Introduction: Animatronic Cosplay Wing Mechanics
Out of all the costume animatronics projects I've taken on, this was by far the most challenging.
Animatronic wings present a lot of problems for costumers- weight, power requirements, movement, and durability all have to be taken into account. They are just flat out hard to make. This small mechanism was created for an Asuna Sword cosplay to allow four wings to lift up and fold back- using only a single servo with as little as 4.8V power. The baseplate measures just 7" wide.
Here's a video showing the mechanism moving four polycarbonate wings. The total wingspan is about 62" and the movement is unusual as the character's wings don't have a defined pivot point- they appear to "float" as they raise up and fold backward.
Here's a video of just the mechanism moving. You can see how the lead screw drive moves the wing base pivots and how the radius arms move the wing mounts.
The goal of this project is to help others with their moving wing projects- think of it as a recipe guide. If all you need is to make wings move up and down this will show you how to make a really compact linear drive. But if you want a folding movement then you're covered too!
Be sure to click on each image as there are notes!
Let's get started!
Step 1: Tools and Materials
The tools for this are pretty basic. You can get by with a bandsaw, drill press and files. Having access to a lathe makes making custom pivot parts a lot easier but it's possible to design around that.
The belt sander just makes cleaning up parts go a whole lot faster than having to file everything by hand. :)
For materials I used:
Various thickness Aluminum plate/sheet
Brass tubing
Steel rod
Music wire
A LOT of 6-32 socket head cap screws
Small brass washers
6-32 set screws
4-40 socket head cap screws
1/4-16 ACME lead screw and nut
Hitec HS-7955TG servo
5K potentiometer
Step 2: Mechanical Design
The design of this mechanism didn't happen overnight.
The Asuna Sword character has beautiful translucent wings so I knew right away the wings needed to be made from a rigid transparent material. Unfortunately that meant they would not be super lightweight. You have to think of a wing as a big long lever that you are trying to pick up by the very end. The more leverage you have and the lighter weight the wing is, the easier it is to move.
Say you have a 30" wing that weighs 5 oz and you have it mounted on a pivot. Servo torque ratings are typically listed as oz/in, meaning that the stall torque of the servo might be 180 oz/in. That means with a one inch long lever the servo will stall just as it tries to lift a 180 oz weight. Now you never really want to max the servo out as it can easily be damaged if it stalls (typically burns out the control circuit) and as you approach the stall rating the power draw goes way up. That 30" long, 5oz wing represents roughly a 150 oz load to the servo when it is mounted directly to the servo output shaft (yes the weight is distributed over the entire wing length but it's a close enough approximation.) While the servo can lift the wing it certainly won't be very happy doing it- it will have a hard time controlling the wing movement (especially when lowering the wing) and it will probably burn out trying to hold the wing up.
This is what I learned when I built the first mechanism. Originally I had eight servos- each wing had a lifting servo as well as a folding motion servo. This was later reduced to six, as I only needed two servos to make the wings fold back in unison. I made wings from laminated plywood for testing and sure enough the servos couldn't control the movement properly. This led me to the idea of using a lead screw to raise the wings.
Lead screws are great. The beauty of a lead screw is that it works kind of like a wedge. With very little input force you can lift a large weight- and it will stay put. This part is super important as it greatly reduces the power requirement of the servo. You can remove power from the servo and the wing will still stay raised. Lead screw mechanisms are typically packaged as a linear actuator or linear servo- the lead screw, motor and controller are all combined together in a nice contained unit. There is a lead screw calculator located here. Just plug in the lead screw specifics and your load and it will tell you the motor torque requirement. The specific type of lead screw can greatly affect how your movement works.
The problem I faced is that most linear actuators/servos were far too big- even the miniature ones made by Actuonix. If you have enough room in your design by all means use them! I needed to come up with my own type of actuator. By removing the internal potentiometer from the servo and using it externally I could have the servo continuously rotate the lead screw while still maintaining positional control. The first lead screw mechanism I built used this arrangement. The nut on the lead screw has a pin brazed to it that slides in a cam. As the lead screw turns the nut will not rotate and the pin slides in a slot, raising the cam/wing as the nut moves down the lead screw. This was a pretty neat solution and it lifted the wings beautifully- but it took up a fair bit of room and it was finicky to construct. I needed a smaller, simpler lead screw mechanism.
