are then glued together to form a hollowed out vessel. The remaining pics show the similar use of a backboard as the previous step, except this time you need to flip the bodies and swap from left hand to right hand. This means your backboard has two sets of paired holes( LH & RH). You need to proceed cautiously thinking wise as it can get confusing? Sometimes, I also use tags to hold the two halves together for the interchange as it becomes difficult to re zero your XYZ axis if they're not held together.
Because my wall thickness is slim in some models (4.5mm), you need to build in a little extra meat to support the dowels. They become a design statement in themselves, so careful consideration of placement is necessary. The last picture shows the internal pillars up the body axis. They get cutoff flush in the end. Incorporating these dowels allows for an entire new world of 3d milling to be carried out on a basic CNC machine. There is one other consideration that will limit you, apart from the working bed size of your machine, and that's the amount of Z travel? On my Axiom AR4 Pro, you start with a gross Z travel of 150mm. Then less a 12mm backboard, projection of your endmill from the collet and clearance over your blank....I'm left with a half height of about 50mm. So I can build vessels up to a height of about a 100mm.
Step 3: The Next Frontier?
The next frontier for me, as well as or instead of dowels, is using 5mm dia allen key countersunk bolts? They start from the underside of the baseboard, go through a spacer that can be incorporated as seperable component of your model and through into 5mm dia female brass pressed inserts. This was going well on my latest build until I stuffed up on wall thickness calculation (it got down to less than a mill thick) and shattered! See picture. Despite the mishap, it bodes well for future applications, so give it a try. Just keep your hole tight as any play will mean the model will yield a little whilst machining.
Happy CNC machining.
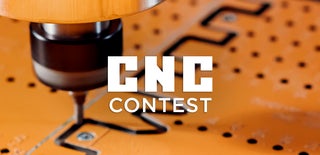
Participated in the
CNC Contest