Introduction: Advanced Push Block
No! Not another push block 'how to', right? There are so many people that have so many different designs, each claiming there push block is the absolute, very best. I admittedly never wanted to make a push block 'how to', because I'm not one who has ever been fond of push blocks/sticks. I very much have shied far away from anything that could protect my fingers. Besides all that, I never figured any innovation could be made to such a creation that would warrant a need to revisit the old as time product.
But things changed a couple instructables ago. I, by mistake, showed my practice of using a table saw where my finger came within inches of the blade (did I say inches? I meant fractions of an inch). The crapstorm that ensued still leaves me awake at night, screaming at the ceiling, "I didn't mean to, I'm sorry!". Post after post I found angry users attacking my behavior with a single individual calling for me to redeem myself by making a push block instructable. I was shocked!
But then my brain went into overdrive. I talked to my good buddy from NZ and confessed to him my grievances with push blocks. I told him I didn't like the lack of control I felt after letting the back end of a board pass behind the front of the blade, and hoping (and praying!) that the back end didn't nick off the end of the board. With my thumb and fingers, I'm able to push against the fence my precious wood as well as pushing it forward, but a push block only moves forward.
I then cut the pin on the back of my push block into an angled position which would allow me to push the board against the fence and forward. But this turned out to be an extremely unsafe practice as it isn't always a static angle: the angle moves and shifts and using just a single angle takes away later leverage needed to push the stock through.
My brain fluttered for days as I crafted the movable pin. I wanted to use a knob on the top so that it could be positioned just right. I needed a way to attach the knob and knew I couldn't use a metal bolt as that would have been unsafe. So I looked at toilet bowl nuts, made of plastic, and then looked at coupling nuts to link them together, higher up on the push block. This was no good. This was turning into a Dexter's Lab experiment!
Enough of the blubbering, what follows is the final design that I came up with. And this baby works quite well...so well, I thought about possibly throwing a patent at it.
Step 1: Gather Materials / Tools Needed and Used
Material List
Wood Needed:
- 7" x 9" x 1/4" (I used walnut)
- (2) 5" x 6 3/8" x 1/4" (I used hard maple)
- 1" x 6 5/8" x 1/8" (I used Pauduk)
- (2) 1" x 1" x 1/4" (I used Pauduk)
- 7" x 1/4" Dowel rod
Other items:
- Glue
- Hot glue
- Polyurethane (Optional)
- Sand paper
- 1/2" steel washer with an outside diameter equaling an inch (to trace with)
Tools Needed and Used
- Drill / 1/4" drill bit
- Bandsaw
- Belt and oscillating spindle sander (sand paper could work)
- Clamps for gluing
Step 2: Necessities and What's...Not
Looking over both the materials and tool list should indicate, to you, how relatively simple this build is. The 'Advanced Push Block' really only has 2 important variables that must stay the same: There will need to be a flat back to it as a dowel rod will be contained within and there will be a 'cam' like pin at the bottom that rotates. I would also add that this push block should have a very narrow profile, which is why I made the Blade a 1/4" thick (more on that in the next step.
The shape of the rest of the push block as well as the width of the handle is completely up to you. When I made the shape of my push block, I randomly put lines on a page until I got a basic shape of a push block. Feel free to make your push block look however you want it to so long as you follow those two (or three?) rules above.
Step 3: Naming and Tagging Our Parts
Now there are three parts that make up the main body. Besides those 3 parts, we'll give labels to all the wood pieces here and refer to them by these labels. Since push blocks look like ice skates, we'll have a little fun with this:
- 'Blade' = 7" x 9" x 1/4"
- 'Boot (side A and B)' = (2) 5" x 6 3/8" x 1/4"
- 'Heel' = 3/4" x 6 5/8" x 1/8"
- 'Eyelet' = 1" x 1" x 1/4"
- 'Pin' = 1" x 1" x 1/4"
- 'Rod' = 7" x 1/4" Dowel rod
Furthermore, I'll underline each term throughout, just like the old school textbooks (hoping there are still textbooks that do this...or, ugh...still textbooks?).
Step 4: Gluing the Main Body Together
We're going to sandwich the Blade between Boot A and B. This will leave 4" of the Blade protruding from the front. I'll placed a sketchup image with this step so you'll get an exact idea of what I'm talking about.
But mine doesn't look like yours. Yours is all blingy and stuff.
Mine can easily be made before sandwiching it together by using a design I have also included with this instructable. Yes, I love you all...unless, of course it doesn't matter to you...then, never mind. Okay, I love you anyway.
Once you've chosen whether or not to use my fancy shmancy Boot A & B pattern (yes, you'd have to cut both sides which can be done by first taping both pieces together before heading to the bandsaw) or just the bare bones one, glue it together. Make absolutely sure (sketchup pic #3 demonstrates this) that you leave a quarter inch cubic valley between the ends of the Boot and the Blade. That is, the Boot will be 1/4" back from the Blade on the one end. If you're unsure, check out the video link as there are more detail there.
Put your clamps on, using a little bit of salt over the glued area (this prevents movement as it clamps, which is totally optional). Keep in mind that the pieces I used in this step look a little different on the video, only because I wasn't sticking to an instructable and didn't have enough solid pieces to do full sheets.
Step 5: The Pin Through the Eyelet
Okay, okay, ignore the verb in the title. In this step we'll be making both the Pin that sits on the base and the Eyelet that will keep the Rod from coming out...but neither will go through the other. If semantics were a set of paints, I would be a discombobulated, abstract painter.