The second lead screw mechanism moved a single lead screw to the center and had rods that now moved the cams. This worked perfectly and was very compact. The wing folding movement was still done by four individual servos, so I was down to five servos total. Five digital servos still draw a lot of power so I began thinking about other means to get the wing folding movement.
I tried all kinds of different cam/ramp type arrangements. I made probably thirty different linkages. Most of them were either just way too complex, not sturdy enough or had way too much friction/binding. Then one night I made a little link/radius arm that had a sort of universal joint on each end and I made a wing mount lever arm that attached to the pivot cam. As the pivot rotated this radius arm would force the lever arm (that the wing attached to) to swing forward and back. Problem solved! And just like that I could now move four wings in an up/down, forward/back motion using a single servo. And because the lead screw mechanism was so powerful I could do it even with a small 4.8V battery pack.
The beauty of this mechanism is that it can be as simple or complex as you want it to be. You can keep it super simple and just raise two wings if you want!
Step 3: Base Plate
The lead screw/base plate is the foundation.
The base plate was made from 1/8" thick Aluminum. You can use any material you like to build a mechanism like this. You could even use plywood! All that matters is that it is strong enough for the weight of your wings.
The base plate holds the four pivot mounts as well as the lead screw support bearing and a small linear guide track. The track is important as it keeps the lead screw block moving straight and keeps it from rotating. The support bearing takes some of the load off the servo output shaft- this could be as simple as a wood block with a bronze bushing. For the pivots you could use a 1/4" bolt fastened to the base plate.
The lead screw block is designed to hold the lead screw nut and keep it from rotating. Thus as the lead screw is turned, the block slides down the track. The lead screw is a 1/4-16 ACME lead screw.
You can see from the photos the construction of this is very simple. The brass plate acts a retainer for the lead screw nut and holds it in place. It's important the nut not fit too tight in the slot on the block- it needs to have a bit of wiggle room so it won't bind as the block moves up and down the lead screw. Attached to the bottom of the block is the slider for the linear guide. If you're trying to keep it super simple you could make the block from plywood and have it rest on the baseplate (this will keep it from rotating as it moves.) Then have a couple of guides (either wood, plastic or aluminum angle) on the sides of the block to keep the block moving straight. Another option would be to 3d print the entire base plate assembly with the guide track and bearing support as a single piece.
Step 4: Main Pivots
The main pivots anchor the wings to the backplate.
The main pivot blocks (or cams as I like to call them) are made from 3/4" thick Aluminum. They rotate on 1/4" diameter steel rods that are held in place by the base plate mounts. I made a little brass tubing bushing for them to pivot on as well as a brass retaining cap but a simple set screw collar would work just fine too. The upper cam is slightly shorter than the lower cam. This means that the lower wing won't move as far relative to the upper wing as they raise up.
The cams have four small 4-40 socket head cap screws threaded into their top side- these help secure the wing pivots that go through the holes in the sides of the cams.
The curved connecting links that join the upper and lower cams are 1/4" thick Aluminum and have upper and lower brass bushings for less friction as they move. The arms are secured to the cams using 6-32 socket head cap screws. Note that the upper screw is recessed in the cam as it needs to be flush with the top of the cam surface.
Next straight links were made from Aluminum that connect the lead screw block to the upper wing cams. So now as the lead screw moves down, the upper cams rotate (lifting the upper wings) while at the same time pushing the curved links that cause the lower cams to rotate (lifting the lower wings.)
Finally the servo mount plates were cut from 1/4" thick Aluminum and bolted to the base plate. The servo mount plates have holes in the sides that serve as locating points for the later to be installed radius arms.
Step 5: Servo Mounting
Time to add some muscle!
The servo I chose is the Hitec HS-7955TG. This is a Titanium geared standard size servo that is extremely powerful and is very easy to modify- you just remove the internal potentiometer and the gear stop that limits the rotation to 180 degrees. This process is reversible too- the only permanent modification is making the wire slot in the case a bit larger. The pictures show the process of how to take apart the servo and remove the pin on the output gear/shaft that limits rotation.
