Introduction: 1st Gen Apple Pencil Charging Dock
The 1st gen Apple pencil that was released on the 11th of November 2015 has a problem: it can only be charged through its lightning port. That means that every time you wish to juice up the pencil, the magnetic cap needs to be removed and stored somewhere where you won't be lost. Then to charge the pencil, it can be plugged into the lightning port of the iPad, or to a lightning charger via a special tiny adapter.
That whole protocol is unnecessarily complicated and stressful, as there are two small pieces involved that can be lost very easily.
Studying at the Catholic University of Louvain in Belgium, I use my iPad every day for note-taking. That means I need to charge my pencil quite frequently, and Apple's really isn't smooth enough.
So, I decided to make a custom docking station, to make the workflow of using the iPad more convenient. Also, it keeps the workspace clean and organized.
In this Instructable, I will show you how to make one for yourself too!
Step 1: Watch the Video
I also made a quick video about the making of this dock if you wish to see some live action crafting:
Step 2: The Design
First, a quick word about the design of this station.
The station will have to satisfy three needs:
- Keeping the charging cable permanently in place with its special adaptor
- Have a place to securely store the magnetic cap of the pencil
- Make it easy and quick to plug in and remove the pencil when desired
We will use 3D printing, so as to obtain a perfectly tailored fit with all the non-3D printed components. To satisfy the last requirement, the holder will be filled with cement. That will make the dock a lot more robust, making sure that it doesn't tip over with the weight of the pencil. Also, it will give it a more qualitative feel in comparison to a plasticky and hollow-sounding 3D-printed shell.
For the design process in Fusion, I first modeled the pencil and the charging adaptor that will nest in the center of the dock. I added a tolerance of 0.5mm using the offset face command. I then created a cylinder around them, that I hollowed out with the cut feature. That's the central shaft that will hold the cable and the pencil upright.
It was then time for the body of the dock. I decided to match the clean and minimal Apple aesthetic with a basic cylinder - less is more. I hollowed it out using the shell command, to make room for the cement.
Finally, I split the model into three models:
- The top of the station that will be filled with cement
- The bottom piece that will hold in place the charging cable
- A temporary bottom piece that will be used for molding the cement and give it the negative of the cable
Step 3: 3D Printing
I 3D printed everything using PLA filament.
To make it easier to remove the last piece from the cement later do not print it with a matte filament, but a shiny one. That will make it harder for cement to grab onto it.
If your 3D printer produces elephant's foot, chances are, the holes for the pencil and the magnetic cap will turn out a bit too small. That issue can be resolved quickly by giving the insides of the holes a quick sanding.
Step 4: The Release Agent
To make the mold even easier to remove later, it can be covered with a special concrete release agent - or simple cooking oil or vaseline will work great too.
Step 5: Cement
Technically, what we will be using is dried-out cement paste - as for it to be called concrete, it would need to include aggregate and sand. But to keep it simple I will call it just cement.
To find out the quantity of water that needs to be added, read the instructions that are on the bag of your cement. In my case, it was 5 parts cement for 1 part water. The mixture should be quite thick and not runny.
Mix everything thoroughly, making sure there aren't any dry lumps in the paste. Then, proceed to fill the 3D-printed cylinder to the brim, before closing it with the 3D-printed cap. The little notch in the cap needs to click with the incision in the molding piece.
Use a wet tissue to clean any spilled cement from the sides.
The drying time of cement can vary hugely on the type you're using. Mine was a fast-setting variety, so I removed the molding print after 3 hours, while the cement hadn't fully hardened yet.
After that, leave the cement to harden completely for 24-48 hours.
Step 6: Cleaning the Surface
Use a dull utility blade to scrape off any protruding parts from the cement surface. As we didn't add any sand or gravel, this is very easy to do.
Step 7: Sealing
Untreated cement has a bad habit of releasing fine cement dust. To prevent that, seal it using simple PVA or wood glue.
Once dry, the glue will become transparent and give the cement a shiny protective layer.
Step 8: The Top Layer
As the dock was printed upside down on the printer bed, it captured the texture of the shiny glass bed. That doesn't look very clean, so I decided to utilize my vinyl plotter to cut out a clean sticker to cover the top. That way, there isn't any messy 3D-printed linework visible.
To install the sticker, insert the pencil and the magnetic cap into the stand so that they can act as a guide.
If you don't have a vinyl cutter, you could leave the top as is, or use the attached PDF template to cut out a disk of some other material to go on the top.
Attachments
Step 9: The Bottom Layer
To give the dock some grip and character, you can cut out a cork or rubber disk and glue it on the bottom of the dock.
Step 10: Done!
Add the cable with its adaptor and close the dock. And just like that, we now have a functional and clutter-free charging station, that is always ready to go!
Thank you for reading so far, and have a wonderful day! :D
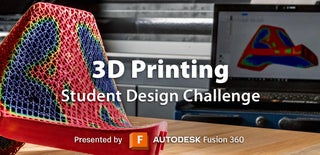
Participated in the
3D Printing Student Design Challenge