We'll take the two precut sizes (both of which are 1" x 1" x 1/4") and we'll mark an 'X' through the center with dual diagonal lines. I suggest not using end grain wood to make these 2 pieces as that would be weak and therefore dangerous. We'll use a 1/4" drill bit and drill through the center of both.
After those holes have been drilled we'll take our Rod and glue the Pin on with a little bit of glue. We'll make sure it's flush with the Rod on one side and we'll give the glue a chance to dry. The Eyelet isn't nearly as important and can be trimmed down with a sander or left alone. It's primary job will be to keep the rod from coming out and, at this stage, will be left alone.
Step 6: Adding Our Heel
Before we start on the Heel, be sure the dowel rod slides in the channel between the left and right Boot, and center Blade. Give it a spin: it should spin easily.
Now then, we are entering a danger zone here. It is absolutely imperative that when you attach the Heel to the Boot that you do not get any glue in the channel that the Dowel fits into. I know, I know, dear Ibilite, this shouldn't need to be said, except it can happen if you're not careful.
Alright, now we'll pull out the Heel piece (3/4" x 6 5/8" x 1/8") and we'll dab a minute amount of glue along both sides of the piece, but not the center. We'll make sure to line up the end of the Heel with the top (the part where your hand goes) of both Boot pieces and allow the end of the Heel to hang below the base. After that has been done, use clamps and tighten down, checking back later to see if there's any movement.
A little video clarification on such a sticky subject (sry)...
Step 7: Shaping the Handle
Now those corners are rough on your hands! You'll never use this push block if its not ergonomically accurate! In the video, I showed a lot of sanding with a hidden purpose: I wanted those viewing and following this instructable to know of the time I spent working on sanding it so that it was absolutely perfect to my hands. And it is! So give it some work, use some sandpaper, an oscillating spindle sander or maybe a belt sander...but make it become part of you. You are one with the push block, young grasshopper. Like water, let it flow from your palm to your...okay, too much. Do take some time with this step and be sure the glued Heel isn't stripped too much of its wooden exterior.
Step 8: Shaping Our Pin
OKAY, pin and dowel are dry, from step 5, but has it cured? I'd probably wait about 12 hours before starting this step. But wait...you have? Well my apologies. Let's continue.
We'll take the 1/2" washer (that ends up having an outer diameter of 1") and we'll place the outside edge of it onto the dowel and pin side, flipped dowel end down. I've referenced it in the picture in this step, so if you're confused at this point, give it a look. Draw on the outer edge of the washer until you've made a half moon on the pin. When that is complete, head over to a sanding device of your choosing and sand baby, sand till the outer wood of your Pin is carved back to the line you made.
After this has been accomplished we'll add a small strip of sandpaper to the opposite side of the curve you made (the flat side that will come in contact with future wood projects, ready to become two on the table saw) with a little hot glue. This could be optional, but probably shouldn't be. I don't have this part included in the video build as it seemed to work (at first) without it. Now I'm convinced it is a good idea to include it.
Step 9: The Rod and the Eyelet
Now that the Pin has been shaped we'll feed the Rod through the opening of the push block channel. We'll take the Rod and thread the Eyelet through it. Now the Eyelet needs to be pressed all the way down to the top of the push block. It will be used to keep the Rod from dropping through the bottom. After the Eyelet is pressed somewhat tight against the push block, cut the excess Rod off and use a bit of hot glue on the top to keep it altogether.
Step 10: Finish Line! + IMPORTANT Tips
Once things are dry (glue), you can throw a coat of polyurethane or some beeswax, motor oil, what ever's your fancy. It's now ready to be used! A few tips:
- I am able to cut as thin as 7/8" strips with my push block. If you can't, consider sanding the sides of the push block until it's thin enough to do what you want.
- Angle the push block tip at or towards the fence as you push.
- The farther away from the fence the pin is, the more diagonal force you'll be able to exert. Thinner pieces will be more difficult to push diagonally over larger, more wider pieces.
- MAKE SURE YOUR BLADE IS SHARP! Duller blades will make it harder to push wood through causing more strength needed to keep it against the fence. This is an extremely import point that you shouldn't gloss over. Sharp blades are safer and will require less force (it's physics, ya know?).
- Thicker pieces of stock will obviously be more difficult to push through so you might cut a piece of thick stock in stages. That is, make several passes over the blade, raising the blade each time.
- Blade angle is also going to cause more resistance, or as much as a thicker piece of stock would.
- The width of Pin is wider than the push block. You will naturally cut off one side of the pin as it will jut out. This is perfectly fine and will not effect the push block. Make sure you don't cut into the body of the push block though.
- Draw a line from the blade to the front of your table saw with a pencil with a carpenters square. This is the blade path and it'll make it easier for you to know whether or not you will cut into the push stick.
- REMEMBER THE PUSH BLOCK CAN BE REMADE!! If push comes to shove, don't try to save the push block as you are pushing the stock through. Let it be destroyed before you try to save it. It is not your body and can be easily replaced. Lifting up on the push block and trying to prevent the blade from cutting it can cause your stock to move and become air born, possibly impaling you. THIS IS NOT A JOKE!
Step 11: Thank You!
Thank you so much for viewing this instructable! If you like it, please consider going to my youtube channel, hitting subscribe and throwing a like (with maybe a comment). Follow me here, if you want, and favorite this. Vote for me in the contest and thank you so very much for taking a little interest in this project!
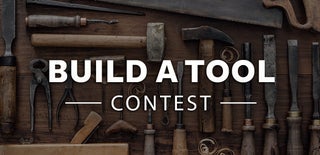
Participated in the
Build a Tool Contest