If modding servos isn't your thing, Hitec manufactures two multi-turn servos that are capable of between 7-8 full rotations with positional feedback. The standard size servo is the new HSR-M9382TH and the large size is the HS-788HB. With either of these servos you get a much cleaner mechanism as the external potentiometer is not necessary. When using either of these servos you'll want to use something like a 4 start 8mm pitch lead screw (same as what many 3d printers use) as that would give you around 50mm-60mm total movement (8mm linear travel for each full turn) at the lead screw block- and it'll be much faster than the 1/4-16 lead screw. If you need to turn the lead screw more than 7-8 turns to get more travel you'll have to do some servo surgery.
The servo has a 1/4" shaft coupler mounted to its output shaft- this is what connects the servo to the lead screw- note that different servos have different output spline patterns so it's important to get the correct coupler. I do not know of an 8mm servo shaft coupler so either you would need to turn the shaft diameter down to either 1/4" or 6mm to fit an existing coupler or come up with some other arrangement if you want to use an 8mm lead screw. The servo is mounted to the base plate mounting frame using a servo plate.
The external potentiometer has a brass arm attached to its shaft so it can be turned by the motion of the lead screw block as it moves. The brass arm is made by soldering the arm to a set screw collar and then it's attached to the lead screw block using a 4-40 threaded link. The potentiometer is held onto the base plate using a small piece of brass sheet.
As far as control goes this now acts just like any normal servo. To control the movement of the mechanism just connect the servo to an Arduino and use the servo library to call out your servo position when you push a button!
Step 6: Wing Mounts
Time to make some wing mounts!
The wing mounting plates are made from 5/16" Aluminum plate. The upper wing plates are slightly longer than the lower plates- this allows the upper wings to sit higher than the lower wings and allows for a bit of clearance as the wings are lowered all the way down. There are two 6-32 threaded holes on the end of each wing plate for mounting the wings.
Each wing mounting plate has two pivots- the lower pivot is what connects the plate to the rotating cam on the base plate and the upper pivot is what connects to the radius arm that makes the wing plate swing. The lower pivot pin also has a 4-40 screw in the cam to help hold it in place.
The pivot pins are steel and they ride in bushings made from brass tubing. The brass bushings aren't really necessary but they do make everything a bit smoother and add to the longevity of the mechanism. The pivot pins are held in place using small circlips.
The upper pivot pin has a larger end on it with a hole in it- this is what attaches to the radius arm and it forms part of the universal type joint.
Step 7: Radius Arms
The radius arms are the magic links that make the folding motion happen!
The radius arms are made from 1/8" stainless steel rod bent to shape. On the end of each arm there is a U shaped piece made from 1/4" thick Aluminum. The rod is inserted into the end of the U shaped piece and is held in place with both a 6-32 set screw and a 6-32 socket head cap screw. One screw would probably be fine but I wanted to be extra sure it wouldn't come loose!
The U shaped piece also has a small steel pin that is press fit into two holes that are drilled across the U opening. This small steel pin rides in a brass tube bushing located in each end link steel pin. The end link pin is free to move in the U shaped opening. This forms a sort of universal joint that allows the radius arms to move throughout their range of motion without binding.
One end of each radius arm is attached to the base plate servo mount frame and the other is attached to the wing mount plate. These little links are a bit fiddly to make and set up but they work great.
Now as the wings rotate upward the wings fold back. By changing the geometry and mounting points of the radius arms you can change the movement of the wings as they raise and lower.
Step 8: Finished!
Making this mechanism was a very long and hard journey.
In the past few years I learned an awful lot about making wing mechanisms. There were a lot of setbacks but in the end I learned how to build a really neat mechanism- in all my searches into the history of animatronics I've never seen anything quite like it and that makes me pretty happy.
In its most basic form (without the radius arms) it's a great simple lead screw mechanism that is capable of lifting heavy wings on very little power. You can make as simple or as complex as you want. It could probably be built even smaller.
I already have a new larger mechanism in the works using a similar lead screw setup that is going to move some really big wings. :)
I hope this inspires people interested in adding animatronic wings to their cosplay costumes and I look forward to seeing what people create!
As always if anyone has any questions just let me know!
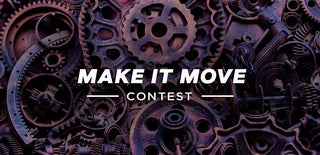
Second Prize in the
Make it Move Contest 2020